What is a Conformal Coating?
A conformal coating is a thin polymeric film that conforms to the contours of a PCB, including its components and the spaces between them. The primary purpose of using a conformal coating on a PCB is to protect it from environmental factors that could potentially lead to damage or malfunction.
Types of Conformal Coatings
There are several types of conformal coatings available, each with its own unique properties and advantages. The most common types include:
-
Acrylic Resin (AR): Acrylic conformal coatings offer excellent moisture and fungal resistance, as well as good dielectric properties. They are easy to apply and remove, making them a popular choice for many applications.
-
Silicone Resin (SR): Silicone conformal coatings provide excellent temperature and humidity resistance, as well as good flexibility and chemical resistance. They are suitable for high-temperature applications.
-
Polyurethane (UR): Polyurethane conformal coatings offer excellent abrasion and chemical resistance, as well as good dielectric properties. They are ideal for applications that require a tough, durable coating.
-
Epoxy Resin (ER): Epoxy conformal coatings provide excellent chemical and abrasion resistance, as well as good thermal stability. They are suitable for applications that require a high level of protection.
-
Parylene (XY): Parylene conformal coatings are ultra-thin, pinhole-free coatings that offer excellent dielectric properties and chemical resistance. They are applied using a vapor deposition process, resulting in a uniform coating that conforms to the PCB’s surface.
Type | Advantages | Disadvantages |
---|---|---|
Acrylic | Easy to apply and remove, good moisture resistance | Limited temperature range, less durable than other types |
Silicone | Excellent temperature and humidity resistance | Difficult to repair, can be expensive |
Polyurethane | Excellent abrasion and chemical resistance | Can be difficult to apply, limited temperature range |
Epoxy | Excellent chemical and abrasion resistance | Difficult to remove, limited flexibility |
Parylene | Ultra-thin, pinhole-free, excellent dielectric properties | Expensive, requires specialized equipment |
Advantages of Using Conformal Coating on PCBs
Applying a conformal coating to a PCB offers several advantages, making it an essential process for many electronic devices. Some of the key benefits include:
-
Environmental Protection: Conformal coatings protect PCBs from moisture, dust, dirt, and other environmental contaminants that could lead to corrosion or electrical failures.
-
Improved Reliability: By shielding the PCB and its components from harsh conditions, conformal coatings help improve the overall reliability and longevity of electronic devices.
-
Increased Dielectric Strength: Conformal coatings provide an additional layer of insulation, increasing the dielectric strength of the PCB and reducing the risk of electrical shorts or arcing.
-
Better Thermal Stability: Some conformal coatings, such as silicone and epoxy, offer excellent thermal stability, allowing PCBs to operate in high-temperature environments without compromising performance.
-
Enhanced Mechanical Protection: Conformal coatings can provide a degree of mechanical protection, shielding PCBs from vibrations, impacts, and abrasion.
Conformal Coating Application Methods
There are several methods for applying conformal coatings to PCBs, each with its own advantages and disadvantages. The choice of application method depends on factors such as the type of coating, the size and complexity of the PCB, and the required thickness of the coating.
Brush Coating
Brush coating is a manual application method that involves using a brush to apply the conformal coating to the PCB. This method is suitable for small-scale production or touch-up work, as it allows for precise control over the coating application. However, brush coating can be time-consuming and may result in an uneven coating thickness.
Spray Coating
Spray coating involves using a spray gun to apply the conformal coating to the PCB. This method is faster than brush coating and can provide a more uniform coating thickness. There are two main types of spray coating:
-
Conventional Spray Coating: This method uses a compressed air gun to atomize the coating and apply it to the PCB. It is suitable for larger PCBs and can provide a thicker coating than other methods.
-
Aerosol Spray Coating: This method uses a pre-pressurized can containing the conformal coating. It is suitable for smaller PCBs and touch-up work, as it provides a thin, even coating.
Dip Coating
Dip coating involves immersing the PCB in a tank containing the conformal coating. This method is suitable for high-volume production and can provide a uniform coating thickness. However, it may not be suitable for PCBs with complex geometries or components that are sensitive to the coating material.
Selective Coating
Selective coating involves applying the conformal coating only to specific areas of the PCB, such as connectors or components that are particularly sensitive to environmental factors. This method can be achieved using a variety of techniques, such as:
-
Robotic Dispensing: A robotic arm is used to apply the coating to specific areas of the PCB, providing precise control over the coating application.
-
Masking: Areas of the PCB that do not require coating are masked off using tape or other materials, allowing the coating to be applied only to the desired areas.
