The Basics of Power PCBs
What is a Power Plane?
A power plane is a large copper area on a PCB that is dedicated to distributing power to the components on the board. Unlike signal traces, which are thin and narrow, power planes cover a significant portion of the PCB’s surface area. This large surface area allows for low resistance and high current-carrying capacity, ensuring a stable and consistent power supply to the connected components.
Power planes are typically located on the inner layers of a multi-layer PCB, sandwiched between the signal layers. This arrangement helps to reduce electromagnetic interference (EMI) and provides a low-impedance path for the power supply.
The Importance of Power Integrity
Power integrity refers to the quality and stability of the power supply delivered to the components on a PCB. Maintaining power integrity is crucial for the proper functioning and reliability of electronic devices. Poor power integrity can lead to various issues, such as:
- Voltage fluctuations
- Excessive ripple and noise
- Electromagnetic interference (EMI)
- Signal integrity problems
- Reduced component lifespan
- Device malfunction or failure
Power PCBs are designed to address these concerns by providing a low-impedance, high-current power distribution network that minimizes voltage drops, reduces noise, and maintains stable power delivery.
Designing Power PCBs
Power Distribution Network (PDN) Design
The power distribution network (PDN) is the system of conductors, planes, and vias that distribute power from the power source to the components on the PCB. Designing an effective PDN is crucial for maintaining power integrity and ensuring reliable performance.
Key considerations in PDN design include:
- Power requirements: Determine the voltage and current requirements for each component on the board.
- Voltage drop: Minimize voltage drop across the PDN to ensure that each component receives the required voltage level.
- Current density: Ensure that the conductors and planes can handle the required current without excessive heating or voltage drop.
- Impedance: Maintain a low-impedance path for the power supply to reduce noise and voltage fluctuations.
Decoupling Capacitors
Decoupling capacitors play a vital role in maintaining power integrity on a PCB. These capacitors are placed close to the power pins of components to provide a local, low-impedance power source and filter out high-frequency noise. Proper placement and sizing of decoupling capacitors are essential for effective power decoupling.
Via Placement and Sizing
Vias are conductive holes that allow signals and power to pass through different layers of the PCB. In power PCBs, vias are used to connect power planes to components and to provide a low-impedance path for the power supply. Proper via placement and sizing are crucial for maintaining power integrity and minimizing voltage drop.
Thermal Management
Power dissipation in electronic components can lead to excessive heating, which can negatively impact performance and reliability. Power PCBs must be designed with thermal management in mind to ensure that the components operate within their specified temperature ranges. Techniques for thermal management include:
- Using thermal vias to conduct heat away from components
- Incorporating heatsinks or thermal pads
- Providing adequate copper area for heat dissipation
- Using high thermal conductivity PCB materials
Manufacturing Power PCBs
PCB Material Selection
The choice of PCB material is critical for power PCBs, as it affects the board’s electrical, thermal, and mechanical properties. Common PCB materials for power applications include:
- FR-4: A glass-reinforced epoxy laminate, FR-4 is the most widely used PCB material. It offers good electrical and mechanical properties at a relatively low cost.
- High-Tg FR-4: This variant of FR-4 has a higher glass transition temperature (Tg), which improves its thermal stability and reliability.
- Isola 370HR: A high-performance laminate with excellent thermal and electrical properties, Isola 370HR is well-suited for power-dense applications.
- Rogers RO4000 series: These high-frequency laminates offer low dielectric loss and high thermal conductivity, making them ideal for power applications with high-speed signals.
Copper Weight and Thickness
The copper weight and thickness of the power planes and conductors play a significant role in determining the current-carrying capacity and voltage drop of the power distribution network. Thicker copper allows for higher current-carrying capacity and lower resistance, but it also increases the cost and weight of the PCB. Common copper weights for power PCBs range from 1 oz/ft² to 4 oz/ft² (35 μm to 140 μm).
Multi-Layer PCB Construction
Power PCBs often utilize multi-layer construction to accommodate the power planes and signal layers. The number of layers depends on the complexity of the design and the power requirements of the components. A typical 4-layer power PCB might have the following layer stack-up:
Layer | Purpose |
---|---|
Top | Signal |
Inner 1 | Power plane |
Inner 2 | Ground plane |
Bottom | Signal |
As the number of layers increases, so does the complexity and cost of the PCB. However, multi-layer construction allows for better power distribution, improved signal integrity, and reduced EMI.
