Introduction to Electronic PCB Assembly
Electronic PCB (Printed Circuit Board) assembly is the process of soldering or mounting electronic components onto a printed circuit board. This process is a crucial step in the manufacturing of electronic devices, as it involves the integration of various components such as resistors, capacitors, transistors, and integrated circuits onto a single board. The assembled PCB forms the backbone of the electronic device, enabling it to perform its intended functions.
The Importance of Electronic PCB Assembly
Electronic PCB assembly plays a vital role in the production of electronic devices across various industries, including:
- Consumer electronics
- Automotive
- Aerospace
- Medical devices
- Telecommunications
- Industrial automation
The proper assembly of PCBs ensures the reliability, functionality, and longevity of the end product. A well-assembled PCB minimizes the risk of device failure, reduces manufacturing costs, and enhances the overall performance of the electronic device.
The PCB Assembly Process
The electronic PCB assembly process typically involves several steps, each of which requires precision and adherence to industry standards. The main stages of PCB assembly include:
1. PCB Design and Fabrication
Before the assembly process can begin, the PCB must be designed and fabricated. This stage involves the creation of a schematic diagram, which outlines the electrical connections between components. The schematic is then used to generate a PCB layout, which defines the physical placement of components and the routing of copper traces on the board. Once the design is finalized, the PCB is fabricated using a variety of techniques, such as etching, drilling, and plating.
2. Solder Paste Application
The first step in the assembly process is the application of solder paste to the PCB. Solder paste is a mixture of tiny solder particles suspended in flux, which helps to clean and protect the metal surfaces during the soldering process. The solder paste is typically applied using a stencil, which is a thin metal sheet with apertures that correspond to the pads on the PCB. The stencil is aligned with the PCB, and the solder paste is spread across the surface using a squeegee.
3. Component Placement
Once the solder paste has been applied, the electronic components are placed onto the PCB. This process can be done manually for small-scale production or prototyping, but it is typically automated for large-scale manufacturing. Automated component placement machines, also known as pick-and-place machines, use computer-controlled robotic arms to pick up components from feeders and place them onto the PCB with high precision and speed.
4. Reflow Soldering
After the components have been placed, the PCB undergoes reflow soldering. In this process, the PCB is passed through a reflow oven, which heats the board to a specific temperature profile. As the temperature rises, the solder paste melts and forms a metallurgical bond between the components and the PCB pads. The temperature is then gradually lowered, allowing the solder to solidify and create a permanent electrical and mechanical connection.
5. Inspection and Testing
Once the soldering process is complete, the assembled PCB undergoes inspection and testing to ensure that it meets the required quality standards. Visual inspection is performed to check for any obvious defects, such as misaligned components, solder bridges, or incomplete solder joints. Automated optical inspection (AOI) systems may also be used to detect more subtle defects that are difficult to spot with the naked eye.
In addition to visual inspection, functional testing is performed to verify that the assembled PCB operates as intended. This may involve using specialized test equipment to measure electrical parameters, such as voltage, current, and resistance, or to simulate the actual operating conditions of the device.
6. Conformal Coating and Final Assembly
Depending on the application and the environmental conditions in which the electronic device will be used, the assembled PCB may require additional protection. Conformal coating is a process in which a thin layer of protective material, such as acrylic, silicone, or polyurethane, is applied to the surface of the PCB. This coating helps to shield the PCB from moisture, dust, and other contaminants that could damage the components or affect the device’s performance.
After the conformal coating process, the assembled PCB is ready for final assembly into the electronic device. This may involve mounting the PCB into an enclosure, connecting it to other subsystems, and performing final functional tests to ensure that the device meets the required specifications.
Types of Electronic PCB Assembly
There are several types of electronic PCB assembly, each with its own advantages and limitations. The choice of assembly method depends on factors such as the complexity of the PCB design, the size and pitch of the components, the production volume, and the available budget. The main types of PCB assembly include:
1. Through-Hole Assembly (THA)
Through-hole assembly is the traditional method of PCB assembly, in which the components have long leads that are inserted through drilled holes in the PCB and soldered to pads on the opposite side. This method is well-suited for larger components and provides a strong mechanical connection. However, through-hole assembly is slower and more labor-intensive than other methods, and it requires more space on the PCB due to the larger hole sizes.
2. Surface Mount Assembly (SMA)
Surface mount assembly is a more modern method of PCB assembly, in which the components are mounted directly onto pads on the surface of the PCB. Surface mount components are smaller and have shorter leads than through-hole components, allowing for higher component density and smaller PCB sizes. Surface mount assembly is faster and more automated than through-hole assembly, making it ideal for high-volume production. However, it requires more precise placement and soldering techniques, and the smaller component sizes can make manual assembly more challenging.
3. Mixed Assembly
Mixed assembly is a combination of through-hole and surface mount assembly, in which both types of components are used on the same PCB. This method allows for the use of specialized or legacy components that may not be available in surface mount packages, while still taking advantage of the benefits of surface mount technology. Mixed assembly can be more complex and time-consuming than either through-hole or surface mount assembly alone, but it offers greater flexibility in PCB design and component selection.