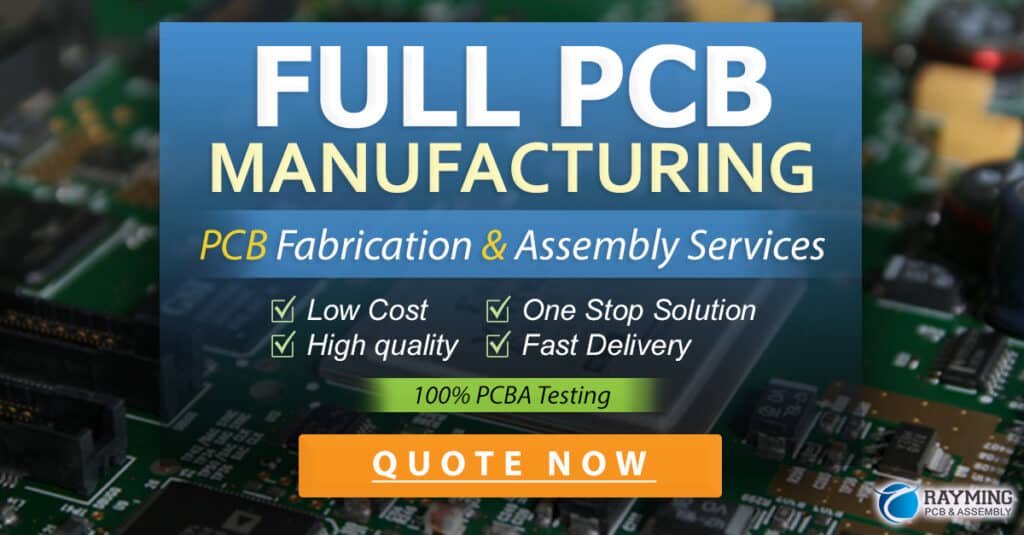
Selecting the Right Conformal Coating
When choosing a conformal coating for a PCB, several factors should be considered to ensure the best performance and protection. These factors include:
-
Environmental Conditions: Consider the environmental conditions the PCB will be exposed to, such as temperature, humidity, and chemical exposure, and choose a coating that offers the necessary protection.
-
Dielectric Properties: Select a coating with suitable dielectric properties to ensure proper insulation and minimize the risk of electrical shorts or arcing.
-
Thickness Requirements: Consider the required thickness of the coating, as this can affect the choice of application method and the overall performance of the coating.
-
Reparability: Some coatings, such as silicone and urethane, can be difficult to repair if damaged. If reparability is a concern, choose a coating that can be easily removed and reapplied.
-
Cost: Conformal coatings vary in price, with some types, such as parylene, being more expensive than others. Consider the cost of the coating in relation to the overall project budget.
Inspecting and Testing Conformal Coatings
After applying a conformal coating to a PCB, it is essential to inspect and test the coating to ensure it meets the required specifications and provides the necessary protection. Some common inspection and testing methods include:
-
Visual Inspection: A visual inspection can help identify any defects in the coating, such as pinholes, bubbles, or uneven coverage.
-
Thickness Measurement: The thickness of the coating can be measured using various techniques, such as eddy current testing or microscopy, to ensure it meets the specified requirements.
-
Adhesion Testing: Adhesion testing can be performed to ensure the coating is properly bonded to the PCB and will not delaminate under stress.
-
Dielectric Withstand Testing: This test involves applying a high voltage to the coated PCB to ensure the coating provides sufficient insulation and does not break down under electrical stress.
-
Environmental Testing: The coated PCB can be subjected to various environmental tests, such as temperature cycling, humidity exposure, or salt spray testing, to evaluate the coating’s performance under harsh conditions.
Frequently Asked Questions (FAQ)
-
Q: What is the purpose of conformal coating on a PCB?
A: The primary purpose of applying a conformal coating to a PCB is to protect it from environmental factors such as moisture, dust, chemicals, and extreme temperatures, which could lead to damage or malfunction. -
Q: Can conformal coating be removed if needed?
A: Yes, most conformal coatings can be removed using various methods, such as solvent stripping, abrasive removal, or thermal decomposition. However, some coatings, like parylene, may be more challenging to remove. -
Q: How does conformal coating affect PCB repair and rework?
A: Conformal coating can make PCB repair and rework more challenging, as the coating must be removed from the affected area before any work can be done. Some coatings, such as acrylic, are easier to remove than others, like silicone or epoxy. -
Q: Is conformal coating necessary for all PCBs?
A: Not all PCBs require conformal coating. The decision to apply a coating depends on the specific application and the environmental conditions the PCB will be exposed to. In some cases, a coating may not be necessary or may even hinder the performance of the device. -
Q: Can conformal coating be applied selectively to specific areas of a PCB?
A: Yes, conformal coating can be applied selectively to specific areas of a PCB using various methods, such as robotic dispensing or masking. This approach can help reduce costs and minimize the impact of the coating on the device’s performance.
Conclusion
Conformal coating for PCB is a critical process that helps protect electronic circuits from harsh environmental conditions, ensuring the reliability and longevity of electronic devices. By understanding the different types of conformal coatings, their advantages and disadvantages, and the various application methods, engineers and manufacturers can select the most suitable coating for their specific application.
Proper inspection and testing of the applied conformal coating are essential to ensure it meets the required specifications and provides the necessary protection. By following best practices and staying up-to-date with the latest advancements in conformal coating technology, manufacturers can produce high-quality, reliable electronic devices that can withstand the rigors of their intended environment.
Leave a Reply