Introduction to Breakaway Tab PCB
Printed Circuit Boards (PCBs) are essential components in modern electronics, providing a platform for electrical components to be mounted and interconnected. One important feature often found in PCBs is the breakaway tab, also known as a breakout tab or snap-off tab. These tabs serve various purposes in the manufacturing, assembly, and utilization of PCBs.
In this comprehensive article, we will delve into the world of breakaway tabs in PCBs, exploring their definition, purposes, design considerations, manufacturing processes, and applications. We will also discuss the advantages and disadvantages of using breakaway tabs and provide insights into their future in the ever-evolving PCB industry.
What are Breakaway Tabs?
Breakaway tabs are small, perforated sections of a PCB that can be easily separated from the main board. These tabs are typically located along the edges of the PCB and are connected to the main board through a series of small, pre-cut holes or perforations. The perforations allow for easy separation of the tab from the main board when necessary.
Breakaway tabs come in various shapes and sizes, depending on their intended purpose and the specific PCB design. Some common shapes include rectangular, circular, and triangular tabs. The size of the tab is usually determined by the space available on the PCB and the required functionality of the tab.
Purposes of Breakaway Tabs in PCBs
Breakaway tabs serve several important purposes in PCBs, including:
-
Panelization: Breakaway tabs are often used to connect multiple PCBs together in a panel format during the manufacturing process. This allows for more efficient production, as several boards can be processed simultaneously. Once the manufacturing is complete, the individual boards can be separated from the panel by breaking away the tabs.
-
Mounting: Some breakaway tabs are designed to provide temporary or permanent mounting points for the PCB. These tabs can be used to secure the board to an enclosure or to attach it to other components within a device.
-
Electrical Connections: In some cases, breakaway tabs are used to establish temporary electrical connections between the PCB and other components or testing equipment. This allows for easier testing and debugging during the manufacturing process.
-
Handling: Breakaway tabs can also serve as handling points for the PCB during assembly or installation. Technicians can hold the board by the tabs to avoid damaging sensitive components on the main board.
Designing Breakaway Tabs for PCBs
When designing breakaway tabs for PCBs, several factors must be considered to ensure proper functionality and ease of use. Some key design considerations include:
Tab Size and Shape
The size and shape of the breakaway tab should be determined based on its intended purpose and the available space on the PCB. For panelization, the tab size should be sufficient to hold the board securely in the panel while allowing for easy separation. Mounting tabs may require specific shapes and sizes to fit the corresponding mounting hardware.
Perforation Design
The perforation design is crucial for ensuring clean and easy separation of the breakaway tab from the main board. The number, size, and spacing of the perforations should be carefully calculated to provide adequate strength during manufacturing and handling while allowing for easy breakaway when needed.
Material Selection
The material used for the breakaway tab should be the same as or compatible with the main PCB material. This ensures consistent manufacturing processes and avoids any potential issues with thermal expansion or mechanical stress.
Placement and Orientation
The placement and orientation of the breakaway tab on the PCB should be carefully considered. Tabs should be positioned to avoid interfering with other components or connectors on the board. They should also be oriented in a way that facilitates easy separation and minimizes the risk of damaging the main board during the breakaway process.
