Understanding the Basics of Castellation
What are Castellated Holes?
Castellated holes, also known as castellations, are semi-circular plated notches or grooves cut into the edges of a PCB. These holes are typically plated with copper and sometimes finished with gold or other surface finishes to enhance conductivity and protect against corrosion. The plating extends from the top surface of the PCB to the bottom, creating an electrical connection point on both sides of the board.
The Purpose of Castellation
The primary purpose of castellation in PCBs is to provide a means of connecting and mounting the board to other PCBs, modules, or components without the need for additional connectors or wires. By aligning the castellated holes of one board with those of another and soldering them together, a secure mechanical and electrical connection is established. This technique is particularly useful in applications where space is limited, as it allows for the stacking of multiple boards and the creation of compact, modular designs.
Advantages of Using Castellated PCBs
1. Space Savings and Miniaturization
One of the main advantages of using castellated PCBs is the ability to save space and achieve miniaturization. By eliminating the need for external connectors and wires, castellated PCBs can be designed with smaller footprints and stacked closely together. This is particularly beneficial in applications where device size is a critical factor, such as wearables, IoT devices, and portable electronics.
2. Improved Mechanical Stability
Castellated PCBs offer improved mechanical stability compared to traditional connector-based designs. The castellated holes provide a larger surface area for soldering, resulting in a stronger and more reliable connection between boards. This increased stability is crucial in applications subject to vibration, shock, or other mechanical stresses, as it helps prevent connection failures and ensures the long-term reliability of the device.
3. Simplified Assembly and Manufacturing
The use of castellated PCBs simplifies the assembly and manufacturing processes. By eliminating the need for external connectors, the number of components required is reduced, leading to faster assembly times and lower manufacturing costs. Additionally, castellated PCBs are compatible with standard SMT (Surface Mount Technology) assembly processes, allowing for automated placement and soldering of components.
4. Enhanced Signal Integrity
Castellated PCBs can help enhance signal integrity by reducing the length of signal paths between boards. By directly connecting the castellated holes of adjacent boards, the signal travel distance is minimized, resulting in reduced signal loss, reflections, and crosstalk. This is particularly important in high-speed digital applications where maintaining signal integrity is critical for proper device functioning.
5. Modular Design Flexibility
Castellation enables modular design approaches, allowing for the creation of stackable and interchangeable PCB modules. This flexibility is advantageous in product development, as it enables the reuse of common modules across different designs, reducing development time and costs. Modular designs also facilitate easier upgrades and maintenance, as individual modules can be replaced without the need to redesign the entire system.
Design Considerations for Castellated PCBs
1. Castellation Hole Dimensions
When designing castellated PCBs, it is essential to consider the dimensions of the castellation holes. The size and spacing of the holes should be carefully chosen based on the requirements of the application, such as the desired board thickness, component sizes, and connection pitch. Standard castellation hole sizes range from 0.5mm to 2.0mm in diameter, with a typical pitch of 1.0mm to 2.54mm.
2. PCB Material Selection
The choice of PCB material is crucial for the successful implementation of castellation. The material should have good mechanical strength to withstand the stresses associated with the castellated edge and the soldering process. Common materials for castellated PCBs include FR-4, Rogers, and polyimide. It is important to select a material that is compatible with the desired plating process and meets the thermal and electrical requirements of the application.
3. Plating and Surface Finish
Proper plating and surface finish are essential for ensuring reliable electrical connections in castellated PCBs. The castellation holes should be plated with copper to provide a conductive path between the top and bottom surfaces of the board. Additional surface finishes, such as gold, silver, or ENIG (Electroless Nickel Immersion Gold), can be applied to improve corrosion resistance and enhance solderability.
4. Solder Mask and Pad Design
The solder mask and pad design around the castellation holes play a crucial role in the assembly process. The solder mask should be designed to expose the necessary amount of copper for soldering while protecting the remaining areas of the PCB. The pad size and shape should be optimized to ensure proper solder joint formation and minimize the risk of bridging or short circuits.
5. Stacking and Alignment Considerations
When designing castellated PCBs for stacking, it is important to consider the alignment and mating of the boards. The castellation holes should be precisely positioned to ensure proper alignment when the boards are stacked together. Additionally, the spacing between the boards should be carefully chosen to accommodate components and provide sufficient clearance for heat dissipation and airflow.
