Introduction to Military PCBs
PCB, which stands for Printed Circuit Board, is a fundamental component in modern electronics. These boards are used in a wide range of applications, from consumer gadgets to industrial equipment and even in military systems. In the context of military applications, PCBs play a crucial role in ensuring the reliability, durability, and performance of various devices and systems used by the armed forces.
Military PCBs are designed and manufactured to meet stringent requirements set by military standards, such as MIL-PRF-31032, MIL-PRF-55110, and MIL-STD-275. These standards ensure that the PCBs can withstand harsh environmental conditions, extreme temperatures, vibrations, and shocks encountered in military operations.
Key Characteristics of Military PCBs
- High reliability and durability
- Resistance to extreme temperatures, vibrations, and shocks
- Conformance to military standards and specifications
- Enhanced security features to prevent tampering and reverse engineering
Types of Military PCBs
Military PCBs can be categorized based on their construction, materials used, and the specific applications they are designed for. Some common types of military PCBs include:
1. Rigid PCBs
Rigid PCBs are the most common type of PCBs used in military applications. They are made from a solid substrate material, typically FR-4, and offer excellent mechanical stability and durability. Rigid PCBs are suitable for a wide range of military applications, such as:
- Communication systems
- Radar and sonar equipment
- Weapon control systems
- Avionics and navigation systems
2. Flexible PCBs
Flexible PCBs, also known as flex circuits, are made from thin, flexible materials like polyimide or polyester. They offer several advantages over rigid PCBs, such as reduced weight, increased flexibility, and the ability to fit into tight spaces. Flexible PCBs are commonly used in military applications that require compact and lightweight designs, such as:
- Wearable devices for soldiers
- Portable communication equipment
- Unmanned aerial vehicles (UAVs) and drones
- Missile guidance systems
3. Rigid-Flex PCBs
Rigid-flex PCBs combine the benefits of both rigid and flexible PCBs. They consist of rigid PCB sections connected by flexible PCB sections, allowing for a more compact and reliable design. Rigid-flex PCBs are ideal for military applications that require high density interconnects and enhanced mechanical stability, such as:
- Handheld communication devices
- Portable radar systems
- Satellite communication equipment
- Ruggedized computers and tablets
Military PCB Design Considerations
Designing PCBs for military applications requires careful consideration of various factors to ensure optimal performance, reliability, and durability. Some key design considerations include:
1. Material Selection
The choice of materials used in military PCBs is crucial to ensure their ability to withstand harsh environmental conditions. Some common materials used in military PCBs include:
- FR-4: A flame-retardant, glass-reinforced epoxy laminate widely used in rigid PCBs.
- Polyimide: A high-temperature, flexible material used in flexible and rigid-flex PCBs.
- PTFE (Teflon): A low-dielectric, high-frequency material used in RF and microwave applications.
- Ceramic: A high-temperature, high-strength material used in specialized military applications.
2. Thermal Management
Military PCBs often operate in extreme temperature conditions, ranging from -55°C to +125°C. Effective thermal management is essential to ensure the reliability and longevity of the PCB and its components. Some thermal management techniques used in military PCBs include:
- Proper component placement and spacing to minimize heat buildup
- Use of thermal vias and heat sinks to dissipate heat
- Selection of components with appropriate temperature ratings
- Use of thermally conductive materials, such as metal-core PCBs
3. Electromagnetic Compatibility (EMC)
Military PCBs must be designed to minimize electromagnetic interference (EMI) and ensure electromagnetic compatibility (EMC) with other electronic systems. EMC design considerations include:
- Proper grounding and shielding techniques
- Use of filters and suppressors to reduce EMI
- Careful routing of high-speed signals to minimize crosstalk and radiation
- Compliance with military EMC standards, such as MIL-STD-461
4. Shock and Vibration Resistance
Military PCBs are subject to severe shock and vibration during operation, transportation, and deployment. Designing PCBs to withstand these mechanical stresses is critical to ensure their reliability and durability. Some design techniques to improve shock and vibration resistance include:
- Use of flexible PCBs or rigid-flex PCBs to absorb mechanical stresses
- Proper component selection and mounting techniques, such as underfill and conformal coating
- Use of shock-absorbing materials and damping techniques
- Compliance with military vibration and shock testing standards, such as MIL-STD-810
5. Security and Anti-Tamper Features
Military PCBs often contain sensitive information and intellectual property that must be protected from unauthorized access and reverse engineering. Some security and anti-tamper features used in military PCBs include:
- Encryption of sensitive data and firmware
- Use of tamper-evident coatings and seals
- Implementation of hardware-based security measures, such as secure boot and hardware trust anchors
- Design obfuscation techniques to deter reverse engineering attempts
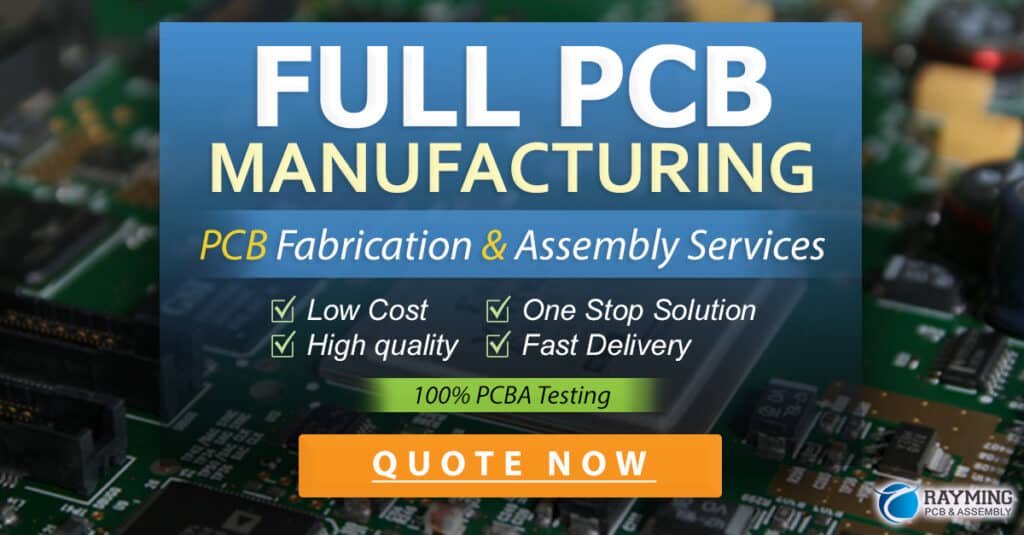
Military PCB Manufacturing Process
The manufacturing process for military PCBs is more rigorous and tightly controlled compared to commercial PCBs. This is to ensure the highest level of quality, reliability, and conformance to military standards. The key steps in the military PCB manufacturing process include:
1. Design Review and Verification
Before manufacturing begins, the PCB design undergoes a thorough review and verification process to ensure compliance with military standards and specifications. This includes:
- Design rule checks (DRC) to verify adherence to design guidelines
- Signal integrity and power integrity simulations
- Thermal and mechanical stress analysis
- EMC simulations and analysis
2. Material Selection and Inspection
The materials used in military PCBs are carefully selected and inspected to ensure they meet the required specifications. This includes:
- Verification of material certifications and traceability
- Incoming inspection of raw materials
- Testing of material properties, such as dielectric constant and thermal conductivity
3. PCB Fabrication
The PCB fabrication process involves several steps, including:
- Etching and plating of conductive layers
- Lamination of multiple layers
- Drilling and plating of through-holes and vias
- Solder mask application and silkscreen printing
Throughout the fabrication process, strict quality control measures are implemented to ensure the PCBs meet the required specifications and are free from defects.
4. Component Assembly
After the PCB fabrication is complete, the components are assembled onto the board. The component assembly process for military PCBs involves:
- Use of high-reliability components that meet military specifications
- Precision placement of components using automated assembly equipment
- Soldering techniques that ensure strong and reliable connections, such as reflow soldering and wave soldering
- Inspection and testing of assembled PCBs to verify proper functionality and workmanship
5. Testing and Qualification
Military PCBs undergo rigorous testing and qualification processes to ensure they meet the required performance, reliability, and durability standards. This includes:
- Functional testing to verify proper operation
- Environmental testing, such as temperature cycling, thermal shock, and humidity exposure
- Mechanical testing, such as vibration and shock testing
- EMC testing to ensure compliance with electromagnetic compatibility standards
PCBs that pass the testing and qualification process are certified for use in military applications.
