Introduction to Circular PCBs
A circular PCB, or printed circuit board, is a unique type of PCB that has a round shape instead of the more common rectangular or square shapes. These PCBs are designed to fit into specific applications where space is limited or a circular form factor is required. Circular PCBs are used in various industries, including consumer electronics, automotive, aerospace, and medical devices.
Advantages of Circular PCBs
Circular PCBs offer several advantages over traditional rectangular PCBs:
- Space-saving design: The circular shape allows for a more compact design, making it ideal for applications with limited space.
- Enhanced mechanical stability: The circular shape provides better mechanical stability and durability compared to rectangular PCBs.
- Improved thermal management: The circular shape allows for better heat dissipation, which is crucial in high-power applications.
- Aesthetic appeal: Circular PCBs can add a unique and appealing look to the final product.
Manufacturing Process of Circular PCBs
PCB Design Software
Designing a circular PCB requires specialized PCB design software that supports round shapes. Some popular PCB design software options include:
- Altium Designer
- Autodesk Eagle
- KiCad
- OrCAD
These software tools allow designers to create custom circular PCB layouts, define layer stackups, and generate manufacturing files.
PCB Fabrication Techniques
The fabrication process for circular PCBs is similar to that of rectangular PCBs, with a few additional considerations:
- Cutting and routing: Circular PCBs require precise cutting and routing to achieve the desired round shape. This is typically done using CNC machines or laser cutting technology.
- Drilling: Holes for components and vias are drilled into the circular PCB using specialized drilling equipment.
- Plating: The drilled holes are plated with copper to establish electrical connections between layers.
- Solder mask and silkscreen: A protective solder mask layer is applied to the PCB, and silkscreen printing is used to add component labels and other markings.
Assembly and Soldering
Assembling components on a circular PCB requires careful planning and precision:
- Component placement: Components are placed on the circular PCB using pick-and-place machines or manual assembly methods.
- Soldering: Components are soldered to the PCB using reflow soldering or wave soldering techniques.
- Inspection and testing: The assembled circular PCB undergoes visual inspection and electrical testing to ensure proper functionality.
Applications of Circular PCBs
Circular PCBs are used in a wide range of applications across various industries:
Consumer Electronics
- Smartwatches and fitness trackers
- Wireless earbuds and headphones
- Portable speakers and sound systems
Automotive Industry
- Sensor modules for advanced driver assistance systems (ADAS)
- Instrument cluster displays
- Electronic control units (ECUs)
Aerospace and Defense
- Avionics systems
- Satellite communication devices
- Radar and surveillance equipment
Medical Devices
- Wearable health monitoring devices
- Implantable medical devices
- Diagnostic imaging equipment
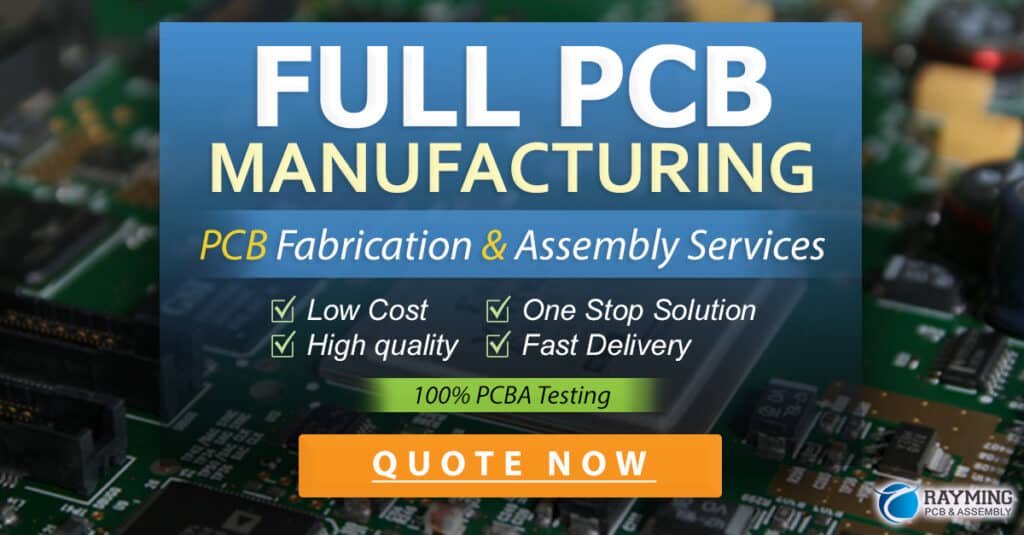
Design Considerations for Circular PCBs
When designing a circular PCB, several factors must be considered to ensure optimal performance and manufacturability:
Component Placement and Routing
- Optimize component placement for minimal board size and improved signal integrity
- Use efficient routing techniques to minimize signal reflections and crosstalk
- Consider the placement of connectors and other external interfaces
Layer Stackup and Via Design
- Choose an appropriate layer stackup based on the application requirements and signal integrity needs
- Optimize via design and placement to minimize signal loss and improve manufacturability
- Consider using blind or buried vias to save space and improve signal routing
Thermal Management
- Incorporate thermal relief pads for components that generate significant heat
- Use copper pours and thermal vias to improve heat dissipation
- Consider using metal core PCBs for high-power applications
Mechanical Considerations
- Ensure the circular PCB design is compatible with the intended enclosure or housing
- Consider the placement of mounting holes and other mechanical features
- Verify the PCB’s mechanical stability and durability under expected operating conditions
Advantages of Using Circular PCBs in Product Design
Incorporating circular PCBs into product design offers several benefits:
- Compact and space-saving design: Circular PCBs enable the development of smaller and more compact devices, which is particularly valuable in portable and wearable applications.
