Introduction to EMS PCB
EMS PCB stands for Electronics Manufacturing Services for Printed Circuit Boards. It refers to the end-to-end services provided by electronics contract manufacturers to design, produce, assemble, and test PCB-based products for Original Equipment Manufacturers (OEMs).
EMS providers offer a wide range of services including:
- PCB design and layout
- Prototyping
- Component sourcing and procurement
- PCB fabrication
- PCB assembly (PCBA)
- Testing and quality control
- Supply chain management
- Aftermarket services
By outsourcing PCB manufacturing to an EMS partner, OEMs can focus on their core competencies of product development and marketing while leveraging the specialized expertise, equipment, and economies of scale of the EMS provider. This allows OEMs to reduce costs, improve quality, accelerate time-to-market, and enhance overall competitiveness.
The global EMS industry was valued at $463 billion in 2020 and is projected to reach $797 billion by 2028, driven by the increasing adoption of outsourced manufacturing strategies by OEMs across various industries such as consumer electronics, automotive, medical, aerospace and defense, and industrial automation.
PCB Design and Layout Services
PCB design is a critical first step in the EMS process that lays the foundation for a high-quality, reliable, and manufacturable product. EMS providers offer PCB design and layout services using advanced CAD tools such as Altium, Cadence, and Mentor Graphics.
Key aspects of PCB design include:
- Schematic capture: Creating a graphical representation of the electrical connections and components in the circuit.
- Component selection: Choosing the right components based on functionality, performance, cost, and availability.
- PCB layout: Arranging the components and routing the traces on the board to optimize signal integrity, power delivery, and manufacturability.
- Design for Manufacturing (DFM): Incorporating manufacturability considerations such as minimum trace width and spacing, hole sizes, and soldermask clearances to ensure high yields and reliability.
- Design for Test (DFT): Adding test points and other features to facilitate automated testing and debugging.
EMS providers work closely with OEMs to understand their requirements and constraints, and provide design reviews and feedback to optimize the PCB design for manufacturing and assembly.
PCB Prototyping Services
Prototyping is an essential step in the product development process that allows OEMs to validate their designs, test functionality, and gather feedback before committing to volume production.
EMS providers offer a range of PCB prototyping services including:
- Quick-turn prototyping: Rapid fabrication of small quantities of boards (typically 1-10) using automated PCB prototyping equipment.
- Low-volume production: Manufacturing of larger prototype quantities (10-100) using the same processes and equipment as volume production.
- Assembly services: Populating the prototype boards with components using manual or automated assembly processes.
- Testing and validation: Performing functional testing, boundary scan testing, and other validation tests to ensure the prototypes meet the design intent.
Prototyping helps identify design issues early in the development cycle when they are easier and less costly to fix. It also provides an opportunity to test the manufacturing processes and identify any potential challenges or bottlenecks before ramping up to volume production.
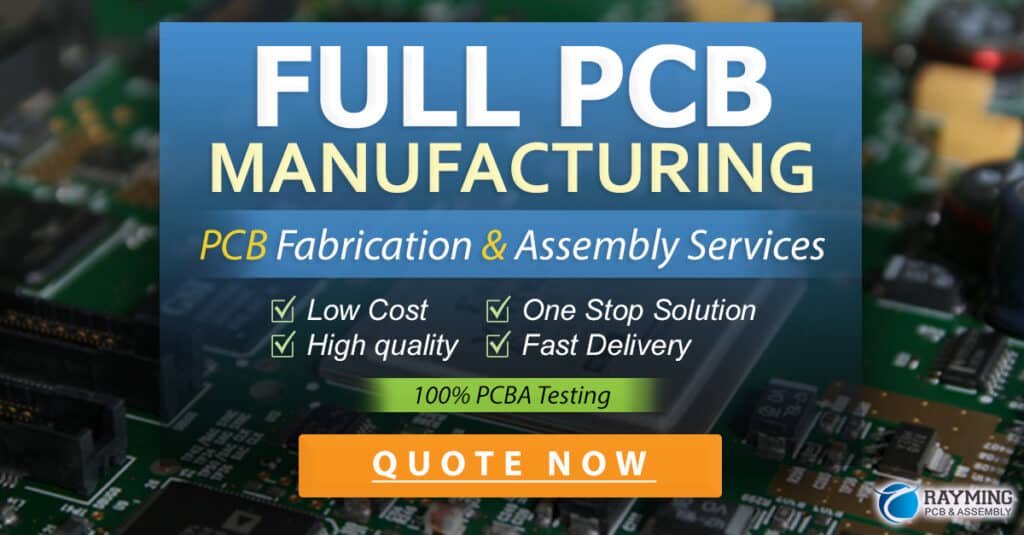
PCB Fabrication Services
PCB fabrication is the process of manufacturing bare printed circuit boards from raw materials such as copper-clad laminates, prepregs, and soldermask.
