Introduction to ENIG (Electroless Nickel Immersion Gold)
ENIG (Electroless Nickel Immersion Gold), also known as Che Ni/Au, is a surface finish technology widely used in the manufacturing of printed circuit boards (PCBs). This advanced surface finish provides excellent solderability, high reliability, and superior shelf life for PCBs. In this comprehensive article, we will delve into the details of ENIG, its advantages, applications, and the process involved in creating this surface finish.
What is ENIG?
ENIG is a two-layer metallic coating that consists of an electroless nickel layer topped with a thin immersion gold layer. The nickel layer provides a barrier between the copper substrate and the gold layer, preventing the formation of intermetallic compounds that can lead to brittle solder joints. The gold layer, on the other hand, protects the nickel from oxidation and ensures excellent solderability.
Advantages of ENIG
- Excellent solderability
- High reliability
- Superior shelf life
- Flat surface finish
- Suitable for fine-pitch components
- Good thermal and electrical conductivity
- RoHS compliant
The ENIG Process
Step 1: Cleaning and Preparation
Before applying the ENIG surface finish, the PCB undergoes a thorough cleaning process to remove any contaminants, such as dirt, grease, or oxide layers. This step ensures a clean and uniform surface for the subsequent plating processes.
Step 2: Copper Microetching
After cleaning, the PCB is subjected to a microetching process that slightly roughens the copper surface. This step improves the adhesion of the electroless nickel layer to the copper substrate.
Step 3: Electroless Nickel Plating
The PCB is then immersed in an electroless nickel plating solution, which contains nickel ions and a reducing agent. The reducing agent reacts with the nickel ions, causing them to deposit onto the copper surface without the need for an external electrical current. The thickness of the nickel layer typically ranges from 3 to 6 microns.
Step 4: Immersion Gold Plating
Following the electroless nickel plating, the PCB is immersed in an immersion gold plating solution. The gold ions in the solution replace some of the nickel atoms on the surface, creating a thin gold layer with a thickness of 0.05 to 0.2 microns. This gold layer protects the nickel from oxidation and provides excellent solderability.
Step 5: Rinsing and Drying
After the plating processes, the PCB is thoroughly rinsed with deionized water to remove any remaining plating solutions. Finally, the PCB is dried using hot air or an oven to ensure a clean and dry surface finish.
ENIG Applications
ENIG is widely used in various industries due to its excellent properties and reliability. Some of the common applications include:
- Consumer electronics
- Automotive electronics
- Medical devices
- Aerospace and defense
- Telecommunications
- Industrial equipment
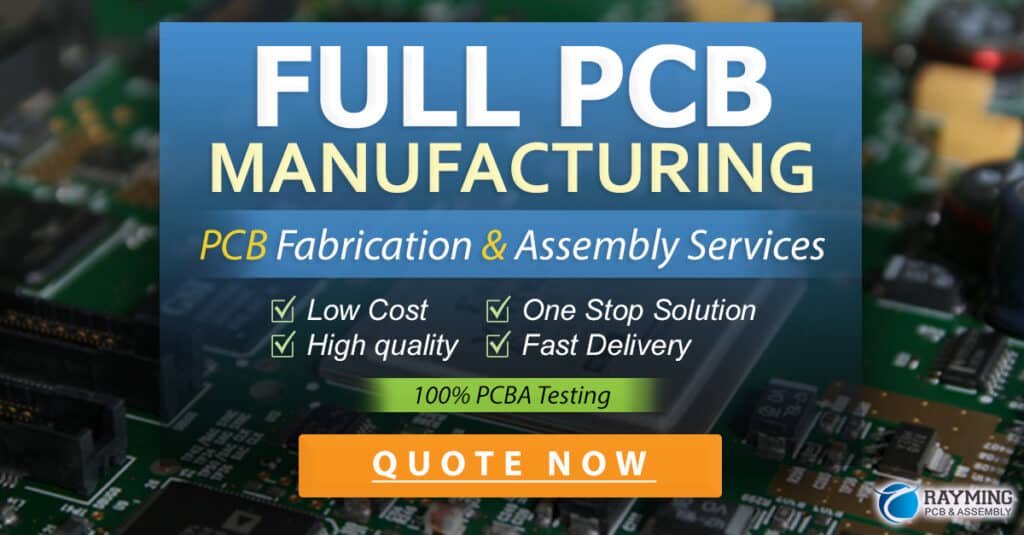
ENIG vs. Other Surface Finishes
ENIG is one of the many surface finishes available for PCBs. Let’s compare ENIG with some of the other popular surface finishes:
ENIG vs. HASL (Hot Air Solder Leveling)
Property | ENIG | HASL |
---|---|---|
Solderability | Excellent | Good |
Shelf Life | 12+ months | 6-12 months |
Surface Flatness | Flat | Uneven |
Fine-Pitch Compatibility | Suitable | Limited |
RoHS Compliance | Yes | Lead-free HASL only |
Cost | Higher than HASL | Lower than ENIG |
ENIG vs. OSP (Organic Solderability Preservative)
Property | ENIG | OSP |
---|---|---|
Solderability | Excellent | Good |
Shelf Life | 12+ months | 3-6 months |
Surface Flatness | Flat | Flat |
Fine-Pitch Compatibility | Suitable | Suitable |
RoHS Compliance | Yes | Yes |
Cost | Higher than OSP | Lower than ENIG |
ENIG vs. Immersion Silver
Property | ENIG | Immersion Silver |
---|---|---|
Solderability | Excellent | Excellent |
Shelf Life | 12+ months | 6-12 months |
Surface Flatness | Flat | Flat |
Fine-Pitch Compatibility | Suitable | Suitable |
RoHS Compliance | Yes | Yes |
Cost | Higher than Immersion Silver | Lower than ENIG |
ENIG Quality Control
To ensure the quality and reliability of ENIG surface finish, several quality control measures are implemented during the manufacturing process:
-
Visual inspection: The PCBs are visually inspected for any defects, such as discoloration, pitting, or uneven plating.
