Introduction to Cam Editor Apertures
Cam editor apertures are an essential component in the design and manufacturing of camshafts for internal combustion engines. These apertures, also known as cam windows or cam slots, are precisely cut openings on the camshaft that allow the valve lifters or followers to interact with the cam lobes. The shape, size, and position of these apertures play a crucial role in determining the valve timing, duration, and lift, which ultimately affects the engine’s performance, efficiency, and emissions.
In this article, we will delve into the world of cam editor apertures, exploring their significance, design considerations, manufacturing processes, and optimization techniques. We will also discuss the various tools and software used for cam editor aperture design and analysis, as well as the latest advancements and trends in this field.
The Significance of Cam Editor Apertures
Role in Valve Train System
Cam editor apertures are a critical part of the valve train system in an internal combustion engine. The valve train system is responsible for controlling the opening and closing of the engine’s intake and exhaust valves, which regulate the flow of air and fuel into the combustion chamber and the release of exhaust gases. The camshaft, equipped with carefully designed cam lobes and apertures, acts as the brain of the valve train system, dictating the precise timing and duration of valve events.
Impact on Engine Performance
The design of cam editor apertures directly impacts the engine’s performance characteristics, such as:
- Power output
- Torque
- Fuel efficiency
- Emissions
- Idle quality
- Low-end and high-end performance
By optimizing the cam editor apertures, engineers can fine-tune the engine’s performance to suit specific applications, such as high-performance racing engines, fuel-efficient passenger cars, or heavy-duty industrial engines.
Relationship with Cam Lobe Profile
The cam editor apertures work in conjunction with the cam lobe profile to determine the valve motion. The cam lobe profile defines the shape of the cam lobe, which includes the base circle, ramp, nose, and flank. The aperture’s shape and position relative to the cam lobe profile determine the following:
- Valve lift: The maximum distance the valve opens from its seat
- Valve duration: The total angle of camshaft rotation during which the valve is open
- Valve timing: The point in the engine cycle at which the valve opens and closes
The relationship between the cam lobe profile and the aperture is crucial for achieving the desired valve motion characteristics and optimizing engine performance.
Design Considerations for Cam Editor Apertures
Aperture Shape and Size
The shape and size of the cam editor aperture are critical design factors that influence the valve motion and engine performance. The most common aperture shapes include:
- Rectangular
- Oval
- D-shaped
- Keyhole
- Custom shapes
The choice of aperture shape depends on various factors, such as the desired valve lift, duration, and timing, as well as the constraints imposed by the engine architecture and valve train components.
The size of the aperture, specifically its width and length, determines the maximum valve lift and duration achievable. A wider aperture allows for a higher valve lift, while a longer aperture enables a longer valve duration. However, increasing the aperture size also increases the stress on the valve train components and may lead to issues such as valve float, bounce, or excessive wear.
Aperture Position and Orientation
The position and orientation of the cam editor aperture relative to the cam lobe profile also play a significant role in determining the valve motion characteristics. The key parameters to consider are:
- Aperture offset: The distance between the center of the aperture and the center of the camshaft
- Aperture phase angle: The angular position of the aperture relative to the cam lobe profile
- Aperture tilt angle: The inclination of the aperture relative to the camshaft axis
By adjusting these parameters, engineers can fine-tune the valve opening and closing points, as well as the ramp rates and acceleration profiles, to achieve the desired engine performance and efficiency.
Material Selection and Surface Treatment
The material selection and surface treatment of the camshaft and apertures are essential for ensuring the durability and reliability of the valve train system. Camshafts are typically made from cast iron or forged steel, with the choice depending on factors such as the engine’s operating conditions, production volume, and cost constraints.
Surface treatments, such as hardening, nitridingn, or coatings, are often applied to the cam lobes and apertures to improve their wear resistance, fatigue strength, and lubricity. These treatments help to extend the camshaft’s service life and maintain optimal valve motion characteristics over the engine’s lifespan.
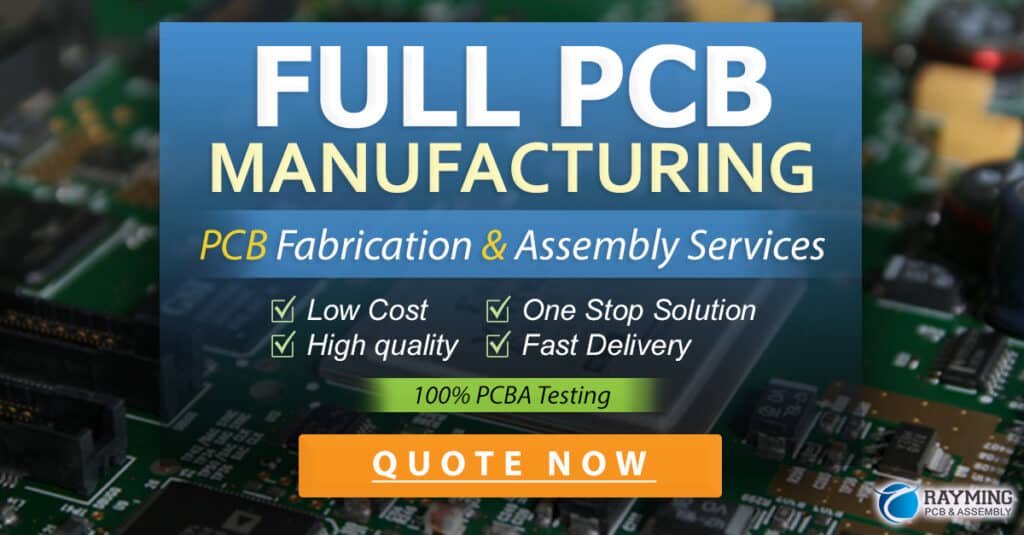
Manufacturing Processes for Cam Editor Apertures
Casting and Forging
Camshafts are typically manufactured using casting or forging processes, depending on the material and production volume. Cast iron camshafts are produced using sand casting or shell molding processes, while forged steel camshafts are made using hammer or press forging techniques.
