Composition of Copper PCBs
Substrate Material
The base material of a copper PCB is typically a dielectric substrate, which is an insulating material that does not conduct electricity. The most common substrate materials used in PCB manufacturing are:
- FR-4: A composite material made of woven fiberglass cloth and epoxy resin. It offers good mechanical strength, electrical insulation, and heat resistance.
- CEM-1 and CEM-3: Composite epoxy materials that use a combination of woven fiberglass and paper reinforcement. They are less expensive than FR-4 but have lower performance characteristics.
- Polyimide: A high-performance substrate material that offers excellent thermal stability, making it suitable for applications with high operating temperatures.
Copper Layers
Copper foil is laminated onto one or both sides of the substrate material to create conductive paths for electrical signals. The thickness of the copper layer is measured in ounces (oz) per square foot, with common thicknesses being:
- 0.5 oz (17 μm)
- 1 oz (35 μm)
- 2 oz (70 μm)
Thicker copper layers are used for high-current applications or to improve heat dissipation.
PCB Manufacturing Process
The manufacturing process for copper PCBs involves several steps:
-
Design: The PCB layout is designed using specialized software, taking into account the placement of components, routing of traces, and adherence to design rules.
-
Fabrication: The designed layout is used to create a photomask, which is then used to transfer the pattern onto the copper-clad substrate through a photolithography process. The unwanted copper is etched away, leaving the desired conductive traces.
-
Drilling: Holes are drilled into the PCB to accommodate through-hole components and provide interconnections between layers in multi-layer boards.
-
Plating: The drilled holes are plated with copper to create electrical connections between layers. Additional surface finishes, such as solder mask and silkscreen, are applied to protect the copper traces and provide labeling for assembly.
-
Assembly: Electronic components are soldered onto the PCB, either through wave soldering for through-hole components or surface mount technology (SMT) for surface-mount devices.
-
Testing and Inspection: The assembled PCB undergoes various tests, such as automated optical inspection (AOI) and electrical testing, to ensure proper functionality and quality.
Types of Copper PCBs
Copper PCBs can be categorized based on the number of layers and the density of components:
Single-Layer PCBs
Single-layer PCBs have copper traces on only one side of the substrate. They are the simplest and most cost-effective option but are limited in terms of component density and routing complexity.
Double-Layer PCBs
Double-layer PCBs have copper traces on both sides of the substrate, allowing for higher component density and more complex routing compared to single-layer boards. They are commonly used in a wide range of electronic devices.
Multi-Layer PCBs
Multi-layer PCBs consist of three or more conductive layers, with insulating layers sandwiched between them. They offer the highest level of component density and routing complexity, making them suitable for advanced electronic systems. The number of layers can range from four to over thirty in some high-end applications.
PCB Type | Layers | Component Density | Routing Complexity | Cost |
---|---|---|---|---|
Single-Layer | 1 | Low | Low | $ |
Double-Layer | 2 | Medium | Medium | $$ |
Multi-Layer | 3+ | High | High | $$$ |
High Density Interconnect (HDI) PCBs
HDI PCBs are a type of multi-layer board that features fine pitch traces, small vias, and high component density. They are used in applications that require miniaturization, such as smartphones, wearables, and high-performance computing.
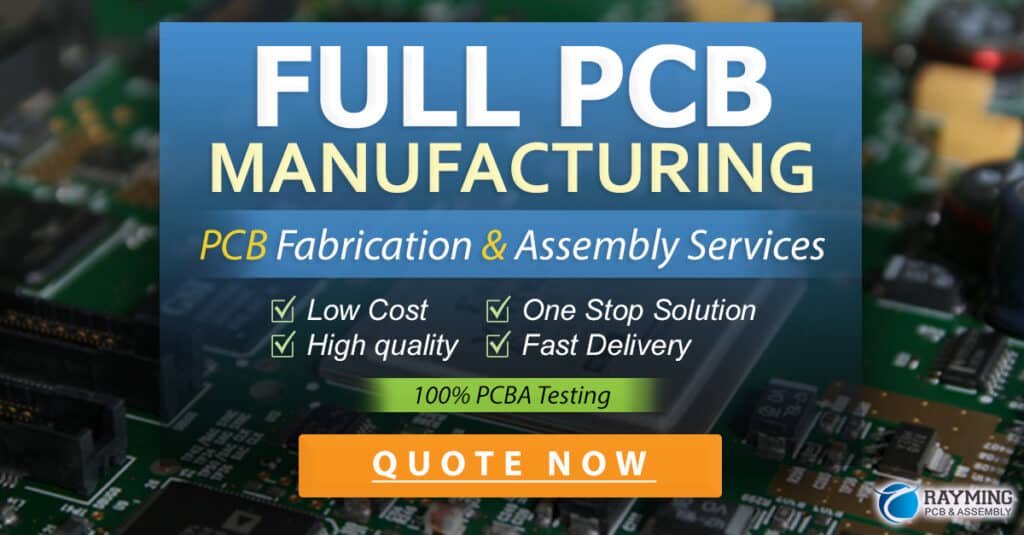
Applications of Copper PCBs
Copper PCBs find applications in virtually every electronic device and system. Some common applications include:
- Consumer electronics (smartphones, laptops, televisions)
- Automotive electronics (infotainment systems, engine control units)
- Industrial automation and control systems
- Medical devices (diagnostic equipment, monitoring systems)
- Aerospace and defense systems
- Internet of Things (IoT) devices
The choice of PCB type and manufacturing process depends on the specific requirements of the application, such as size constraints, performance demands, environmental factors, and cost considerations.
