Understanding Coplanar Waveguides
What is a Coplanar Waveguide?
A coplanar waveguide is a type of planar transmission line that consists of a center conductor strip and two ground planes, all located on the same plane of a dielectric substrate. The center conductor is separated from the ground planes by a narrow gap, which determines the characteristic impedance of the waveguide.
Advantages of Coplanar Waveguides
Coplanar waveguides offer several advantages over other transmission line structures:
-
Low dispersion: CPWs have low dispersion, which means that the phase velocity of the propagating wave remains relatively constant over a wide frequency range. This property makes CPWs suitable for high-frequency applications.
-
Ease of fabrication: CPWs can be easily fabricated using standard photolithography and etching techniques, making them cost-effective and compatible with integrated circuit manufacturing processes.
-
Compatibility with active devices: CPWs can be easily integrated with active devices, such as transistors and diodes, making them suitable for designing monolithic microwave integrated circuits (MMICs).
-
Flexibility in design: The characteristic impedance of a CPW can be easily controlled by adjusting the width of the center conductor and the gap between the conductor and ground planes.
Applications of Coplanar Waveguides
Coplanar waveguides find applications in various high-frequency systems, such as:
- Microwave and millimeter-wave integrated circuits
- Wireless communication systems
- Radar and imaging systems
- High-speed digital circuits
- Microwave filters and couplers
The Need for a Coplanar Waveguide Calculator
Challenges in Designing Coplanar Waveguides
Designing coplanar waveguides for high-frequency applications can be challenging due to several factors:
-
Frequency-dependent behavior: The characteristic impedance and propagation constant of a CPW vary with frequency, making it difficult to maintain a consistent performance over a wide frequency range.
-
Losses and dispersion: CPWs suffer from conductor, dielectric, and radiation losses, which can degrade the signal integrity and limit the transmission distance. Dispersion can also cause signal distortion and limit the bandwidth of the waveguide.
-
Discontinuities and parasitic effects: Discontinuities in the CPW structure, such as bends, T-junctions, and transitions, can introduce parasitic reactances and reflections, which can affect the performance of the waveguide.
Benefits of Using a Coplanar Waveguide Calculator
A coplanar waveguide calculator is an essential tool for addressing the challenges in designing CPWs. The calculator offers several benefits:
-
Accurate and efficient design: The calculator uses precise mathematical models to determine the characteristic impedance, propagation constant, and other parameters of the CPW based on the input dimensions and material properties. This enables designers to quickly and accurately evaluate the performance of different CPW configurations.
-
Optimization of CPW structures: By using the calculator, designers can optimize the dimensions of the CPW to achieve the desired characteristic impedance, minimize losses, and improve the overall performance of the waveguide.
-
Time and cost savings: The calculator eliminates the need for time-consuming and expensive trial-and-error prototyping, reducing the design cycle time and development costs.
-
Improved system performance: By designing CPWs with the help of a calculator, designers can ensure that the waveguides meet the performance requirements of the target application, leading to improved system performance and reliability.
Using a Coplanar Waveguide Calculator
Input Parameters
To use a coplanar waveguide calculator, designers need to provide the following input parameters:
- Center conductor width (w): The width of the center conductor strip.
- Gap width (s): The width of the gap between the center conductor and the ground planes.
- Substrate thickness (h): The thickness of the dielectric substrate.
- Substrate dielectric constant (εr): The relative permittivity of the substrate material.
- Conductor thickness (t): The thickness of the conductor layer.
- Conductor conductivity (σ): The electrical conductivity of the conductor material.
- Frequency range: The range of frequencies over which the CPW will be analyzed.
Output Parameters
Based on the input parameters, the coplanar waveguide calculator provides the following output parameters:
- Characteristic impedance (Z0): The impedance of the CPW that determines the reflection and transmission of the propagating wave.
- Effective dielectric constant (εeff): The effective permittivity of the CPW, which takes into account the fringing fields and the presence of the ground planes.
- Attenuation constant (α): The loss per unit length of the CPW, which includes conductor, dielectric, and radiation losses.
- Phase constant (β): The change in phase per unit length of the CPW, which determines the wavelength and phase velocity of the propagating wave.
