Understanding Small PCBs
Definition and Characteristics
A small PCB is a miniaturized version of a standard printed circuit board. These boards are designed to fit within compact electronic devices while still providing the necessary connectivity and functionality. The main characteristics of small PCBs include:
- Reduced size: Small PCBs are typically less than 50mm x 50mm in size, although the exact dimensions may vary depending on the specific application.
- High component density: Due to their limited space, small PCBs often feature a high density of components, requiring precise placement and routing.
- Multilayer designs: To accommodate complex circuitry within a small area, small PCBs often utilize multilayer designs, with conductive layers stacked and interconnected through vias.
Advantages of Small PCBs
Small PCBs offer several advantages over their larger counterparts:
- Space savings: The compact size of small PCBs allows for the development of smaller, more portable electronic devices.
- Cost-effectiveness: Smaller PCBs require less material and can be produced in larger quantities, reducing overall manufacturing costs.
- Improved performance: The reduced size of small PCBs minimizes signal propagation delays and power losses, leading to improved system performance.
- Enhanced reliability: With fewer connections and shorter traces, small PCBs are less susceptible to noise and interference, resulting in enhanced reliability.
Applications of Small PCBs
Small PCBs find applications across a wide range of industries and devices. Some common applications include:
Consumer Electronics
- Smartphones and tablets
- Wearable devices (e.g., smartwatches, fitness trackers)
- Wireless earbuds and headphones
- Digital cameras and portable media players
Medical Devices
- Implantable medical devices (e.g., pacemakers, cochlear implants)
- Portable medical monitoring systems
- Wearable health sensors
- Miniaturized surgical instruments
Automotive Electronics
- Sensors and control modules
- In-vehicle infotainment systems
- Advanced driver assistance systems (ADAS)
- Electronic control units (ECUs)
Industrial Automation
- Compact sensors and actuators
- Miniaturized control systems
- Wireless communication modules
- Embedded systems for IoT applications
Designing Small PCBs
Designing small PCBs requires careful consideration of various factors to ensure optimal performance and manufacturability. Some key design aspects include:
Component Selection
When designing a small PCB, it’s crucial to select components that are compact, surface-mountable, and compatible with the intended application. Some common component packages for small PCBs include:
- Chip-scale packages (CSPs)
- Quad-flat no-lead (QFN) packages
- Ball grid arrays (BGAs)
- Wafer-level chip-scale packages (WLCSPs)
Layout and Routing
Efficient layout and routing are essential for small PCBs to minimize signal integrity issues and ensure proper functionality. Designers should consider the following:
- Component placement: Optimize component placement to minimize trace lengths and reduce signal interference.
- Trace width and spacing: Use appropriate trace widths and spacing to minimize crosstalk and ensure manufacturability.
- Via placement: Strategically place vias to minimize signal reflections and maintain signal integrity.
- Ground and power planes: Incorporate ground and power planes to provide a low-impedance return path and minimize noise.
Thermal Management
Small PCBs with high component density can generate significant amounts of heat, which can affect device performance and reliability. Proper thermal management techniques should be employed, such as:
- Thermal vias: Use thermal vias to conduct heat away from components and into the PCB substrate.
- Heatsinks and thermal pads: Incorporate heatsinks and thermal pads to dissipate heat from high-power components.
- Copper pours: Use copper pours on the PCB surface to distribute heat more evenly and improve thermal performance.
Signal Integrity and EMI/EMC Considerations
Maintaining signal integrity and minimizing electromagnetic interference (EMI) and electromagnetic compatibility (EMC) issues are critical when designing small PCBs. Designers should consider the following:
- Impedance matching: Ensure proper impedance matching between components and traces to minimize signal reflections and distortions.
- Differential pair routing: Use differential pair routing for high-speed signals to minimize crosstalk and EMI.
- Shielding: Incorporate shielding techniques, such as grounded copper pours or metal enclosures, to reduce EMI and improve EMC performance.
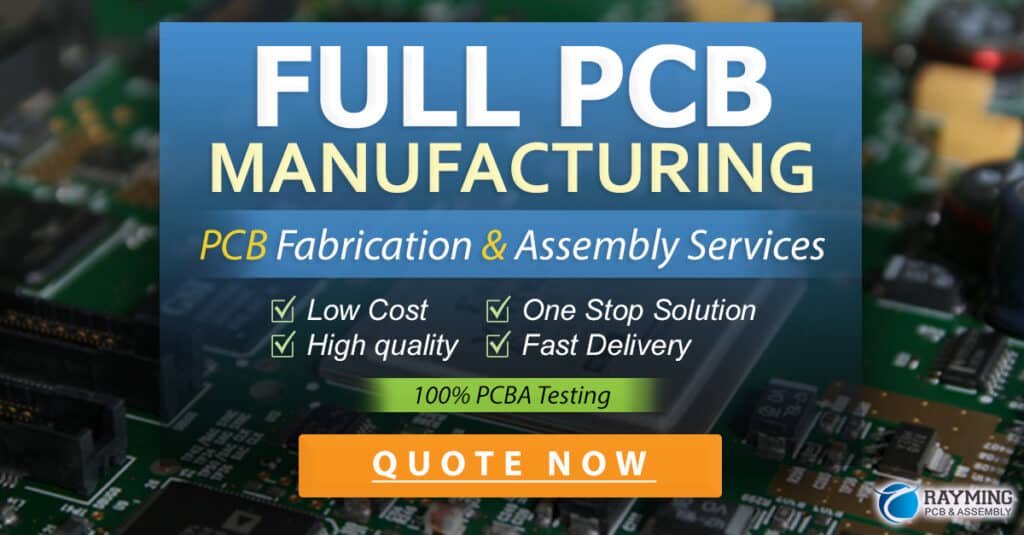
Manufacturing Small PCBs
The manufacturing process for small PCBs involves several key steps to ensure high quality and reliability.
