Introduction to 2 Layer PCBs
A 2 layer PCB, also known as a double-sided PCB, is a printed circuit board that consists of two conductive copper layers separated by an insulating substrate material. These two layers are typically referred to as the top layer and the bottom layer, or the component side and the solder side. 2 layer PCBs are widely used in various electronic devices and applications due to their cost-effectiveness, reliability, and versatility.
Advantages of 2 Layer PCBs
- Cost-effective: 2 layer PCBs are generally less expensive to manufacture compared to multi-layer PCBs, making them an attractive option for low-complexity designs and high-volume production.
- Simplified design: With only two layers to work with, the design process for 2 layer PCBs is relatively straightforward, reducing the time and effort required for layout and routing.
- Improved signal integrity: By utilizing both sides of the board, 2 layer PCBs offer better signal integrity compared to single-layer PCBs, as the return currents can flow more easily on the adjacent layer.
- Enhanced thermal management: The additional copper layer in a 2 layer PCB helps dissipate heat more efficiently, improving the overall thermal performance of the board.
Construction of 2 Layer PCBs
Core Materials
The core of a 2 layer PCB is typically made of a dielectric substrate material, such as FR-4, which is a glass-reinforced epoxy laminate. FR-4 is the most common choice for PCBs due to its excellent mechanical and electrical properties, as well as its affordability. Other substrate materials, such as polyimide or Rogers laminates, may be used for specialized applications that require higher temperature resistance or improved high-frequency performance.
Copper Layers
The two conductive layers in a 2 layer PCB are made of copper foil, which is laminated onto the core substrate material. The thickness of the copper foil is typically measured in ounces per square foot (oz/ft²), with common thicknesses ranging from 0.5 oz/ft² to 2 oz/ft². Thicker copper layers offer better current-carrying capacity and improved thermal dissipation but may increase the overall cost of the board.
Solder Mask and Silkscreen
To protect the exposed copper traces and prevent accidental short-circuits, a solder mask layer is applied over the copper layers. The solder mask is a thin, protective coating that covers the areas of the PCB where soldering is not required. It also provides electrical insulation and helps to prevent oxidation of the copper traces.
In addition to the solder mask, a silkscreen layer is often applied to the PCB to add labels, logos, and other identifying markings. The silkscreen is typically a white or yellow color and is used to improve the readability and aesthetics of the board.
Design Considerations for 2 Layer PCBs
Component Placement
When designing a 2 layer PCB, it is essential to carefully consider the placement of components to ensure optimal performance and manufacturability. Some key factors to keep in mind include:
- Grouping related components together to minimize trace lengths and improve signal integrity
- Placing heat-generating components away from sensitive devices to avoid thermal issues
- Ensuring adequate spacing between components to facilitate assembly and repair
- Orienting components to minimize the need for vias and layer transitions
Trace Routing
Routing traces on a 2 layer PCB requires careful planning to ensure signal integrity, minimize crosstalk, and avoid manufacturing issues. Some best practices for trace routing include:
- Keeping trace lengths as short as possible to reduce resistance and inductance
- Avoiding sharp angles or abrupt changes in trace direction to minimize reflections and impedance mismatches
- Using appropriate trace widths based on the current-carrying requirements and manufacturing constraints
- Providing adequate spacing between traces to minimize crosstalk and improve manufacturability
Ground and Power Planes
In a 2 layer PCB, it is common to dedicate one layer (usually the bottom layer) to a solid ground plane, while the other layer is used for signal routing and power distribution. The ground plane serves several important functions, including:
- Providing a low-impedance return path for signals
- Minimizing ground loops and reducing electromagnetic interference (EMI)
- Improving the overall power supply stability and noise reduction
When designing the power distribution network on a 2 layer PCB, it is essential to ensure adequate copper pour for the power traces to minimize voltage drop and improve current-carrying capacity. Additionally, placing decoupling capacitors close to the power pins of ICs can help to reduce high-frequency noise and improve power supply stability.
Vias and Layer Transitions
Vias are used in 2 layer PCBs to connect traces between the top and bottom layers. There are two main types of vias:
- Through-hole vias: These vias extend through the entire thickness of the board and are typically used for component mounting or to provide mechanical strength.
- Blind and buried vias: These vias are used to connect traces between layers without extending through the entire board thickness. Blind vias are exposed on one side of the board, while buried vias are completely internal.
