Introduction to Edge Connector Bevelling
Edge connector bevelling is a manufacturing process used to create angled or sloped edges on the ends of printed circuit boards (PCBs). The bevelled edges allow the PCB to be inserted into a mating connector at an angle, providing a secure and reliable electrical connection.
PCBs are flat boards made of insulating material with conductive copper traces printed on the surface. They are used to mechanically support and electrically connect electronic components using conductive pathways, tracks or signal traces etched from copper sheets laminated onto a non-conductive substrate.
Bevelling the edges of the PCB where it will connect to another component is often necessary for proper fit and function. The angled edges guide the board into place and provide a lead-in for the mating connector.
How Edge Connector Bevelling Works
Edge connector bevelling is typically performed using specialized equipment that grinds or cuts the edges of the PCB at a precise angle. The most common methods are:
Mechanical Bevelling
Mechanical bevelling uses physical abrasion to grind down the PCB edges to the desired angle. The board is fed through a machine with angled grinding wheels or belts that remove material from the edges. Key aspects of mechanical bevelling include:
- Grinding wheels are positioned at the specific angle required for the application
- Multiple passes may be needed to achieve the full bevel depth
- Depth stops ensure a consistent bevel profile across the edge
- Coolant is used to manage heat and prevent damaging the PCB
Laser Bevelling
Laser bevelling uses a focused beam of light to vaporize the PCB material and create the angled edge. A high-powered laser is directed at the edge of the board and traced along the length to profile the bevel. Advantages of laser bevelling include:
- Non-contact process eliminates physical stresses on the board
- Highly precise control over bevel angle and depth
- Reduced risk of cracking or delaminating sensitive PCB materials
- Minimal debris and no coolant requirements
V-Scoring
V-scoring is a technique that cuts a V-shaped groove along the length of the PCB edge. The board can then be snapped along this groove to create a rough bevelled edge. V-scoring is often used for:
- Panelized PCB arrays that need to be depanelized after assembly
- Protototyping and low-volume production runs
- Applications where the precision of mechanical or laser bevelling is not required
Key Parameters of Edge Connector Bevels
There are several key parameters that define an edge connector bevel. The specific dimensions are dictated by the requirements of the mating connector.
Parameter | Description |
---|---|
Angle | The angle of the bevel relative to the PCB surface, typically 20-45°. |
Depth | The perpendicular distance from the tip of the bevel to the board edge, typically 0.2-2 mm. |
Length | The distance along the edge that is bevelled, may be the full edge or just a central portion. |
Backcut | An optional secondary angle machined into the back of the bevel to aid alignment. |
Getting these parameters right is critical for proper fit and function of the final assembled product. The connector manufacturer will specify the required bevel dimensions.
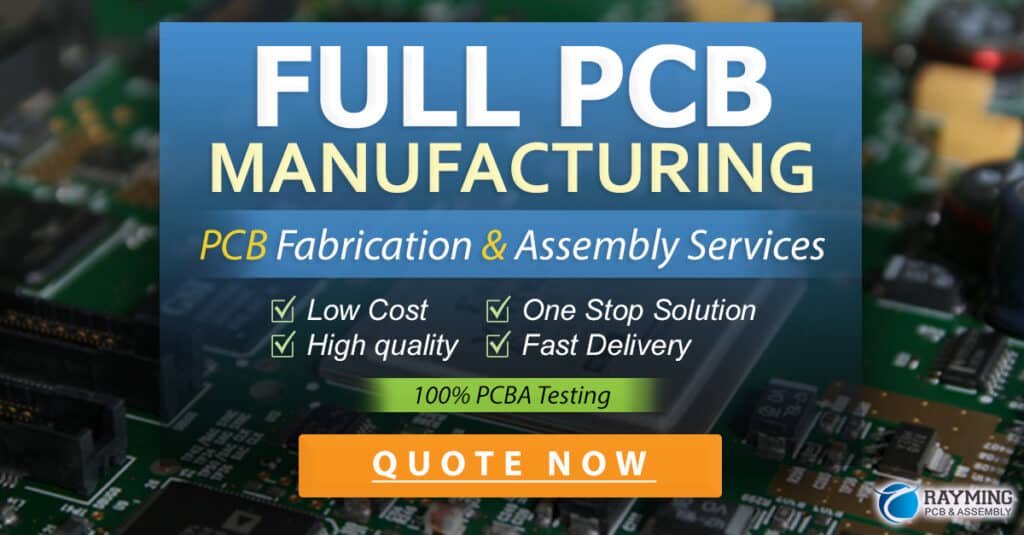
Benefits of Bevelled Edge Connectors
Creating a bevelled edge connector offers several benefits over a simple straight edge:
Easier Insertion
The angled lead-in of the bevel helps guide the PCB into the mating connector. This reduces the risk of misalignment and makes the assembly process easier, especially for manual insertion.
