Table of Contents
- Introduction to BGA Packages
- Challenges in BGA Fanout Routing
- BGA Fanout Routing Techniques
- Via-in-Pad
- Dog Bone
- Micro Vias
- BGA Fanout Routing Strategies
- Matrix Fanout
- X-Y Fanout
- Asymmetric Fanout
- Design Considerations for BGA Fanout Routing
- Trace Width and Spacing
- Via Size and Placement
- Signal Integrity
- Thermal Management
- Best Practices for BGA Fanout Routing
- Tools for BGA Fanout Routing
- Case Studies
- Future Trends in BGA Fanout Routing
- Frequently Asked Questions (FAQ)
- Conclusion
1. Introduction to BGA Packages
BGA packages are surface-mount devices that utilize an array of solder balls on the bottom of the package to establish connections with the PCB. They offer several advantages over other package types, such as:
- High connection density
- Improved electrical and thermal performance
- Reduced package size
However, these benefits come with the challenge of routing the signals from the BGA package to the rest of the circuit, which is known as BGA fanout routing.
2. Challenges in BGA Fanout Routing
BGA fanout routing presents several challenges for PCB designers, including:
- Limited space between the solder balls
- high pin count
- Signal integrity concerns
- Manufacturability constraints
To overcome these challenges, designers must carefully plan the fanout pattern, select appropriate routing techniques, and adhere to best practices.
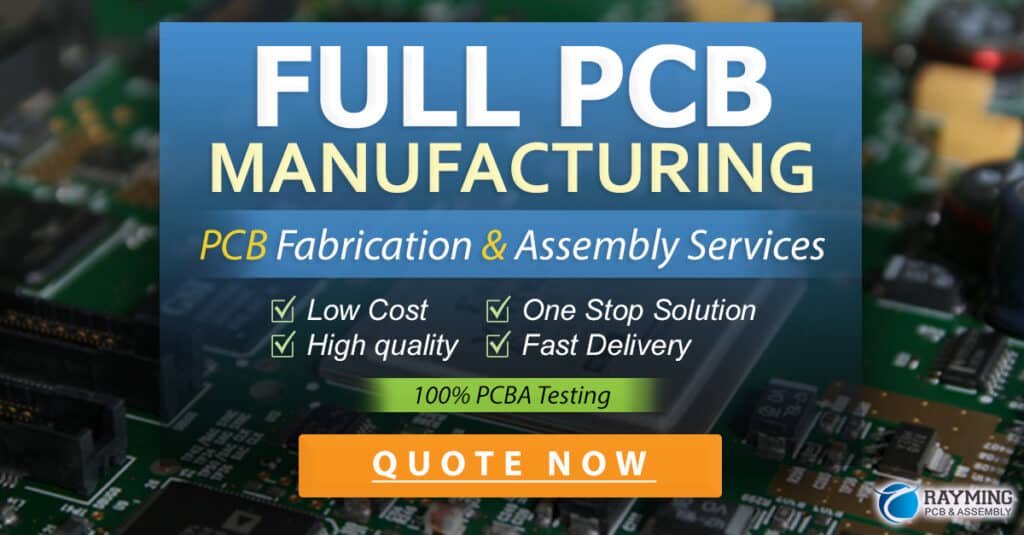
3. BGA Fanout Routing Techniques
There are several techniques used in BGA fanout routing, each with its own advantages and limitations. Some of the most common techniques are:
3.1 Via-in-Pad
Via-in-pad is a technique where vias are placed directly on the BGA pads, allowing for a direct connection between the BGA package and the inner layers of the PCB. This technique offers the following benefits:
- Saves space on the PCB surface
- Reduces the number of routing layers required
- Improves signal integrity
However, via-in-pad also has some drawbacks, such as:
- Increased manufacturing complexity
- Potential for solder joint reliability issues
- Limited to certain BGA pitch sizes
3.2 Dog Bone
The dog bone technique involves placing a via offset from the BGA pad and connecting the two with a short trace resembling a dog bone. This technique is useful when via-in-pad is not feasible or when more routing flexibility is needed. Some advantages of the dog bone technique include:
- Compatibility with a wider range of BGA pitch sizes
- Reduced manufacturing complexity compared to via-in-pad
- Improved solder joint reliability
However, the dog bone technique also has some limitations, such as:
- Increased trace length, which may impact signal integrity
- Consumes more space on the PCB surface
3.3 Micro Vias
Micro vias are small-diameter vias that can be used to create high-density interconnects between layers in a PCB. They are particularly useful in BGA fanout routing, as they allow for more efficient use of space and improved signal integrity. Some benefits of using micro vias include:
- Reduced via size, allowing for tighter routing
- Improved signal integrity due to shorter via lengths
- Compatibility with high-density BGA packages
However, micro vias also have some limitations, such as:
- Increased manufacturing cost
- Potential for reliability issues if not designed properly
4. BGA Fanout Routing Strategies
In addition to the routing techniques discussed above, there are several strategies that can be employed to optimize BGA fanout routing. These strategies focus on the overall layout and organization of the fanout pattern to achieve the best possible results.
