Characteristics of Copper Foil
Copper foil possesses several key characteristics that make it an ideal material for numerous applications:
Thickness
Copper foil is available in a range of thicknesses, typically ranging from 0.025mm to 0.1mm (1-4 mils). The thickness of the foil is chosen based on the specific requirements of the application.
Thickness (mm) | Thickness (mils) | Common Applications |
---|---|---|
0.025 | 1 | Flexible circuits, RFID antennas |
0.035 | 1.4 | Printed circuit boards (PCBs) |
0.050 | 2 | Electromagnetic interference (EMI) shielding |
0.070 | 2.8 | High-current applications, busbars |
0.100 | 4 | Heavy-duty electrical connections |
Electrical Conductivity
Copper is an excellent conductor of electricity, second only to silver among pure metals. This high electrical conductivity makes copper foil an ideal choice for applications that require efficient and reliable electrical transmission.
Thermal Conductivity
In addition to its excellent electrical conductivity, copper foil also exhibits high thermal conductivity. This property allows for efficient heat dissipation, which is crucial in electronic devices and electrical equipment to prevent overheating and ensure optimal performance.
Malleability and Ductility
Copper foil is highly malleable and ductile, meaning it can be easily shaped and formed without breaking. This flexibility allows copper foil to be used in applications that require intricate designs or conformity to complex surfaces.
Corrosion Resistance
Copper foil has a natural resistance to corrosion, particularly in dry environments. However, when exposed to moisture and certain chemicals, copper can develop a patina or tarnish over time. To enhance its corrosion resistance, copper foil can be treated with various coatings or alloys.
Manufacturing Process of Copper Foil
The production of copper foil involves several key steps:
1. Electrolytic Deposition
The most common method for manufacturing copper foil is through electrolytic deposition. In this process, a thin layer of copper is deposited onto a rotating stainless steel drum that is immersed in an electrolytic solution containing copper ions. An electric current is applied, causing the copper ions to adhere to the drum surface, forming a thin, continuous sheet of copper foil.
2. Peeling and Trimming
Once the desired thickness of copper foil is achieved, the foil is peeled off the drum and trimmed to the required width. The peeling process must be carefully controlled to ensure a smooth and consistent surface finish.
3. Surface Treatment
Depending on the intended application, the copper foil may undergo various surface treatments to enhance its properties. These treatments can include:
- Electrochemical polishing: Removes surface imperfections and improves smoothness
- Passivation: Applies a protective coating to increase corrosion resistance
- Adhesive coating: Applies a thin layer of adhesive to one side of the foil for bonding purposes
4. Slitting and Packaging
The treated copper foil is then slit into the desired widths and lengths, and packaged for distribution. Proper packaging is essential to protect the foil from damage and contamination during storage and transportation.
Applications of Copper Foil
Copper foil finds use in a wide range of industries and applications, including:
Electronics
Copper foil is a key component in the production of printed circuit boards (PCBs), which are the foundation of modern electronic devices. The foil is laminated onto an insulating substrate, such as fiberglass or epoxy resin, and then etched to create the desired circuit pattern. Copper foil is also used in the manufacture of flexible circuits, RFID antennas, and other electronic components.
Electrical Equipment
Due to its excellent electrical conductivity, copper foil is used in various electrical equipment, such as transformers, motors, and generators. It is also used in the production of busbars, which are thick strips of copper used for high-current applications in switchgear and power distribution systems.
Shielding and Grounding
Copper foil is an effective material for electromagnetic interference (EMI) shielding and grounding. It can be used to line the interior of electronic enclosures, such as computer cases or medical equipment, to prevent electromagnetic radiation from interfering with sensitive components or escaping into the environment.
Decorative Applications
In addition to its functional uses, copper foil is also used for decorative purposes. It can be applied to various surfaces, such as furniture, wall art, and crafts, to create a unique and attractive metallic finish. Copper foil can be embossed, patinated, or colored to achieve different aesthetic effects.