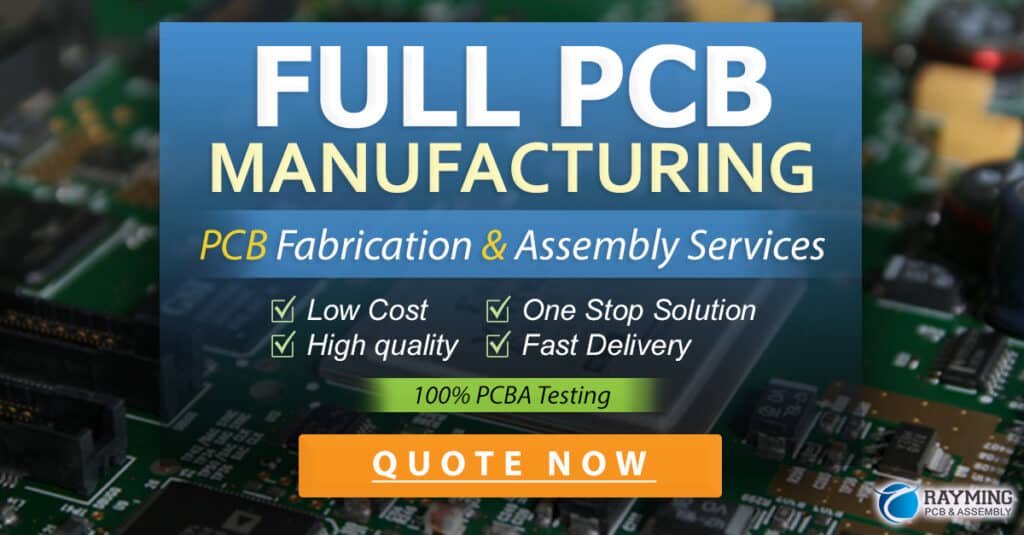
Applications of Power PCBs
Power PCBs find applications in a wide range of industries and devices, including:
- Consumer electronics: Smartphones, laptops, tablets, and wearables
- Automotive: Electric vehicles, hybrid vehicles, and advanced driver assistance systems (ADAS)
- Industrial: Power supplies, motor drives, and control systems
- Aerospace and defense: Avionics, radar systems, and communication equipment
- Medical: Diagnostic equipment, patient monitoring systems, and implantable devices
Each application has its own unique power requirements and design challenges, necessitating careful consideration of the power distribution network, component placement, and thermal management.
Frequently Asked Questions (FAQ)
1. What is the difference between a power plane and a ground plane?
A power plane is a copper layer dedicated to distributing a specific voltage level to components on the PCB, while a ground plane is a copper layer that serves as a common reference point for all signals and provides a low-impedance return path for currents. Both planes work together to maintain power integrity and reduce EMI.
2. How does the thickness of the copper affect the current-carrying capacity of a power plane?
The current-carrying capacity of a power plane is directly proportional to its cross-sectional area, which is determined by the copper thickness and width. Thicker copper allows for higher current-carrying capacity and lower resistance, reducing voltage drop and improving power integrity. However, increasing copper thickness also increases the cost and weight of the PCB.
3. What is the purpose of decoupling capacitors in a power PCB?
Decoupling capacitors serve two main purposes in a power PCB:
- They provide a local, low-impedance power source for components, reducing the impact of voltage fluctuations and noise from the main power supply.
- They filter out high-frequency noise generated by the switching activity of digital components, preventing this noise from propagating throughout the power distribution network.
Proper placement and sizing of decoupling capacitors are essential for effective power decoupling and maintaining power integrity.
4. How does multi-layer construction benefit power PCBs?
Multi-layer construction offers several benefits for power PCBs:
- It allows for the incorporation of dedicated power and ground planes, providing a low-impedance, high-current power distribution network.
- It enables better separation of power and signal layers, reducing electromagnetic interference (EMI) and improving signal integrity.
- It provides more space for routing signals, accommodating complex designs with high component density.
- It facilitates better thermal management by allowing for the use of thermal vias and increased copper area for heat dissipation.
5. What are some common challenges in designing power PCBs?
Designing power PCBs presents several challenges, including:
- Maintaining power integrity: Ensuring stable and clean power delivery to all components on the board requires careful consideration of the power distribution network design, decoupling strategies, and component placement.
- Managing voltage drop: Minimizing voltage drop across the power distribution network is crucial for ensuring that each component receives the required voltage level for proper operation.
- Controlling EMI: The high currents and switching activity in power PCBs can generate electromagnetic interference, which must be mitigated through proper layout, grounding, and filtering techniques.
- Thermal management: Power dissipation in electronic components can lead to excessive heating, requiring effective thermal management strategies to maintain reliability and performance.
- Balancing cost and performance: Selecting the appropriate PCB materials, copper weights, and layer counts to meet performance requirements while minimizing cost can be a challenging optimization problem.
By understanding these challenges and applying best design practices, engineers can create robust and reliable power PCBs that meet the demands of modern electronic devices.
Conclusion
Power PCBs are essential components in modern electronic devices, responsible for distributing stable and clean power to the various components on the board. By utilizing dedicated power planes, multi-layer construction, and proper design techniques, power PCBs ensure power integrity, reduce EMI, and maintain reliable performance.
As electronic devices continue to become more complex and power-hungry, the importance of well-designed power PCBs will only continue to grow. By staying informed about the latest technologies, design strategies, and manufacturing processes, engineers can create power PCBs that meet the evolving needs of the electronics industry.
Leave a Reply