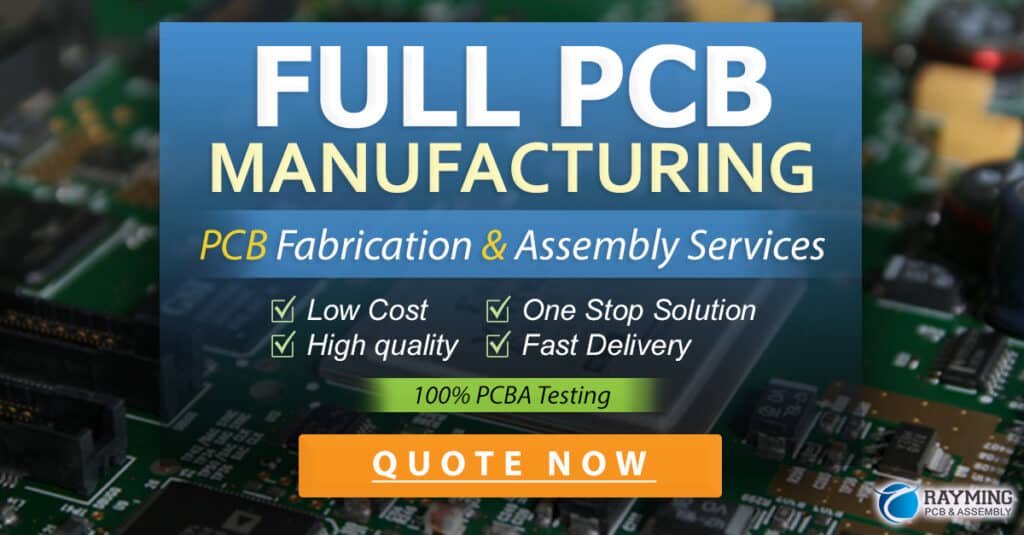
Advantages of Outsourcing Electronic PCB Assembly
Many companies choose to outsource their electronic PCB assembly to specialized contract manufacturers, rather than performing the assembly in-house. Outsourcing PCB assembly offers several advantages, including:
1. Cost Savings
Outsourcing PCB assembly can significantly reduce manufacturing costs, particularly for small to medium-sized businesses. Contract manufacturers have the economies of scale and the specialized equipment necessary to assemble PCBs efficiently and cost-effectively. By outsourcing, companies can avoid the high capital costs of purchasing and maintaining assembly equipment, as well as the labor costs associated with hiring and training assembly technicians.
2. Access to Expertise and Technology
Contract manufacturers specialize in PCB assembly and have the expertise and technology necessary to assemble even the most complex PCB designs. They invest in state-of-the-art equipment and employ experienced technicians who are skilled in the latest assembly techniques. By outsourcing, companies can access this expertise and technology without having to develop it in-house.
3. Faster Time-to-Market
Outsourcing PCB assembly can help companies bring their products to market faster. Contract manufacturers have streamlined assembly processes and can often assemble PCBs more quickly than in-house teams. They also have established relationships with component suppliers and can source components more efficiently, reducing lead times and minimizing supply chain disruptions.
4. Scalability and Flexibility
Outsourcing PCB assembly allows companies to scale their production up or down as needed, without having to invest in additional equipment or personnel. Contract manufacturers can accommodate changes in demand and can quickly ramp up production to meet unexpected spikes in orders. This scalability and flexibility can be particularly valuable for companies with seasonal or cyclical demand patterns.
5. Quality Assurance
Contract manufacturers have rigorous quality control processes in place to ensure that assembled PCBs meet the required specifications. They use automated inspection equipment and follow industry-standard testing procedures to detect and correct any defects or anomalies. By outsourcing, companies can benefit from these quality assurance measures and can have confidence that their PCBs will perform as intended.
Challenges and Considerations in Electronic PCB Assembly
While electronic PCB assembly has many benefits, there are also several challenges and considerations that companies must take into account. These include:
1. Component Availability and Lead Times
One of the biggest challenges in PCB assembly is ensuring the availability of the necessary components. Many electronic components have long lead times, particularly for specialized or custom parts. Companies must carefully plan their production schedules and inventory levels to avoid delays or shortages. They may also need to work closely with their contract manufacturers to identify alternative components or to redesign their PCBs to use more readily available parts.
2. Design for Manufacturability (DFM)
To ensure that PCBs can be assembled efficiently and reliably, companies must design their boards with manufacturability in mind. This involves following best practices for component placement, trace routing, and solder pad design, as well as considering factors such as thermal management and signal integrity. Companies may need to collaborate closely with their contract manufacturers to optimize their PCB designs for assembly and to identify any potential issues before production begins.
3. Intellectual Property Protection
When outsourcing PCB assembly, companies must take steps to protect their intellectual property (IP). This may involve signing non-disclosure agreements (NDAs) with their contract manufacturers, as well as implementing security measures to prevent unauthorized access to sensitive design files or proprietary information. Companies may also need to consider the legal and regulatory requirements for protecting IP in different countries or regions.
