How PCB Stencils Work
The PCB stencil is placed on top of the PCB, aligning the apertures with the corresponding pads. Solder paste is then applied over the stencil using a squeegee, forcing the paste through the apertures and onto the pads. The stencil is then removed, leaving a precise amount of solder paste on each pad. The PCB is then ready for component placement and reflow soldering.
Types of PCB Stencils
There are two main types of PCB stencils:
-
Stainless Steel Stencils: These are the most common type of stencils used in the industry. They are durable, long-lasting, and can withstand multiple cleaning cycles. Stainless steel stencils are available in various thicknesses, typically ranging from 0.1mm to 0.2mm.
-
Polyester Stencils: These stencils are made from a thin, flexible polyester film. They are less expensive than stainless steel stencils and are suitable for low-volume production or prototyping. However, they are less durable and may not provide the same level of precision as stainless steel stencils.
Stencil Thickness
The thickness of the PCB stencil is a critical factor in determining the amount of solder paste deposited on the pads. The stencil thickness is typically chosen based on the size of the components and the pitch of the pads. Here are some common stencil thicknesses and their applications:
Stencil Thickness | Application |
---|---|
0.1mm | Fine pitch components (0.3mm to 0.4mm) |
0.12mm | Standard SMD components (0.5mm to 0.8mm) |
0.15mm | Larger SMD components (0.8mm to 1.27mm) |
0.2mm | Power components and connectors |
Benefits of Using PCB Stencils
Using a PCB stencil offers several benefits in the electronic manufacturing process:
-
Consistency: PCB stencils ensure a consistent amount of solder paste is applied to each pad, reducing the risk of insufficient or excessive solder joints.
-
Accuracy: The laser-cut apertures in the stencil provide a high level of accuracy in solder paste placement, ensuring proper alignment with the pads on the PCB.
-
Efficiency: Using a stencil significantly reduces the time required for solder paste application compared to manual methods, making it suitable for high-volume production.
-
Cost-effective: PCB stencils are relatively inexpensive and can be reused multiple times, reducing the overall manufacturing cost.
Stencil Design Considerations
When designing a PCB stencil, several factors need to be considered:
-
Aperture Size: The size of the apertures should match the size of the pads on the PCB. The aperture size is typically 1:1 with the pad size, but can be adjusted based on the solder paste properties and the desired solder joint profile.
-
Aperture Shape: The shape of the apertures can affect the solder paste release and the final solder joint shape. Common aperture shapes include square, circular, and rounded rectangle.
-
Stencil Thickness: As mentioned earlier, the stencil thickness should be chosen based on the component size and pad pitch.
-
Stencil Material: The choice of stencil material (stainless steel or polyester) depends on the production volume, required durability, and budget.
Stencil Aperture Reduction
In some cases, the aperture size may need to be reduced to prevent solder paste bridging between closely spaced pads. This is known as aperture reduction or home plate design. The aperture size is reduced on the pad side, while maintaining the original size on the squeegee side. This helps in achieving a good solder paste release while preventing bridging.
Stencil Cleaning and Maintenance
To ensure consistent performance and long life, PCB stencils need to be regularly cleaned and maintained. Solder paste residue can accumulate on the stencil surface and in the apertures, affecting the paste release and print quality. Here are some best practices for stencil cleaning and maintenance:
-
Underside Cleaning: After each print, the underside of the stencil should be cleaned using a lint-free wipe and a suitable solvent to remove any solder paste residue.
-
Periodic Deep Cleaning: Depending on the usage, stencils should be periodically deep cleaned using an ultrasonic cleaner or a stencil cleaning machine. This helps in removing any dried solder paste or debris from the apertures.
-
Proper Storage: When not in use, stencils should be stored in a clean, dry environment to prevent contamination and damage.
Stencil Inspection
Regular inspection of the PCB stencil is essential to ensure its quality and performance. Here are some key aspects to inspect:
-
Aperture Size and Shape: Check for any deviations in the aperture size or shape compared to the original design.
-
Stencil Thickness: Measure the stencil thickness to ensure it meets the specified requirements.
