Introduction to Blue PCB
Blue PCB, or Printed Circuit Board, is a specialized type of circuit board that has gained popularity in recent years due to its unique properties and advantages over traditional green PCBs. This article will delve into the world of blue PCBs, exploring their characteristics, manufacturing process, applications, and benefits.
What is a PCB?
Before we dive into the specifics of blue PCBs, let’s briefly discuss what a PCB is. A Printed Circuit Board is a flat board made of insulating material, such as fiberglass or composite epoxy, with conductive copper traces etched onto its surface. These traces connect various electronic components, such as resistors, capacitors, and integrated circuits, to create a functional electronic circuit.
PCBs are used in virtually all electronic devices, from smartphones and computers to medical equipment and aerospace systems. They provide a compact, reliable, and efficient way to interconnect electronic components, enabling the development of complex electronic systems.
The Rise of Blue PCB
Traditionally, PCBs have been green in color due to the solder mask applied to the board’s surface. The solder mask is a protective layer that prevents short circuits and oxidation of the copper traces. Green has been the standard color for PCBs for decades, but in recent years, blue PCBs have gained popularity for several reasons.
Characteristics of Blue PCB
Color and Appearance
The most distinguishing feature of blue PCBs is their color. Unlike the traditional green PCBs, blue PCBs have a distinctive blue solder mask. This blue color is not just for aesthetic purposes; it also serves functional benefits, which we will discuss later in this article.
Material Composition
Blue PCBs are typically made of the same materials as green PCBs, such as FR-4 (Flame Retardant 4) laminate. FR-4 is a composite material made of woven fiberglass cloth with an epoxy resin binder. It is known for its excellent mechanical and electrical properties, making it suitable for a wide range of applications.
Copper Thickness
The copper thickness of blue PCBs can vary depending on the specific application and design requirements. Common copper thicknesses include:
Copper Weight (oz) | Thickness (mm) |
---|---|
0.5 | 0.017 |
1 | 0.035 |
2 | 0.070 |
3 | 0.105 |
Thicker copper layers are used for high-current applications or when greater mechanical strength is required.
Manufacturing Process of Blue PCB
The manufacturing process of blue PCBs is similar to that of green PCBs, with a few key differences. The main steps involved in the manufacturing process are:
-
Design and Layout: The PCB design is created using specialized software, such as Altium Designer or Eagle. The layout includes the placement of components, routing of traces, and the creation of solder mask and silkscreen layers.
-
PCB Fabrication: The designed PCB is then fabricated using a multi-step process:
- Copper clad laminate is cut to the desired size.
- Holes are drilled for through-hole components and vias.
- Copper traces are etched using a photolithography process.
- Solder mask is applied to protect the copper traces and prevent short circuits.
-
Silkscreen is applied for component labeling and identification.
-
Component Assembly: Once the PCB is fabricated, electronic components are soldered onto the board using either through-hole or surface-mount technology (SMT).
-
Testing and Quality Control: The assembled PCB undergoes various tests to ensure its functionality, reliability, and adherence to design specifications. This may include visual inspection, automated optical inspection (AOI), and electrical testing.
The key difference in the manufacturing process of blue PCBs lies in the application of the blue solder mask. The blue solder mask is applied using the same techniques as the green solder mask, but with a different pigment to achieve the desired blue color.
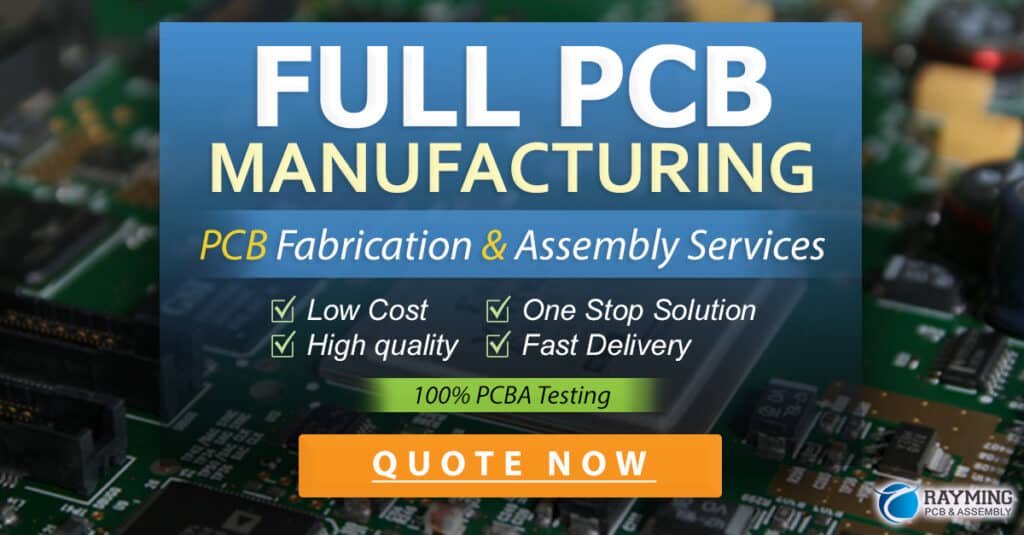
Advantages of Blue PCB
Blue PCBs offer several advantages over traditional green PCBs, making them an attractive choice for various applications.