The cam editor apertures are initially formed during the casting or forging process, with the raw aperture shape and position roughly defined. However, these raw apertures require further machining and finishing to achieve the desired precision and surface quality.
Machining and Finishing
The machining and finishing of cam editor apertures involve several processes, such as:
- Milling: Removing excess material and shaping the aperture to the desired form using a milling machine
- Grinding: Fine-tuning the aperture shape and size using abrasive wheels or belts
- Polishing: Improving the surface finish and removing any burrs or sharp edges
- Superfinishing: Achieving a very smooth surface finish to reduce friction and wear
These machining and finishing processes are critical for ensuring the accuracy and consistency of the cam editor apertures, which directly impact the valve motion and engine performance.
Quality Control and Inspection
Strict quality control and inspection procedures are essential for ensuring that the cam editor apertures meet the required specifications and tolerances. Some of the key quality control methods include:
- Coordinate Measuring Machine (CMM): Measuring the aperture dimensions and positions using a high-precision probe
- Optical Comparator: Comparing the aperture shape and profile against a reference template
- Surface Roughness Tester: Measuring the surface finish and texture of the apertures
- Magnetic Particle Inspection (MPI): Detecting surface and sub-surface cracks or defects
By implementing rigorous quality control and inspection processes, manufacturers can ensure that the cam editor apertures are consistent, reliable, and meet the desired performance standards.
Cam Editor Aperture Design Tools and Software
Computer-Aided Design (CAD) Software
CAD software plays a crucial role in the design and optimization of cam editor apertures. Engineers use CAD tools to create 3D models of the camshaft, cam lobes, and apertures, allowing them to visualize and analyze the valve train system’s geometry and motion.
Some popular CAD software used in the automotive industry include:
- Autodesk Inventor
- SolidWorks
- CATIA
- PTC Creo
- Siemens NX
These CAD tools provide powerful modeling, assembly, and drafting capabilities, enabling engineers to design and refine cam editor apertures efficiently.
Valve Train Simulation Software
Valve train simulation software is used to analyze and optimize the dynamic behavior of the valve train system, including the interaction between the cam lobes, apertures, and valve lifters. These tools allow engineers to predict the valve motion, forces, and stresses under various operating conditions, helping them to identify potential issues and optimize the system’s performance.
Some popular valve train simulation software includes:
- Ricardo VALDYN
- GT-SUITE Valve Train Module
- AVL EXCITE Timing Drive
- LMS Virtual.Lab Motion
- MATLAB Simulink
By using valve train simulation software, engineers can perform virtual testing and optimization of the cam editor apertures, reducing the need for physical prototypes and saving time and cost in the development process.
Finite Element Analysis (FEA) Tools
FEA tools are used to analyze the structural integrity and durability of the camshaft and apertures under various loading conditions. These tools help engineers to predict the stress distribution, fatigue life, and potential failure modes of the components, enabling them to optimize the design for strength and reliability.
Some popular FEA software used in the automotive industry include:
- ANSYS Mechanical
- Altair HyperWorks
- Abaqus
- MSC Nastran
- COMSOL Multiphysics
By applying FEA techniques, engineers can ensure that the cam editor apertures and camshaft can withstand the demanding operating conditions of the engine, reducing the risk of premature failure or performance degradation.
Optimization Techniques for Cam Editor Apertures
Parametric Studies and Sensitivity Analysis
Parametric studies and sensitivity analysis are used to investigate the impact of various design parameters on the performance of the cam editor apertures and valve train system. Engineers vary the aperture shape, size, position, and orientation parameters systematically and analyze their effects on the valve motion, forces, and stresses.
By conducting parametric studies, engineers can identify the most influential design parameters and optimize them for specific performance targets, such as maximizing valve lift, minimizing valve train friction, or improving low-end torque.
Design of Experiments (DOE) and Response Surface Methodology (RSM)
DOE and RSM are statistical techniques used to optimize the cam editor aperture design efficiently. DOE involves planning and conducting a series of experiments or simulations, where multiple design parameters are varied simultaneously to investigate their effects and interactions.
RSM is a technique used to create a mathematical model that relates the design parameters to the performance responses, based on the data obtained from the DOE. This model can be used to predict the performance of the cam editor apertures for any combination of design parameters within the studied range, allowing engineers to identify the optimal design configuration.
