Understanding turnkey pcb Assembly
Turnkey PCB assembly is a comprehensive solution for designing, manufacturing, and assembling printed circuit boards (PCBs) from start to finish. This approach streamlines the entire process, making it easier for businesses and individuals to obtain high-quality, fully assembled PCBs without the need to manage multiple vendors or navigate the complex world of PCB production.
The Benefits of Turnkey PCB Assembly
- Time-saving: By outsourcing the entire pcb assembly process to a single provider, businesses can save significant time and resources that would otherwise be spent coordinating with multiple vendors.
- Cost-effective: Turnkey PCB assembly providers often offer competitive pricing due to their established relationships with component suppliers and their ability to optimize the manufacturing process.
- Quality assurance: Reputable turnkey PCB assembly providers adhere to strict quality control standards, ensuring that the final product meets or exceeds the client’s specifications.
- Scalability: Turnkey PCB assembly services can accommodate projects of various sizes, from small prototype runs to large-scale production, making it an ideal solution for businesses of all sizes.
The Turnkey PCB Assembly Process
Step 1: PCB Design
The first step in the turnkey PCB assembly process is designing the printed circuit board. This involves creating a schematic diagram that outlines the electrical connections and components required for the board to function as intended. The schematic is then used to create a PCB layout, which determines the physical placement of components and traces on the board.
PCB Design Software
Several popular PCB design software packages are used in the industry, including:
- Altium Designer
- KiCad
- Eagle
- OrCAD
- Cadence Allegro
These software tools allow designers to create complex PCB layouts, simulate circuit behavior, and generate manufacturing files for production.
Step 2: PCB Fabrication
Once the PCB design is finalized, the next step is to fabricate the bare printed circuit board. This process involves several sub-steps:
- Substrate selection: The base material for the PCB, typically FR-4, is chosen based on the board’s intended application and performance requirements.
- Copper lamination: Thin layers of copper foil are laminated onto the substrate using heat and pressure.
- Etching: The unwanted copper is removed using a chemical etching process, leaving behind the desired traces and pads.
- Drilling: Holes are drilled through the board to accommodate through-hole components and vias.
- Solder mask application: A protective layer of solder mask is applied to the board, which helps to prevent short circuits and improves the board’s aesthetics.
- Silkscreen printing: Text and symbols are printed onto the board using a silkscreen process, which aids in component placement and identification.
PCB Fabrication Techniques
There are several PCB fabrication techniques, each with its own advantages and limitations:
Technique | Advantages | Limitations |
---|---|---|
Through-hole | Strong mechanical connections, easy to solder | Larger size, higher cost |
Surface mount | Smaller size, lower cost, higher component density | More difficult to solder, requires specialized equipment |
Mixed technology | Combines the benefits of through-hole and surface mount | Higher complexity, increased design challenges |
Step 3: Component Sourcing
With the bare PCB fabricated, the next step is to source the components required for the assembly. Turnkey PCB assembly providers typically have established relationships with component suppliers, allowing them to obtain the necessary parts quickly and at competitive prices.
Common PCB Components
PCBs can incorporate a wide variety of components, depending on the specific application. Some common components include:
- Resistors
- Capacitors
- Inductors
- Diodes
- Transistors
- Integrated circuits (ICs)
- Connectors
- Switches
Step 4: PCB Assembly
The final step in the turnkey PCB assembly process is assembling the components onto the bare PCB. This can be done using either through-hole or surface mount technology (SMT), depending on the components and the PCB design.
Through-hole Assembly
Through-hole assembly involves inserting component leads through holes drilled in the PCB and soldering them to pads on the opposite side of the board. This process can be done manually or using automated insertion machines.
Surface Mount Assembly
Surface mount assembly involves placing components directly onto pads on the surface of the PCB and soldering them in place using a reflow oven. This process is typically automated using pick-and-place machines, which can place components at high speeds and with great precision.
Step 5: Quality Control and Testing
Throughout the turnkey PCB assembly process, quality control measures are implemented to ensure that the final product meets the required specifications. This includes:
- Visual inspection: Assembled PCBs are visually inspected for defects such as misaligned components, solder bridges, or damaged parts.
- Automated optical inspection (AOI): Machine vision systems are used to quickly and accurately detect assembly defects.
- X-ray inspection: X-ray imaging is used to detect hidden defects, such as voids in solder joints or misaligned ball grid array (BGA) components.
- Functional testing: Assembled PCBs are powered on and tested to ensure that they function as intended.
Choosing a Turnkey PCB Assembly Provider
When selecting a turnkey PCB assembly provider, several factors should be considered:
- Experience and expertise: Look for a provider with a proven track record of successfully completing projects similar to yours.
- Quality certifications: Ensure that the provider holds relevant quality certifications, such as ISO 9001, ISO 14001, or IPC-A-610.
- Capabilities: Verify that the provider has the necessary equipment and expertise to handle your specific PCB assembly requirements.