Key Considerations for Copper PCBs
When designing and manufacturing copper PCBs, several key factors must be considered to ensure optimal performance and reliability:
Material Selection
The choice of substrate material and copper thickness should be based on the electrical, thermal, and mechanical requirements of the application. Factors such as dielectric constant, loss tangent, thermal conductivity, and coefficient of thermal expansion (CTE) should be taken into account.
Design Rules
PCB design must adhere to a set of rules that govern aspects such as minimum trace width, spacing between traces, via sizes, and hole-to-copper clearances. These rules ensure manufacturability and help prevent issues such as signal integrity problems and electromagnetic interference (EMI).
Signal Integrity
As signal speeds and frequencies increase, maintaining signal integrity becomes crucial. Proper routing techniques, impedance control, and termination strategies must be employed to minimize signal reflections, crosstalk, and other issues that can degrade performance.
Thermal Management
Copper PCBs must be designed to effectively dissipate heat generated by electronic components. Techniques such as using thicker copper layers, incorporating thermal vias, and optimizing component placement can help improve thermal management.
Manufacturing Considerations
The manufacturability of a PCB design should be considered early in the development process. Factors such as minimum feature sizes, aspect ratios, and tolerances should be discussed with the PCB manufacturer to ensure a design is feasible and cost-effective to produce.
Frequently Asked Questions (FAQ)
- What is the difference between copper PCBs and aluminum PCBs?
Copper PCBs use copper as the conductive material for traces and layers, while aluminum PCBs use aluminum. Copper is the most common choice due to its superior electrical conductivity and thermal performance. Aluminum PCBs are less common and are typically used in specialized applications where weight reduction is a primary concern.
- Can copper PCBs be flexible?
Yes, copper PCBs can be made flexible by using a flexible substrate material, such as polyimide or polyester. Flexible PCBs, also known as flex circuits, are used in applications that require the PCB to bend or conform to a specific shape, such as in wearable devices or compact electronic systems.
- How does the number of layers in a copper PCB affect its performance?
Increasing the number of layers in a copper PCB allows for higher component density and more complex routing. Multi-layer PCBs offer several advantages, such as reduced board size, improved signal integrity, and better power distribution. However, they are also more expensive and complex to manufacture compared to single- or double-layer PCBs.
- What surface finishes are commonly used on copper PCBs?
Common surface finishes for copper PCBs include:
- Hot Air Solder Leveling (HASL): A tin-lead alloy is applied to the copper traces and pads, providing a solderable surface.
- Electroless Nickel Immersion Gold (ENIG): A layer of nickel is plated onto the copper, followed by a thin layer of gold. ENIG offers good solderability and corrosion resistance.
- Immersion Silver: A thin layer of silver is applied to the copper surface, providing good solderability and lower cost compared to ENIG.
-
Organic Solderability Preservative (OSP): An organic compound is applied to the copper surface to protect it from oxidation and maintain solderability.
-
How do I choose the right copper PCB manufacturer?
When selecting a copper PCB manufacturer, consider the following factors:
- Technical capabilities: Ensure the manufacturer has experience with the specific type of PCB you require and can meet your design requirements.
- Quality standards: Look for manufacturers with relevant certifications, such as ISO 9001, and a proven track record of producing high-quality PCBs.
- Lead times: Consider the manufacturer’s lead times and whether they align with your project schedule.
- Cost: Obtain quotes from multiple manufacturers and compare pricing, but be cautious of sacrificing quality for lower costs.
- Communication and support: Choose a manufacturer that is responsive, communicative, and offers technical support throughout the development process.
Conclusion
Copper PCBs are essential components in modern electronics, providing the foundation for the assembly and interconnection of electronic components. Understanding the composition, manufacturing process, and key considerations of copper PCBs is crucial for designing and developing reliable and high-performance electronic systems.
As technology advances and electronic devices become more complex, the demand for advanced copper PCBs with higher layer counts, finer feature sizes, and improved performance will continue to grow. By staying informed about the latest developments in PCB technology and working closely with experienced PCB manufacturers, engineers and designers can create innovative electronic solutions that meet the evolving needs of various industries.
Leave a Reply