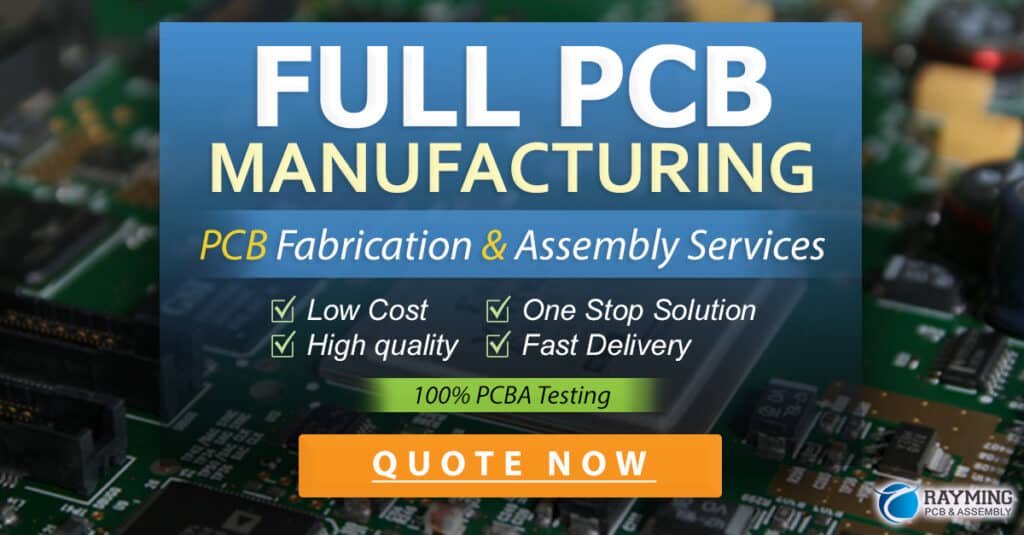
Manufacturing Breakaway Tab PCBs
The manufacturing process for breakaway tab PCBs is similar to that of standard PCBs, with a few additional steps to create the perforations and tabs. The process typically involves the following stages:
-
PCB Design: The PCB design, including the breakaway tabs, is created using CAD software. The design files are then used to generate the necessary manufacturing files, such as Gerber files and drill files.
-
Panelization: If the PCBs are to be manufactured in a panel format, the individual board designs are arranged in a panel layout, with breakaway tabs connecting the boards.
-
Copper Etching: The PCB panel undergoes a series of chemical processes to etch away the unwanted copper, leaving behind the desired circuit patterns and breakaway tab outlines.
-
Drilling: Holes are drilled through the PCB panel, including the perforations for the breakaway tabs. The drill file generated during the design phase guides this process.
-
Solder Mask and Silkscreen: A solder mask is applied to the PCB panel to protect the copper traces, and a silkscreen layer is added for component labeling and identification.
-
Surface Finishing: The exposed copper areas on the PCB, including the breakaway tabs, are coated with a surface finish to protect against oxidation and enhance solderability.
-
Breakaway Tab Creation: The perforations for the breakaway tabs are created by milling or V-scoring the PCB panel. This process creates small, pre-cut holes along the tab outline, allowing for easy separation.
-
Electrical Testing: The assembled PCB panel undergoes electrical testing to ensure proper functionality and connectivity.
-
Depanelization: If required, the individual PCBs are separated from the panel by breaking away the tabs along the perforations.
Applications of Breakaway Tab PCBs
Breakaway tab PCBs find applications across various industries and product categories, including:
-
Consumer Electronics: Breakaway tabs are commonly used in the manufacturing of consumer electronic devices, such as smartphones, tablets, and laptops. They facilitate the efficient production and assembly of PCBs within these devices.
-
Automotive Electronics: In the automotive industry, breakaway tab PCBs are used in the production of electronic control units (ECUs), sensors, and infotainment systems. The tabs allow for secure mounting and easy separation during the assembly process.
-
Industrial Electronics: Breakaway tabs are utilized in the manufacturing of industrial control systems, power electronics, and automation equipment. They provide a means for efficient panelization and separation of PCBs in these applications.
-
Medical Devices: PCBs with breakaway tabs are used in the production of various medical devices, such as patient monitors, diagnostic equipment, and wearable sensors. The tabs facilitate easy handling and assembly of the PCBs within these devices.
-
Aerospace and Defense: In the aerospace and defense industries, breakaway tab PCBs are used in the production of avionics systems, communication equipment, and navigation devices. The tabs provide secure mounting points and allow for efficient manufacturing processes.
Advantages and Disadvantages of Breakaway Tab PCBs
Advantages
-
Efficient Manufacturing: Breakaway tabs allow for the panelization of PCBs, enabling more efficient production processes and reducing manufacturing costs.
-
Secure Mounting: Breakaway tabs can provide secure mounting points for PCBs, ensuring proper positioning and stability within a device.
-
Easy Handling: The tabs serve as convenient handling points during PCB assembly and installation, minimizing the risk of damage to sensitive components.
-
Temporary Connections: Breakaway tabs can be used to establish temporary electrical connections for testing and debugging purposes, simplifying the manufacturing process.
