Introduction to Rogers PCB
A Rogers PCB, also known as a high-frequency printed circuit board, is a specialized type of PCB designed to operate at high frequencies with minimal signal loss and distortion. These PCBs are manufactured using advanced materials developed by Rogers Corporation, a leading provider of high-performance electronic materials for various applications.
Rogers PCBs are widely used in high-frequency and high-speed applications, such as:
- Wireless communication systems
- Radar and satellite technology
- Automotive radar sensors
- 5G infrastructure
- Aerospace and defense systems
- Medical imaging equipment
The unique properties of rogers pcb materials enable the fabrication of circuit boards that can handle high-frequency signals with excellent signal integrity, making them essential for modern electronic devices and systems.
Advantages of Rogers PCB
Rogers PCBs offer several advantages over traditional FR-4 PCBs, making them the preferred choice for high-frequency applications:
-
Low dielectric constant and dissipation factor: Rogers materials have a low dielectric constant (Dk) and dissipation factor (Df), which minimizes signal loss and distortion at high frequencies. This property ensures that the signals maintain their integrity as they travel through the PCB.
-
High thermal conductivity: Rogers PCB materials have excellent thermal conductivity, which helps dissipate heat efficiently. This property is crucial for high-power applications, as it prevents the PCB from overheating and ensures reliable operation.
-
Dimensional stability: Rogers materials maintain their dimensions and properties over a wide range of temperatures and humidity levels. This stability is essential for applications that require consistent performance in varying environmental conditions.
-
Low moisture absorption: Rogers PCB materials have low moisture absorption rates, which helps maintain the board’s electrical and mechanical properties even in humid environments. This property is particularly important for outdoor applications or devices exposed to moisture.
-
Excellent high-frequency performance: The combination of low dielectric constant, low dissipation factor, and high thermal conductivity makes Rogers PCBs ideal for high-frequency applications. These properties enable the PCBs to handle high-speed signals with minimal losses and distortion.
Popular Rogers PCB Materials
Rogers Corporation offers a range of high-performance materials for PCB fabrication. Some of the most popular Rogers PCB materials include:
-
RT/duroid®: This material is known for its low dielectric constant, low dissipation factor, and excellent thermal conductivity. It is widely used in microwave and RF applications, such as wireless communication systems and radar technology.
-
RO4000® Series: The RO4000® series materials offer a balance of high-performance and cost-effectiveness. They have a low dielectric constant and dissipation factor, making them suitable for a wide range of high-frequency applications, including automotive radar sensors and 5G infrastructure.
-
TMM® Laminates: TMM® laminates are designed for high-frequency applications that require a low dielectric constant and dissipation factor. These materials are often used in aerospace and defense systems, as well as in medical imaging equipment.
-
CLTE Series: The CLTE series materials are characterized by their low thermal expansion coefficient, which ensures excellent dimensional stability over a wide temperature range. These materials are ideal for applications that require consistent performance in varying environmental conditions.
