The Purpose of PCB Test Fixtures
Ensuring Reliable Connections
One of the primary functions of a PCB test fixture is to provide a stable and reliable connection between the PCB and the testing equipment. The fixture securely holds the PCB in place, preventing any movement or vibration that could disrupt the electrical connections during testing. This ensures that the measurements obtained are accurate and consistent, reducing the likelihood of false positives or negatives.
Protecting the PCB
PCB test fixtures also serve to protect the board from damage during the testing process. Handling bare PCBs can be risky, as they are prone to scratches, bending, or other physical damage that can affect their performance. A well-designed test fixture minimizes the need for manual handling, reducing the risk of accidental damage and ensuring the integrity of the PCB.
Improving Testing Efficiency
By using a PCB test fixture, engineers can streamline the testing process and improve overall efficiency. The fixture allows for quick and easy connection of the PCB to the testing equipment, reducing setup time and minimizing the possibility of human error. Additionally, test fixtures enable automated testing, which can significantly increase throughput and reduce the time required for testing large batches of PCBs.
Types of PCB Test Fixtures
Bed of Nails Fixture
A bed of nails fixture is a common type of PCB test fixture that consists of an array of spring-loaded pins arranged in a pattern that matches the test points on the PCB. When the board is placed on the fixture, the pins make contact with the designated test points, establishing an electrical connection between the PCB and the testing equipment.
Bed of nails fixtures are ideal for testing PCBs with a large number of test points, as they provide simultaneous access to all the required connections. However, designing and manufacturing these fixtures can be complex and time-consuming, as the pin layout must be precisely matched to the PCB’s test points.
Vacuum Fixture
Vacuum fixtures use suction to hold the PCB securely in place during testing. The fixture consists of a vacuum chamber with a perforated top surface that matches the shape of the PCB. When the board is placed on the fixture, air is evacuated from the chamber, creating a vacuum that holds the PCB firmly in position.
Vacuum fixtures are particularly useful for testing flexible or thin PCBs that may be difficult to secure using other methods. They also provide a clear view of the PCB’s surface, allowing for visual inspection during testing. However, vacuum fixtures may not be suitable for PCBs with large components or irregular shapes that could interfere with the vacuum seal.
Clamshell Fixture
A clamshell fixture consists of two halves that open and close like a clamshell, with the PCB being secured between them. The fixture’s top half contains probes or pins that make contact with the test points on the PCB when the fixture is closed.
Clamshell fixtures offer several advantages, such as easy access to both sides of the PCB, adjustable probe positions, and the ability to accommodate a wide range of board sizes and shapes. They are also well-suited for testing PCBs with tall components or those requiring access to edge connectors.
Custom Fixtures
In some cases, standard test fixtures may not be suitable for a particular PCB design, necessitating the development of a custom fixture. Custom fixtures are designed and manufactured specifically for a given PCB, taking into account its unique shape, size, component layout, and testing requirements.
While custom fixtures can be more expensive and time-consuming to develop compared to standard fixtures, they offer the highest level of compatibility and performance for the specific PCB being tested.
Designing PCB Test Fixtures
Considering PCB Layout
The design of a PCB test fixture is heavily influenced by the layout of the PCB itself. Engineers must consider factors such as the location and spacing of test points, the size and shape of the board, and the presence of any components or connectors that may interfere with the fixture’s operation.
To facilitate efficient testing, it is essential to incorporate test points into the PCB design from the outset. These test points should be strategically placed to provide access to critical signals and components, while also ensuring compatibility with the chosen test fixture.
Selecting the Right Materials
The choice of materials for a PCB test fixture is crucial to its performance and durability. The fixture must be made from materials that can withstand the rigors of repeated testing, including mechanical stress, temperature variations, and exposure to environmental factors such as humidity and dust.
Common materials used in PCB test fixtures include:
- Aluminum: Lightweight, strong, and easy to machine, aluminum is a popular choice for fixture frames and support structures.
- Stainless steel: Known for its durability and resistance to corrosion, stainless steel is often used for fixture components that require high strength and stability.
- Plastics: High-performance plastics, such as Delrin and Teflon, are used for insulating components and probe housings due to their excellent electrical and thermal properties.
Ensuring Proper Grounding
Proper grounding is essential for accurate and reliable PCB testing. The test fixture must provide a low-impedance path to ground, minimizing the impact of electrical noise and interference on the measurements.
To achieve proper grounding, the fixture should incorporate dedicated grounding points that are connected to a common ground plane. Additionally, the use of shielded cables and connectors can help to reduce the influence of external electromagnetic interference on the test results.
Accommodating Fixture Maintenance
PCB test fixtures are subject to wear and tear over time, requiring regular maintenance to ensure optimal performance. When designing a fixture, engineers should consider factors that facilitate easy maintenance, such as:
- Modularity: Designing the fixture with modular components allows for easy replacement of worn or damaged parts without the need to replace the entire fixture.
- Accessibility: The fixture should provide easy access to critical components, such as probes and connectors, for inspection and cleaning.
- Documentation: Clear and comprehensive documentation, including assembly instructions and maintenance guidelines, can help to ensure that the fixture is properly maintained throughout its lifespan.
