How PCB Sensors Work
Sensing Elements
At the core of every PCB sensor is a sensing element. This component is responsible for detecting changes in the physical quantity being measured. Some common sensing elements include:
- Thermistors for temperature measurement
- Piezoresistive elements for pressure sensing
- Capacitive elements for humidity detection
- Photoresistors for light intensity measurement
The sensing element is typically connected to a PCB, which provides the necessary circuitry to process the sensor data.
Signal Conditioning
Once the sensing element detects a change in the physical quantity, the signal needs to be conditioned before it can be processed by the electronic system. Signal conditioning involves amplifying, filtering, and converting the sensor output into a suitable format.
Some common signal conditioning techniques used in PCB sensors include:
- Amplification: Increasing the strength of the sensor output signal
- Filtering: Removing unwanted noise from the signal
- Analog-to-digital conversion: Converting the analog sensor output into a digital format
Data Processing
After the sensor data has been conditioned, it can be processed by the electronic system. This may involve:
- Comparing the sensor output to a predetermined threshold
- Performing calculations based on the sensor data
- Storing the sensor data for later analysis
- Triggering an action based on the sensor output (e.g., turning on a fan when the temperature exceeds a certain level)
Types of PCB Sensors
There are many different types of PCB sensors, each designed to measure a specific physical quantity. Some common examples include:
Temperature Sensors
Temperature sensors are used to measure the temperature of a system or environment. They are commonly used in:
- HVAC systems
- Automotive electronics
- Industrial process control
- Consumer electronics
Sensor Type | Operating Temperature Range | Accuracy |
---|---|---|
Thermistor | -90°C to 130°C | ±0.1°C |
RTD | -200°C to 850°C | ±0.1°C |
Thermocouple | -270°C to 1372°C | ±0.5°C |
Pressure Sensors
Pressure sensors measure the force applied to a surface area. They are used in a wide range of applications, including:
- Automotive tire pressure monitoring
- Industrial process control
- Medical devices
- Consumer electronics
Sensor Type | Pressure Range | Accuracy |
---|---|---|
Piezoresistive | 0-10,000 psi | ±0.1% |
Capacitive | 0-100 psi | ±0.25% |
Optical | 0-1,000 psi | ±0.5% |
Humidity Sensors
Humidity sensors measure the amount of water vapor in the air. They are commonly used in:
- HVAC systems
- Weather monitoring
- Industrial process control
- Consumer electronics
Sensor Type | Humidity Range | Accuracy |
---|---|---|
Capacitive | 0-100% RH | ±2% RH |
Resistive | 0-100% RH | ±3% RH |
Thermal | 0-100% RH | ±5% RH |
Accelerometers
Accelerometers measure acceleration forces, including gravity. They are used in:
- Automotive safety systems
- Consumer electronics
- Robotics
- Industrial machinery
Sensor Type | Acceleration Range | Bandwidth |
---|---|---|
Piezoelectric | ±1,000 g | 0.1-10 kHz |
Piezoresistive | ±50 g | 0-5 kHz |
Capacitive | ±100 g | 0-1 kHz |
Advantages of PCB Sensors
PCB sensors offer several advantages over traditional discrete sensors:
Integration
By integrating the sensing element and signal conditioning circuitry onto a single PCB, manufacturers can create more compact and reliable sensors. This integration also reduces the number of components required, simplifying the assembly process and reducing costs.
Customization
PCB sensors can be easily customized to meet the specific requirements of an application. Manufacturers can choose the appropriate sensing element, signal conditioning circuitry, and form factor to create a sensor that is optimized for a particular use case.
Scalability
PCB sensors are well-suited for high-volume production. By using automated assembly processes and standardized components, manufacturers can quickly and efficiently produce large quantities of sensors at a relatively low cost.