4.1 Matrix Fanout
Matrix fanout is a strategy where the BGA pads are divided into a grid, and each pin is assigned to a specific row and column. This approach allows for a systematic and organized fanout pattern that can be easily modified and optimized. Some advantages of matrix fanout include:
- Simplifies the fanout process
- Provides a clear and organized structure
- Allows for easy modification and optimization
However, matrix fanout may not always be the most efficient strategy, particularly for high-density BGA packages or complex routing requirements.
4.2 X-Y Fanout
X-Y fanout is a strategy where the BGA pads are divided into two groups: one for horizontal routing (X) and one for vertical routing (Y). This approach allows for more efficient use of routing channels and can help minimize the number of layers required. Some benefits of X-Y fanout include:
- Efficient use of routing channels
- Reduced layer count
- Improved signal integrity
However, X-Y fanout may not be suitable for all BGA packages, particularly those with irregular pin assignments or non-square layouts.
4.3 Asymmetric Fanout
Asymmetric fanout is a strategy where the fanout pattern is not symmetrical around the BGA package. This approach can be useful when dealing with irregular pin assignments or when trying to optimize for specific design constraints. Some advantages of asymmetric fanout include:
- Flexibility to accommodate irregular pin assignments
- Ability to optimize for specific design constraints
- Potential for improved signal integrity
However, asymmetric fanout can be more complex to design and may require more manual intervention compared to other strategies.
5. Design Considerations for BGA Fanout Routing
When designing BGA fanout routing, there are several key factors that must be considered to ensure optimal performance and manufacturability.
5.1 Trace Width and Spacing
Trace width and spacing are critical parameters in BGA fanout routing, as they directly impact signal integrity and manufacturability. Designers must carefully balance the need for narrow traces to accommodate high-density routing with the requirements for signal integrity and manufacturing tolerances.
Some general guidelines for trace width and spacing in BGA fanout routing include:
BGA Pitch (mm) | Minimum Trace Width (mm) | Minimum Trace Spacing (mm) |
---|---|---|
1.00 | 0.10 | 0.10 |
0.80 | 0.08 | 0.08 |
0.65 | 0.06 | 0.06 |
0.50 | 0.05 | 0.05 |
5.2 Via Size and Placement
Via size and placement are also important considerations in BGA fanout routing, as they can impact signal integrity, manufacturability, and reliability. Designers must select via sizes that are appropriate for the BGA pitch and the routing density, while also ensuring that the vias are placed in a way that minimizes signal degradation and manufacturing defects.
Some general guidelines for via size and placement in BGA fanout routing include:
BGA Pitch (mm) | Minimum Via Diameter (mm) | Minimum Via Spacing (mm) |
---|---|---|
1.00 | 0.25 | 0.50 |
0.80 | 0.20 | 0.40 |
0.65 | 0.15 | 0.30 |
0.50 | 0.10 | 0.25 |
5.3 Signal Integrity
Signal integrity is a critical concern in BGA fanout routing, as the high-density routing and close proximity of traces can lead to issues such as crosstalk, reflections, and signal attenuation. Designers must carefully analyze and simulate the signal integrity of their BGA fanout routing to ensure that the signals meet the required specifications and performance criteria.
Some techniques for improving signal integrity in BGA fanout routing include:
- Using appropriate trace widths and spacings
- Minimizing via stubs and maximizing via-to-pad clearance
- Utilizing differential pair routing for high-speed signals
- Implementing proper grounding and shielding techniques
5.4 Thermal Management
Thermal management is another important consideration in BGA fanout routing, as the high-density routing and power dissipation of the BGA package can lead to thermal issues if not properly addressed. Designers must ensure that there is adequate thermal relief and heat dissipation in the BGA fanout area to prevent excessive temperature rise and potential reliability issues.
Some techniques for improving thermal management in BGA fanout routing include:
- Providing thermal relief pads around the BGA solder balls
- Utilizing thermal vias to conduct heat away from the BGA package
- Incorporating copper pours and heatsinks to dissipate heat
- Optimizing the placement of high-power components
6. Best Practices for BGA Fanout Routing
To achieve the best possible results in BGA fanout routing, designers should follow some general best practices and guidelines. Some of these best practices include:
- Start with a well-defined component placement and pin assignment strategy.
- Use a consistent and systematic fanout pattern, such as matrix or X-Y fanout.
- Follow the manufacturer’s recommended guidelines for trace width, spacing, and via size.
- Minimize the number of routing layers required by using techniques such as via-in-pad or micro vias.
- Analyze and simulate the signal integrity of the fanout routing to ensure that it meets the required specifications.
- Provide adequate thermal relief and heat dissipation in the fanout area.
