Introduction to Peelable Soldermask
A peelable soldermask, also known as a temporary soldermask or removable soldermask, is a specialized coating applied to printed circuit boards (PCBs) to protect specific areas during the soldering process. Unlike permanent soldermasks, which remain on the PCB throughout its lifetime, peelable soldermasks are designed to be easily removed after soldering, exposing the underlying pads or traces for further processing or inspection.
Key Features of Peelable Soldermasks
- Temporary protection: Peelable soldermasks provide temporary protection to selected areas of the PCB during soldering, preventing solder bridging and other defects.
- Easy removal: After soldering, peelable soldermasks can be easily removed without damaging the PCB or its components.
- Selective application: Peelable soldermasks can be applied to specific areas of the PCB, allowing for targeted protection and exposure of desired regions.
How Peelable Soldermasks Work
Composition and Properties
Peelable soldermasks are typically composed of a polymer base, such as polyvinyl alcohol (PVA) or polyvinyl acetate (PVAc), along with additives that enhance their properties. These additives may include:
- Plasticizers: To improve flexibility and prevent cracking during removal.
- Fillers: To adjust viscosity and improve thermal stability.
- Colorants: To provide visual contrast and aid in inspection.
The composition of peelable soldermasks is carefully formulated to achieve the desired balance of protection, easy removal, and compatibility with the PCB materials and soldering process.
Application Methods
Peelable soldermasks can be applied to PCBs using various methods, depending on the specific requirements and available equipment. Common application methods include:
-
Screen printing: A stencil is used to selectively apply the peelable soldermask to the desired areas of the PCB. This method is suitable for high-volume production and allows for precise control over the application area.
-
Spraying: The peelable soldermask is sprayed onto the PCB using specialized equipment. This method is more flexible and can accommodate irregular shapes or hard-to-reach areas, but may require masking to protect areas that should not be coated.
-
Dipping: The PCB is dipped into a bath containing the peelable soldermask solution. This method provides a uniform coating but may require additional processing to remove excess material and achieve the desired thickness.
Curing and Removal
After application, peelable soldermasks must be cured to achieve their final properties and ensure proper adhesion to the PCB. Curing is typically performed using heat, either in an oven or by passing the PCB through a heated conveyor system. The curing temperature and duration depend on the specific formulation of the peelable soldermask and the recommendations of the manufacturer.
Once the soldering process is complete, the peelable soldermask can be removed by simply peeling it off the PCB surface. The ease of removal depends on factors such as the soldermask formulation, curing conditions, and the strength of adhesion to the PCB. In some cases, the peelable soldermask may require the use of a solvent or mild abrasive to aid in removal.
Applications and Benefits
Selective Soldering
One of the primary applications of peelable soldermasks is in selective soldering processes. In these processes, only specific areas of the PCB need to be soldered, while others must be protected from solder exposure. By applying a peelable soldermask to the areas that should not be soldered, manufacturers can ensure that solder only adheres to the desired locations, preventing short circuits and other defects.
Rework and Repair
Peelable soldermasks are also useful in PCB rework and repair processes. When a component needs to be replaced or a soldering defect needs to be corrected, the peelable soldermask can be applied to protect the surrounding areas while the repair is performed. After the rework is complete, the peelable soldermask is removed, leaving the repaired area exposed and the surrounding components unaffected.
Prototype Development
In prototype development and small-scale production, peelable soldermasks offer a flexible and cost-effective solution for protecting PCBs during soldering. Unlike permanent soldermasks, which require specialized equipment and longer lead times, peelable soldermasks can be applied quickly and easily, allowing for faster iteration and testing of prototype designs.
Benefits of Using Peelable Soldermasks
The use of peelable soldermasks offers several key benefits in PCB manufacturing and assembly:
-
Improved solder joint quality: By preventing solder bridging and other defects, peelable soldermasks contribute to higher-quality solder joints and more reliable PCBs.
-
Increased design flexibility: Peelable soldermasks allow for selective soldering and targeted protection of specific areas, enabling more complex and densely populated PCB designs.
-
Reduced manufacturing costs: By simplifying the soldering process and reducing the need for post-soldering cleaning and inspection, peelable soldermasks can help lower overall manufacturing costs.
-
Faster time-to-market: The ease of application and removal of peelable soldermasks streamlines the PCB assembly process, enabling faster production and shorter lead times.
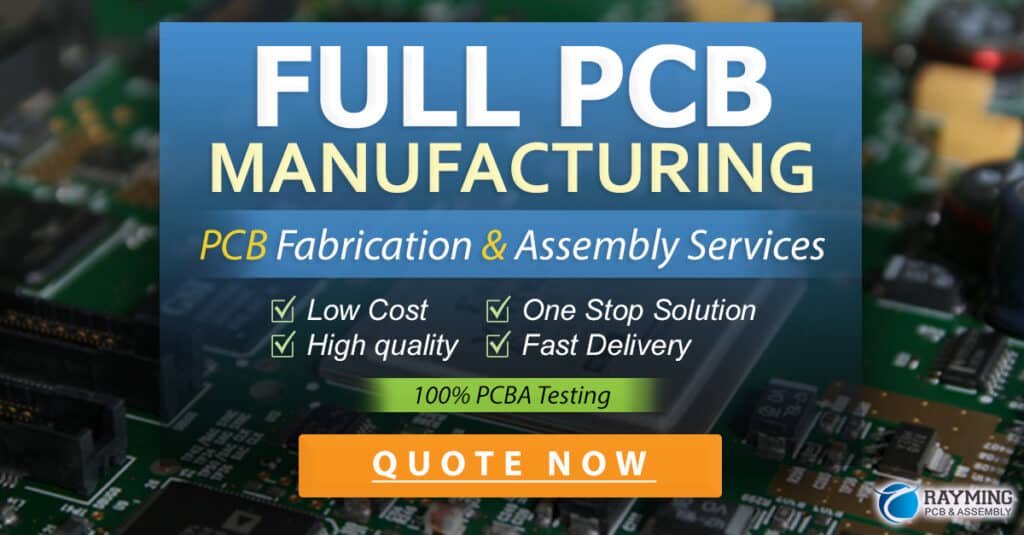
Choosing the Right Peelable Soldermask
When selecting a peelable soldermask for a specific application, several factors should be considered to ensure optimal performance and compatibility with the PCB materials and manufacturing process.