The key steps in PCB fabrication include:
- CAM processing: Converting the PCB design files into machine-readable instructions for the fabrication equipment.
- Etching: Selectively removing unwanted copper from the laminate to create the circuit patterns using photolithography and chemical etching.
- Drilling: Creating holes in the board for through-hole components and vias using CNC drilling machines.
- Plating: Applying a thin layer of copper to the holes and exposed traces to improve conductivity and solderability.
- Soldermask application: Coating the board with a protective layer of soldermask to insulate the traces and prevent solder bridging.
- Silkscreen printing: Adding component labels, logos, and other markings to the board using silkscreen printing.
- Surface finish application: Applying a surface finish such as HASL, ENIG, or OSP to protect the exposed copper and facilitate soldering.
- Electrical testing: Performing continuity and isolation testing to ensure the board is free of short circuits and open circuits.
EMS providers invest in state-of-the-art PCB fabrication equipment and processes to ensure high quality, consistency, and reliability. They also have the ability to manufacture a wide variety of PCB types including:
- Single-sided boards
- Double-sided boards
- Multi-layer boards (up to 40+ layers)
- High-density interconnect (HDI) boards
- Flexible and rigid-flex PCBs
- Metal core PCBs
- RF and microwave PCBs
PCB Assembly (PCBA) Services
PCB assembly is the process of populating the bare circuit board with electronic components such as ICs, resistors, capacitors, and connectors.
The two main types of PCB assembly are:
- Through-hole assembly: Inserting component leads through holes in the board and soldering them to pads on the opposite side using wave soldering or selective soldering processes.
- Surface-mount assembly: Placing components directly onto pads on the surface of the board and soldering them using reflow soldering processes.
The key steps in PCB assembly include:
- Solder paste printing: Applying a thin layer of solder paste to the pads on the board using a stencil and automated printing machine.
- Component placement: Picking and placing components onto the solder paste using high-speed pick-and-place machines or robotic assembly cells.
- Reflow soldering: Passing the board through a reflow oven to melt the solder paste and form permanent solder joints between the components and pads.
- Inspection: Visually inspecting the assembled boards for defects such as missing components, improper placement, or solder bridges using automated optical inspection (AOI) equipment.
- Rework and repair: Manually repairing any defects identified during inspection using soldering irons, hot air rework stations, or other specialized tools.
- Conformal coating: Applying a protective coating to the assembled board to provide insulation, moisture resistance, and mechanical protection.
EMS providers use a variety of PCBA equipment and processes to accommodate different component types, board sizes, and production volumes. They also have the ability to handle complex assemblies with high component densities, fine pitch devices, and advanced packaging technologies.
Testing and Quality Control Services
Testing and quality control are critical aspects of the EMS process that ensure the manufactured products meet the required specifications, functionality, and reliability standards.
EMS providers offer a comprehensive range of testing and quality control services including:
- In-circuit testing (ICT): Verifying the presence, orientation, and value of components using a bed-of-nails test fixture and automated test equipment (ATE).
- Flying probe testing: Testing individual components and traces using movable probes instead of a fixed test fixture.
- Functional testing: Verifying the functionality and performance of the assembled product using custom test fixtures and software.
- Boundary scan testing: Testing the interconnects and functionality of digital components using built-in test access ports (TAPs) and JTAG test equipment.
- Burn-in testing: Subjecting the products to elevated temperatures and voltages to identify early failures and improve reliability.
- Environmental testing: Testing the products under various environmental conditions such as temperature, humidity, vibration, and shock to ensure they meet the required environmental specifications.
- Automated optical inspection (AOI): Inspecting the assembled boards for manufacturing defects such as missing components, improper placement, or solder bridges using machine vision systems.
- X-ray inspection: Inspecting the internal structure of the assembled boards for defects such as voids, cracks, or short circuits using X-ray imaging equipment.
EMS providers also implement various quality management systems and standards such as ISO 9001, IATF 16949, AS9100, and IPC standards to ensure consistent and reliable quality across their operations.
Supply Chain Management Services
Supply chain management is a critical aspect of EMS that involves sourcing, purchasing, storing, and managing the flow of components and materials needed for PCB manufacturing and assembly.
EMS providers offer a range of supply chain management services including:
- Component sourcing: Identifying and selecting the best suppliers for each component based on cost, quality, availability, and lead time.
- Vendor management: Managing relationships with suppliers to ensure timely delivery, consistent quality, and favorable pricing.