Reduced Wear
The bevel provides a smooth transition into the connector, reducing wear on the connector contacts over repeated insertion cycles. This improves reliability of the final product.
Better Contact Wipe
As the bevelled edge slides into the connector, it creates a wiping action across the contacts. This helps clear away any contamination or oxidation, ensuring a good electrical connection.
Controlled Insertion Depth
The bevel depth acts as a hard stop to control how far the PCB is inserted into the connector. This ensures the board is seated properly every time.
Applications of Bevelled Edge Connectors
PCBs with bevelled edge connectors are used in a wide range of industries and applications, such as:
Consumer Electronics
Many consumer devices use edge connector PCBs, including:
- SD memory cards
- SIM cards for mobile phones
- Video game cartridges
- USB flash drives
Industrial Automation
Bevelled edge PCBs are widely used in industrial control systems for:
- Programmable logic controllers (PLCs)
- Human-machine interfaces (HMIs)
- Motor drives and power electronics
- Sensor and I/O modules
Medical Devices
Medical electronics often utilize edge connector PCBs for:
- Monitoring and diagnostic equipment
- Ultrasound and imaging systems
- Patient worn devices
- Disposable sensor connections
Automotive
Bevelled edge PCBs are found in various automotive electronic systems, such as:
- Engine control units
- Body control modules
- Infotainment and navigation systems
- Driver assistance sensors
Best Practices for Edge Connector Bevelling
To ensure the best results when bevelling PCBs for edge connector applications:
Follow Manufacturer Specifications
Always adhere to the connector manufacturer’s recommended specifications for bevel angle, depth, and other parameters. If in doubt, consult with the connector supplier.
Consider PCB Material
Some PCB materials are more prone to cracking or delamination during bevelling, especially with mechanical processes. Select a material that is compatible with the bevelling method being used.
Provide Proper Support
The PCB must be adequately supported during bevelling to prevent damage. Use fixtures that provide even support across the board and avoid flexing.
Control Dust and Debris
Bevelling can create dust that may contaminate the PCB surface. Use vacuum shrouds and dust collection systems to minimize debris.
Inspect Finished Bevels
Visually inspect the bevelled edges for consistency and any signs of damage. Cross-section a sample of boards to verify bevel depth and profile.
Frequently Asked Questions
What is the most common bevel angle for edge connectors?
The most common bevel angle is 30°, but angles can range from 20-45° depending on the specific connector. Always refer to the manufacturer’s specifications.
Can bevelling be performed on assembled PCBs?
It is preferable to bevel the PCB edges prior to assembly to avoid damaging components. If bevelling after assembly is necessary, components must be a safe distance from the bevelled edge.
How does edge bevelling affect signal integrity?
Properly bevelled edges should not have a significant impact on signal integrity. However, poor quality bevelling that leaves a rough or inconsistent edge can lead to signal reflections or crosstalk.
Are there any industry standards for PCB edge bevelling?
Specific bevel dimensions will vary by manufacturer, but the IPC (Association Connecting Electronics Industries) does provide general guidelines for edge board connectors in the IPC-2223 standard on PCB design.
What is the typical cost of edge bevelling?
The cost of bevelling will depend on factors such as PCB material, bevel specifications, and production volume. In general, laser bevelling has a higher upfront cost but can be more economical for high-volume production, while mechanical bevelling has a lower initial cost but higher operating costs.
Conclusion
Edge connector bevelling is a critical process for creating reliable and robust connections between PCBs and mating connectors. By providing a smooth, angled lead-in, bevelled edges help guide the board into position, reduce wear, and ensure proper electrical contact.
As electronic devices continue to get smaller and more complex, the demand for high-density interconnects and compact packaging will only increase. Bevelled edge connectors offer a proven solution for a wide range of industries and applications.
When designing a PCB for an edge connector application, it is important to work closely with the connector manufacturer to ensure the bevel specifications are correct. Proper material selection, careful process control, and thorough inspection are also key to achieving consistent, high-quality results.
As technology continues to evolve, it is likely that new bevelling methods and connector designs will emerge to meet the ever-changing needs of the electronics industry. But the fundamental benefits of edge connector bevelling – easier assembly, improved reliability, and better performance – will continue to make it an essential technique for PCB fabrication.
Leave a Reply