By applying DOE and RSM techniques, engineers can reduce the number of iterations required to arrive at the optimal cam editor aperture design, saving time and resources in the development process.
Multi-Objective Optimization and Trade-off Analysis
Multi-objective optimization is used to find the best compromise solution when multiple, often conflicting, performance objectives need to be satisfied simultaneously. In the case of cam editor apertures, engineers may need to optimize the design for maximum valve lift, minimum valve train friction, and maximum durability, among other objectives.
Trade-off analysis is used to investigate the relationships and trade-offs between different performance objectives, helping engineers to make informed decisions when selecting the final design configuration. By visualizing the trade-off frontiers and Pareto-optimal solutions, engineers can identify the best balance of performance attributes that meet the overall system requirements.
Latest Advancements and Trends in Cam Editor Aperture Design
Variable Valve Timing (VVT) and Lift Systems
VVT and lift systems are becoming increasingly popular in modern engines, as they offer greater flexibility in optimizing the valve motion for different operating conditions. These systems use advanced cam editor aperture designs, such as:
- Dual-profile cam lobes
- Concentric cam lobes
- Eccentric cam lobes
- Cam phasers
- Cam profile switching
By incorporating VVT and lift systems, engineers can achieve improved engine performance, fuel efficiency, and emissions across a wide range of engine speeds and loads.
3D Printing and Additive Manufacturing
3D printing and additive manufacturing technologies are emerging as promising alternatives to traditional casting and forging processes for camshaft and aperture production. These technologies offer several advantages, such as:
- Rapid prototyping and iterative design
- Customization and small-batch production
- Complex geometries and lightweight designs
- Material flexibility and multi-material components
By leveraging 3D printing and additive manufacturing, engineers can accelerate the development process, explore novel aperture designs, and optimize the camshaft for specific applications or performance requirements.
Integrated Camshaft and Aperture Design
Integrated camshaft and aperture design is an approach that considers the cam lobes and apertures as a single, holistic system rather than separate components. This approach allows for greater optimization of the valve train system, as the cam lobe profiles and aperture shapes can be co-designed to achieve the desired valve motion characteristics.
By using advanced CAD, simulation, and optimization tools, engineers can develop integrated camshaft and aperture designs that offer improved performance, efficiency, and durability compared to traditional, sequential design approaches.
Frequently Asked Questions (FAQ)
1. What is the difference between a cam editor aperture and a cam lobe?
A cam editor aperture is the opening or window on the camshaft through which the valve lifter or follower interacts with the cam lobe. The cam lobe, on the other hand, is the raised portion of the camshaft that determines the valve lift profile. The aperture and cam lobe work together to control the valve motion.
2. How does the aperture shape affect the valve motion?
The aperture shape influences the valve lift, duration, and timing. For example, a wider aperture allows for a higher maximum valve lift, while a longer aperture enables a longer valve duration. The shape also affects the ramp rates and acceleration profiles of the valve motion, which can impact the engine’s performance and efficiency.
3. What materials are typically used for camshafts and apertures?
Camshafts and apertures are typically made from cast iron or forged steel. Cast iron is more common in lower-performance engines and offers good wear resistance and damping properties. Forged steel is used in high-performance engines and provides higher strength and durability.
4. How are cam editor apertures manufactured?
Cam editor apertures are initially formed during the casting or forging process of the camshaft. They are then further refined through machining and finishing processes, such as milling, grinding, polishing, and superfinishing, to achieve the desired shape, size, and surface quality.
5. What are the latest advancements in cam editor aperture design?
Some of the latest advancements in cam editor aperture design include variable valve timing and lift systems, which use advanced aperture designs to optimize valve motion for different operating conditions. 3D printing and additive manufacturing technologies are also emerging as promising alternatives for camshaft and aperture production, offering greater design flexibility and customization. Additionally, integrated camshaft and aperture design approaches are being developed to optimize the valve train system holistically.
Conclusion
Cam editor apertures are a critical component in the design and performance of internal combustion engines. These precisely engineered openings on the camshaft work in conjunction with the cam lobes to control the valve motion, directly impacting the engine’s power, efficiency, and emissions.
Designing optimal cam editor apertures involves considering various factors, such as the aperture shape, size, position, and orientation, as well as the material selection and surface treatment. Advanced manufacturing processes, quality control methods, and design tools and software are employed to ensure the accuracy, consistency, and reliability of the apertures.
As engine technologies continue to evolve, cam editor aperture design is also advancing, with developments in variable valve timing and lift systems, 3D printing and additive manufacturing, and integrated camshaft and aperture design approaches. These advancements offer engineers new opportunities to optimize the valve train system and achieve higher levels of engine performance and efficiency.
By understanding the significance, design considerations, manufacturing processes, and optimization techniques for cam editor apertures, engineers can develop cutting-edge valve train systems that meet the ever-increasing demands of the automotive industry. As the quest for more efficient, clean, and powerful engines continues, the role of cam editor apertures in shaping the future of internal combustion engines remains crucial.
Leave a Reply