PCB Fabrication
- Substrate preparation: The PCB substrate, typically FR-4, is cleaned and prepared for the subsequent steps.
- Copper cladding: A thin layer of copper is laminated onto the substrate to form the conductive layer.
- Photoresist application: A photoresist layer is applied to the copper surface and exposed to UV light through a photomask, which defines the desired circuit pattern.
- Etching: The exposed copper is etched away, leaving only the desired circuit pattern on the substrate.
- Drilling and plating: Holes are drilled through the PCB, and the walls of the holes are plated with copper to form vias and through-hole connections.
- Solder mask application: A solder mask layer is applied to the PCB surface to protect the copper traces and prevent solder bridging.
- Silkscreen printing: A silkscreen layer is printed onto the PCB to provide component labels, logos, and other markings.
Component Assembly
- Solder paste application: Solder paste is applied to the PCB pads using a stencil or screen printing process.
- Component placement: Components are placed onto the PCB using automated pick-and-place machines or manual assembly methods.
- Reflow soldering: The PCB is heated in a reflow oven, melting the solder paste and forming a strong mechanical and electrical connection between the components and the PCB.
- Inspection and testing: The assembled PCB undergoes visual inspection and electrical testing to ensure proper functionality and quality.
Quality Control and Testing
To ensure the reliability and performance of small PCBs, various quality control and testing procedures are employed, including:
- Automated optical inspection (AOI): AOI systems use high-resolution cameras to detect manufacturing defects, such as missing components or solder bridges.
- X-ray inspection: X-ray imaging is used to inspect the internal structure of the PCB, including vias, solder joints, and component placement.
- Functional testing: Assembled PCBs are subjected to functional tests to verify their performance under various operating conditions.
- Environmental testing: Small PCBs may undergo environmental testing, such as temperature cycling or vibration testing, to ensure their reliability in harsh environments.
Future Trends in Small PCB Technology
As electronic devices continue to shrink in size and increase in complexity, small PCB technology must adapt to meet new challenges and demands. Some future trends in small PCB technology include:
Advanced Materials
The development of advanced PCB materials, such as high-frequency laminates and flexible substrates, will enable the design of smaller, high-performance PCBs for emerging applications.
3D Printing
The use of 3D printing technology for PCB fabrication may allow for the creation of complex, three-dimensional PCB structures with enhanced functionality and reduced size.
Embedded Components
The integration of components directly into the PCB substrate, known as embedded component technology, can further reduce the size and increase the density of small PCBs.
High-Density Interconnect (HDI)
HDI PCBs, which feature fine-pitch traces and micro-vias, will continue to be essential for the development of compact, high-performance electronic devices.
Frequently Asked Questions (FAQ)
- What is the typical size of a small PCB?
Small PCBs are typically less than 50mm x 50mm in size, although the exact dimensions may vary depending on the specific application and design requirements.
- What are the advantages of using small PCBs in electronic devices?
Small PCBs offer several advantages, including space savings, cost-effectiveness, improved performance, and enhanced reliability. They enable the development of compact, portable, and efficient electronic devices.
- What are some common applications for small PCBs?
Small PCBs find applications in various industries, such as consumer electronics (smartphones, wearables), medical devices (implantables, monitoring systems), automotive electronics (sensors, control modules), and industrial automation (compact sensors, IoT devices).
- What are the key design considerations when developing small PCBs?
When designing small PCBs, key considerations include component selection (compact, surface-mountable packages), efficient layout and routing (minimizing trace lengths, proper via placement), thermal management (thermal vias, heatsinks), and signal integrity (impedance matching, differential pair routing, shielding).
- What are some future trends in small PCB technology?
Future trends in small PCB technology include the use of advanced materials (high-frequency laminates, flexible substrates), 3D printing for complex PCB structures, embedded component technology, and the continued development of high-density interconnect (HDI) PCBs.
Conclusion
Small PCBs are essential components in the ever-evolving world of electronics, enabling the development of compact, efficient, and cost-effective devices. By understanding the characteristics, applications, design considerations, and manufacturing processes associated with small PCBs, engineers and designers can create innovative solutions that meet the demands of today’s technology landscape. As electronic devices continue to shrink in size and increase in complexity, the importance of small PCB technology will only continue to grow, driving advancements in various industries and shaping the future of electronics.
Leave a Reply