How Auto Routers Work
Auto routers use algorithms to determine the optimal paths for the connections between components on a PCB or IC. The process typically involves the following steps:
Input of design data: The auto router receives the design data, including the component placement, net list (a list of all the connections between components), and design constraints (such as the minimum spacing between traces and the maximum number of layers).
Routing strategy selection: The user selects the routing strategy, which determines the order in which the connections are routed and the criteria used to evaluate the quality of the routing solution.
Routing process: The auto router generates the routing paths based on the selected strategy and design constraints. This process may involve multiple passes, with each pass refining the routing solution.
Output of routing solution: The auto router outputs the final routing solution, which can be reviewed and modified by the user if necessary.
Routing Strategies
There are several routing strategies that auto routers can use, each with its own advantages and disadvantages. Some common routing strategies include:
Maze routing: This strategy uses a grid-based approach to find the shortest path between two points while avoiding obstacles. It is simple and fast but may not always produce the most efficient routing solution.
Line-probe routing: This strategy uses a line-based approach to find the optimal path between two points. It is more efficient than maze routing but may require more computational resources.
Topological routing: This strategy uses a graph-based approach to find the optimal path between two points. It is the most efficient routing strategy but also the most complex and computationally intensive.
Design Constraints
Auto routers must take into account various design constraints when generating routing paths. These constraints ensure that the final routing solution is manufacturable, reliable, and meets the performance requirements of the PCB or IC. Some common design constraints include:
Trace width and spacing: The minimum width of the traces and the minimum spacing between traces must be specified to ensure that the PCB or IC can be manufactured reliably.
Via size and spacing: The minimum size of the vias (holes that connect traces on different layers) and the minimum spacing between vias must be specified to ensure that the PCB or IC can be manufactured reliably.
Layer stack-up: The number and arrangement of the layers in the PCB or IC must be specified to ensure that the routing solution is feasible and meets the performance requirements.
Component placement: The placement of the components on the PCB or IC must be specified to ensure that the routing solution is feasible and meets the performance requirements.
Advantages of Using Auto Routers
Using an auto router offers several advantages over manual routing, including:
Faster routing process: Auto routers can generate routing paths much faster than manual routing, especially for complex designs with many components and connections.
More efficient routing solutions: Auto routers can generate more efficient routing solutions than manual routing, as they can explore a larger number of potential paths and optimize the routing based on various criteria.
Reduced risk of human error: Auto routers eliminate the risk of human error in the routing process, as they follow a set of predefined rules and constraints.
Improved design consistency: Auto routers ensure that the routing is consistent across the entire PCB or IC, as they use the same rules and constraints for all connections.
Limitations of Auto Routers
Despite their advantages, auto routers also have some limitations that users should be aware of:
Limited flexibility: Auto routers may not be able to handle certain complex or unusual routing scenarios that require manual intervention.
Dependence on accurate design data: Auto routers rely on accurate design data, such as the component placement and net list, to generate reliable routing solutions. Inaccurate or incomplete design data can lead to suboptimal or even incorrect routing solutions.
Computational resources: Auto routers, especially those that use more advanced routing strategies, can require significant computational resources, which may limit their use on older or less powerful computers.