Solar Panels
Copper foil is used in the production of photovoltaic (PV) solar cells, which convert sunlight into electricity. The foil serves as a conductive backing for the PV cells, allowing for efficient collection and transmission of the generated electrical current.
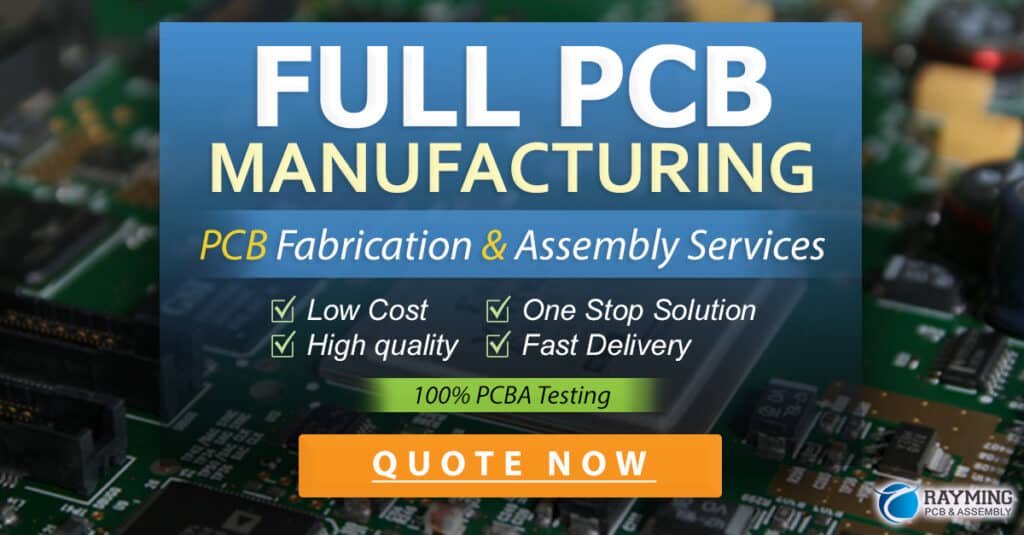
Frequently Asked Questions (FAQ)
1. What is the difference between copper foil and copper sheet?
Copper foil is much thinner than copper sheet, typically ranging from 0.025mm to 0.1mm (1-4 mils) in thickness. Copper sheet, on the other hand, is thicker and more rigid, with thicknesses starting at around 0.15mm (6 mils) and going up to several millimeters.
2. Can copper foil be soldered?
Yes, copper foil can be easily soldered using standard soldering techniques. However, it is important to ensure that the foil surface is clean and free from oxidation or contamination to achieve a strong and reliable solder joint.
3. Is copper foil recyclable?
Yes, copper foil is fully recyclable. In fact, recycling copper is an important aspect of the global copper industry, as it helps to conserve natural resources and reduce environmental impact. Scrap copper foil can be collected, melted down, and reprocessed into new foil or other copper products.
4. How do I choose the right thickness of copper foil for my application?
The choice of copper foil thickness depends on the specific requirements of your application. Factors to consider include the desired electrical and thermal conductivity, mechanical strength, and flexibility. Thinner foils are generally more flexible and suitable for applications such as flexible circuits, while thicker foils offer better conductivity and mechanical stability for high-current or structural applications.
5. Can copper foil be used for RF shielding?
Yes, copper foil is an excellent material for radio frequency (RF) shielding. Its high electrical conductivity and ability to be easily formed and applied to surfaces make it effective at blocking or attenuating RF signals. Copper foil is commonly used to shield sensitive electronic equipment, cables, and enclosures from RF interference.
In conclusion, copper foil is a versatile and essential material with a wide range of applications across various industries. Its unique combination of electrical and thermal conductivity, malleability, and corrosion resistance make it an indispensable component in the production of electronic devices, electrical equipment, and decorative items. As technology continues to advance, the demand for high-quality copper foil is expected to grow, driving innovation in manufacturing processes and expanding the scope of its applications.
Leave a Reply