- Use design for manufacturability (DFM) techniques to ensure that the fanout routing is compatible with the chosen manufacturing process.
7. Tools for BGA Fanout Routing
There are several tools available to assist designers with BGA fanout routing, ranging from simple calculators to complex simulation and optimization software. Some of the most common tools used in BGA fanout routing include:
- BGA fanout calculators: These tools help designers determine the optimal trace widths, spacings, and via sizes for a given BGA package and PCB stackup.
- PCB design software: Most PCB design software packages, such as Altium Designer, Cadence Allegro, and Mentor Graphics PADS, include features and tools specifically designed for BGA fanout routing.
- Signal integrity simulation tools: Tools such as Ansys SIwave, Cadence Sigrity, and Mentor Graphics HyperLynx can be used to analyze and optimize the signal integrity of BGA fanout routing.
- Thermal simulation tools: Tools such as Ansys Icepak, Cadence Celsius, and Mentor Graphics FloTHERM can be used to simulate and optimize the thermal performance of BGA fanout routing.
8. Case Studies
To illustrate the practical application of BGA fanout routing techniques and best practices, let’s consider a few case studies.
8.1 High-Density BGA Fanout Routing
In this case study, a designer is tasked with routing a high-density BGA package with a 0.5mm pitch on a 6-layer PCB. The design requirements include:
- Minimize the number of routing layers required
- Maintain a minimum trace width of 0.05mm and spacing of 0.05mm
- Ensure adequate signal integrity and thermal performance
To meet these requirements, the designer chooses to use a combination of via-in-pad and micro via techniques, along with a matrix fanout strategy. By carefully planning the fanout pattern and optimizing the via placement, the designer is able to route the BGA package using only four layers while meeting all the design requirements.
8.2 Mixed-Signal BGA Fanout Routing
In this case study, a designer is working on a mixed-signal PCB that includes a BGA package with both high-speed digital and sensitive analog signals. The design requirements include:
- Maintain signal integrity for the high-speed digital signals
- Minimize crosstalk and noise coupling to the analog signals
- Provide adequate thermal relief for the BGA package
To address these requirements, the designer uses a combination of X-Y fanout and asymmetric fanout strategies, along with differential pair routing for the high-speed digital signals. The analog signals are routed on a separate layer with additional shielding to minimize noise coupling. Thermal vias and copper pours are used to provide thermal relief for the BGA package.
9. Future Trends in BGA Fanout Routing
As BGA packages continue to increase in density and complexity, new techniques and technologies are being developed to address the challenges of BGA fanout routing. Some of the future trends in BGA fanout routing include:
- Advanced materials: The use of advanced materials, such as low-loss dielectrics and embedded capacitance materials, can help improve signal integrity and reduce the number of routing layers required.
- 3D printing: The adoption of 3D printing technologies for PCB fabrication can enable new possibilities for BGA fanout routing, such as the ability to create complex three-dimensional structures and embedded components.
- AI-assisted design: The use of artificial intelligence and machine learning algorithms can help automate and optimize the BGA fanout routing process, leading to faster design cycles and improved performance.
10. Frequently Asked Questions (FAQ)
- What is the difference between via-in-pad and dog bone techniques in BGA fanout routing?
-
Via-in-pad places the via directly on the BGA pad, while dog bone offsets the via and connects it to the pad with a short trace. Via-in-pad saves space but is more complex to manufacture, while dog bone is simpler but consumes more space.
-
How does the BGA pitch affect the fanout routing design?
-
The BGA pitch determines the spacing between the solder balls and, consequently, the available space for routing. Smaller pitches require narrower traces and smaller vias, which can increase the complexity and cost of the design.
-
What is the purpose of thermal relief in BGA fanout routing?
-
Thermal relief pads around the BGA solder balls help dissipate heat and prevent excessive temperature rise, which can cause reliability issues. They also improve the solderability of the BGA package during assembly.
-
How can signal integrity be optimized in BGA fanout routing?
-
Signal integrity can be optimized by using appropriate trace widths and spacings, minimizing via stubs, utilizing differential pair routing for high-speed signals, and implementing proper grounding and shielding techniques.
-
What are some common tools used for BGA fanout routing?
- Common tools for BGA fanout routing include BGA fanout calculators, PCB design software with specific BGA fanout features, signal integrity simulation tools, and thermal simulation tools.
11. Conclusion
BGA fanout routing is a critical aspect of PCB design that requires careful planning, analysis, and execution to achieve optimal results. By understanding the various techniques, strategies, and best practices involved in BGA fanout routing, designers can effectively overcome the challenges posed by high-density BGA packages and ensure the success of their PCB designs.
As BGA technology continues to evolve, designers must stay up-to-date with the latest techniques and tools to stay competitive in the industry. By embracing new technologies and methodologies, such as advanced materials, 3D printing, and AI-assisted design, designers can unlock new possibilities for BGA fanout routing and push the boundaries of PCB design.
Leave a Reply