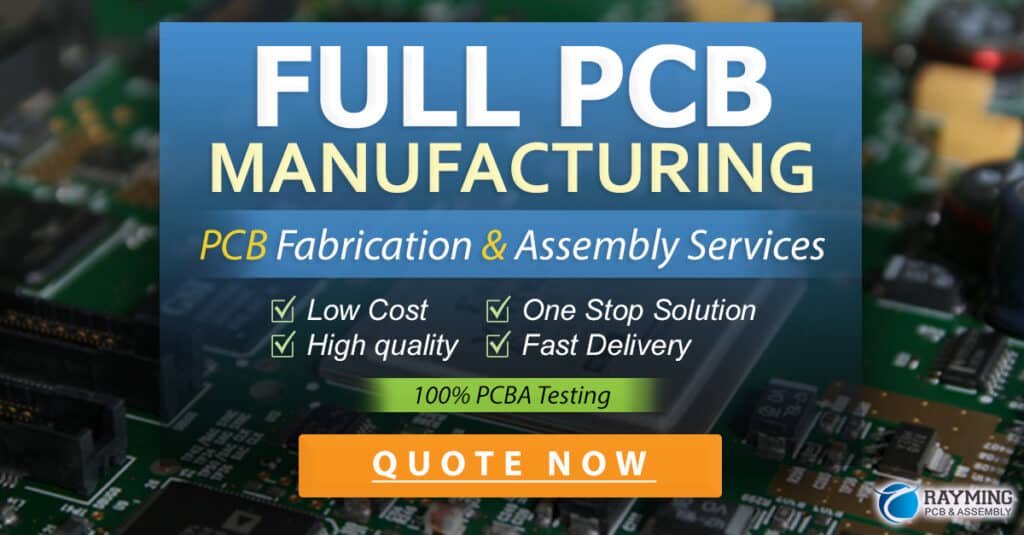
Best Practices for PCB Testing with Fixtures
Calibration and Verification
Before using a PCB test fixture, it is essential to calibrate and verify its performance to ensure accurate and reliable measurements. This process involves:
- Calibrating the testing equipment: Ensure that all testing instruments, such as oscilloscopes and multimeters, are properly calibrated according to the manufacturer’s specifications.
- Verifying fixture connectivity: Use a test PCB with known characteristics to verify that the fixture is making proper connections and providing accurate measurements.
- Documenting the calibration process: Maintain a record of all calibration and verification procedures, including the date, equipment used, and results obtained.
Implementing Automated Testing
Automated testing can significantly improve the efficiency and accuracy of PCB testing with fixtures. By using software-controlled testing equipment and fixtures, engineers can:
- Reduce testing time: Automated tests can be run quickly and continuously, without the need for manual intervention.
- Minimize human error: Automated testing eliminates the possibility of operator error, ensuring consistent and reliable results.
- Generate comprehensive test reports: Automated testing software can generate detailed reports, including pass/fail criteria, measurement data, and statistical analysis.
Maintaining Fixture Cleanliness
Keeping PCB test fixtures clean is crucial for ensuring accurate and reliable measurements. Dust, debris, and oxidation on fixture components can interfere with electrical connections and lead to erroneous test results.
To maintain fixture cleanliness:
- Regularly inspect and clean the fixture, paying close attention to probes, connectors, and contact surfaces.
- Use appropriate cleaning materials, such as isopropyl alcohol and lint-free wipes, to remove contaminants without damaging the fixture components.
- Store the fixture in a clean, dry environment when not in use to prevent the accumulation of dust and moisture.
Training and Safety
Proper training is essential for operators working with PCB test fixtures to ensure safe and effective use. Operators should be familiar with:
- The correct procedures for handling and inserting PCBs into the fixture
- The proper use and maintenance of testing equipment
- Safety guidelines, including the use of personal protective equipment (PPE) and the handling of potentially hazardous materials
Regular training sessions and clear documentation can help to ensure that all operators are equipped with the knowledge and skills necessary to perform PCB testing safely and efficiently.
Frequently Asked Questions (FAQ)
-
What is the purpose of a PCB test fixture?
A PCB test fixture is used to securely hold and connect a printed circuit board (PCB) during testing, ensuring reliable and repeatable measurements of the board’s functionality and performance. -
What are the common types of PCB test fixtures?
The common types of PCB test fixtures include bed of nails fixtures, vacuum fixtures, clamshell fixtures, and custom fixtures designed for specific PCB requirements. -
What factors should be considered when designing a PCB test fixture?
When designing a PCB test fixture, engineers must consider factors such as the PCB layout, the selection of appropriate materials, proper grounding, and accommodations for fixture maintenance. -
How can automated testing improve PCB testing with fixtures?
Automated testing can improve the efficiency and accuracy of PCB testing with fixtures by reducing testing time, minimizing human error, and generating comprehensive test reports. -
Why is maintaining fixture cleanliness important for PCB testing?
Maintaining fixture cleanliness is crucial for ensuring accurate and reliable measurements, as dust, debris, and oxidation on fixture components can interfere with electrical connections and lead to erroneous test results.
Conclusion
PCB test fixtures play a vital role in the electronics manufacturing process, ensuring that printed circuit boards meet the required specifications before being integrated into the final product. By providing reliable connections, protecting the PCB from damage, and enabling efficient testing, these fixtures help to guarantee the quality and performance of electronic devices.
When designing and using PCB test fixtures, engineers must consider various factors, such as PCB layout, material selection, grounding, and maintenance. By implementing best practices, including calibration, automated testing, cleanliness, and operator training, manufacturers can optimize their PCB testing processes and deliver high-quality products to their customers.
As electronics continue to advance and become more complex, the importance of effective PCB testing will only continue to grow. By staying up-to-date with the latest developments in PCB test fixtures and best practices, manufacturers can position themselves to meet the evolving demands of the industry and remain competitive in the global marketplace.
Leave a Reply