- Inventory management: Maintaining optimal levels of inventory to meet production demands while minimizing carrying costs and obsolescence risks.
- Logistics and transportation: Coordinating the movement of components and finished products between suppliers, factories, and customers.
- Risk management: Identifying and mitigating supply chain risks such as component shortages, price fluctuations, and geopolitical events.
EMS providers use advanced supply chain management tools and techniques such as enterprise resource planning (ERP) systems, electronic data interchange (EDI), and just-in-time (JIT) inventory management to optimize their supply chain operations and reduce costs.
Aftermarket Services
Aftermarket services are the support and maintenance services provided by EMS companies after the products have been manufactured and shipped to the end customers.
Common aftermarket services offered by EMS providers include:
- Warranty support: Providing repair or replacement services for products that fail within the warranty period.
- Repair and refurbishment: Repairing or refurbishing products that have failed or reached end-of-life to extend their useful life.
- Spare parts management: Maintaining an inventory of spare parts and providing them to customers as needed for repairs and maintenance.
- Technical support: Providing technical assistance and troubleshooting services to customers to help resolve product issues and answer questions.
- Product upgrades and modifications: Offering product upgrades and modifications to improve performance, add new features, or meet changing customer requirements.
Aftermarket services help EMS providers build long-term relationships with their customers and generate additional revenue streams beyond the initial product sale.
Conclusion
EMS PCB is a comprehensive set of services provided by electronics contract manufacturers to help OEMs design, manufacture, and support PCB-based products. By outsourcing these services to an EMS partner, OEMs can reduce costs, improve quality, accelerate time-to-market, and focus on their core competencies.
EMS providers offer a wide range of services across the entire product lifecycle including PCB design, prototyping, fabrication, assembly, testing, supply chain management, and aftermarket support. They invest in advanced equipment, processes, and expertise to provide high-quality and reliable electronics manufacturing services to customers across various industries.
As the electronics industry continues to evolve and become more complex, the role of EMS providers in enabling innovation and driving efficiency will only become more important. OEMs that can effectively leverage the capabilities of their EMS partners will be well-positioned to succeed in the competitive global marketplace.
FAQ
What are the benefits of using an EMS provider for PCB manufacturing?
Using an EMS provider for PCB manufacturing offers several benefits including:
- Access to specialized expertise and advanced manufacturing capabilities
- Reduced capital investment in equipment and facilities
- Improved economies of scale and purchasing power
- Increased flexibility and scalability to meet changing demand
- Faster time-to-market and reduced product development risks
- Improved quality and reliability through standardized processes and controls
How do I choose the right EMS provider for my PCB project?
Choosing the right EMS provider depends on several factors such as:
- Technical capabilities and experience in manufacturing similar products
- Quality management systems and certifications
- Financial stability and business continuity
- Geographical location and logistics capabilities
- Pricing and terms of service
- Cultural fit and communication style
It’s important to conduct thorough due diligence and evaluate multiple providers before making a selection.
What are the different types of PCBs that can be manufactured by EMS providers?
EMS providers can manufacture a wide variety of PCB types including:
- Single-sided boards
- Double-sided boards
- Multi-layer boards (up to 40+ layers)
- High-density interconnect (HDI) boards
- Flexible and rigid-flex PCBs
- Metal core PCBs
- RF and microwave PCBs
The specific capabilities may vary by provider, so it’s important to check with them directly.
What are the key challenges in outsourcing PCB manufacturing to an EMS provider?
Some of the key challenges in outsourcing PCB manufacturing to an EMS provider include:
- Ensuring clear and effective communication of requirements and expectations
- Managing intellectual property and data security risks
- Coordinating complex supply chains and logistics
- Ensuring consistent quality and reliability across multiple production sites and suppliers
- Managing cultural differences and language barriers
- Balancing cost pressures with quality and service requirements
Effective planning, communication, and risk management can help mitigate these challenges.
How can I ensure the quality and reliability of PCBs manufactured by an EMS provider?
There are several ways to ensure the quality and reliability of PCBs manufactured by an EMS provider:
- Conduct thorough due diligence and select a provider with a proven track record of quality and reliability
- Clearly communicate your quality requirements and expectations upfront
- Use industry-standard specifications and design for manufacturability (DFM) guidelines
- Implement robust testing and inspection processes throughout the manufacturing process
- Conduct regular audits and performance reviews of the EMS provider
- Establish clear quality agreements and service level agreements (SLAs) with the provider
- Maintain open and frequent communication to identify and resolve issues quickly
By taking a proactive and collaborative approach to quality management, OEMs can ensure that their EMS-manufactured PCBs meet or exceed their quality and reliability requirements.
Leave a Reply