Disadvantages
-
Additional Design Considerations: Incorporating breakaway tabs into a PCB design requires careful consideration of tab size, shape, placement, and perforation design. This can add complexity to the design process.
-
Increased Material Usage: The presence of breakaway tabs slightly increases the overall material usage in PCB manufacturing, as the tabs are ultimately removed and discarded.
-
Potential for Damage: If not designed or manufactured properly, the breakaway process can potentially cause damage to the main PCB or surrounding components.
FAQs
-
Q: Can breakaway tabs be used for permanent mounting of PCBs?
A: Yes, breakaway tabs can be designed to provide permanent mounting points for PCBs. However, this requires careful consideration of the tab size, shape, and material to ensure adequate strength and durability. -
Q: How are the perforations for breakaway tabs created during manufacturing?
A: The perforations for breakaway tabs are typically created through milling or V-scoring processes. These processes create small, pre-cut holes along the tab outline, allowing for easy separation of the tab from the main PCB. -
Q: Are there any specific design guidelines for breakaway tabs in different industries?
A: While the general principles of breakaway tab design apply across industries, there may be specific guidelines or standards that need to be followed in certain sectors, such as automotive or medical devices. It is important to consult the relevant industry standards and regulations when designing breakaway tabs for PCBs in these fields. -
Q: Can breakaway tabs be used for establishing electrical connections?
A: Yes, breakaway tabs can be used to establish temporary electrical connections for testing and debugging purposes during the manufacturing process. However, they are not typically used for permanent electrical connections, as the tabs are designed to be removable. -
Q: Are there any alternatives to breakaway tabs for PCB panelization?
A: While breakaway tabs are a common method for PCB panelization, there are alternatives available, such as tab routing and V-scoring without perforations. The choice of panelization method depends on factors such as the PCB design, manufacturing capabilities, and end-use requirements.
Future of Breakaway Tab PCBs
As the electronics industry continues to evolve, the use of breakaway tab PCBs is likely to remain prevalent in the foreseeable future. However, advancements in PCB manufacturing technologies and materials may lead to improvements in tab design and performance.
One potential development is the increased use of flexible PCB materials, which may require new approaches to breakaway tab design to account for the unique properties of these materials. Additionally, the growing demands for miniaturization and high-density PCB layouts may necessitate the development of smaller, more precise breakaway tab solutions.
Furthermore, the increasing adoption of automation in PCB manufacturing and assembly processes may lead to the development of new methods for creating and separating breakaway tabs, enhancing efficiency and reducing the risk of damage during the breakaway process.
As the industry progresses, it is important for PCB designers and manufacturers to stay informed about the latest advancements in breakaway tab technology and to adapt their practices accordingly to ensure the production of high-quality, reliable PCBs.
Conclusion
Breakaway tabs play a crucial role in the manufacturing, assembly, and utilization of PCBs across various industries. By facilitating panelization, providing mounting points, and enabling temporary electrical connections, these tabs contribute to the efficiency and reliability of PCB production processes.
Designing and manufacturing breakaway tab PCBs requires careful consideration of factors such as tab size, shape, perforation design, and material selection. By understanding these considerations and staying informed about industry advancements, PCB designers and manufacturers can effectively incorporate breakaway tabs into their products, ensuring optimal performance and functionality.
As the electronics industry continues to evolve, the use of breakaway tab PCBs is likely to remain an important aspect of PCB manufacturing. By embracing new technologies and adapting to changing demands, the industry can continue to produce high-quality, reliable PCBs that meet the needs of a wide range of applications.
Component Type | Typical Breakaway Tab Shape |
---|---|
Rectangular PCB | Rectangular or Circular |
Circular PCB | Circular or Triangular |
Irregular PCB | Custom-shaped tabs |
Table 1: Common breakaway tab shapes for different PCB component types.
Industry | Key Considerations for Breakaway Tabs |
---|---|
Consumer Electronics | Miniaturization, high-density layouts |
Automotive Electronics | Durability, vibration resistance |
Industrial Electronics | Secure mounting, environmental resistance |
Medical Devices | Biocompatibility, sterilization compatibility |
Aerospace and Defense | High-reliability, shock and vibration resistance |
Table 2: Key considerations for breakaway tab design in different industries.
Leave a Reply