When designing a 2 layer PCB, it is important to minimize the number of vias and layer transitions to reduce manufacturing complexity and improve signal integrity. Strategies for optimizing via placement include:
- Placing vias near the endpoints of traces to minimize stub lengths
- Using via stitching to create low-impedance ground connections between layers
- Avoiding vias in high-speed signal paths whenever possible
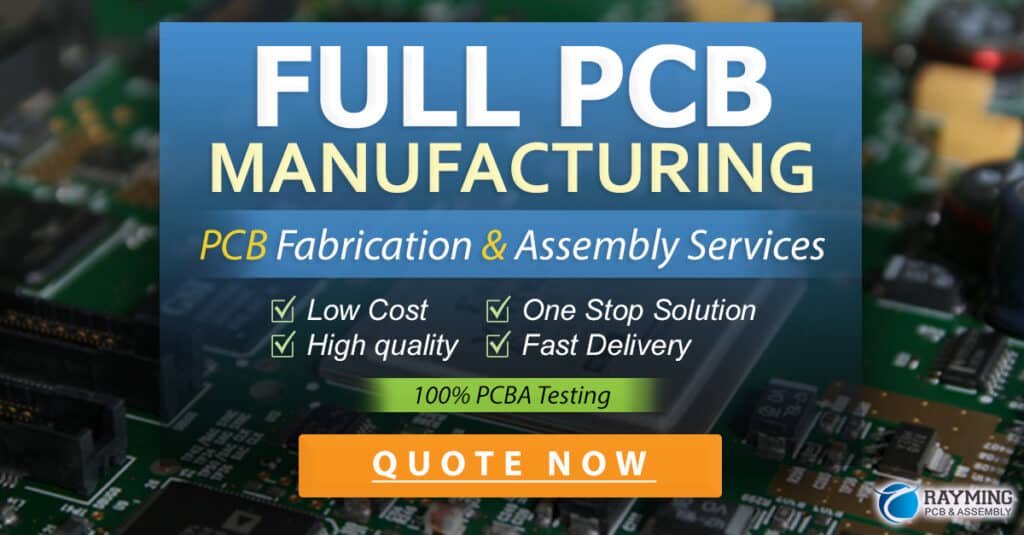
Manufacturing Process for 2 Layer PCBs
The manufacturing process for 2 layer PCBs typically involves the following steps:
-
PCB Design: The PCB design is created using electronic design automation (EDA) software, which generates the necessary Gerber files and drill files for manufacturing.
-
Film Preparation: The Gerber files are used to create photographic films or direct imaging (DI) files for each layer of the PCB.
-
Copper Lamination: The core substrate material is laminated with copper foil on both sides using heat and pressure.
-
Drilling: Holes are drilled through the PCB stack-up using a computer numerical control (CNC) drilling machine, based on the drill files generated during the design phase.
-
Plating: The drilled holes are plated with copper to create electrical connections between the layers and to provide a surface for component mounting.
-
Etching: The unwanted copper is removed from the PCB using a chemical etching process, leaving only the desired traces and pads.
-
Solder Mask Application: The solder mask is applied to the PCB to protect the copper traces and prevent accidental short-circuits.
-
Silkscreen Printing: The silkscreen layer is printed onto the PCB to add labels, logos, and other identifying markings.
-
Surface Finish: A surface finish, such as Hot Air Solder Leveling (HASL), Electroless Nickel Immersion Gold (ENIG), or Organic Solderability Preservative (OSP), is applied to the exposed copper pads to improve solderability and protect against oxidation.
-
Electrical Testing: The manufactured PCBs undergo electrical testing to ensure proper functionality and conformance to the design specifications.
Applications of 2 Layer PCBs
2 layer PCBs are widely used in various electronic devices and applications, including:
- Consumer electronics: Smartphones, tablets, laptops, and wearables
- Industrial control systems: Sensors, actuators, and process control equipment
- Automotive electronics: Engine control units, infotainment systems, and lighting control modules
- Medical devices: Portable monitors, diagnostic equipment, and implantable devices
- IoT and embedded systems: Wireless modules, sensor nodes, and single-board computers
The versatility and cost-effectiveness of 2 layer PCBs make them a popular choice for a wide range of industries and applications, particularly those that require low-complexity designs and high-volume production.
