Understanding the Basics of PCB Layering
Before we delve into the specifics of ELIC PCB, let’s first understand the fundamentals of PCB layering. A printed circuit board consists of multiple layers of conductive copper and insulating material, typically FR-4. These layers are stacked and laminated together to form a complete PCB. The number of layers in a PCB can vary depending on the complexity and requirements of the circuit design.
Types of PCB Layers
- Signal Layers: These layers contain the actual copper traces that carry electrical signals between components on the PCB.
- Power Planes: Dedicated layers that provide a constant voltage supply to the components on the board.
- Ground Planes: Layers that serve as a reference point for electrical signals and help reduce electromagnetic interference (EMI).
Conventional PCB Layer Interconnections
In traditional PCB design, interconnections between layers are achieved through vias. Vias are essentially small holes drilled through the PCB layers and plated with conductive material, allowing signals to pass from one layer to another. There are several types of vias, including:
- Through-hole Vias: These vias go through all layers of the PCB, from top to bottom.
- Blind Vias: Vias that start from either the top or bottom layer and terminate at an inner layer.
- Buried Vias: Vias that connect inner layers without reaching the top or bottom layer.
While vias have been the standard method for layer interconnections, they come with certain limitations, such as:
- Increased board size due to the space required for via placement
- Signal integrity issues, especially at high frequencies
- Manufacturing challenges and higher costs for complex via structures
The Concept of ELIC PCB
ELIC PCB, or Every Layer Interconnection PCB, is an advanced technology that aims to overcome the limitations of traditional via-based interconnections. The core idea behind ELIC is to create interconnections between all layers of the PCB without the need for conventional vias.
How ELIC Works
In an ELIC PCB, the interconnections between layers are achieved through a unique process called “vertical conductive structures” (VCS). These structures are formed by creating precise openings in the insulating layers of the PCB and filling them with conductive material, such as copper or a conductive polymer. The result is a seamless, vertical interconnection that spans all layers of the board.
The ELIC process involves the following steps:
- Layer Stacking: The PCB layers, including signal, power, and ground planes, are stacked together with insulating material between them.
- VCS Formation: Precise openings are created in the insulating layers using advanced laser drilling or photolithography techniques. These openings are then filled with conductive material to form the vertical conductive structures.
- Lamination: The layers are laminated together under high pressure and temperature to form a solid, interconnected structure.
Advantages of ELIC PCB
ELIC PCB offers several significant advantages over traditional via-based interconnections:
- Space Savings: By eliminating the need for conventional vias, ELIC allows for more compact PCB designs, enabling higher component density and smaller board sizes.
- Improved Signal Integrity: The seamless, vertical interconnections in ELIC PCBs minimize signal discontinuities and reflections, resulting in better signal integrity, especially at high frequencies.
- Enhanced Thermal Management: The vertical conductive structures in ELIC PCBs provide an efficient path for heat dissipation, improving the overall thermal management of the board.
- Reduced Manufacturing Complexity: ELIC technology simplifies the PCB manufacturing process by eliminating the need for complex via structures, leading to lower production costs and higher yields.
Applications of ELIC PCB
ELIC PCB technology finds applications in various industries and domains where high-density, high-performance electronic circuits are required. Some of the key application areas include:
- Consumer Electronics: Smartphones, tablets, wearables, and other compact consumer devices can benefit from the space savings and improved performance offered by ELIC PCBs.
- Automotive Electronics: The automotive industry demands reliable, high-performance electronics for advanced driver assistance systems (ADAS), infotainment, and vehicle control. ELIC PCBs can meet these requirements while enabling miniaturization of electronic modules.
- Aerospace and Defense: ELIC technology can be used in aerospace and defense applications that require high-density, high-reliability electronic systems, such as avionics, radar, and communication equipment.
- Medical Devices: The compact size and improved signal integrity of ELIC PCBs make them suitable for medical devices, including implantable electronics, diagnostic equipment, and wearable health monitors.
- Industrial Automation: ELIC PCBs can be employed in industrial automation systems, such as robots, control units, and sensor networks, where space constraints and harsh environments demand robust and reliable electronics.
