Introduction to high speed pcb Design
High speed PCB design refers to the design and fabrication of printed circuit boards that are capable of handling high frequency signals and fast data transmission rates. As electronic devices continue to evolve and become more complex, the demand for high speed PCB design has increased significantly. In this article, we will explore what constitutes high speed PCB design, its challenges, and best practices for achieving optimal performance.
What Defines High Speed in PCB Design?
The term “high speed” in PCB design is relative and can vary depending on the application and industry. However, generally speaking, high speed PCB design involves dealing with signals that have rise times shorter than 1 nanosecond (ns) or frequencies higher than 100 MHz. These high speed signals are more susceptible to various issues such as signal integrity, electromagnetic interference (EMI), and crosstalk, which can negatively impact the performance of the PCB.
Challenges in High Speed PCB Design
Designing high speed PCBs presents several challenges that must be addressed to ensure optimal performance and reliability. Some of the main challenges include:
-
Signal Integrity: High speed signals are more vulnerable to distortion, reflection, and attenuation, which can compromise signal integrity and lead to data errors.
-
Electromagnetic Interference (EMI): High speed signals can generate unwanted electromagnetic radiation that can interfere with other electronic devices and cause compliance issues.
-
Crosstalk: When high speed signals travel through adjacent traces, they can induce unwanted signals in neighboring traces, leading to crosstalk and signal degradation.
-
Power Integrity: High speed devices often require clean and stable power supplies to maintain signal integrity and prevent power-related issues.
Key Aspects of High Speed PCB Design
To successfully design high speed PCBs, several key aspects must be considered and optimized. These include:
Material Selection
Choosing the right PCB materials is crucial for high speed design. The dielectric constant (Dk) and dissipation factor (Df) of the substrate material can significantly impact signal propagation and loss. Low-loss materials with stable Dk and Df values across the desired frequency range are preferred for high speed applications. Some common high speed PCB materials include:
- FR-4: A cost-effective and widely used material suitable for frequencies up to a few GHz.
- Rogers RO4000 series: Low-loss, high-frequency laminates ideal for applications up to 30 GHz.
- Isola I-Speed: A low-loss, high-speed laminate designed for data rates up to 25 Gbps.
Stackup Design
The PCB stackup plays a vital role in high speed design, as it determines the impedance of the traces and the overall signal integrity. A well-designed stackup should:
- Minimize signal reflections by maintaining consistent impedance throughout the signal path.
- Provide adequate power and ground planes to minimize noise and ensure power integrity.
- Use appropriate dielectric materials and thicknesses to control impedance and minimize signal loss.
Here’s an example of a high speed PCB stackup:
Layer | Material | Thickness (mm) | Purpose |
---|---|---|---|
1 | Copper | 0.035 | Signal |
2 | FR-4 | 0.2 | Core |
3 | Copper | 0.035 | Ground |
4 | FR-4 | 0.2 | Core |
5 | Copper | 0.035 | Signal |
6 | FR-4 | 0.2 | Core |
7 | Copper | 0.035 | Power |
8 | FR-4 | 0.2 | Core |
9 | Copper | 0.035 | Signal |
Controlled Impedance Routing
Controlling the impedance of the traces is essential for maintaining signal integrity in high speed PCBs. The characteristic impedance of a trace depends on factors such as the trace width, thickness, spacing, and the dielectric constant of the substrate material. To achieve controlled impedance, designers must:
- Calculate the required trace dimensions based on the target impedance and stackup parameters.
- Route traces with consistent widths and spacings to maintain the desired impedance throughout the signal path.
- Avoid abrupt changes in trace geometry, such as sharp bends or discontinuities, which can cause impedance mismatches and signal reflections.
Length Matching and Timing
In high speed designs, it is crucial to ensure that signals arrive at their destinations at the correct time to maintain proper system operation. Length matching and timing control techniques are used to achieve this:
-
Length Matching: Traces carrying related signals (e.g., differential pairs or bus signals) should be matched in length to minimize skew and ensure synchronous arrival of signals.
-
Delay Tuning: In some cases, intentional delays may be introduced to synchronize signals or compensate for path differences. Techniques such as serpentine routing or delay lines can be used for this purpose.
-
Clock Distribution: In synchronous systems, proper clock distribution is critical for maintaining timing relationships between signals. Techniques such as clock buffering, skew control, and length matching are used to ensure reliable clock distribution.
Crosstalk Mitigation
Crosstalk occurs when signals from one trace induce unwanted signals in adjacent traces, leading to signal degradation and potential data errors. To mitigate crosstalk in high speed PCBs, designers can employ the following techniques:
-
Trace Spacing: Increase the spacing between adjacent traces to reduce the coupling between them. The spacing should be determined based on the signal rise time, frequency, and substrate properties.
-
Guard Traces: Place grounded or unused traces between sensitive signal traces to act as barriers and reduce crosstalk.
-
Differential Signaling: Use differential signaling techniques, such as LVDS or CML, to minimize crosstalk by sending complementary signals over a pair of traces. The induced noise tends to cancel out due to the differential nature of the signals.
Power Integrity
Maintaining power integrity is essential for high speed PCBs to ensure stable and clean power delivery to the components. Power integrity issues can lead to signal degradation, noise, and even device malfunction. To address power integrity, designers should:
-
Power Distribution Network (PDN) Design: Create a robust PDN that provides low-impedance power delivery across the required frequency range. This involves proper placement of power and ground planes, decoupling capacitors, and power connectors.
-
Decoupling: Place decoupling capacitors close to power pins of high speed components to provide local, high-frequency current and minimize power supply noise.
-
Voltage Regulation: Use voltage regulators with adequate bandwidth and transient response to maintain stable voltage levels under dynamic load conditions.
