The Role of Signal Harnesses in Buses
Signal harnesses play a crucial role in the overall operation of a bus. They are responsible for transmitting electrical signals and power between various components, ensuring that each system functions as intended. Some of the key systems that rely on signal harnesses include:
- Lighting systems (interior and exterior)
- Audio and visual entertainment systems
- Climate control systems
- Safety features (e.g., cameras, sensors)
- Instrument clusters and dashboard displays
Without properly functioning signal harnesses, these systems would not be able to operate, leading to potential safety hazards and passenger discomfort.
Components of a Bus Signal Harness
A typical bus signal harness consists of several components that work together to ensure reliable signal transmission and power distribution. These components include:
Wires and Cables
The primary component of a signal harness is the network of wires and cables that carry electrical signals and power. These wires are typically made of copper and are insulated to prevent short circuits and interference. The gauge (thickness) of the wires varies depending on the specific application and the amount of current they need to carry.
Connectors
Connectors are used to join different sections of the harness and to connect the harness to various components within the bus. There are several types of connectors used in bus signal harnesses, including:
- Plug and socket connectors
- Crimp connectors
- Solder connectors
- Insulation displacement connectors (IDC)
The choice of connector depends on factors such as the environment, the required connection strength, and the ease of assembly or maintenance.
Terminals
Terminals are the points at which wires are attached to connectors. They provide a secure and reliable connection between the wire and the connector, ensuring that electrical signals are transmitted efficiently. Terminals can be either male or female, depending on the type of connector being used.
Protective Coverings
To protect the wires and cables from damage, abrasion, and environmental factors, signal harnesses are often covered with protective materials. These can include:
- Plastic or rubber insulation
- Braided sleeving
- Heat-shrink tubing
- Convoluted tubing
The choice of protective covering depends on the specific application and the environment in which the harness will be used.
Manufacturing Process of Bus Signal Harnesses
The manufacturing process of bus signal harnesses involves several steps to ensure the highest quality and reliability. These steps include:
-
Design and Engineering: The first step in the manufacturing process is to design the harness based on the specific requirements of the bus. This involves creating detailed schematics and 3D models of the harness, specifying the types of wires, connectors, and protective coverings to be used.
-
Wire Cutting and Stripping: Once the design is finalized, the wires are cut to the required lengths and stripped of their insulation at the ends. This is typically done using automated machines to ensure consistency and accuracy.
-
Crimping and Soldering: The stripped ends of the wires are then connected to the appropriate terminals using crimping or soldering techniques. Crimping involves using a special tool to compress the terminal around the wire, while soldering involves melting a small amount of metal to join the wire and terminal.
-
Connector Assembly: The terminated wires are then inserted into the appropriate connectors, following the design schematic. This process is often done manually to ensure proper alignment and secure connections.
-
Protective Covering Application: Once the harness is assembled, the protective coverings are applied. This may involve sliding on pre-cut lengths of insulation, braided sleeving, or heat-shrink tubing, and applying heat where necessary to create a snug fit.
-
Testing and Quality Control: Before the harness is shipped, it undergoes rigorous testing to ensure that all connections are secure and that the harness functions as intended. This may involve visual inspections, continuity tests, and functional tests with the actual components the harness will be connected to.
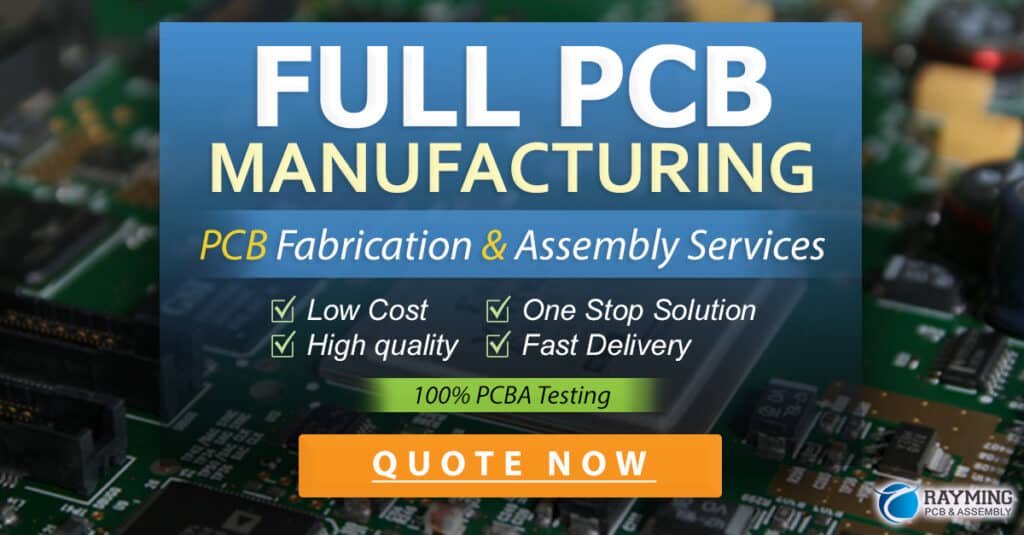
Maintenance and Troubleshooting
Proper maintenance and troubleshooting of bus signal harnesses are essential for ensuring the longevity and reliability of the vehicle’s electrical systems. Some key aspects of harness maintenance and troubleshooting include:
Regular Inspections
Regularly inspecting the signal harnesses for signs of wear, damage, or corrosion can help identify potential issues before they lead to system failures. This may involve visually checking the harness for cracks, fraying, or exposed wires, as well as testing for continuity and resistance.
