Introduction to Blind Vias in PCB Design
In the world of printed circuit board (PCB) design, vias play a crucial role in connecting different layers of the board. Among the various types of vias, blind vias have gained popularity due to their ability to save space and improve signal integrity. In this article, we will dive deep into the concept of blind vias in PCB design, exploring their benefits, manufacturing process, and best practices for implementation.
What are Vias in PCB?
Before we delve into blind vias specifically, let’s first understand what vias are in the context of PCB design. Vias are essentially small holes drilled through the layers of a PCB to create electrical connections between different layers. They allow signals to travel vertically through the board, enabling more complex routing and reducing the overall size of the PCB.
Types of Vias in PCB
There are three main types of vias used in PCB design:
- Through Vias: These vias extend through all layers of the PCB, from the top to the bottom.
- Blind Vias: Blind vias start from either the top or bottom layer and terminate at an inner layer, without extending through the entire board.
- Buried Vias: Buried vias are hidden within the inner layers of the PCB and do not reach either the top or bottom layer.
Understanding Blind Vias
What are Blind Vias?
Blind vias, as mentioned earlier, are vias that start from either the top or bottom layer of a PCB and terminate at an inner layer, without extending through the entire board. They are called “blind” because they are not visible from one side of the board.
Benefits of Using Blind Vias in PCB Design
- Space Saving: Blind vias allow for more compact PCB designs by eliminating the need for through vias, which require additional space on the outer layers.
- Improved Signal Integrity: By reducing the via length, blind vias minimize signal reflections and improve overall signal integrity.
- Enhanced Routing Flexibility: Blind vias provide more routing options, as they can be placed in areas where through vias may not be feasible.
- Reduced Electromagnetic Interference (EMI): Shorter via lengths associated with blind vias help reduce EMI, as they minimize the antenna effect.
Manufacturing Process of Blind Vias
The manufacturing process of blind vias involves several steps:
- Drilling: Holes are drilled partially through the PCB, starting from either the top or bottom layer and stopping at the desired inner layer.
- Plating: The drilled holes are then plated with a conductive material, typically copper, to create an electrical connection between the layers.
- Filling: After plating, the blind vias are filled with a non-conductive material to prevent any unwanted electrical connections and improve the structural integrity of the board.
Implementing Blind Vias in PCB Design
Design Considerations for Blind Vias
When incorporating blind vias into your PCB design, keep the following considerations in mind:
- Via Size: Blind vias typically have smaller diameters compared to through vias, which can impact the manufacturing process and cost.
- Layer Stack-up: Carefully plan your layer stack-up to ensure proper placement of blind vias and minimize the number of drilling operations required.
- Design Rules: Adhere to the design rules provided by your PCB manufacturer, including minimum via size, spacing, and aspect ratio.
- Signal Integrity: Conduct signal integrity simulations to ensure that the use of blind vias does not introduce any signal integrity issues.
Best Practices for Blind Via PCB Design
To optimize your blind via PCB design, follow these best practices:
- Use blind vias only when necessary, as they can increase manufacturing complexity and cost.
- Keep blind vias as short as possible to minimize signal reflections and improve signal integrity.
- Avoid placing blind vias in high-stress areas of the PCB, such as near corners or edges.
- Coordinate with your PCB manufacturer early in the design process to ensure that your blind via design is feasible and cost-effective.
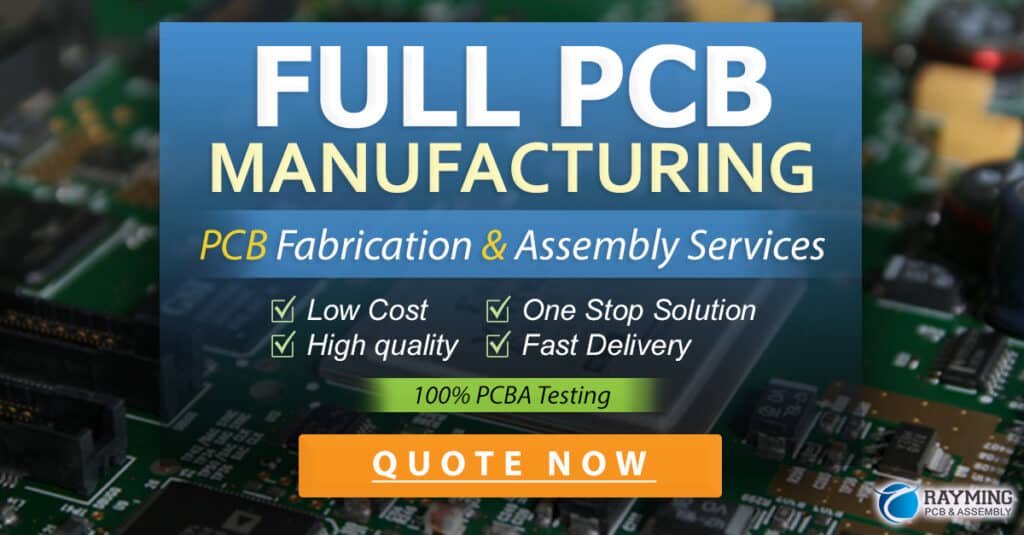
Blind Via PCB Manufacturing Process
The manufacturing process for blind via PCBs involves several specialized steps to create the partially drilled and plated holes. Let’s take a closer look at each step:
- Layer Stack-up Preparation: The PCB layers are prepared according to the design specifications, including the placement of blind vias.