4. Supply Chain Management
Effective supply chain management is critical for successful PCB assembly. Companies must select reliable component suppliers and contract manufacturers, and must establish clear communication channels and processes for managing orders, deliveries, and inventory levels. They may also need to monitor market conditions and geopolitical risks that could impact the availability or pricing of components or assembly services.
5. Cost vs. Quality Trade-offs
Finally, companies must carefully balance the trade-offs between cost and quality when outsourcing PCB assembly. While outsourcing can provide significant cost savings, companies must also ensure that their assembled PCBs meet the required quality standards and performance specifications. This may involve investing in additional testing or inspection procedures, or working closely with their contract manufacturers to identify and address any quality issues.
Best Practices for Successful Electronic PCB Assembly
To ensure successful electronic PCB assembly, companies should follow several best practices, including:
1. Early Collaboration with Contract Manufacturers
Companies should engage with their contract manufacturers early in the product development process, ideally during the PCB design phase. This allows the contract manufacturer to provide input on design for manufacturability, component selection, and assembly processes, and can help to identify and resolve any potential issues before production begins.
2. Comprehensive Documentation
Companies should provide their contract manufacturers with comprehensive documentation, including Bill of Materials (BOM), Gerber files, assembly drawings, and test specifications. This documentation should be clear, accurate, and up-to-date, and should include any special instructions or requirements for assembly or testing.
3. Robust Quality Management
Companies should work with their contract manufacturers to establish robust quality management processes, including incoming inspection, in-process monitoring, and final testing. They should also define clear quality metrics and acceptance criteria, and should regularly review quality performance data to identify opportunities for improvement.
4. Effective Communication and Project Management
Effective communication and project management are essential for successful PCB assembly. Companies should establish clear communication channels with their contract manufacturers, including regular status updates and escalation procedures for any issues or delays. They should also assign dedicated project managers to oversee the assembly process and to ensure that milestones are met and deliverables are delivered on time and to specification.
5. Continuous Improvement
Finally, companies should embrace a culture of continuous improvement in their PCB assembly processes. This may involve regularly reviewing performance data, conducting root cause analysis of any issues or defects, and implementing corrective and preventive actions to prevent recurrence. By continuously improving their assembly processes, companies can reduce costs, improve quality, and enhance customer satisfaction.
Frequently Asked Questions (FAQ)
- What is the difference between through-hole and surface mount assembly?
-
Through-hole assembly involves inserting component leads through drilled holes in the PCB and soldering them to pads on the opposite side, while surface mount assembly involves mounting components directly onto pads on the surface of the PCB. Surface mount assembly allows for higher component density and smaller PCB sizes, but requires more precise placement and soldering techniques.
-
What are the advantages of outsourcing electronic PCB assembly?
-
Outsourcing electronic PCB assembly can provide cost savings, access to expertise and technology, faster time-to-market, scalability and flexibility, and quality assurance. Contract manufacturers have the specialized equipment, expertise, and processes necessary to assemble PCBs efficiently and reliably.
-
What are some of the challenges in electronic PCB assembly?
-
Some of the challenges in electronic PCB assembly include component availability and lead times, design for manufacturability, intellectual property protection, supply chain management, and balancing cost and quality trade-offs. Companies must carefully plan and manage their assembly processes to address these challenges and ensure successful outcomes.
-
What are some best practices for successful electronic PCB assembly?
-
Best practices for successful electronic PCB assembly include early collaboration with contract manufacturers, comprehensive documentation, robust quality management, effective communication and project management, and continuous improvement. By following these best practices, companies can optimize their assembly processes and achieve better results.
-
How can companies protect their intellectual property when outsourcing PCB assembly?
- Companies can protect their intellectual property when outsourcing PCB assembly by signing non-disclosure agreements (NDAs) with their contract manufacturers, implementing security measures to prevent unauthorized access to sensitive design files or proprietary information, and considering the legal and regulatory requirements for protecting IP in different countries or regions. They should also work closely with their contract manufacturers to establish clear policies and procedures for handling and protecting IP throughout the assembly process.
Conclusion
Electronic PCB assembly is a critical process in the production of electronic devices, involving the integration of various components onto a single board. Successful PCB assembly requires precision, adherence to industry standards, and careful planning and management of the various stages of the process, from design and fabrication to soldering, inspection, and testing.
Outsourcing PCB assembly to specialized contract manufacturers can provide significant benefits, including cost savings, access to expertise and technology, faster time-to-market, scalability and flexibility, and quality assurance. However, companies must also navigate various challenges and considerations, such as component availability, design for manufacturability, intellectual property protection, supply chain management, and balancing cost and quality trade-offs.
By following best practices such as early collaboration with contract manufacturers, comprehensive documentation, robust quality management, effective communication and project management, and continuous improvement, companies can optimize their PCB assembly processes and achieve better results. As electronic devices continue to evolve and become more complex, the importance of reliable and efficient PCB assembly will only continue to grow, making it a critical area of focus for companies across a wide range of industries.
Leave a Reply