What is a PCB Shield?
A PCB shield is a metal enclosure that surrounds a specific area of a printed circuit board to protect the components within from electromagnetic interference. It acts as a barrier, preventing unwanted signals from entering or leaving the shielded region. PCB shields are crucial in ensuring the proper functioning and reliability of electronic devices, especially in environments with high levels of EMI or RFI.
Why are PCB Shields Important?
PCB shields play a vital role in maintaining the integrity of electronic circuits. Here are some key reasons why PCB shields are important:
-
EMI Protection: PCB shields help protect sensitive electronic components from electromagnetic interference, which can cause signal distortion, data corruption, or even complete system failure.
-
RFI Reduction: Shields minimize the impact of radio frequency interference on PCB circuits, ensuring clear and reliable communication between components.
-
Signal Integrity: By isolating specific areas of the PCB, shields help maintain signal integrity and prevent crosstalk between different sections of the board.
-
Compliance with Regulations: Many industries have strict regulations regarding EMI and RFI emissions. PCB shields help ensure compliance with these standards, such as FCC and CE regulations.
Types of PCB Shields
There are several types of PCB shields available, each with its own characteristics and applications. Let’s explore the most common types:
1. One-Piece Shields
One-piece shields, also known as can shields, are the simplest and most cost-effective type of PCB shield. They are typically made of metal and cover the entire area that needs to be shielded. One-piece shields are ideal for small to medium-sized PCBs with relatively simple shielding requirements.
2. Two-Piece Shields
Two-piece shields consist of a frame and a removable lid. The frame is soldered onto the PCB, and the lid is attached to the frame using snap-fits or screws. Two-piece shields offer better accessibility to the shielded components compared to one-piece shields, making them suitable for PCBs that require frequent maintenance or debugging.
3. Custom Shields
Custom shields are designed and manufactured according to specific PCB requirements. They can be tailored to fit unique board shapes, accommodate special components, or provide additional features like heat dissipation or grounding. Custom shields are often used in complex or high-performance applications where standard shield designs may not suffice.
Shield Materials
PCB shields can be made from various materials, each with its own properties and benefits. The most common materials used for PCB shields are:
-
Aluminum: Aluminum is lightweight, cost-effective, and provides good shielding effectiveness. It is often used in consumer electronics and general-purpose applications.
-
Stainless Steel: Stainless steel offers excellent durability and corrosion resistance. It is commonly used in industrial and harsh environments.
-
Copper: Copper shields provide superior shielding effectiveness due to their high electrical conductivity. They are often used in high-frequency applications or where maximum shielding performance is required.
-
Nickel Silver: Nickel silver, an alloy of copper, nickel, and zinc, combines good shielding effectiveness with attractive aesthetics. It is commonly used in consumer electronics and decorative applications.
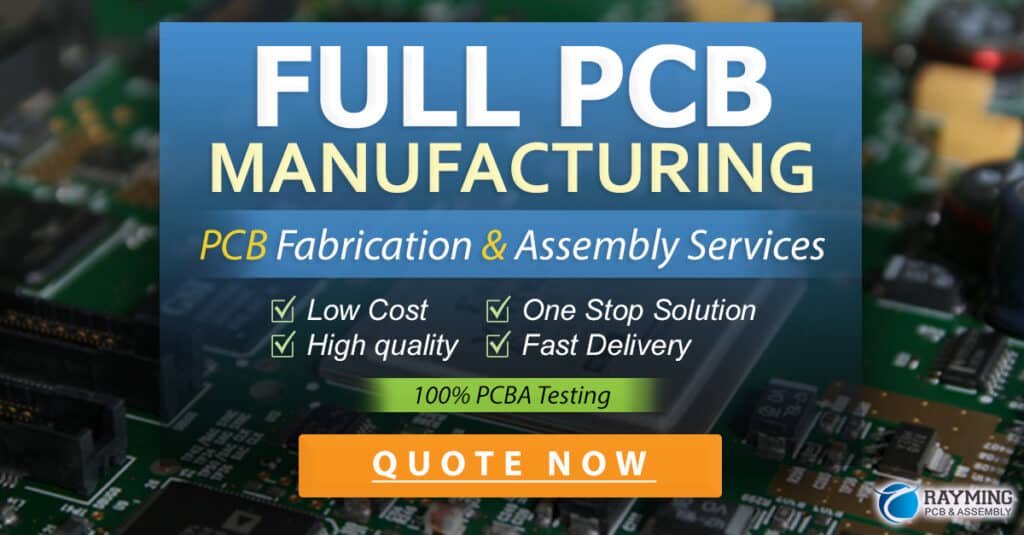
Shielding Effectiveness
Shielding effectiveness (SE) is a measure of how well a shield attenuates electromagnetic energy. It is expressed in decibels (dB) and represents the ratio of the incident energy to the transmitted energy through the shield. The higher the SE value, the better the shielding performance.