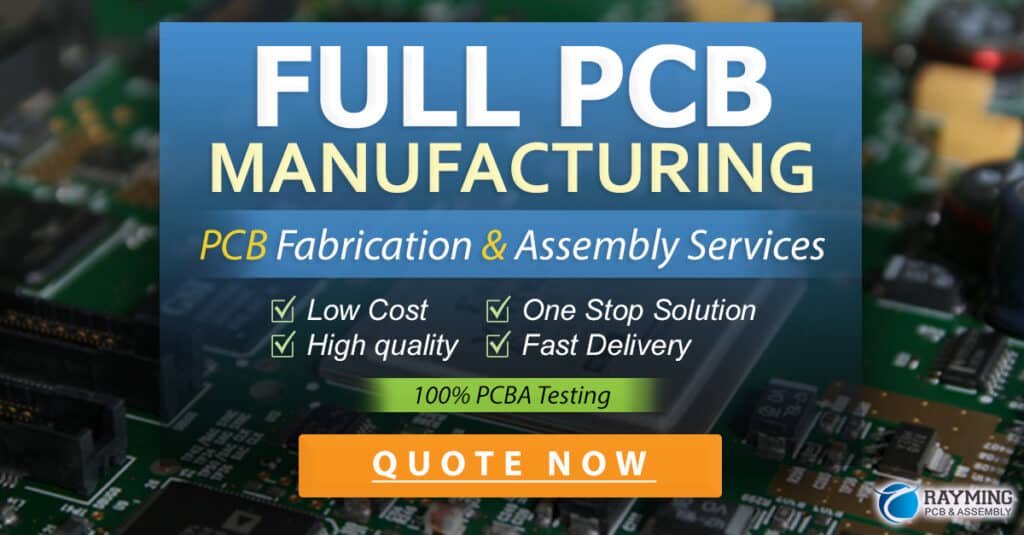
Rogers PCB Fabrication Process
The fabrication process for Rogers PCBs is similar to that of traditional FR-4 PCBs, but with some additional considerations due to the unique properties of Rogers materials:
-
Material selection: The first step in Rogers PCB fabrication is selecting the appropriate material based on the application’s requirements, such as frequency range, power handling, and environmental conditions.
-
PCB design: The PCB layout is designed using specialized software, taking into account the specific properties of the Rogers material. The design must ensure proper impedance matching, signal routing, and grounding to minimize signal loss and distortion.
-
Lamination: The Rogers material is laminated to the copper foil using high temperature and pressure. This process ensures a strong bond between the layers and minimizes the risk of delamination.
-
Drilling and plating: Holes are drilled through the laminated board, and the holes are plated with copper to create electrical connections between layers.
-
Patterning: The desired circuit pattern is transferred to the copper layer using photolithography and etching processes. The unwanted copper is removed, leaving only the desired circuit traces.
-
Solder mask and silkscreen: A solder mask is applied to the board to protect the copper traces from oxidation and prevent short circuits. A silkscreen layer is added to provide component labels and other markings.
-
Surface finish: A surface finish, such as ENIG (Electroless Nickel Immersion Gold) or HASL (Hot Air Solder Leveling), is applied to the exposed copper areas to prevent oxidation and improve solderability.
-
Electrical testing: The finished Rogers PCB undergoes electrical testing to ensure that it meets the required specifications and performance criteria.
Applications of Rogers PCB
Rogers PCBs find applications in various industries due to their superior high-frequency performance and reliability. Some of the most common applications include:
Wireless Communication Systems
Rogers PCBs are extensively used in wireless communication systems, such as cellular base stations, satellite communication systems, and wireless routers. The low dielectric constant and dissipation factor of Rogers materials ensure minimal signal loss and distortion, enabling efficient and reliable communication.
Radar and Satellite Technology
High-frequency radar systems and satellite technology rely on Rogers PCBs for their ability to handle high-power signals with excellent signal integrity. The high thermal conductivity of Rogers materials helps dissipate heat efficiently, ensuring reliable operation in demanding environments.
Automotive Radar Sensors
Advanced driver assistance systems (ADAS) and autonomous vehicles rely on automotive radar sensors to detect obstacles and navigate safely. Rogers PCBs are used in these sensors due to their low dielectric constant and dissipation factor, which enable accurate and reliable detection of objects at high frequencies.
5G Infrastructure
The deployment of 5G networks requires high-frequency PCBs that can handle the increased data rates and bandwidth. Rogers PCBs are an essential component in 5G infrastructure, enabling efficient signal transmission and reception at millimeter-wave frequencies.
Aerospace and Defense Systems
Aerospace and defense systems often operate in harsh environments and require PCBs that can withstand extreme temperatures and humidity levels. Rogers PCBs, with their excellent dimensional stability and low moisture absorption, are well-suited for these demanding applications.