- Guided wavelength (λg): The wavelength of the propagating wave in the CPW, which is shorter than the free-space wavelength due to the presence of the dielectric substrate.
Design Guidelines and Best Practices
When using a coplanar waveguide calculator, designers should follow these guidelines and best practices:
- Choose appropriate dimensions: Select the center conductor width and gap width based on the desired characteristic impedance and the fabrication constraints of the target technology.
- Consider substrate properties: Choose a substrate material with a suitable dielectric constant and thickness to achieve the desired performance and compatibility with the fabrication process.
- Minimize losses: Optimize the conductor thickness and conductivity to minimize conductor losses, and choose a low-loss substrate material to minimize dielectric losses.
- Account for discontinuities: Use the calculator to analyze the impact of discontinuities, such as bends and transitions, on the performance of the CPW, and design appropriate compensation structures to minimize their effects.
- Validate the design: Verify the calculated results using electromagnetic simulation tools and perform experimental measurements to ensure that the CPW meets the desired performance specifications.
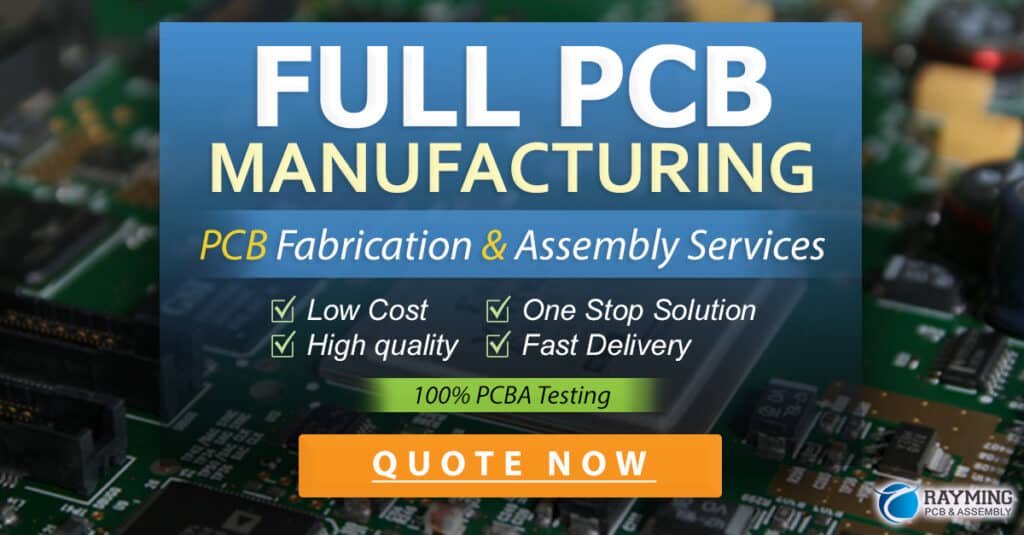
Advanced Topics in Coplanar Waveguide Design
Coplanar Waveguide Filters
Coplanar waveguide filters are essential components in microwave and millimeter-wave systems for selecting desired frequency bands and rejecting unwanted signals. CPW filters can be designed using various topologies, such as:
- Stepped-impedance filters: These filters consist of alternating sections of high and low impedance CPWs, which create resonances at specific frequencies to achieve the desired filter response.
- Coupled-resonator filters: These filters use coupled CPW resonators to create bandpass or bandstop responses, with the coupling strength determining the bandwidth and selectivity of the filter.
- Defected ground structure (DGS) filters: These filters incorporate periodic defects in the ground planes of the CPW to create stopband responses, which can be used for suppressing unwanted harmonics or creating notch filters.
Designers can use a coplanar waveguide calculator in combination with filter synthesis techniques to determine the dimensions and spacing of the CPW sections and resonators to achieve the desired filter response.
Coplanar Waveguide Transitions
Coplanar waveguide transitions are used to interface CPWs with other transmission line structures, such as microstrip lines, striplines, or waveguides. Some common types of CPW transitions include:
- CPW-to-microstrip transitions: These transitions use a tapered center conductor and ground planes to match the impedance and field distribution of the CPW to that of the microstrip line.
