What is the Purpose of a Thermal Relief PCB?
The primary purpose of a thermal relief PCB is to facilitate efficient heat transfer during the soldering process while minimizing the risk of thermal damage to the PCB and its components. When soldering components to a PCB, the heat applied by the soldering iron must be sufficient to melt the solder and create a strong electrical and mechanical connection. However, excessive heat can cause damage to the PCB substrate, copper traces, and components.
Thermal relief PCBs address this issue by incorporating a specialized pad design that allows for better heat dissipation. The thermal relief design features a pad with a series of “spokes” or “traces” that connect the pad to the surrounding copper pour or plane. These spokes provide a controlled thermal path for heat to dissipate away from the pad and into the surrounding copper area.
Thermal Relief PCB Design Considerations
When designing a thermal relief PCB, several key factors must be considered to ensure optimal performance and reliability:
Pad Size and Shape
The size and shape of the thermal relief pad can significantly impact its effectiveness. Generally, larger pads with more surface area will dissipate heat more efficiently than smaller pads. However, the pad size must also be balanced against the available space on the PCB and the size of the component being soldered.
Common thermal relief pad shapes include circular, square, and octagonal designs. The choice of pad shape may depend on the specific component and the PCB layout requirements.
Number and Width of Spokes
The number and width of the spokes connecting the thermal relief pad to the surrounding copper area play a crucial role in heat dissipation. A higher number of spokes will provide more thermal paths for heat to escape, while wider spokes will allow for greater heat flow.
However, increasing the number and width of spokes also reduces the available copper area for electrical connections. Therefore, a balance must be struck between thermal performance and electrical integrity.
Copper Pour or Plane
The copper pour or plane surrounding the thermal relief pad acts as a heat sink, allowing heat to dissipate away from the pad and into the larger copper area. The size and shape of the copper pour can affect the overall thermal performance of the PCB.
In general, larger copper pours will provide better heat dissipation, but they may also increase the overall size and weight of the PCB. The copper pour should be designed to optimize thermal performance while minimizing any negative impacts on the PCB layout and manufacturing process.
Soldermask and Paste Mask Openings
The soldermask and paste mask openings around the thermal relief pad can also impact its performance. The soldermask opening should be large enough to allow for proper soldering and heat transfer, while the paste mask opening should be sized to ensure an adequate amount of solder is deposited on the pad.
Properly designed soldermask and paste mask openings will help to ensure a strong and reliable solder joint between the component and the thermal relief pad.
Advantages of Thermal Relief PCBs
Incorporating thermal relief pads into a PCB design offers several key advantages:
-
Improved Solderability: Thermal relief pads allow for better heat dissipation during the soldering process, which can lead to improved solder joint quality and reliability. The spokes of the thermal relief pad provide a controlled thermal path for heat to escape, preventing overheating and potential damage to the PCB and components.
-
Reduced Thermal Stress: By allowing heat to dissipate more efficiently, thermal relief pads help to reduce thermal stress on the PCB and its components. This can help to prevent issues such as pad lifting, trace damage, and component failure due to excessive heat exposure.
-
Enhanced Manufacturing Efficiency: Thermal relief pads can also improve the efficiency of the PCB manufacturing process. By promoting better heat dissipation, thermal relief pads can reduce the time required for soldering operations, leading to faster production times and lower manufacturing costs.
-
Increased Reliability: The improved solderability and reduced thermal stress provided by thermal relief pads can contribute to increased overall reliability of the PCB assembly. Stronger, more consistent solder joints and less thermal damage can help to prevent premature failures and extend the lifespan of the PCB and its components.
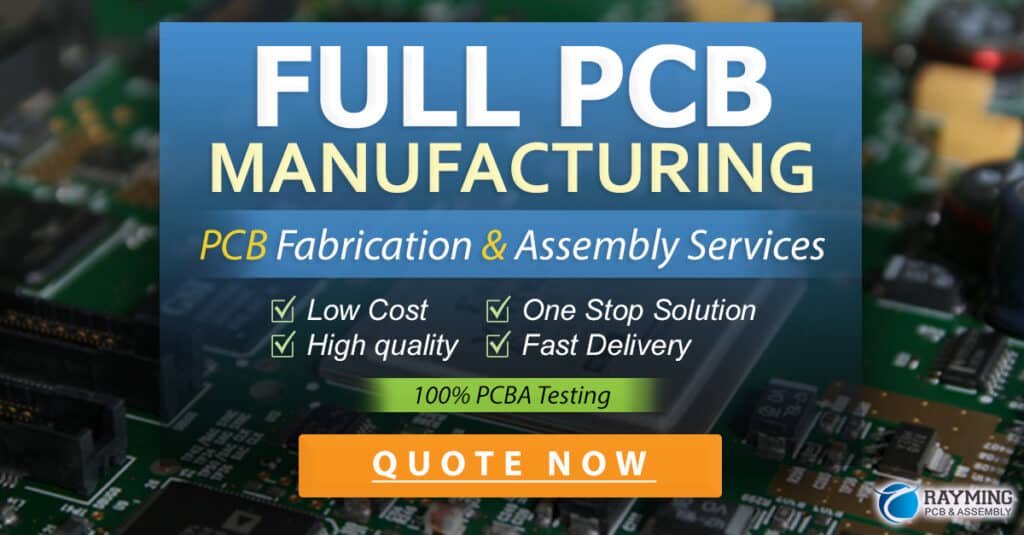
Frequently Asked Questions (FAQ)
-
Q: When should thermal relief pads be used in a PCB design?