Medical Imaging Equipment
Medical imaging equipment, such as MRI and X-ray machines, requires high-frequency PCBs to generate and process high-resolution images. Rogers PCBs are used in these applications due to their low dielectric constant and dissipation factor, which enable accurate signal processing and imaging.
Comparison of Rogers PCB with Traditional FR-4 PCB
Property | Rogers PCB | Traditional FR-4 PCB |
---|---|---|
Dielectric Constant (Dk) | Low (2.2 to 10.2) | Higher (4.2 to 4.6) |
Dissipation Factor (Df) | Low (0.0009 to 0.0035) | Higher (0.02) |
Thermal Conductivity | High (0.4 to 1.5 W/m·K) | Lower (0.3 W/m·K) |
Dimensional Stability | Excellent | Good |
Moisture Absorption | Low (0.02% to 0.25%) | Higher (0.1% to 0.3%) |
High-Frequency Performance | Excellent | Poor |
Cost | Higher | Lower |
As evident from the comparison, Rogers PCBs offer superior high-frequency performance and reliability compared to traditional FR-4 PCBs. However, these advantages come at a higher cost, making Rogers PCBs more suitable for applications that demand the highest level of performance and reliability.
FAQ
-
Q: What is the main difference between Rogers PCBs and traditional FR-4 PCBs?
A: The main difference between Rogers PCBs and traditional FR-4 PCBs lies in their high-frequency performance. Rogers PCBs have a lower dielectric constant and dissipation factor, which minimizes signal loss and distortion at high frequencies. In contrast, FR-4 PCBs have higher dielectric constant and dissipation factor, making them less suitable for high-frequency applications. -
Q: Can Rogers PCBs be used for low-frequency applications?
A: While Rogers PCBs are primarily designed for high-frequency applications, they can also be used for low-frequency applications. However, due to their higher cost compared to traditional FR-4 PCBs, it may not be economically viable to use Rogers PCBs for low-frequency applications unless there are specific requirements for thermal conductivity or dimensional stability. -
Q: What are the most popular Rogers PCB materials?
A: The most popular Rogers PCB materials include RT/duroid®, RO4000® Series, TMM® Laminates, and CLTE Series. Each material has its unique properties and is suited for specific applications based on factors such as frequency range, power handling, and environmental conditions. -
Q: How do I select the appropriate Rogers PCB material for my application?
A: Selecting the appropriate Rogers PCB material depends on several factors, such as the frequency range, power handling requirements, and environmental conditions. It is essential to consult with a Rogers PCB manufacturer or an experienced RF engineer to determine the most suitable material for your specific application. -
Q: Are Rogers PCBs more expensive than traditional FR-4 PCBs?
A: Yes, Rogers PCBs are generally more expensive than traditional FR-4 PCBs due to the advanced materials and specialized manufacturing processes involved. However, the superior high-frequency performance and reliability offered by Rogers PCBs justify the higher cost for applications that demand the highest level of performance.
Conclusion
Rogers PCBs are specialized high-frequency printed circuit boards designed to handle high-speed signals with minimal loss and distortion. These PCBs are manufactured using advanced materials developed by Rogers Corporation, which offer low dielectric constant, low dissipation factor, high thermal conductivity, and excellent dimensional stability.
Rogers PCBs find applications in various industries, including wireless communication systems, radar and satellite technology, automotive radar sensors, 5G infrastructure, aerospace and defense systems, and medical imaging equipment. The superior high-frequency performance and reliability of Rogers PCBs make them essential for modern electronic devices and systems that operate at high frequencies.
While Rogers PCBs are more expensive than traditional FR-4 PCBs, their unique properties and performance advantages justify the higher cost for applications that demand the highest level of signal integrity and reliability. As technology continues to advance and the demand for high-frequency electronics grows, the importance of Rogers PCBs in enabling cutting-edge applications will only continue to increase.
Leave a Reply