Why Use Multiple PCB Layers?
There are several reasons why multi-layer PCBs are used instead of single or double-sided boards:
-
Increased component density: Multi-layer PCBs allow for a higher density of components and interconnects compared to single or double-sided boards. This is because the additional layers provide more space for routing traces.
-
Improved signal integrity: Having dedicated layers for power and ground planes helps reduce electromagnetic interference (EMI) and improves signal integrity. The power and ground planes act as shields between signal layers.
-
Better power distribution: Multi-layer PCBs have lower inductance and resistance compared to single or double-sided boards, which results in better power distribution to components.
-
Reduced crosstalk: The additional layers allow for greater separation between signal traces, which reduces crosstalk and improves signal quality.
-
Smaller form factor: By using multiple layers, PCBs can be made smaller and more compact while still accommodating a large number of components and interconnects.
PCB Layer Stack-up
The arrangement of copper and insulating layers in a multi-layer PCB is referred to as the stack-up. The stack-up defines the number of layers, the thickness of each layer, and the order in which they are stacked.
Here is an example of a typical 4-layer PCB stack-up:
Layer | Material | Thickness |
---|---|---|
Top Solder Mask | Epoxy | 0.0005″ |
Top Copper | Copper | 0.0014″ |
Core | FR-4 | 0.0079″ |
Inner Copper 1 | Copper | 0.0014″ |
Prepreg | FR-4 | 0.0039″ |
Inner Copper 2 | Copper | 0.0014″ |
Core | FR-4 | 0.0079″ |
Bottom Copper | Copper | 0.0014″ |
Bottom Solder Mask | Epoxy | 0.0005″ |
The stack-up includes the following elements:
-
Solder mask: This is a thin layer of polymer applied to the outer layers of the PCB. It protects the copper traces from oxidation and prevents solder bridges from forming between closely spaced pads.
-
Copper layers: These are the conductive layers that carry electrical signals and power. The thickness of the copper is specified in ounces per square foot, with 1 oz/ft² (35 µm) being a common standard.
-
Core: This is a thick layer of insulating material, typically FR-4 glass-reinforced epoxy laminate. The core provides mechanical support for the PCB.
-
Prepreg: This is a thin layer of insulating material used to bond multiple cores together in PCBs with more than two layers. Prepreg is typically made from the same material as the core, but is partially cured to allow for better adhesion during lamination.
The number and arrangement of layers in the stack-up depends on the specific requirements of the PCB design, such as signal integrity, power distribution, and routing density.
Types of PCB Layers
There are several types of layers that can be included in a multi-layer PCB, each serving a specific purpose:
Signal Layers
Signal layers are used for routing traces that carry electrical signals between components. These layers are typically located on the outer layers of the PCB, but can also be placed on inner layers in more complex designs.
When routing signal traces, it is important to consider factors such as trace width, spacing, and impedance control to ensure signal integrity and minimize crosstalk.
Power and Ground Planes
Power and ground planes are continuous copper layers that provide a low-impedance path for distributing power and ground to components. These planes are typically located on inner layers of the PCB, sandwiched between signal layers.
Having dedicated power and ground planes helps reduce EMI and improves signal integrity by providing a stable reference voltage for signals. The planes also act as shields between signal layers, reducing crosstalk.
Split Planes
In some cases, it may be necessary to split a power or ground plane into multiple regions to accommodate different voltage levels or to isolate noise-sensitive circuits. This is referred to as a split plane.
Split planes are created by etching a gap in the copper to separate the regions. The gap is typically filled with the same insulating material as the core or prepreg.
Mechanical Layers
Mechanical layers are non-conductive layers that provide structural support for the PCB. These layers are typically made from the same material as the core or prepreg, and do not contain any copper.
Mechanical layers can be added to increase the overall thickness of the PCB for improved rigidity, or to provide additional insulation between conductive layers.
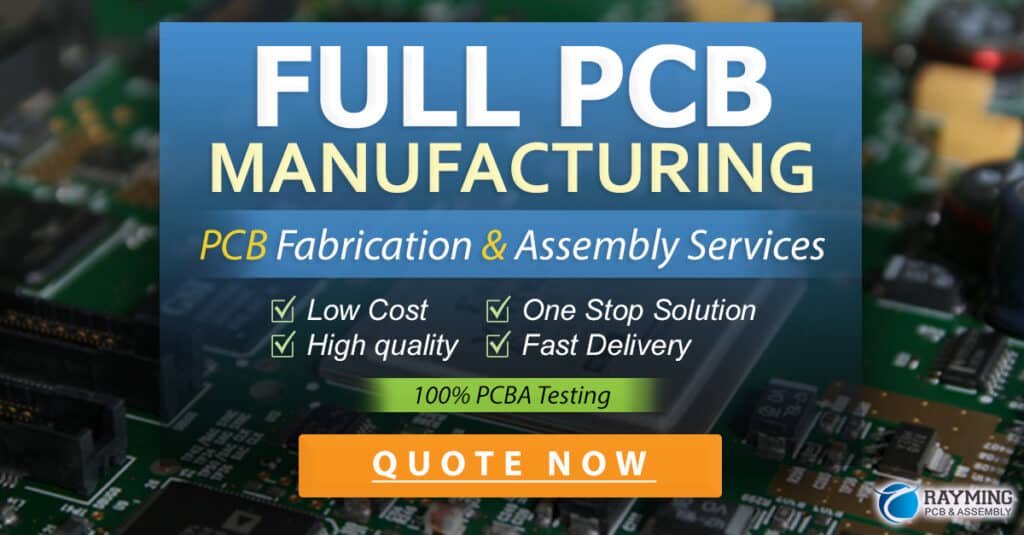
Designing Multi-Layer PCBs
Designing multi-layer PCBs requires careful planning and consideration of various factors such as signal integrity, power distribution, and manufacturability. Here are some key considerations when designing multi-layer PCBs:
Layer Stack-up
Choosing the appropriate layer stack-up is critical for ensuring the performance and reliability of the PCB. Factors to consider include the number of layers, the thickness of each layer, and the arrangement of signal, power, and ground layers.