- CPW-to-stripline transitions: These transitions use a vertical transition structure, such as a via hole or a metallic post, to connect the center conductor of the CPW to the stripline conductor.
- CPW-to-waveguide transitions: These transitions use a tapered or stepped CPW section to match the impedance and mode of the CPW to that of the waveguide, often using a probe or aperture coupling mechanism.
A coplanar waveguide calculator can be used to optimize the dimensions and taper profiles of the transitions to minimize reflections and losses and ensure a smooth transfer of energy between the different transmission line structures.
Coplanar Waveguide Antennas
Coplanar waveguide antennas are widely used in wireless communication systems due to their planar structure, wide bandwidth, and ease of integration with active devices. Some popular types of CPW antennas include:
- CPW-fed slot antennas: These antennas consist of a slot etched in the ground plane of the CPW, which is excited by the electric field of the CPW mode. The length and width of the slot determine the resonant frequency and radiation pattern of the antenna.
- CPW-fed patch antennas: These antennas use a CPW to feed a patch radiator, which is typically printed on a dielectric substrate. The patch can be of various shapes, such as rectangular, circular, or triangular, to achieve different radiation characteristics.
- CPW-fed monopole antennas: These antennas consist of a monopole radiator, such as a straight wire or a planar structure, which is fed by a CPW. The length of the monopole determines the resonant frequency, and the shape of the radiator can be designed to achieve a desired radiation pattern.
A coplanar waveguide calculator can be used to design the CPW feed network for these antennas, ensuring a good impedance match and minimizing feed line losses. The calculator can also be used to optimize the dimensions of the radiating elements to achieve the desired frequency response and radiation properties.
Coplanar Waveguide Calculator: Frequency Asked Questions (FAQ)
1. What is the difference between a coplanar waveguide and a microstrip line?
A coplanar waveguide (CPW) and a microstrip line are both planar transmission line structures, but they differ in their geometry and field distribution. A CPW consists of a center conductor strip and two ground planes on the same plane of a dielectric substrate, with a narrow gap separating the conductor from the ground planes. In contrast, a microstrip line consists of a conductor strip on one side of a dielectric substrate, with a ground plane on the opposite side.
The main differences between CPWs and microstrip lines are:
- Field distribution: In a CPW, the electric field lines are concentrated in the gaps between the center conductor and the ground planes, while in a microstrip line, the electric field lines are concentrated between the conductor strip and the ground plane.
- Dispersion: CPWs generally have lower dispersion than microstrip lines, making them more suitable for high-frequency applications.
- Characteristic impedance: The characteristic impedance of a CPW is determined by the width of the center conductor and the gap, while in a microstrip line, it is determined by the width of the conductor strip and the thickness and dielectric constant of the substrate.
- Fabrication: CPWs are easier to fabricate than microstrip lines, as they do not require a backside ground plane and can be easily integrated with active devices.
2. How does the substrate dielectric constant affect the performance of a coplanar waveguide?
The substrate dielectric constant (εr) is an important parameter that affects the performance of a coplanar waveguide (CPW). A higher dielectric constant results in a slower propagation velocity, a shorter guided wavelength, and a higher effective dielectric constant (εeff) of the CPW.
The main effects of the substrate dielectric constant on CPW performance are:
-
Characteristic impedance: A higher dielectric constant reduces the characteristic impedance of the CPW for a given center conductor width and gap width. This means that a wider center conductor or a narrower gap is required to achieve the same characteristic impedance on a high-dielectric-constant substrate compared to a low-dielectric-constant substrate.
-
Losses: A higher dielectric constant increases the dielectric losses of the CPW, as a larger fraction of the electric field propagates through the substrate. This can lead to higher attenuation and lower quality factors of CPW resonators and filters.
-
Dispersion: A higher dielectric constant increases the dispersion of the CPW, as the difference between the phase velocity of the propagating wave and the speed of light becomes larger. This can limit the bandwidth and cause signal distortion in high-frequency applications.