- Drilling: Using precise drilling machines, holes are drilled partially through the PCB, starting from either the top or bottom layer and stopping at the desired inner layer.
- Plating: The drilled holes are then plated with a conductive material, typically copper, using electroplating techniques. This creates an electrical connection between the layers.
- Filling: After plating, the blind vias are filled with a non-conductive material, such as epoxy resin, to prevent any unwanted electrical connections and improve the structural integrity of the board.
- Lamination: The PCB layers are laminated together under high pressure and temperature to create a solid, unified board.
- Outer Layer Processing: The outer layers of the PCB undergo additional processing, such as copper patterning, solder mask application, and silkscreen printing.
- Surface Finishing: The PCB receives a surface finish, such as HASL (Hot Air Solder Leveling) or ENIG (Electroless Nickel Immersion Gold), to protect the exposed copper and enhance solderability.
Challenges in Blind Via PCB Manufacturing
Manufacturing blind via PCBs comes with its own set of challenges:
- Increased Complexity: The additional drilling and plating steps required for blind vias increase the overall complexity of the manufacturing process.
- Higher Cost: Due to the specialized equipment and processes involved, blind via PCBs tend to be more expensive compared to standard PCBs with through vias.
- Limited Manufacturers: Not all PCB manufacturers have the capability to produce blind via PCBs, as it requires specialized equipment and expertise.
- Longer Lead Times: The added complexity of blind via PCB manufacturing can result in longer lead times compared to standard PCB production.
Blind Via PCB Applications
Blind via PCBs find applications in various industries where space saving, signal integrity, and high-density interconnects are crucial. Some common applications include:
- Smartphones and Tablets: The compact nature of blind vias allows for the miniaturization of electronic devices, making them ideal for smartphones, tablets, and wearable technology.
- High-Speed Communication Systems: Blind vias are used in high-speed communication systems, such as 5G networks and data centers, to improve signal integrity and reduce signal loss.
- Aerospace and Defense: In aerospace and defense applications, where reliability and space constraints are critical, blind vias provide a compact and robust solution for PCB design.
- Medical Devices: Blind vias are used in medical devices, such as implantable electronics and diagnostic equipment, where miniaturization and reliability are paramount.
Frequently Asked Questions (FAQ)
-
Q: What is the difference between blind vias and buried vias?
A: Blind vias start from either the top or bottom layer of a PCB and terminate at an inner layer, while buried vias are hidden within the inner layers and do not reach either the top or bottom layer. -
Q: Are blind vias more expensive than through vias?
A: Yes, blind vias are generally more expensive than through vias due to the specialized manufacturing processes and equipment required. -
Q: Can blind vias improve signal integrity in high-speed PCB designs?
A: Yes, blind vias can improve signal integrity by reducing via length, minimizing signal reflections, and reducing electromagnetic interference (EMI). -
Q: Are there any limitations to using blind vias in PCB design?
A: Yes, blind vias have limitations such as smaller diameters, increased manufacturing complexity, and higher costs compared to through vias. -
Q: How can I ensure that my blind via PCB design is manufacturable?
A: To ensure manufacturability, work closely with your PCB manufacturer, adhere to their design rules, and conduct thorough signal integrity simulations and design reviews.
Conclusion
Blind vias have become an essential tool in modern PCB design, offering numerous benefits such as space saving, improved signal integrity, and enhanced routing flexibility. By understanding the manufacturing process, design considerations, and best practices associated with blind vias, designers can create high-performance, compact PCBs for a wide range of applications.
As technology continues to advance, the demand for miniaturized and high-speed electronic devices will only increase. Blind via PCB technology will play a crucial role in meeting these demands, enabling the development of innovative solutions across industries.
When incorporating blind vias into your PCB design, remember to collaborate closely with your PCB manufacturer, adhere to design rules, and prioritize signal integrity. By following best practices and staying up-to-date with the latest advancements in blind via technology, you can unlock the full potential of your PCB designs and stay ahead of the curve in the ever-evolving world of electronics.
Leave a Reply