-
Via Placement: Minimize the inductance of power and ground vias by placing them close to the power pins of components and using multiple vias in parallel.
High Speed PCB Layout Techniques
Proper PCB layout is critical for achieving optimal high speed performance. Some key layout techniques include:
Component Placement
- Place high speed components close to their associated connectors or interfaces to minimize trace lengths and signal degradation.
- Group related components together to reduce the overall trace lengths and simplify routing.
- Consider the orientation of components to minimize crosstalk and optimize signal flow.
Routing Techniques
- Use smooth, curved traces instead of sharp angles to minimize reflections and improve signal integrity.
- Avoid routing high speed traces over gaps or splits in the reference plane, as this can cause impedance discontinuities.
- Use via shielding or ground vias to minimize the impact of vias on signal integrity.
Shielding and Grounding
- Implement proper shielding techniques, such as ground planes or shielding cans, to reduce EMI and crosstalk.
- Use a solid ground plane to provide a low-impedance return path for high speed signals.
- Connect shields and ground planes to the system ground using low-impedance connections, such as multiple vias or wide traces.
Signal Integrity Simulation
- Perform pre-layout and post-layout signal integrity simulations to analyze and optimize the high speed design.
- Use tools like Mentor Graphics HyperLynx or Cadence Sigrity to simulate signal behavior, identify potential issues, and validate the design before fabrication.
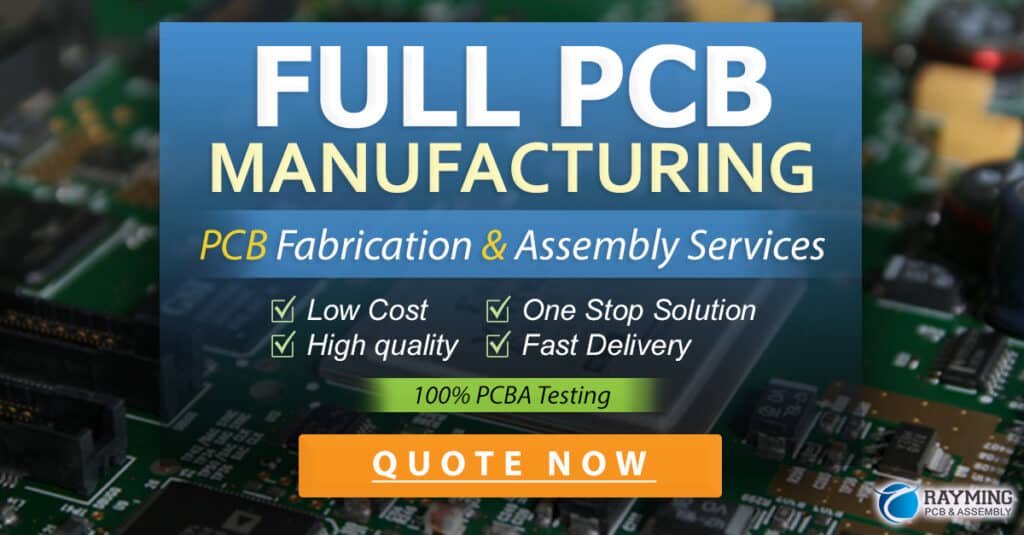
Best Practices for High Speed PCB Design
To ensure the success of high speed PCB designs, follow these best practices:
-
Collaborate with stakeholders: Engage with system architects, component engineers, and signal integrity experts early in the design process to align on requirements and constraints.
-
Define a clear design methodology: Establish a consistent design methodology that includes guidelines for stackup design, routing, component placement, and simulation.
-
Use verified models and libraries: Employ accurate, verified models for components, packages, and interconnects to ensure reliable simulation results.
-
Perform early and frequent simulations: Conduct signal integrity simulations early and often in the design process to identify and address issues before they become costly to fix.
-
Document and communicate: Maintain clear documentation of design decisions, constraints, and guidelines, and communicate them effectively to all team members.
-
Validate and test: Perform thorough validation and testing of the fabricated PCBs to ensure they meet the required specifications and performance criteria.
Frequently Asked Questions (FAQ)
-
What is the difference between high speed PCB design and regular PCB design?
High speed PCB design focuses on managing signal integrity, minimizing crosstalk, and ensuring proper timing for signals with fast rise times and high frequencies. Regular PCB design may not require the same level of attention to these aspects. -
What are the most common challenges in high speed PCB design?
The most common challenges include maintaining signal integrity, minimizing crosstalk and EMI, ensuring power integrity, and achieving proper timing and synchronization of high speed signals. -
What materials are best suited for high speed PCB design?
Low-loss materials with stable dielectric constant (Dk) and dissipation factor (Df) are preferred for high speed PCBs. Examples include Rogers RO4000 series, Isola I-Speed, and Nelco N4000-13SI. -
How can I mitigate crosstalk in high speed PCBs?
Crosstalk can be mitigated by increasing trace spacing, using guard traces, employing differential signaling techniques, and optimizing the PCB stackup and routing. -
What tools are used for high speed PCB design and simulation?
Popular tools for high speed PCB design and simulation include Mentor Graphics HyperLynx, Cadence Sigrity, Ansys SIwave, and Keysight Advanced Design System (ADS).
Conclusion
High speed PCB design is a complex and challenging field that requires careful consideration of signal integrity, power integrity, crosstalk, and timing. By understanding the key aspects of high speed design, such as material selection, stackup design, controlled impedance routing, and layout techniques, designers can create PCBs that meet the demanding requirements of today’s high speed applications.
Successful high speed PCB design relies on a combination of strong technical knowledge, robust design methodologies, and close collaboration between various stakeholders. As the demand for faster and more complex electronic systems continues to grow, the importance of mastering high speed PCB design will only increase.
Leave a Reply