-
Stencil Flatness: Check for any warping or unevenness in the stencil surface, which can affect the print quality.
-
Aperture Blockage: Inspect the apertures for any blockages or residue buildup, which can hinder the solder paste release.
Stencil Repair
In case of minor damage or wear, PCB stencils can be repaired using laser welding or chemical etching techniques. However, if the damage is extensive or the stencil has reached the end of its life, it should be replaced to maintain the print quality and consistency.
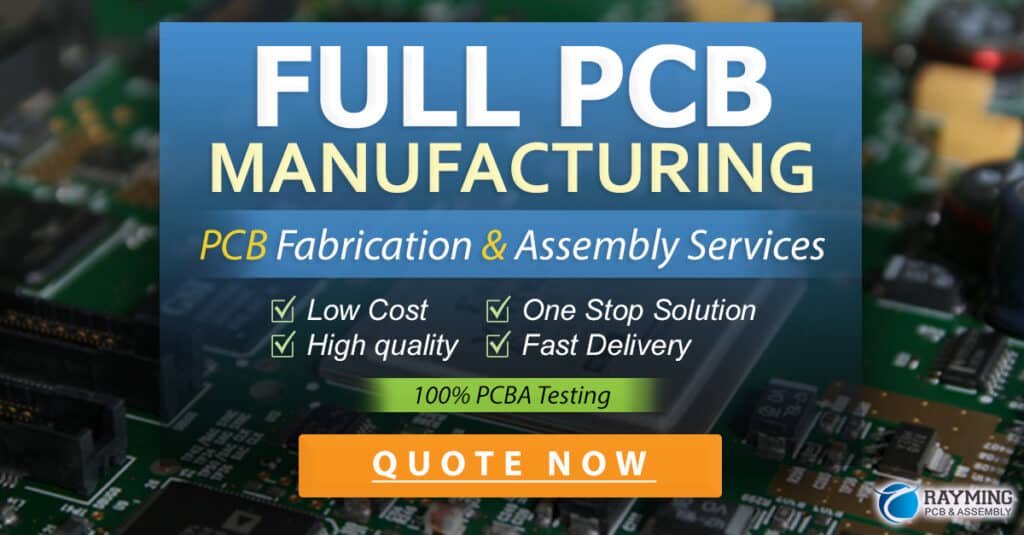
Frequently Asked Questions (FAQ)
-
What is the difference between a solder paste stencil and a solder mask stencil?
A solder paste stencil is used to apply solder paste onto the PCB pads, while a solder mask stencil is used to apply a solder mask layer over the PCB surface, leaving the pads exposed. -
How often should I clean my PCB stencil?
The cleaning frequency depends on the usage and the solder paste properties. As a general guideline, the underside of the stencil should be cleaned after each print, and a periodic deep cleaning should be performed based on the manufacturer’s recommendations or when print quality issues arise. -
Can I use the same stencil for different PCB designs?
No, each PCB design requires a specific stencil with apertures that match the pad layout. Using the wrong stencil can result in incorrect solder paste placement and component misalignment. -
How long does a PCB stencil last?
The life of a PCB stencil depends on various factors such as the stencil material, usage frequency, and maintenance practices. A well-maintained stainless steel stencil can last for thousands of prints, while a polyester stencil may have a shorter lifespan. -
Can I make my own PCB stencil?
While it is possible to make a PCB stencil using DIY methods such as cutting a template from a thin sheet of metal or plastic, it is recommended to use professionally manufactured stencils for better accuracy and consistency. Many PCB fabrication services offer stencil manufacturing as an additional service.
Conclusion
PCB stencils play a crucial role in the electronic manufacturing process by ensuring accurate and consistent solder paste application. By understanding the types of stencils, design considerations, and maintenance practices, manufacturers can optimize their solder paste printing process and achieve high-quality solder joints. As the electronics industry continues to evolve with smaller components and tighter tolerances, the importance of PCB stencils in ensuring reliable and efficient manufacturing will only continue to grow.
Leave a Reply