The stack-up should be designed to minimize crosstalk and EMI, while providing adequate insulation between layers. It is also important to consider the manufacturing capabilities of the pcb fabricator, as some stack-ups may be more difficult or expensive to manufacture.
Signal Integrity
Maintaining signal integrity is crucial in multi-layer PCBs, especially at high frequencies. Factors that can affect signal integrity include trace geometry, impedance control, and crosstalk.
To minimize crosstalk and ensure proper impedance control, traces should be routed with appropriate spacing and width, and should be matched in length where necessary. In some cases, it may be necessary to use techniques such as guard traces or differential pairs to further improve signal integrity.
Power Distribution Network (PDN)
The power distribution network (PDN) is responsible for delivering power to all the components on the PCB. In multi-layer PCBs, the PDN typically consists of one or more power and ground planes, as well as decoupling capacitors and other components.
Designing an effective PDN requires careful consideration of factors such as voltage drop, current density, and impedance. The PDN should be designed to minimize voltage ripple and ensure that each component receives adequate power.
Thermal Management
Multi-layer PCBs can generate significant amounts of heat, especially in high-power applications. Proper thermal management is essential to ensure the reliability and longevity of the PCB and its components.
Techniques for managing heat in multi-layer PCBs include using thermal vias to transfer heat from inner layers to outer layers, incorporating thermal planes or heat spreaders, and using high-thermal-conductivity materials such as metal-core PCBs.
Manufacturability
Designing a multi-layer PCB that is easy to manufacture can help reduce costs and improve reliability. Factors to consider include the minimum feature size, aspect ratio, and drill size.
It is also important to follow good design for manufacturing (DFM) practices, such as avoiding acute angles and using appropriate clearances and tolerances. Working closely with the PCB fabricator can help ensure that the design is manufacturable and meets their capabilities.
PCB Layer FAQs
1. What is the maximum number of layers in a PCB?
There is no hard limit to the number of layers that can be used in a PCB, but practical considerations such as cost and manufacturability typically limit the number of layers to around 40 or 50. The most complex PCBs used in advanced applications such as aerospace or high-performance computing may have up to 100 layers or more.
2. What is the typical thickness of a PCB layer?
The thickness of a PCB layer depends on the specific material and manufacturing process used. Copper layers are typically specified in ounces per square foot, with 1 oz/ft² (35 µm) being a common standard. The thickness of the insulating layers (core and prepreg) can vary depending on the desired overall thickness of the PCB, but is typically in the range of 0.005″ to 0.010″ (0.13 to 0.25 mm).
3. What materials are used for PCB layers?
The most common material used for PCB layers is FR-4, a glass-reinforced epoxy laminate. Other materials include polyimide, PTFE (Teflon), and high-frequency laminates such as Rogers or Isola. Copper is used for the conductive layers, while solder mask is typically made from a photosensitive polymer.
4. How are multi-layer PCBs manufactured?
Multi-layer PCBs are manufactured by laminating multiple layers of copper and insulating material together under high pressure and temperature. The process involves the following steps:
- Etching the copper layers to create the desired traces and features
- Aligning and stacking the layers in the proper order
- Laminating the layers together using heat and pressure
- Drilling and plating through-holes to connect the layers
- Applying solder mask and silkscreen
- Cutting the PCB to its final shape
5. What are blind and buried vias in a multi-layer PCB?
Blind vias are holes that connect an outer layer to an inner layer, but do not go all the way through the PCB. Buried vias are holes that connect two or more inner layers, but do not connect to either outer layer. These types of vias are used to save space and improve routing density in multi-layer PCBs, but they are more complex and expensive to manufacture than through-hole vias.
Conclusion
PCB layers are a critical aspect of designing and manufacturing multi-layer PCBs. By using multiple layers of copper and insulating material, PCBs can achieve higher component density, improved signal integrity, better power distribution, and reduced crosstalk compared to single or double-sided boards.
When designing multi-layer PCBs, it is important to consider factors such as the layer stack-up, signal integrity, power distribution network, thermal management, and manufacturability. By carefully planning and optimizing these aspects, designers can create high-performance PCBs that meet the specific requirements of their application.
As PCB technology continues to evolve, the use of multi-layer designs will become increasingly important for meeting the demands of advanced electronic systems. By understanding the fundamentals of PCB layers and applying best practices in design and manufacturing, engineers can create PCBs that are reliable, efficient, and cost-effective.
Leave a Reply