Factors that influence shielding effectiveness include:
- Material properties (conductivity, permeability)
- Shield thickness
- Frequency of the electromagnetic waves
- Aperture size and shape (gaps, holes, seams)
To achieve optimal shielding effectiveness, designers must carefully consider these factors and select the appropriate shield material, thickness, and design.
PCB Shield Design Considerations
Designing an effective PCB shield involves several key considerations. Let’s discuss some of the most important aspects:
1. Grounding
Proper grounding is essential for effective shielding. The shield should be electrically connected to the PCB ground plane to provide a low-impedance path for electromagnetic energy to be diverted away from sensitive components. Grounding can be achieved through direct contact, conductive gaskets, or dedicated grounding points.
2. Apertures and Seams
Apertures (holes) and seams in the shield can compromise its effectiveness by allowing electromagnetic energy to leak through. It is crucial to minimize the size and number of apertures and ensure that seams are properly sealed. Conductive gaskets, overlapping joints, or welding can be used to maintain shielding integrity.
3. Frequency Range
The frequency range of the electromagnetic interference should be considered when selecting the shield material and designing the shield. Different materials have varying shielding effectiveness across different frequency ranges. For example, aluminum is more effective at lower frequencies, while copper performs better at higher frequencies.
4. Component Placement
The placement of components within the shielded area is crucial for optimal performance. Sensitive components should be placed away from potential sources of interference, such as power lines or high-speed digital circuits. Additionally, the shield should provide sufficient clearance for components and allow for proper airflow to prevent overheating.
5. Manufacturing Considerations
When designing PCB shields, it is essential to consider manufacturing constraints. The shield design should be compatible with the pcb fabrication and assembly processes. Factors such as shield attachment methods, tolerances, and accessibility for automated assembly should be taken into account to ensure a cost-effective and manufacturable design.
PCB Shield Attachment Methods
There are several methods for attaching PCB shields to the board. The choice of attachment method depends on factors such as shield type, board design, and manufacturing requirements. Common attachment methods include:
-
Soldering: Shields can be directly soldered onto the PCB using through-hole or surface-mount techniques. Soldering provides a strong mechanical and electrical connection but may require additional assembly steps.
-
Snap-Fits: Two-piece shields often use snap-fits to secure the lid to the frame. Snap-fits allow for easy assembly and disassembly without the need for tools or soldering.
-
Screws: Screws can be used to attach shields to the PCB or to secure the lid to the frame in two-piece designs. Screws provide a robust mechanical connection but may increase assembly time and cost.
-
Conductive Adhesives: Conductive adhesives, such as conductive epoxies or tapes, can be used to attach shields to the PCB. They offer a simple and quick attachment method but may not provide as strong a connection as soldering or screws.
Testing and Verification
Once the PCB shield is designed and manufactured, it is essential to test and verify its performance to ensure it meets the desired shielding requirements. Several methods can be used to assess shield effectiveness:
-
EMI/RFI Testing: EMI/RFI testing involves subjecting the shielded PCB to controlled electromagnetic interference and measuring the level of interference that penetrates the shield. This testing can be performed in specialized labs or using portable test equipment.
-
Near-Field Probing: Near-field probing uses small antennas or probes to measure the electromagnetic fields in close proximity to the shield. This method helps identify areas of weakness or leakage in the shield design.
