What is a PCB Substrate?
A PCB substrate is the insulating material that forms the base of a printed circuit board. It is typically made from a non-conductive material, such as fiberglass, paper, or plastic, which is then coated with a thin layer of copper on one or both sides. The copper layer is etched to create the desired circuit pattern, connecting the various components mounted on the board.
The primary functions of a PCB substrate are:
- Providing mechanical support for the components and copper traces
- Electrically insulating the conductive parts of the circuit
- Dissipating heat generated by the components
- Maintaining the dimensional stability of the PCB
The choice of substrate material depends on several factors, including the intended application, operating environment, required performance characteristics, and cost.
Types of PCB Substrates
There are several types of substrates used in PCB manufacturing, each with its own set of properties and advantages. The most common PCB substrates include:
1. FR-4
FR-4 (Flame Retardant 4) is the most widely used PCB substrate material. It is a composite material made from woven fiberglass cloth impregnated with an epoxy resin binder. FR-4 offers excellent mechanical strength, good electrical insulation properties, and reasonable thermal stability. It is suitable for a wide range of applications, from consumer electronics to industrial control systems.
Advantages of FR-4:
– Good mechanical strength and durability
– Excellent electrical insulation properties
– Reasonable thermal stability
– Flame retardant
– Cost-effective
Disadvantages of FR-4:
– Limited high-frequency performance due to its relatively high dielectric constant and loss tangent
– Not suitable for extreme temperature applications
2. High Tg FR-4
High Tg (Glass Transition Temperature) FR-4 is an enhanced version of the standard FR-4 substrate. It offers improved thermal stability and better performance at elevated temperatures compared to regular FR-4. This makes it suitable for applications that require higher operating temperatures or increased reliability, such as automotive electronics and aerospace systems.
Advantages of High Tg FR-4:
– Higher glass transition temperature (Tg) compared to standard FR-4
– Improved thermal stability and performance at elevated temperatures
– Better reliability in harsh environments
Disadvantages of High Tg FR-4:
– Higher cost compared to standard FR-4
– Still limited in terms of high-frequency performance
3. Rogers Materials
Rogers materials are a family of high-performance PCB substrates designed for demanding applications, particularly in the high-frequency and microwave domains. These substrates offer excellent electrical properties, such as low dielectric constant and loss tangent, as well as good thermal conductivity and mechanical stability.
Some popular Rogers materials include:
- RO4003C: A ceramic-filled PTFE composite with low dielectric constant and loss tangent, suitable for high-frequency applications up to 50 GHz.
- RO4350B: A glass-reinforced hydrocarbon/ceramic laminate with low dielectric constant and loss tangent, designed for high-frequency applications up to 30 GHz.
- RT/duroid 5880: A glass microfiber-reinforced PTFE composite with a very low dielectric constant and loss tangent, ideal for microwave applications up to 77 GHz.
Advantages of Rogers Materials:
– Excellent high-frequency performance due to low dielectric constant and loss tangent
– Good thermal conductivity for better heat dissipation
– Stable mechanical and electrical properties over a wide temperature range
Disadvantages of Rogers Materials:
– Higher cost compared to FR-4 and other standard substrates
– More challenging to process due to their unique properties
4. Polyimide
Polyimide is a high-performance polymer substrate known for its excellent thermal stability, mechanical strength, and chemical resistance. It can withstand extremely high temperatures (up to 400°C) and is often used in applications that require reliability in harsh environments, such as aerospace, military, and oil and gas industries.
Advantages of Polyimide:
– Exceptional thermal stability and high temperature resistance
– Excellent mechanical strength and flexibility
– Good chemical resistance
– Low dielectric constant and loss tangent
Disadvantages of Polyimide:
– Higher cost compared to FR-4 and other standard substrates
– More challenging to process due to its unique properties
5. Aluminum
Aluminum PCB substrates consist of an aluminum base with a thin layer of dielectric material (usually a polymer) bonded to one or both sides. The dielectric layer is then coated with copper to create the circuit pattern. Aluminum substrates offer excellent thermal conductivity, making them ideal for applications that require efficient heat dissipation, such as high-power electronics and LED lighting.
Advantages of Aluminum Substrates:
– Excellent thermal conductivity for efficient heat dissipation
– Good mechanical stability and durability
– Lightweight compared to other metal-based substrates
Disadvantages of Aluminum Substrates:
– Higher cost compared to FR-4 and other standard substrates
– Limited flexibility and bendability
– Potential for thermal expansion mismatch with components
Properties of PCB Substrates
When choosing a PCB substrate, several key properties must be considered to ensure the desired performance and reliability of the final product. These properties include:
1. Dielectric Constant (Dk)
The dielectric constant (Dk) is a measure of a material’s ability to store electrical energy. In PCB substrates, a lower Dk value is generally desirable, especially for high-frequency applications, as it results in faster signal propagation and reduced signal loss. The dielectric constant of a substrate can vary with frequency and temperature.