- Enhanced product aesthetics: The unique circular shape of the PCB can contribute to a more appealing and distinctive product design.
- Improved reliability and durability: The circular shape provides better mechanical stability and resistance to vibration and shock, leading to enhanced product reliability.
- Potential for cost savings: By optimizing the PCB design and reducing the overall board size, circular PCBs can help reduce material costs and manufacturing expenses.
Challenges and Limitations of Circular PCBs
While circular PCBs offer many benefits, there are also some challenges and limitations to consider:
- Limited component placement options: The circular shape may restrict the placement of certain components, particularly those with larger footprints or specific orientation requirements.
- Increased design complexity: Designing a circular PCB may require more advanced design skills and specialized software tools compared to traditional rectangular PCBs.
- Higher manufacturing costs: The custom nature of circular PCBs and the need for specialized fabrication techniques can result in higher manufacturing costs compared to standard rectangular PCBs.
- Reduced availability of off-the-shelf components: Some components may not be readily available in packages suitable for circular PCB designs, limiting component selection options.
Best Practices for Circular PCB Design and Manufacturing
To ensure the success of a circular PCB project, consider the following best practices:
- Collaborate closely with the PCB fabricator and assembly provider to ensure the design is manufacturable and meets their capabilities.
- Use appropriate design for manufacturing (DFM) guidelines to minimize potential issues during fabrication and assembly.
- Perform thorough design reviews and simulations to verify signal integrity, thermal performance, and mechanical stability.
- Conduct prototype testing and validation to identify and address any issues before mass production.
- Maintain clear communication and documentation throughout the design and manufacturing process to avoid misunderstandings and delays.
Future Trends and Innovations in Circular PCBs
As technology continues to advance, circular PCBs are expected to evolve and find new applications:
- Miniaturization: The demand for smaller and more compact devices will drive the development of even smaller circular PCBs with higher component densities.
- Flexible and stretchable substrates: The use of flexible and stretchable materials for circular PCBs will enable new applications in wearable electronics and medical devices.
- Advanced manufacturing techniques: The adoption of advanced manufacturing techniques, such as 3D printing and embedded components, will expand the design possibilities for circular PCBs.
- Integration with emerging technologies: Circular PCBs will play a crucial role in the development of new technologies, such as the Internet of Things (IoT), 5G networks, and artificial intelligence (AI) devices.
Frequently Asked Questions (FAQ)
1. What is the minimum size for a circular PCB?
The minimum size for a circular PCB depends on the specific manufacturing capabilities of the PCB fabricator. Generally, circular PCBs can be as small as 5mm in diameter, but it is essential to consult with the fabricator to determine their minimum size requirements.
2. Can circular PCBs have multiple layers?
Yes, circular PCBs can have multiple layers, just like rectangular PCBs. The number of layers depends on the application requirements and the manufacturing capabilities of the PCB fabricator. Multi-layer circular PCBs are commonly used in applications that require high component density or complex signal routing.
3. Are circular PCBs more expensive than rectangular PCBs?
In general, circular PCBs may be more expensive than rectangular PCBs due to the custom nature of their design and the need for specialized fabrication techniques. However, the cost difference can vary depending on factors such as the PCB size, layer count, and production volume. It is essential to obtain quotes from multiple PCB fabricators to compare costs and find the most cost-effective solution for a specific project.
4. What are the common materials used for circular PCBs?
Circular PCBs can be manufactured using the same materials as rectangular PCBs. The most common materials include:
- FR-4: A glass-reinforced epoxy laminate, widely used for its good electrical and mechanical properties.
- High-Tg FR-4: A variant of FR-4 with improved thermal stability, suitable for high-temperature applications.
- Polyimide: A flexible material used for applications that require bendability or high temperature resistance.
- Metal core: A PCB substrate with a metal core, often used for high-power applications that require efficient heat dissipation.
5. Can circular PCBs be used for high-frequency applications?
Yes, circular PCBs can be used for high-frequency applications, such as RF and microwave devices. However, designing circular PCBs for high-frequency applications requires careful consideration of signal integrity, impedance matching, and electromagnetic compatibility (EMC). It is essential to follow best practices for high-frequency PCB design and work closely with experienced PCB designers and fabricators to ensure optimal performance.
Conclusion
Circular PCBs offer unique advantages and opportunities for product design and development. By understanding the manufacturing process, design considerations, and best practices, engineers and designers can successfully incorporate circular PCBs into their projects. As technology advances, circular PCBs are expected to find new applications and drive innovation in various industries.
When considering the use of circular PCBs, it is essential to collaborate with experienced PCB fabricators and assembly providers to ensure the design is manufacturable and meets the desired performance and reliability requirements. By leveraging the benefits of circular PCBs and staying informed about the latest trends and innovations, companies can create compact, reliable, and visually appealing products that stand out in the market.
Leave a Reply