Compatibility with PCB Materials
The peelable soldermask must be compatible with the base materials of the PCB, including the substrate, copper traces, and any permanent soldermask or surface finishes present. Incompatible materials can lead to poor adhesion, difficulty in removal, or even damage to the PCB.
Thermal Stability
The peelable soldermask should be able to withstand the temperatures encountered during the soldering process without degrading or losing its protective properties. The thermal stability of the soldermask will depend on its composition and the specific soldering method used (e.g., wave soldering, reflow soldering, or hand soldering).
Ease of Application and Removal
The chosen peelable soldermask should be easy to apply using the available equipment and methods, ensuring consistent coverage and thickness. Similarly, the soldermask should be easy to remove after soldering, without leaving residue or requiring excessive force that could damage the PCB.
Environmental and Health Considerations
When selecting a peelable soldermask, it is important to consider any environmental and health implications associated with its use. Some soldermask formulations may contain solvents or other chemicals that require special handling, storage, and disposal procedures. Additionally, the soldermask should be compliant with relevant industry standards and regulations, such as RoHS (Restriction of Hazardous Substances) and REACH (Registration, Evaluation, Authorization, and Restriction of Chemicals).
Peelable Soldermask FAQ
-
Q: Can peelable soldermasks be used on both rigid and flexible PCBs?
A: Yes, peelable soldermasks can be formulated for use on both rigid and flexible PCB substrates. However, the specific composition and properties of the soldermask may need to be adjusted to ensure compatibility with the substrate material and to accommodate any flexing or bending of the PCB. -
Q: How long does a peelable soldermask take to cure?
A: The curing time for a peelable soldermask depends on the specific formulation and the curing method used. Typically, curing times range from a few minutes to several hours, with heat-cured soldermasks generally requiring longer curing times than air-dried or UV-cured formulations. -
Q: Can peelable soldermasks be used in automated assembly processes?
A: Yes, peelable soldermasks are compatible with automated assembly processes, such as pick-and-place machines and conveyor systems. However, the specific application and removal methods may need to be adapted to suit the requirements of the automated process, and the soldermask formulation should be chosen to withstand the rigors of the assembly environment. -
Q: Are there any limitations to the use of peelable soldermasks?
A: While peelable soldermasks offer many benefits, there are some limitations to their use. For example, peelable soldermasks may not be suitable for very fine-pitch components or high-density PCB designs, as the thickness of the soldermask can interfere with the placement and soldering of these components. Additionally, some peelable soldermasks may not be compatible with certain surface finishes or may require special handling to ensure proper adhesion and removal. -
Q: How do I choose the right peelable soldermask for my application?
A: When selecting a peelable soldermask, consider factors such as compatibility with the PCB materials, thermal stability, ease of application and removal, and environmental and health considerations. Consult with the soldermask manufacturer or supplier to discuss your specific requirements and to obtain recommendations for the most suitable product for your application. It may also be necessary to conduct trials or testing to validate the performance of the chosen soldermask in your manufacturing process.
Conclusion
Peelable soldermasks are a valuable tool in PCB manufacturing and assembly, offering temporary protection for selected areas of the board during the soldering process. By preventing solder bridging and other defects, peelable soldermasks contribute to higher-quality solder joints and more reliable PCBs. The ease of application and removal of these soldermasks also enables greater design flexibility, faster production times, and lower manufacturing costs.
When choosing a peelable soldermask, it is important to consider factors such as compatibility with the PCB materials, thermal stability, ease of use, and environmental and health implications. By selecting the right soldermask for the specific application and manufacturing process, PCB manufacturers can optimize the benefits of this versatile and valuable material.
As PCB designs continue to evolve and become more complex, the use of peelable soldermasks will likely remain an essential part of the manufacturing toolkit, enabling the production of high-quality, reliable, and cost-effective electronic devices.
Property | Peelable Soldermask | Permanent Soldermask |
---|---|---|
Purpose | Temporary protection during soldering | Long-term protection of the PCB |
Application | Screen printing, spraying, or dipping | Screen printing, photoimaging, or curtain coating |
Removal | Easily peeled off after soldering | Remains on the PCB throughout its lifetime |
Thickness | Typically thicker than permanent soldermasks | Thinner and more uniform |
Thermal Stability | Must withstand Soldering Temperatures | Must withstand higher temperatures and environmental stresses |
Compatibility | Must be compatible with PCB materials and soldering process | Must be compatible with PCB materials and surface finishes |
Leave a Reply