2. Loss Tangent (Df)
The loss tangent (Df) is a measure of a material’s ability to dissipate electrical energy as heat. A lower loss tangent is desirable for PCB substrates, as it minimizes signal loss and thermal generation. Like the dielectric constant, the loss tangent can vary with frequency and temperature.
3. Thermal Conductivity
Thermal conductivity is a measure of a material’s ability to conduct heat. PCB substrates with higher thermal conductivity can more efficiently dissipate the heat generated by components, improving the overall thermal management of the system. This is particularly important for high-power applications or designs with high component density.
4. Glass Transition Temperature (Tg)
The glass transition temperature (Tg) is the temperature at which a material transitions from a rigid, glassy state to a softer, more flexible state. In PCB substrates, a higher Tg is desirable, as it indicates better thermal stability and the ability to maintain its mechanical and electrical properties at elevated temperatures.
5. Coefficient of Thermal Expansion (CTE)
The coefficient of thermal expansion (CTE) is a measure of how much a material expands or contracts with changes in temperature. In PCB substrates, a lower CTE is generally preferable, as it minimizes the risk of thermal expansion mismatch between the substrate and the components mounted on it. This mismatch can lead to mechanical stress, warpage, and even failure of the solder joints.
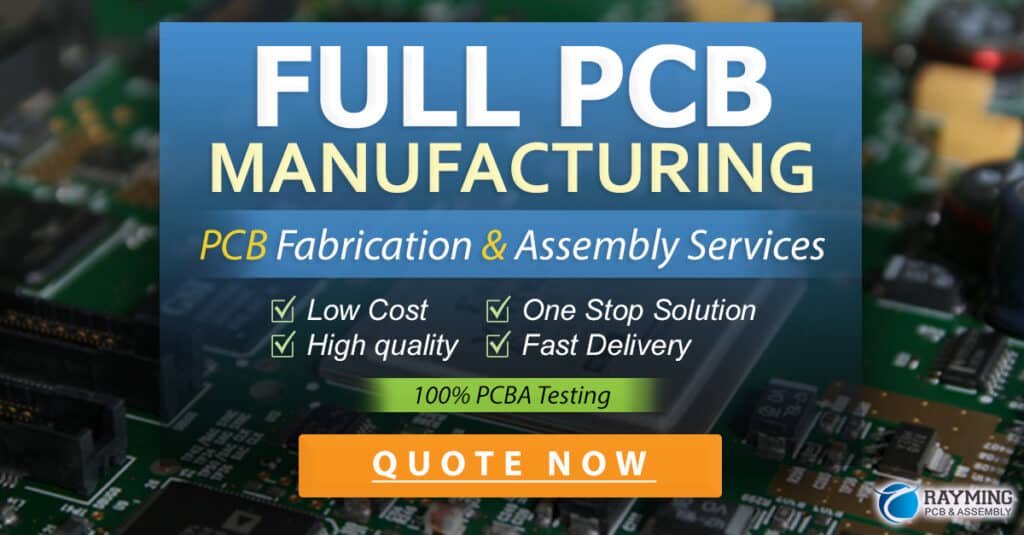
Impact of Substrate Choice on PCB Performance
The choice of PCB substrate can have a significant impact on the performance and reliability of the final product. Some key areas where substrate selection plays a crucial role include:
1. Signal Integrity
In high-frequency applications, the dielectric constant and loss tangent of the substrate directly influence signal integrity. Substrates with lower Dk and Df values, such as Rogers materials, can help minimize signal loss, distortion, and crosstalk, ensuring better signal quality and reliability.
2. Thermal Management
The thermal conductivity of the substrate affects the PCB’s ability to dissipate heat generated by the components. Substrates with higher thermal conductivity, such as aluminum or high-performance ceramics, can help prevent overheating and improve the overall thermal management of the system.
3. Mechanical Stability
The mechanical properties of the substrate, such as its stiffness, strength, and CTE, influence the PCB’s ability to withstand physical stress and maintain its dimensional stability. Choosing a substrate with the appropriate mechanical properties for the intended application can help ensure the long-term reliability and durability of the PCB.
4. Cost and Manufacturability
The choice of substrate also affects the cost and manufacturability of the PCB. Standard materials like FR-4 are generally more cost-effective and easier to process than high-performance substrates like Rogers materials or polyimide. However, the improved performance and reliability offered by these advanced substrates may justify the additional cost and complexity for certain applications.