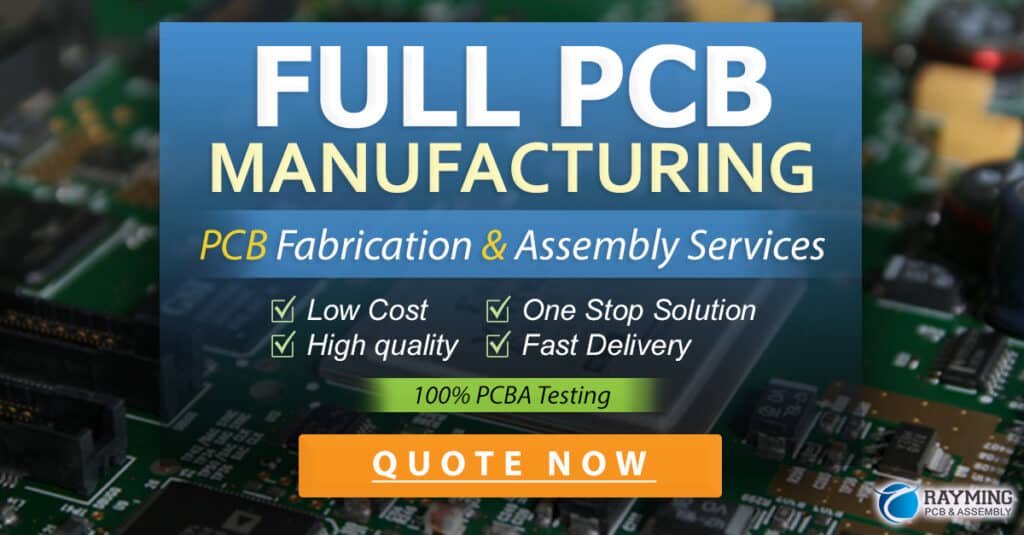
Applications of Castellated PCBs
Castellated PCBs find applications in a wide range of industries and products, including:
- Wearable devices
- Internet of Things (IoT) devices
- Sensor modules
- Wireless communication modules
- Compact industrial controllers
- Automotive electronics
- Medical devices
- Consumer electronics
In each of these applications, the benefits of castellation, such as space savings, improved mechanical stability, and simplified assembly, are leveraged to create compact, reliable, and cost-effective designs.
Castellation vs. Other Connection Methods
Castellated PCBs offer several advantages over alternative connection methods, such as connectors and wire soldering:
Connection Method | Advantages | Disadvantages |
---|---|---|
Castellation | – Space savings – Improved mechanical stability – Simplified assembly – Enhanced signal integrity |
– Requires precise alignment – Limited to board-to-board connections |
Connectors | – Easy to assemble and disassemble – Suitable for board-to-cable connections |
– Increased space requirements – Additional component cost – Potential for contact wear and tear |
Wire Soldering | – Flexibility in routing – Suitable for low-volume production |
– Time-consuming assembly – Prone to human error – Limited mechanical stability |
The choice of connection method depends on the specific requirements of the application, such as space constraints, assembly processes, and the need for modularity or cable connections.
Frequently Asked Questions (FAQ)
1. What is the difference between castellation and edge plating?
Castellation refers to the plated half-circle notches or grooves cut into the edges of a PCB, while edge plating is the process of applying a conductive coating to the entire edge of the board. Castellation provides specific connection points, whereas edge plating offers a continuous conductive surface along the edge.
2. Can castellated PCBs be used for high-current applications?
Yes, castellated PCBs can be used for high-current applications, provided that the castellation holes and plating are designed to handle the required current levels. Factors such as hole size, plating thickness, and copper weight should be considered to ensure adequate current carrying capacity.
3. How does the choice of surface finish affect the performance of castellated PCBs?
The choice of surface finish can impact the solderability, corrosion resistance, and durability of the castellated connections. Common surface finishes include gold, silver, and ENIG. Gold offers excellent corrosion resistance and solderability, while ENIG provides a balance of cost and performance. The selection of surface finish should be based on the specific requirements of the application, such as environmental conditions and storage life.
4. Are there any limitations to the number of boards that can be stacked using castellation?
The number of boards that can be stacked using castellation depends on several factors, including the mechanical stability of the stack, the heat dissipation requirements, and the overall device size constraints. In general, castellated PCBs can be stacked as long as the design ensures proper alignment, sufficient clearance for components, and adequate thermal management.
5. Can castellated PCBs be reworked or repaired?
Castellated PCBs can be reworked or repaired, but the process requires careful handling and specialized techniques. Rework methods may involve the use of hot air, soldering irons, or specialized desoldering tools to remove and replace components or repair damaged castellation holes. It is important to follow proper rework guidelines and use appropriate tools to minimize the risk of further damage to the PCB.
Conclusion
Castellation in PCBs is a valuable technique that offers numerous benefits, including space savings, improved mechanical stability, simplified assembly, and enhanced signal integrity. By creating plated half-circle notches or grooves along the edges of the board, castellated PCBs enable direct board-to-board connections without the need for external connectors or wires. This makes them particularly suitable for applications that require compact, modular, and reliable designs.
When designing castellated PCBs, it is essential to consider factors such as castellation hole dimensions, PCB material selection, plating and surface finish, solder mask and pad design, and stacking and alignment considerations. By carefully addressing these aspects, designers can ensure the optimal performance and reliability of their castellated PCB designs.
Castellated PCBs find applications in various industries, including wearables, IoT devices, automotive electronics, and medical devices. As the demand for miniaturization and modular design continues to grow, the use of castellation in PCBs is expected to increase, driving innovation and enabling the development of more compact and efficient electronic devices.
Leave a Reply