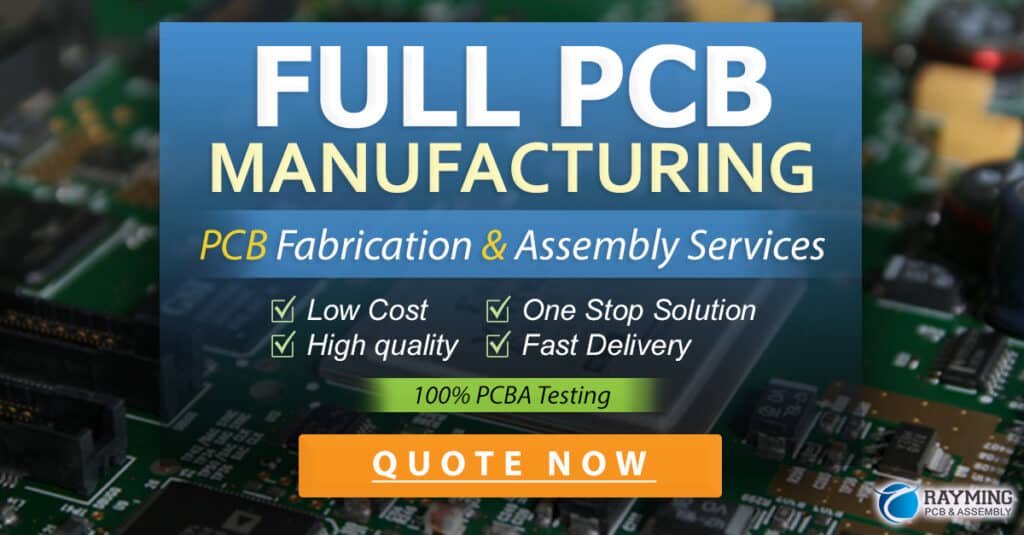
Applications of PCB Sensors
PCB sensors are used in a wide range of industries and applications. Some common examples include:
Automotive
In the automotive industry, PCB sensors are used for:
- Engine management
- Tire pressure monitoring
- Airbag deployment
- Climate control
Industrial
PCB sensors are used in industrial settings for:
- Process control
- Machinery monitoring
- Quality control
- Safety systems
Medical
In the medical field, PCB sensors are used in:
- Patient monitoring devices
- Diagnostic equipment
- Drug delivery systems
- Wearable health monitors
Consumer Electronics
PCB sensors are found in many consumer electronic devices, including:
- Smartphones
- Smartwatches
- Fitness trackers
- Home automation systems
Challenges and Considerations
While PCB sensors offer many benefits, there are also some challenges and considerations to keep in mind:
Environmental Factors
PCB sensors are often exposed to harsh environmental conditions, such as extreme temperatures, humidity, and vibration. Manufacturers must design their sensors to withstand these conditions and ensure reliable operation over the intended lifespan of the device.
Calibration
To ensure accurate measurements, PCB sensors must be properly calibrated. This involves comparing the sensor output to a known reference and adjusting the sensor parameters accordingly. Calibration can be a time-consuming and costly process, particularly for high-precision applications.
Interference
PCB sensors can be susceptible to electromagnetic interference (EMI) from nearby electronic devices. This interference can cause errors in the sensor output and lead to inaccurate measurements. To mitigate this risk, manufacturers must design their sensors with appropriate shielding and filtering capabilities.
Cost
While PCB sensors can be more cost-effective than discrete sensors in high-volume applications, they may still be too expensive for some low-cost products. Manufacturers must carefully balance the cost of the sensor with the overall cost of the device to ensure profitability.
Future Trends in PCB Sensors
As technology continues to advance, we can expect to see several trends in the development of PCB sensors:
Miniaturization
There is a growing demand for smaller, more compact sensors that can be easily integrated into portable and wearable devices. Manufacturers are responding by developing new sensing elements and packaging techniques that enable the creation of ultra-small pcb sensors.
Wireless Connectivity
Many PCB sensors are now being designed with wireless connectivity, allowing them to transmit data to remote monitoring systems or cloud-based platforms. This enables real-time monitoring and analysis of sensor data, as well as the ability to control the sensor remotely.
Machine Learning
Machine learning algorithms are being increasingly used to analyze sensor data and identify patterns or anomalies that may indicate a problem. By integrating machine learning capabilities into PCB sensors, manufacturers can create smart sensors that can adapt to changing conditions and provide more accurate and reliable measurements.
Energy Harvesting
To extend the battery life of portable and wearable devices, some PCB sensors are being designed with energy harvesting capabilities. These sensors can generate their own power from ambient sources such as light, vibration, or temperature gradients, reducing the need for frequent battery replacements.
Frequently Asked Questions (FAQ)
-
What is the difference between a PCB sensor and a discrete sensor?
A PCB sensor integrates the sensing element and signal conditioning circuitry onto a single printed circuit board, while a discrete sensor uses separate components for each function. -
How do I choose the right PCB sensor for my application?
When choosing a PCB sensor, consider factors such as the physical quantity to be measured, the required accuracy and resolution, the environmental conditions, and the cost and size constraints of your application. -
Can PCB sensors be used in harsh environments?
Yes, PCB sensors can be designed to withstand harsh environmental conditions such as extreme temperatures, humidity, and vibration. However, manufacturers must take these factors into account when designing and testing their sensors. -
How often do PCB sensors need to be calibrated?
The frequency of calibration depends on the specific sensor and application. Some sensors may require calibration only once during manufacturing, while others may need periodic recalibration to maintain accuracy over time. -
Are PCB sensors more expensive than discrete sensors?
In general, PCB sensors can be more cost-effective than discrete sensors in high-volume applications due to their integrated design and automated assembly processes. However, for low-volume or low-cost applications, discrete sensors may be a more economical choice.
Leave a Reply