-
Transfer Impedance Measurement: Transfer impedance is a measure of the shield’s ability to attenuate electromagnetic energy. It is calculated by measuring the voltage induced on the inside of the shield when a current is applied to the outside. Lower transfer impedance values indicate better shielding performance.
-
Simulation and Modeling: Electromagnetic simulation software can be used to model and analyze shield performance before physical prototyping. These tools help optimize shield design and identify potential issues early in the development process.
Best Practices for PCB Shield Design
To ensure optimal shielding performance and reliability, consider the following best practices when designing PCB shields:
-
Keep Shields Simple: Avoid complex shield geometries and minimize the number of apertures and seams. Simple designs are easier to manufacture and provide better shielding effectiveness.
-
Maximize Shielding Coverage: Ensure that the shield covers all sensitive components and traces that require protection. Avoid leaving gaps or exposed areas that could allow electromagnetic interference to penetrate.
-
Use Appropriate Grounding Techniques: Properly ground the shield to the PCB using low-impedance connections. Use multiple grounding points to minimize the risk of ground loops and ensure a stable reference plane.
-
Consider Thermal Management: Shields can affect the thermal performance of the PCB by trapping heat inside the enclosure. Incorporate adequate ventilation or heat dissipation techniques to prevent overheating of shielded components.
-
Collaborate with Manufacturers: Work closely with PCB fabrication and assembly partners to ensure that the shield design is compatible with their processes and capabilities. Consider their feedback and recommendations to optimize the design for manufacturability and cost-effectiveness.
Frequently Asked Questions (FAQ)
-
Q: What is the difference between EMI and RFI?
A: EMI (electromagnetic interference) refers to any electromagnetic disturbance that disrupts the normal operation of electronic devices. RFI (radio frequency interference) is a specific type of EMI that occurs in the radio frequency spectrum, typically between 3 kHz and 300 GHz. -
Q: Can PCB shields be used for waterproofing?
A: PCB shields are primarily designed for electromagnetic shielding and not for waterproofing. However, some shield materials and designs can provide a certain level of protection against moisture and dust. For specific waterproofing requirements, additional measures such as conformal coatings or sealed enclosures may be necessary. -
Q: How do I select the right shield material for my application?
A: The choice of shield material depends on factors such as the frequency range of the interference, shielding effectiveness requirements, environmental conditions, and cost constraints. Aluminum is a common choice for general-purpose applications, while copper and stainless steel offer higher performance in demanding environments. Consult with shielding experts or refer to material datasheets to make an informed decision. -
Q: Can PCB shields be reused?
A: In most cases, PCB shields are designed for single use and are not meant to be reused. The removal process, especially for soldered shields, can damage the shield or the PCB. However, some two-piece shield designs with removable lids may allow for limited reuse if handled carefully. -
Q: How can I minimize the cost of PCB shielding?
A: To minimize the cost of PCB shielding, consider the following strategies: - Optimize shield design for simplicity and ease of manufacturing.
- Choose cost-effective shield materials that meet performance requirements.
- Minimize the shield size and coverage area to reduce material usage.
- Consider alternative shielding methods, such as grounded copper traces or conformal shielding, where applicable.
- Work with experienced PCB fabrication and assembly partners to identify cost-saving opportunities in the manufacturing process.
Conclusion
PCB shields are vital components in protecting sensitive electronic circuits from electromagnetic interference and ensuring the proper functioning and reliability of electronic devices. By understanding the types of shields, materials, design considerations, and best practices, designers can create effective and efficient shielding solutions for their pcb projects.
When designing PCB shields, it is essential to consider factors such as shielding effectiveness, grounding, apertures and seams, frequency range, component placement, and manufacturing constraints. Proper testing and verification should be conducted to validate shield performance and identify any areas for improvement.
By following best practices and collaborating with experienced PCB fabrication and assembly partners, designers can optimize their shield designs for maximum effectiveness, reliability, and cost-efficiency. With the right approach, PCB shields can provide robust protection against electromagnetic interference, enabling electronic devices to operate safely and reliably in diverse environments.
Leave a Reply