Future Trends in 2 Layer PCB Design and Manufacturing
As electronic devices continue to evolve and become more complex, there is a growing demand for advanced PCB technologies that can support higher performance, greater miniaturization, and improved reliability. Some of the key trends shaping the future of 2 layer PCB design and manufacturing include:
-
High-Density Interconnect (HDI): HDI PCBs feature finer trace widths, smaller vias, and tighter component spacing, enabling the integration of more functionality into smaller form factors. While HDI designs are more commonly associated with multi-layer PCBs, advances in manufacturing technologies are making it possible to incorporate HDI features into 2 layer PCBs as well.
-
Flexible and Rigid-Flex PCBs: Flexible PCBs and rigid-flex PCBs are gaining popularity in applications that require conformable or bendable circuits, such as wearables, medical devices, and aerospace systems. By combining the benefits of rigid and flexible substrates, 2 layer rigid-flex PCBs offer enhanced mechanical stability and improved signal integrity in complex 3D assemblies.
-
Advanced Materials: The development of new substrate materials, such as high-frequency laminates, low-loss dielectrics, and thermally conductive materials, is enabling the design of 2 layer PCBs with improved electrical and thermal performance. These advanced materials are particularly valuable in applications that require high-speed data transmission, enhanced power handling capability, or operation in extreme environments.
-
Embedded Components: The integration of passive components, such as resistors and capacitors, directly into the PCB substrate is an emerging trend that offers several benefits, including reduced board size, improved signal integrity, and enhanced reliability. While embedded component technologies are more commonly used in multi-layer PCBs, advances in manufacturing processes are making it possible to incorporate embedded components into 2 layer PCBs as well.
-
Additive Manufacturing: Additive manufacturing techniques, such as 3D printing and inkjet printing, are being explored as potential alternatives to traditional subtractive PCB manufacturing methods. These technologies offer the potential for faster prototyping, greater design flexibility, and reduced material waste, which could lead to more cost-effective and environmentally friendly production of 2 layer PCBs in the future.
As these trends continue to evolve, it is likely that 2 layer PCBs will remain a critical component in the design and manufacturing of electronic devices, while also benefiting from advances in materials, processes, and technologies that enable higher performance, greater miniaturization, and improved sustainability.
Frequently Asked Questions (FAQ)
-
Q: What is the difference between a 2 layer PCB and a 4 layer PCB?
A: A 2 layer PCB has two conductive copper layers (top and bottom), while a 4 layer PCB has four conductive layers (top, bottom, and two inner layers). 4 layer PCBs offer more routing space and better signal integrity but are more expensive and complex to manufacture compared to 2 layer PCBs. -
Q: Can 2 layer PCBs be used for high-speed designs?
A: While 2 layer PCBs are not ideal for high-speed designs due to the limited routing space and potential for crosstalk, they can still be used for moderately high-speed applications with proper design techniques, such as careful component placement, optimized trace routing, and the use of ground planes. -
Q: What are the typical copper thicknesses used in 2 layer PCBs?
A: The most common copper thicknesses for 2 layer PCBs are 0.5 oz/ft², 1 oz/ft², and 2 oz/ft². Thicker copper layers provide better current-carrying capacity and improved thermal dissipation but may increase the cost of the board. -
Q: Are 2 layer PCBs suitable for prototype development?
A: Yes, 2 layer PCBs are often used for prototype development due to their lower cost and faster turnaround times compared to multi-layer PCBs. They are particularly well-suited for low-complexity designs and proof-of-concept testing. -
Q: Can 2 layer PCBs be manufactured with advanced features like blind or buried vias?
A: While blind and buried vias are more commonly used in multi-layer PCBs, it is possible to incorporate these features into 2 layer PCBs using specialized manufacturing processes. However, this may increase the cost and complexity of the board compared to a standard 2 layer PCB design.
Conclusion
2 layer PCBs are a fundamental building block in the world of electronic design and manufacturing, offering a cost-effective and reliable solution for a wide range of applications. By understanding the construction, design considerations, and manufacturing processes involved in 2 layer PCBs, engineers and designers can create high-quality, high-performance circuits that meet the demands of today’s electronic devices.
As technology continues to advance, 2 layer PCBs are likely to benefit from innovations in materials, manufacturing processes, and design techniques, enabling them to support increasingly complex and sophisticated electronic systems. By staying up-to-date with the latest trends and best practices in 2 layer PCB design and manufacturing, engineers and designers can ensure that their products remain at the forefront of the rapidly evolving electronics industry.
Leave a Reply