A: Thermal relief pads should be used in situations where components will be soldered to the PCB, particularly in cases where the component has a large thermal mass or where the soldering process may introduce significant heat. They are especially important for surface mount components and in high-density PCB designs where thermal management is critical. -
Q: Can thermal relief pads be used with through-hole components?
A: Yes, thermal relief pads can be used with both surface mount and through-hole components. In the case of through-hole components, the thermal relief pad is typically incorporated into the design of the through-hole pad itself. -
Q: How do I choose the right size and shape for a thermal relief pad?
A: The size and shape of the thermal relief pad should be chosen based on the specific component being used and the available space on the PCB. Larger pads with more surface area will generally provide better heat dissipation, but this must be balanced against other design constraints. Common pad shapes include circular, square, and octagonal designs. -
Q: What is the optimal number and width of spokes for a thermal relief pad?
A: The optimal number and width of spokes will depend on the specific design requirements and constraints of the PCB. Generally, a higher number of spokes and wider spokes will provide better heat dissipation, but this must be balanced against the need for electrical connectivity and the available copper area on the PCB. Simulation tools and empirical testing can help to determine the best spoke configuration for a given design. -
Q: Are there any drawbacks to using thermal relief pads in a PCB design?
A: While thermal relief pads offer many benefits, there are some potential drawbacks to consider. The additional copper area required for the spokes and surrounding pour can increase the overall size and weight of the PCB. Additionally, the spokes themselves can introduce some additional complexity to the PCB layout and routing process. However, these drawbacks are generally outweighed by the improved solderability, reduced thermal stress, and increased reliability provided by thermal relief pads.
Conclusion
Thermal relief PCBs are an essential design feature for ensuring optimal solderability, reducing thermal stress, and improving the overall reliability of PCB assemblies. By incorporating thermal relief pads with carefully designed spokes and surrounding copper pour, PCB designers can effectively manage heat dissipation during the soldering process, leading to stronger solder joints and less risk of thermal damage.
When designing a thermal relief PCB, it is important to consider factors such as pad size and shape, the number and width of spokes, the surrounding copper pour, and the soldermask and paste mask openings. By carefully balancing these design elements, PCB designers can create thermal relief pads that provide the necessary thermal management while maintaining electrical integrity and minimizing any negative impacts on the PCB layout and manufacturing process.
As PCB technology continues to advance and component densities continue to increase, the importance of effective thermal management in PCB design will only continue to grow. By understanding the principles and best practices of thermal relief PCB design, PCB designers can create more reliable, efficient, and cost-effective PCB assemblies that meet the ever-increasing demands of modern electronics applications.
Thermal Relief PCB Design Considerations | Recommendations |
---|---|
Pad Size and Shape | – Choose larger pads for better heat dissipation – Balance pad size against available PCB space and component size – Common shapes: circular, square, octagonal |
Number and Width of Spokes | – Higher number of spokes provides more thermal paths – Wider spokes allow for greater heat flow – Balance spoke configuration against electrical connectivity and available copper area |
Copper Pour or Plane | – Larger copper pours provide better heat dissipation – Consider impact on PCB size and weight – Design copper pour to optimize thermal performance while minimizing negative impacts on layout and manufacturing |
Soldermask and Paste Mask Openings | – Soldermask opening should allow for proper soldering and heat transfer – Paste mask opening should ensure adequate solder deposition on pad – Properly designed openings help ensure strong, reliable solder joints |
By carefully considering these design factors and following best practices for thermal relief PCB design, PCB designers can create assemblies that offer improved solderability, reduced thermal stress, enhanced manufacturing efficiency, and increased overall reliability.
Leave a Reply