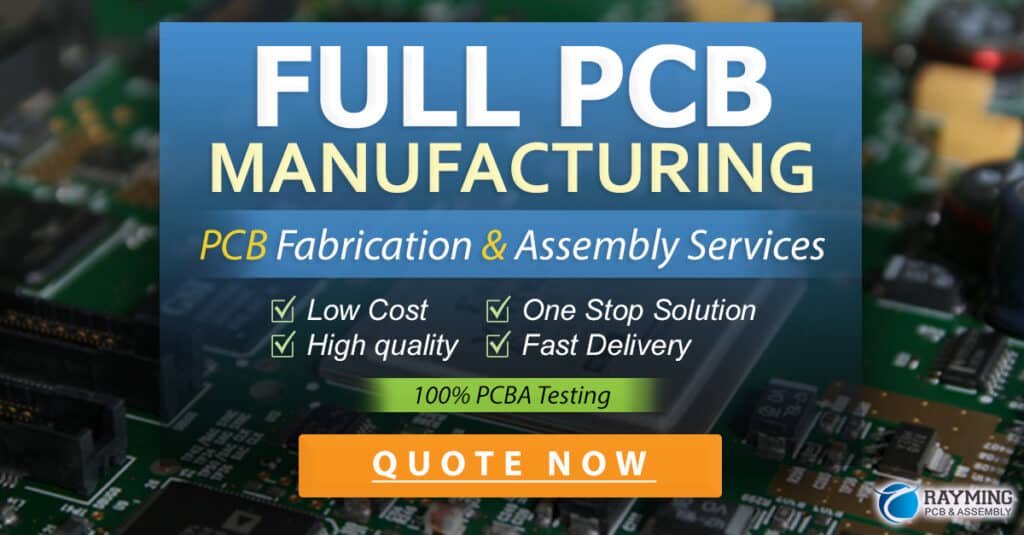
Examples of Auto Routers
There are many auto routers available on the market, ranging from standalone software packages to integrated solutions within larger PCB or IC design tools. Some examples of popular auto routers include:
Auto Router | Description |
---|---|
Altium Designer | A comprehensive PCB design tool that includes a powerful auto router with support for multiple routing strategies and design constraints. |
Cadence Allegro | A high-end PCB design tool that includes an auto router with advanced features such as multi-threading and concurrent routing. |
Mentor Graphics Expedition | A PCB design tool that includes an auto router with support for high-speed design and advanced packaging technologies. |
Eagle | A popular PCB design tool that includes a basic auto router suitable for simpler designs. |
KiCad | A free and open-source PCB design tool that includes a basic auto router. |
Best Practices for Using Auto Routers
To get the most out of an auto router, users should follow some best practices:
Ensure accurate design data: Make sure that the component placement, net list, and design constraints are accurate and complete before running the auto router.
Choose the appropriate routing strategy: Select the routing strategy that best suits the complexity and performance requirements of the design.
Review and refine the routing solution: Review the auto router’s output and make manual adjustments if necessary to optimize the routing solution further.
Verify the manufacturability: Ensure that the final routing solution meets all the manufacturability requirements, such as minimum trace width and spacing, via size and spacing, and layer stack-up.
The Future of Auto Routers
As PCB and IC designs continue to become more complex and demanding, auto routers will need to evolve to keep pace. Some potential future developments in auto routing technology include:
Artificial intelligence and machine learning: Incorporating AI and machine learning algorithms into auto routers could enable them to learn from past routing solutions and improve their performance over time.
Cloud-based routing: Moving the routing process to the cloud could enable faster and more efficient routing by leveraging the scalability and computational power of cloud computing platforms.
Integration with other design tools: Deeper integration between auto routers and other PCB or IC design tools, such as simulation and analysis tools, could enable more holistic and optimized design solutions.
Frequently Asked Questions (FAQ)
Q: Can auto routers completely replace manual routing?
A: While auto routers can handle most routing tasks, there may still be some complex or unusual scenarios that require manual intervention. Auto routers should be seen as a tool to complement and accelerate the routing process, rather than a complete replacement for manual routing.Q: How long does it take for an auto router to generate a routing solution?
A: The time required for an auto router to generate a solution depends on the complexity of the design, the routing strategy used, and the computational resources available. Simple designs may take only a few minutes, while complex designs could take several hours or even days.Q: Can auto routers handle high-speed design requirements?
A: Yes, many modern auto routers have features and constraints specifically designed to handle the challenges of high-speed PCB or IC design, such as impedance matching and signal integrity analysis.Q: Are auto routers expensive?
A: The cost of auto routers varies widely depending on the features and capabilities offered. Standalone auto routing software packages can range from a few hundred to several thousand dollars, while integrated solutions within larger PCB or IC design tools can cost tens of thousands of dollars. However, there are also some free and open-source auto routers available, such as the one included in KiCad.Q: What should I do if the auto router generates a suboptimal routing solution?
A: If the auto router generates a suboptimal routing solution, users can try adjusting the routing strategy, design constraints, or component placement and rerunning the auto router. If the issue persists, manual intervention may be necessary to optimize the routing solution further.
In conclusion, auto routers are an essential tool for modern PCB and IC design, offering significant advantages in terms of speed, efficiency, and consistency. By understanding the capabilities and limitations of auto routers, and following best practices for their use, designers can harness the power of this technology to create high-quality, reliable, and manufacturable electronic products.
Leave a Reply