Frequently Asked Questions (FAQ)
1. What is the most common PCB substrate material?
The most common PCB substrate material is FR-4, a composite made from woven fiberglass cloth impregnated with an epoxy resin binder. FR-4 is widely used due to its good mechanical strength, excellent electrical insulation properties, reasonable thermal stability, and cost-effectiveness.
2. What are high-frequency PCB substrates?
High-frequency PCB substrates are materials specifically designed for applications operating at high frequencies, typically in the microwave and millimeter-wave ranges. These substrates have low dielectric constant and loss tangent values, which help minimize signal loss and distortion. Examples of high-frequency substrates include Rogers materials, such as RO4003C, RO4350B, and RT/duroid 5880.
3. Why are aluminum PCB substrates used?
Aluminum PCB substrates are used in applications that require efficient heat dissipation, such as high-power electronics and LED lighting. The aluminum base provides excellent thermal conductivity, allowing the PCB to quickly transfer heat away from the components and prevent overheating. This improves the overall thermal management of the system and enhances its reliability.
4. What is the difference between Tg and Td in PCB substrates?
Tg (Glass Transition Temperature) and Td (Decomposition Temperature) are both important thermal properties of PCB substrates, but they represent different aspects of a material’s behavior:
- Tg is the temperature at which a material transitions from a rigid, glassy state to a softer, more flexible state. It is a reversible change and does not involve chemical decomposition.
- Td is the temperature at which a material begins to chemically decompose and break down irreversibly.
In PCB design, Tg is often used as a reference for the maximum operating temperature of the substrate, while Td represents the ultimate limit beyond which the material will degrade and fail.
5. Can I use FR-4 for high-frequency applications?
While FR-4 is a popular and cost-effective substrate for many applications, it has limitations when it comes to high-frequency performance. FR-4 has a relatively high dielectric constant and loss tangent compared to specialized high-frequency substrates like Rogers materials. As a result, using FR-4 in high-frequency applications can lead to increased signal loss, distortion, and poor signal integrity.
For applications operating at frequencies above a few gigahertz, it is generally recommended to use substrates specifically designed for high-frequency performance, such as Rogers materials or other low-loss substrates. These materials have lower dielectric constant and loss tangent values, which help minimize the issues associated with using FR-4 in high-frequency designs.
Conclusion
In summary, the substrate is a critical component of a printed circuit board, serving as the foundation upon which the circuit is built. The choice of substrate material depends on various factors, including the intended application, operating environment, required performance characteristics, and cost.
Common PCB substrates include FR-4, High Tg FR-4, Rogers materials, polyimide, and aluminum, each with its own set of properties and advantages. When selecting a substrate, designers must consider key properties such as dielectric constant, loss tangent, thermal conductivity, glass transition temperature, and coefficient of thermal expansion.
The choice of substrate can significantly impact the performance and reliability of the final product, influencing signal integrity, thermal management, mechanical stability, and manufacturability. By understanding the properties and characteristics of different PCB substrates, designers can make informed decisions and choose the most suitable material for their specific application, ensuring optimal performance and long-term reliability.
As technology continues to advance and new applications emerge, the development of innovative PCB substrate materials will play a crucial role in enabling the next generation of electronic devices and systems.
| Substrate | Dielectric Constant (Dk) | Loss Tangent (Df) | Thermal Conductivity (W/mK) | Glass Transition Temperature (Tg) |
|-------------|--------------------------|-------------------|------------------------------|-----------------------------------|
| FR-4 | 4.3-4.6 @ 1 MHz | 0.02 @ 1 MHz | 0.3-0.4 | 130-140°C |
| High Tg FR-4| 4.3-4.6 @ 1 MHz | 0.02 @ 1 MHz | 0.3-0.4 | 170-180°C |
| RO4003C | 3.38 @ 10 GHz | 0.0027 @ 10 GHz | 0.64 | >280°C |
| RO4350B | 3.48 @ 10 GHz | 0.0037 @ 10 GHz | 0.62 | >280°C |
| RT/duroid 5880| 2.20 @ 10 GHz | 0.0009 @ 10 GHz | 0.20 | >260°C |
| Polyimide | 3.4-3.5 @ 1 MHz | 0.002-0.003 @ 1 MHz| 0.1-0.4 | >300°C |
| Aluminum | Depends on dielectric layer | Depends on dielectric layer | 150-220 | Depends on dielectric layer |
This table provides a comparison of key properties for common PCB substrates, including dielectric constant (Dk), loss tangent (Df), thermal conductivity, and glass transition temperature (Tg). Note that the values for aluminum substrates depend on the specific dielectric layer used, as the aluminum base itself is not an insulating material.
Leave a Reply