-
Radiation: A higher dielectric constant reduces the radiation losses of the CPW, as the fields are more tightly confined to the substrate. This can be advantageous for minimizing crosstalk and interference in densely packed circuits, but it can also make it more difficult to design efficient CPW antennas.
In summary, the choice of the substrate dielectric constant is a trade-off between the characteristic impedance, losses, dispersion, and radiation properties of the CPW. A coplanar waveguide calculator can help designers evaluate the impact of different substrate materials on the performance of the CPW and choose the most suitable one for their application.
3. What are the main sources of loss in a coplanar waveguide, and how can they be minimized?
There are three main sources of loss in a coplanar waveguide (CPW): conductor loss, dielectric loss, and radiation loss. These losses can degrade the signal integrity, reduce the transmission distance, and limit the quality factors of CPW resonators and filters.
- Conductor loss: This loss is caused by the finite conductivity of the center conductor and ground planes of the CPW. As the current flows through the conductors, it experiences resistance, which dissipates power in the form of heat. Conductor loss increases with frequency, as the current becomes more concentrated near the surface of the conductors due to the skin effect.
To minimize conductor loss, designers can:
– Use a high-conductivity material, such as copper or gold, for the conductors.
– Increase the thickness of the conductor layer to reduce the resistance.
– Optimize the width of the center conductor and the gap to reduce the current density and the loss per unit length.
- Dielectric loss: This loss is caused by the dissipation of energy in the dielectric substrate of the CPW. As the electric field propagates through the substrate, it interacts with the dielectric molecules, causing them to oscillate and generate heat. Dielectric loss increases with frequency and is proportional to the loss tangent of the substrate material.
To minimize dielectric loss, designers can:
– Choose a low-loss substrate material, such as quartz, alumina, or high-resistivity silicon.
– Reduce the thickness of the substrate to minimize the volume of the dielectric that interacts with the electric field.
– Use a suspended or elevated CPW structure to reduce the fraction of the electric field that propagates through the substrate.
- Radiation loss: This loss is caused by the leakage of energy from the CPW into the surrounding space in the form of electromagnetic radiation. Radiation loss becomes significant at high frequencies, especially when the dimensions of the CPW become comparable to the wavelength of the propagating wave.
To minimize radiation loss, designers can:
– Use a narrow center conductor and a wide gap to increase the confinement of the fields to the CPW structure.
– Avoid abrupt discontinuities, such as bends or transitions, which can cause radiation and reflections.
– Use a shielded or grounded CPW structure to prevent the leakage of energy into the surrounding space.
A coplanar waveguide calculator can help designers estimate the different types of losses in a CPW based on the dimensions, material properties, and frequency range of interest. By optimizing these parameters, designers can minimize the overall loss and improve the performance of the CPW for their specific application.
4. How can a coplanar waveguide calculator be used to design CPW filters and antennas?
A coplanar waveguide (CPW) calculator is a versatile tool that can be used to design various CPW-based components, such as filters and antennas. By providing the necessary input parameters, such as the dimensions, material properties, and frequency range, designers can use the calculator to determine the characteristic impedance, propagation constant, and other key parameters of the CPW. This information can then be used to design and optimize CPW filters and antennas for specific applications.
Designing CPW filters:
1. Determine the desired filter specifications, such as the center frequency, bandwidth, and type of response (e.g., lowpass, highpass, bandpass, or bandstop).
2. Use filter synthesis techniques, such as the insertion loss method or the coupled-resonator method, to calculate the required coupling coefficients and quality factors of the CPW resonators.
3. Use the CPW calculator to determine the dimensions (center conductor width, gap width, and length) of the CPW resonators that achieve the desired resonant frequency and quality factor.
4. Calculate the spacing between the resonators to achieve the required coupling coefficients, using the CPW calculator to estimate the coupling capacitance or inductance.
5. Optimize the overall filter layout, including the input and output coupling structures, to minimize losses and achieve the desired frequency response.
6. Verify the filter design using electromagnetic simulation tools and refine the dimensions as necessary.
Designing CPW antennas:
1. Determine the desired antenna specifications, such as the operating frequency, bandwidth, gain, and radiation pattern.
2. Choose a suitable CPW antenna topology
Leave a Reply