-
Thickness measurement: The thickness of the nickel and gold layers is measured using X-ray fluorescence (XRF) or cross-sectional analysis to ensure they meet the specified requirements.
-
Solderability testing: The solderability of the ENIG surface is tested using wetting balance tests or dip-and-look methods to ensure excellent solder wettability.
-
Adhesion testing: The adhesion between the nickel layer and the copper substrate is tested using peel tests or cross-hatch tests to ensure a strong bond.
-
Porosity testing: The porosity of the nickel layer is tested using porosity tests or corrosion resistance tests to ensure a dense and uniform coating.
ENIG Troubleshooting
Despite the numerous advantages of ENIG, some issues may arise during the manufacturing process. Here are some common problems and their potential solutions:
-
Black pad: Black pad is a defect characterized by the formation of a brittle intermetallic compound between the nickel and gold layers, leading to poor solderability. This issue can be addressed by optimizing the plating process parameters and ensuring proper cleaning and activation of the copper surface.
-
Gold porosity: Excessive porosity in the gold layer can lead to nickel oxidation and poor solderability. This problem can be solved by adjusting the immersion gold plating parameters, such as solution composition, temperature, and immersion time.
-
Nickel corrosion: Nickel corrosion can occur due to inadequate gold coverage or exposure to harsh environments. This issue can be mitigated by ensuring a uniform and sufficient gold layer thickness and using proper storage and handling procedures.
-
Solder mask incompatibility: Some solder mask materials may not adhere well to the ENIG surface, leading to delamination or blistering. This problem can be addressed by selecting compatible solder mask materials and optimizing the solder mask application process.
Future Trends in ENIG
As the electronics industry continues to evolve, so does the development of surface finish technologies. Some of the future trends in ENIG include:
-
Thinner gold layers: To reduce costs and improve the environmental friendliness of the process, there is a trend towards using thinner gold layers (0.05 to 0.1 microns) while maintaining excellent solderability.
-
Alternative nickel alloys: Research is being conducted on alternative nickel alloys, such as nickel-phosphorus-boron (Ni-P-B), which can offer improved mechanical and thermal properties compared to traditional nickel-phosphorus (Ni-P) alloys.
-
Selective ENIG: Selective ENIG is a process where the ENIG surface finish is applied only to specific areas of the PCB, reducing material consumption and costs. This technique is gaining popularity, especially in high-density PCB designs.
-
Environmentally friendly processes: There is a growing demand for more environmentally friendly ENIG processes that minimize the use of hazardous chemicals and reduce waste generation. This includes the development of low-temperature plating solutions and the use of recycled materials.
Frequently Asked Questions (FAQ)
- What is the typical thickness of the nickel and gold layers in ENIG?
-
The typical thickness of the nickel layer is 3 to 6 microns, while the gold layer is usually 0.05 to 0.2 microns thick.
-
How long does ENIG last in storage?
-
ENIG has a shelf life of 12 months or more when stored in proper conditions (e.g., low humidity and temperature).
-
Is ENIG suitable for lead-free soldering?
-
Yes, ENIG is compatible with lead-free soldering processes and is RoHS compliant.
-
Can ENIG be used for wire bonding?
-
Yes, ENIG is suitable for wire bonding applications due to its flat surface and good bondability.
-
How does ENIG compare to other surface finishes in terms of cost?
- ENIG is generally more expensive than HASL and OSP but less expensive than some other surface finishes, such as immersion silver and electroless palladium.
Conclusion
ENIG (Electroless Nickel Immersion Gold) is a highly reliable and versatile surface finish technology that offers excellent solderability, superior shelf life, and compatibility with a wide range of applications. By understanding the ENIG process, its advantages, and potential issues, PCB manufacturers can ensure the production of high-quality PCBs that meet the demanding requirements of various industries. As the electronics industry continues to evolve, advancements in ENIG technology will play a crucial role in enabling the development of more advanced and reliable electronic devices.
Leave a Reply