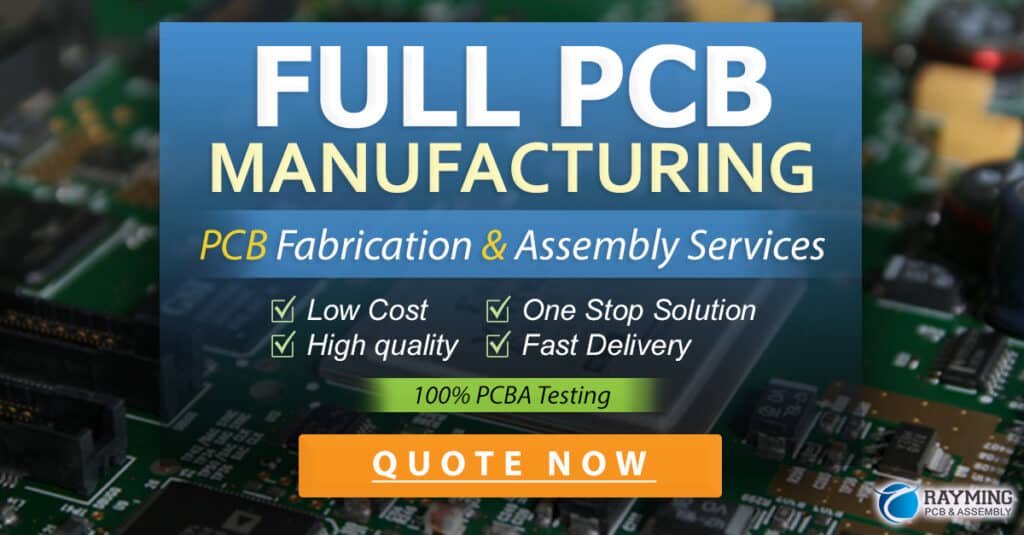
Future of ELIC PCB Technology
As the demand for miniaturization and high-performance electronics continues to grow, ELIC PCB technology is poised to play a significant role in shaping the future of the electronics industry. With ongoing research and development, we can expect further advancements in ELIC technology, including:
- Improved Materials: The development of new conductive materials and insulators with better electrical and thermal properties will enhance the performance and reliability of ELIC PCBs.
- Advanced Manufacturing Techniques: Innovations in laser drilling, photolithography, and other manufacturing processes will enable the creation of even smaller and more precise vertical conductive structures.
- Integration with Other Technologies: ELIC PCBs can be combined with other advanced packaging technologies, such as 3D packaging and system-in-package (SiP), to create highly integrated, multi-functional electronic modules.
- Expanded Applications: As ELIC technology matures, it will find applications in emerging fields, such as 5G communication, artificial intelligence, and the Internet of Things (IoT), where high-density, high-performance electronics are essential.
Frequently Asked Questions (FAQ)
-
What is the main difference between ELIC PCBs and traditional PCBs?
The main difference lies in the way interconnections between layers are achieved. In traditional PCBs, vias are used to connect layers, while ELIC PCBs use vertical conductive structures (VCS) that span all layers without the need for conventional vias. -
What are the benefits of using ELIC technology in PCB design?
ELIC technology offers several benefits, including space savings, improved signal integrity, enhanced thermal management, and reduced manufacturing complexity. These advantages enable the creation of compact, high-performance electronic devices. -
Can ELIC PCBs be manufactured using existing PCB production equipment?
While ELIC PCBs require some specialized equipment for creating the vertical conductive structures, such as advanced laser drilling or photolithography machines, they can be integrated into existing PCB manufacturing processes with appropriate upgrades and modifications. -
Are ELIC PCBs more expensive than traditional PCBs?
Initially, ELIC PCBs may have higher production costs due to the specialized equipment and processes involved. However, as the technology matures and becomes more widely adopted, the cost is expected to decrease, making ELIC PCBs more cost-competitive with traditional PCBs. -
What are some of the key industries that can benefit from ELIC PCB technology?
ELIC PCB technology finds applications in various industries, including consumer electronics, automotive electronics, aerospace and defense, medical devices, and industrial automation. Any industry that requires compact, high-performance electronic circuits can benefit from the advantages offered by ELIC PCBs.
Conclusion
ELIC PCB technology represents a significant advancement in the world of printed circuit board design and manufacturing. By enabling interconnections between all layers without the need for conventional vias, ELIC PCBs offer numerous benefits, such as space savings, improved signal integrity, enhanced thermal management, and reduced manufacturing complexity. As the demand for miniaturization and high-performance electronics continues to grow, ELIC technology is set to play a crucial role in shaping the future of the electronics industry.
With ongoing research and development, we can expect further advancements in ELIC technology, including improved materials, advanced manufacturing techniques, and integration with other cutting-edge technologies. As ELIC PCBs find applications in various industries, from consumer electronics to aerospace and defense, they will undoubtedly contribute to the creation of more compact, efficient, and reliable electronic devices that meet the ever-increasing demands of our technology-driven world.
Aspect | Traditional PCBs | ELIC PCBs |
---|---|---|
Layer Interconnections | Vias | Vertical Conductive Structures (VCS) |
Space Utilization | Less efficient | More efficient |
Signal Integrity | Potential issues at high frequencies | Improved, minimal signal discontinuities |
Thermal Management | Limited | Enhanced, better heat dissipation |
Manufacturing Complexity | Higher, complex via structures | Lower, simplified process |
Cost | Lower | Initially higher, expected to decrease with adoption |
Table 1: Comparison between Traditional PCBs and ELIC PCBs
In conclusion, ELIC PCB technology represents a significant leap forward in the evolution of printed circuit board design and manufacturing. By addressing the limitations of traditional via-based interconnections, ELIC PCBs open up new possibilities for creating compact, high-performance electronic devices that will drive innovation across various industries. As we look towards the future, it is clear that ELIC technology will play a pivotal role in shaping the electronics landscape, enabling the development of groundbreaking products that will transform our lives in countless ways.
Leave a Reply