Enhanced Visual Inspection
One of the primary benefits of blue PCBs is improved visual inspection. The blue color provides a high contrast against the copper traces and components, making it easier for technicians to spot defects, solder bridges, or missing components during the assembly and quality control processes. This enhanced visual inspection can lead to higher quality PCBs and reduced manufacturing errors.
Improved Solder Mask Adhesion
The blue solder mask used in blue PCBs has been found to have better adhesion properties compared to the green solder mask. This improved adhesion helps prevent the solder mask from peeling or flaking off during the manufacturing process or in harsh operating conditions. Better solder mask adhesion enhances the overall reliability and durability of the PCB.
Reduced Eye Strain
Working with traditional green PCBs for extended periods can cause eye strain and fatigue due to the low contrast between the green solder mask and the copper traces. The high contrast provided by the blue solder mask in blue PCBs reduces eye strain, making it more comfortable for technicians to work with these boards for longer durations.
Aesthetic Appeal
While not a functional benefit, the unique blue color of blue PCBs can add an aesthetic appeal to electronic devices. The blue color can make the PCB stand out and give the device a distinctive look. This can be especially attractive for consumer electronics or high-end equipment where visual appearance is important.
Applications of Blue PCB
Blue PCBs find applications in various industries and electronic devices, including:
-
Consumer Electronics: Blue PCBs are commonly used in consumer electronic devices, such as smartphones, tablets, laptops, and gaming consoles, where their enhanced visual inspection and aesthetic appeal are desirable.
-
Medical Devices: The improved reliability and durability of blue PCBs make them suitable for use in medical devices, where high-quality and long-lasting performance are critical.
-
Automotive Electronics: Blue PCBs are used in automotive electronics, such as infotainment systems, engine control units, and advanced driver assistance systems (ADAS), where their enhanced visual inspection and reliability are valuable.
-
Industrial Control Systems: The high contrast and reduced eye strain provided by blue PCBs make them a good choice for industrial control systems, where technicians need to work with PCBs for extended periods.
-
Aerospace and Defense: The durability and reliability of blue PCBs make them suitable for use in aerospace and defense applications, where the electronics must withstand harsh environments and meet stringent quality standards.
Frequently Asked Questions (FAQ)
1. Are blue PCBs more expensive than green PCBs?
The cost difference between blue and green PCBs is minimal. The main factor affecting the cost of a PCB is the complexity of the design, the number of layers, and the overall manufacturing process, rather than the color of the solder mask.
2. Can blue PCBs be manufactured with the same design rules as green PCBs?
Yes, blue PCBs can be manufactured using the same design rules and specifications as green PCBs. The color of the solder mask does not affect the design rules or the manufacturing process.
3. Are blue PCBs suitable for all applications?
Blue PCBs are suitable for a wide range of applications, but there may be some specific cases where green PCBs are preferred. For example, in some military or aerospace applications, green PCBs may be specified due to legacy standards or specific requirements.
4. Do blue PCBs have any disadvantages compared to green PCBs?
There are no significant disadvantages of blue PCBs compared to green PCBs. The choice between blue and green PCBs often comes down to personal preference, aesthetic considerations, or specific industry standards.
5. Can blue PCBs be recycled in the same way as green PCBs?
Yes, blue PCBs can be recycled using the same processes as green PCBs. The color of the solder mask does not affect the recyclability of the PCB material.
Conclusion
Blue PCBs have emerged as a popular alternative to traditional green PCBs, offering several advantages such as enhanced visual inspection, improved solder mask adhesion, reduced eye strain, and aesthetic appeal. While the manufacturing process and material composition of blue PCBs are similar to green PCBs, the blue solder mask provides unique benefits that make them suitable for a wide range of applications, including consumer electronics, medical devices, automotive electronics, industrial control systems, and aerospace and defense.
As the electronics industry continues to evolve and demand higher quality and reliability, blue PCBs are likely to gain further popularity. With their combination of functional benefits and aesthetic appeal, blue PCBs offer a compelling choice for designers and manufacturers looking to create high-quality, reliable, and visually appealing electronic devices.
Leave a Reply