Applications of Military PCBs
Military PCBs find applications in a wide range of systems and equipment used by the armed forces. Some key application areas include:
1. Communication Systems
Military communication systems require reliable and secure PCBs to ensure uninterrupted and tamper-proof communication. Examples include:
- Tactical radios and handheld communication devices
- Satellite communication equipment
- Encrypted communication systems
2. Radar and Sonar Systems
PCBs used in radar and sonar systems must be able to handle high-frequency signals and withstand harsh environmental conditions. Examples include:
- Ground-based and airborne radar systems
- Shipboard and submarine sonar systems
- Radar warning receivers and electronic countermeasures
3. Avionics and Navigation Systems
Avionics and navigation systems rely on high-performance PCBs to ensure accurate and reliable operation. Examples include:
- Flight control systems and autopilots
- GPS and inertial navigation systems
- Heads-up displays and cockpit instrumentation
4. Weapon Control Systems
PCBs used in weapon control systems must be highly reliable and resistant to electromagnetic interference. Examples include:
- Missile guidance and control systems
- Fire control systems for artillery and tanks
- Electronic fuses and detonators
5. Unmanned Systems
Unmanned systems, such as UAVs and UGVs, require compact, lightweight, and reliable PCBs to enable autonomous operation. Examples include:
- Drone flight control and navigation systems
- Sensor and payload integration on unmanned platforms
- Ground control stations and communication links
Challenges in Military PCB Design and Manufacturing
Designing and manufacturing PCBs for military applications presents several unique challenges compared to commercial PCBs. Some of these challenges include:
1. Stringent Requirements and Standards
Military PCBs must comply with a wide range of stringent requirements and standards, such as MIL-PRF-31032, MIL-PRF-55110, and MIL-STD-275. Meeting these requirements often involves additional design and manufacturing processes, which can increase costs and lead times.
2. Harsh Environmental Conditions
Military PCBs must be able to operate reliably in harsh environmental conditions, such as extreme temperatures, high humidity, and exposure to dust, sand, and salt spray. Designing PCBs to withstand these conditions requires careful material selection, thermal management, and protective coatings.
3. Electromagnetic Compatibility
Ensuring electromagnetic compatibility in military PCBs is critical to prevent interference with other electronic systems and to avoid detection by enemy forces. This requires careful design and layout of the PCB, as well as the use of shielding and filtering techniques.
4. Obsolescence Management
Military systems often have long lifecycles, which can lead to component obsolescence issues. Designing PCBs to accommodate alternative components or using obsolescence management techniques, such as lifetime buy or redesign, is essential to ensure the long-term supportability of the system.
5. Security and Anti-Tamper Requirements
Military PCBs often contain sensitive information and intellectual property that must be protected from unauthorized access and reverse engineering. Implementing security and anti-tamper features, such as encryption and tamper-evident coatings, can add complexity to the design and manufacturing process.
Frequently Asked Questions (FAQ)
1. What is the difference between military and commercial PCBs?
Military PCBs are designed and manufactured to meet stringent requirements set by military standards, such as MIL-PRF-31032 and MIL-PRF-55110. They are built to withstand harsh environmental conditions, extreme temperatures, vibrations, and shocks encountered in military operations. Commercial PCBs, on the other hand, are designed for less demanding applications and may not have the same level of durability and reliability as military PCBs.
2. What materials are commonly used in military PCBs?
Common materials used in military PCBs include FR-4, polyimide, PTFE (Teflon), and ceramic. The choice of material depends on the specific application and the required performance characteristics, such as thermal stability, dielectric constant, and mechanical strength.
3. How are military PCBs tested and qualified?
Military PCBs undergo rigorous testing and qualification processes to ensure they meet the required performance, reliability, and durability standards. This includes functional testing, environmental testing (temperature cycling, thermal shock, humidity exposure), mechanical testing (vibration and shock), and EMC testing.
4. What are some common applications of military PCBs?
Military PCBs find applications in a wide range of systems and equipment used by the armed forces, such as communication systems, radar and sonar systems, avionics and navigation systems, weapon control systems, and unmanned systems (UAVs and UGVs).
5. What are the challenges in designing and manufacturing military PCBs?
Designing and manufacturing PCBs for military applications presents several unique challenges, including stringent requirements and standards, harsh environmental conditions, electromagnetic compatibility, obsolescence management, and security and anti-tamper requirements. Meeting these challenges requires specialized design and manufacturing processes, which can increase costs and lead times compared to commercial PCBs.
Conclusion
Military PCBs play a critical role in ensuring the reliability, durability, and performance of various devices and systems used by the armed forces. These PCBs are designed and manufactured to meet stringent requirements set by military standards, enabling them to withstand harsh environmental conditions, extreme temperatures, vibrations, and shocks encountered in military operations.
Designing and manufacturing military PCBs involves careful consideration of various factors, such as material selection, thermal management, electromagnetic compatibility, shock and vibration resistance, and security and anti-tamper features. The manufacturing process for military PCBs is more rigorous and tightly controlled compared to commercial PCBs, with strict quality control measures implemented throughout the fabrication and assembly stages.
Military PCBs find applications in a wide range of systems and equipment, including communication systems, radar and sonar systems, avionics and navigation systems, weapon control systems, and unmanned systems. As military technology continues to evolve, the demand for high-performance, reliable, and secure PCBs will only increase, driving innovation in PCB design and manufacturing for military applications.
Leave a Reply