Cleaning and Protection
Over time, harnesses can accumulate dirt, grease, and other contaminants that can degrade their performance. Regularly cleaning the harnesses and applying protective coatings, such as dielectric grease, can help prevent corrosion and extend their lifespan.
Proper Repair Techniques
When a harness is damaged or a connection fails, it is essential to use proper repair techniques to ensure a reliable fix. This may involve splicing wires, replacing connectors, or even fabricating new sections of the harness. It is important to follow the manufacturer’s guidelines and use appropriate tools and materials when making repairs.
Diagnostic Tools
When troubleshooting electrical issues related to signal harnesses, diagnostic tools such as multimeters, oscilloscopes, and scan tools can be invaluable. These tools can help identify open circuits, short circuits, and other faults within the harness, allowing for targeted repairs.
The Future of Bus Signal Harnesses
As technology continues to advance, bus signal harnesses are evolving to keep pace with new features and requirements. Some of the trends shaping the future of bus signal harnesses include:
Increased Data Transmission
With the proliferation of sensors, cameras, and other data-generating components in modern buses, signal harnesses are being designed to carry more data than ever before. This may involve the use of higher-bandwidth cables, such as fiber optics, or the integration of wireless data transmission technologies.
Modular Design
To simplify maintenance and repair, some manufacturers are moving towards modular harness designs. This involves breaking the harness down into smaller, interchangeable sections that can be easily replaced if damaged or upgraded as needed.
Lightweight Materials
As fuel efficiency and electric propulsion become increasingly important in the bus industry, manufacturers are looking for ways to reduce the weight of all components, including signal harnesses. This may involve the use of lighter-weight wires, connectors, and protective coverings, as well as the optimization of harness routing to minimize overall length.
Integration with Wireless Technologies
In some cases, wireless technologies such as Bluetooth, Wi-Fi, and cellular networks are being used to supplement or replace traditional wired connections within the bus. This can help reduce the complexity of the harness and provide greater flexibility in the placement of components.
Conclusion
Buses signal harnesses are a critical component in ensuring the safe, reliable, and comfortable operation of modern buses. By understanding the role of these harnesses, their components, and the manufacturing and maintenance processes involved, transit authorities and maintenance personnel can ensure that their vehicles are always operating at peak performance. As technology continues to advance, it will be important to stay up-to-date with the latest developments in harness design and manufacturing to ensure that buses remain at the forefront of passenger transportation.
Frequently Asked Questions (FAQ)
-
What is the purpose of a bus signal harness?
A bus signal harness is responsible for transmitting electrical signals and power between various components within the bus, ensuring that each system functions as intended. It connects systems such as lighting, audio/visual equipment, climate control, and safety features. -
What are the main components of a bus signal harness?
The main components of a bus signal harness include wires and cables, connectors, terminals, and protective coverings. Wires and cables carry electrical signals and power, connectors join different sections of the harness and connect it to various components, terminals provide secure connections between wires and connectors, and protective coverings shield the harness from damage and environmental factors. -
How are bus signal harnesses manufactured?
The manufacturing process of bus signal harnesses involves several steps, including design and engineering, wire cutting and stripping, crimping and soldering, connector assembly, protective covering application, and testing and quality control. Each step is crucial in ensuring the highest quality and reliability of the harness. -
What are some best practices for maintaining bus signal harnesses?
Regular inspections, cleaning and protection, proper repair techniques, and the use of diagnostic tools are all important aspects of maintaining bus signal harnesses. Inspections help identify potential issues, cleaning and protection prevent corrosion and extend harness lifespan, proper repair techniques ensure reliable fixes, and diagnostic tools assist in troubleshooting electrical issues. -
How are bus signal harnesses evolving with new technologies?
As technology advances, bus signal harnesses are being designed to accommodate increased data transmission, modular designs, lightweight materials, and integration with wireless technologies. These trends aim to improve harness performance, simplify maintenance, reduce weight, and provide greater flexibility in component placement.
Component | Purpose |
---|---|
Wires and Cables | Carry electrical signals and power |
Connectors | Join harness sections and connect to components |
Terminals | Provide secure connections between wires and connectors |
Protective Coverings | Shield harness from damage and environmental factors |
Table 1: Main components of a bus signal harness and their purposes.
Manufacturing Step | Description |
---|---|
Design and Engineering | Create detailed schematics and 3D models of the harness |
Wire Cutting and Stripping | Cut wires to required lengths and strip insulation |
Crimping and Soldering | Connect wire ends to terminals using crimping or soldering |
Connector Assembly | Insert terminated wires into appropriate connectors |
Protective Covering Application | Apply insulation, braided sleeving, or heat-shrink tubing |
Testing and Quality Control | Perform visual inspections, continuity tests, and functional tests |
Table 2: Manufacturing process steps for bus signal harnesses.
Maintenance Practice | Importance |
---|---|
Regular Inspections | Identify potential issues before they lead to system failures |
Cleaning and Protection | Prevent corrosion and extend harness lifespan |
Proper Repair Techniques | Ensure reliable fixes when harness is damaged or connections fail |
Diagnostic Tools | Identify open circuits, short circuits, and other faults within the harness |
Table 3: Key aspects of bus signal harness maintenance and their importance.
Leave a Reply