- Communication and support: Choose a provider that offers clear communication and responsive support throughout the project.
- Pricing and lead times: Compare pricing and lead times from multiple providers to ensure that you are getting a competitive deal without compromising on quality or service.
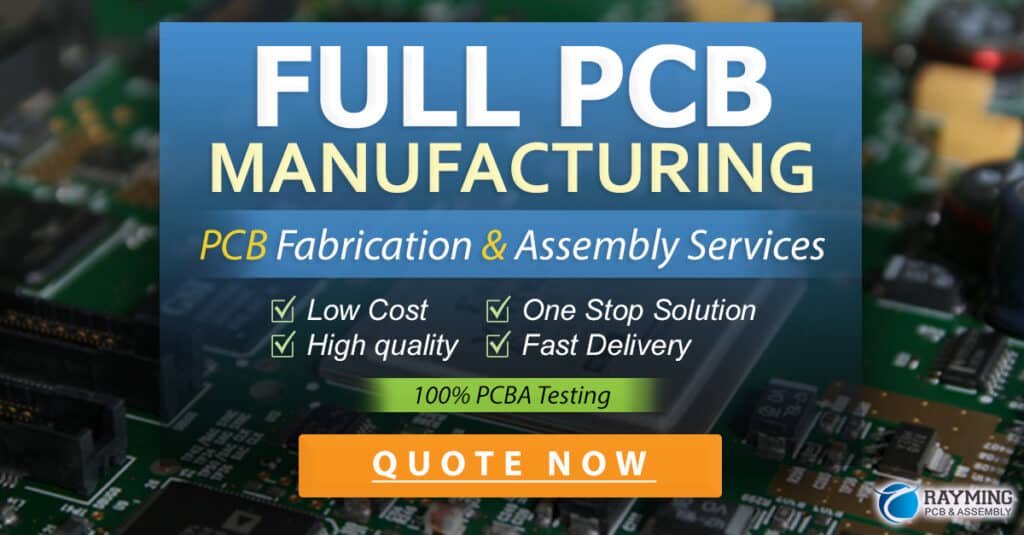
The Future of Turnkey PCB Assembly
As technology continues to advance, the demand for more complex and highly integrated PCBs will continue to grow. Turnkey PCB assembly providers will need to stay at the forefront of these developments to remain competitive. Some trends that are likely to shape the future of turnkey PCB assembly include:
- Miniaturization: As devices become smaller and more compact, PCBs will need to follow suit. This will require advanced manufacturing techniques and the use of smaller, more precise components.
- High-speed design: With the increasing demand for faster data transmission and processing speeds, PCBs will need to be designed to minimize signal integrity issues and support high-frequency operation.
- Flexible and rigid-flex PCBs: The growing popularity of wearable devices and the need for more compact, lightweight electronics will drive the demand for flexible and rigid-flex PCBs.
- Environmentally friendly materials: As sustainability becomes a greater concern, turnkey PCB assembly providers will need to incorporate more eco-friendly materials and processes into their operations.
Conclusion
Turnkey PCB assembly is a comprehensive solution that simplifies the process of designing, manufacturing, and assembling printed circuit boards. By outsourcing the entire process to a single provider, businesses can save time, reduce costs, and ensure high-quality results. When choosing a turnkey PCB assembly provider, it is essential to consider factors such as experience, capabilities, quality certifications, communication, and pricing. As technology continues to evolve, turnkey PCB assembly providers will need to adapt to new trends and challenges to remain competitive in the industry.
Frequently Asked Questions (FAQ)
1. What is the difference between through-hole and surface mount assembly?
Through-hole assembly involves inserting component leads through holes drilled in the PCB and soldering them to pads on the opposite side of the board. Surface mount assembly, on the other hand, involves placing components directly onto pads on the surface of the PCB and soldering them in place using a reflow oven.
2. How long does the turnkey PCB assembly process typically take?
The lead time for turnkey PCB assembly can vary depending on the complexity of the design, the number of components, and the quantity of boards required. Generally, prototype runs can be completed in 1-2 weeks, while larger production runs may take several weeks or more.
3. What factors should I consider when choosing a turnkey PCB assembly provider?
When selecting a turnkey PCB assembly provider, consider factors such as their experience and expertise, quality certifications, capabilities, communication and support, pricing, and lead times.
4. Can turnkey PCB assembly providers handle both small prototype runs and large-scale production?
Yes, most turnkey PCB assembly providers can accommodate projects of various sizes, from small prototype runs to large-scale production. However, it is essential to verify that the provider has the necessary equipment and expertise to handle your specific requirements.
5. What quality control measures are typically implemented during the turnkey PCB assembly process?
Quality control measures in turnkey PCB assembly include visual inspection, automated optical inspection (AOI), X-ray inspection, and functional testing. These measures help to ensure that the final product meets the required specifications and functions as intended.
Leave a Reply