Introduction to PCB Assembly
PCB assembly, short for printed circuit board assembly, is the process of attaching electronic components to a printed circuit board to create a functional electronic device. It involves a series of steps, including placing components on the board, soldering them in place, and testing the completed assembly to ensure proper functionality.
PCBs are the backbone of modern electronics. They provide a platform for components to be mounted and interconnected, allowing for complex circuits to be built in a compact and organized manner. PCB assembly is a crucial step in the manufacturing process of electronic devices, as it determines the reliability, performance, and overall quality of the final product.
Types of PCB Assembly
There are two main types of PCB assembly: through-hole and surface mount.
Through-Hole Assembly
Through-hole assembly is the traditional method of PCB assembly. It involves inserting component leads through drilled holes in the PCB and soldering them to pads on the opposite side of the board. This method is suitable for larger components and provides a strong mechanical connection. However, it is slower and less space-efficient compared to surface mount assembly.
Surface Mount Assembly
Surface mount assembly, also known as SMT (Surface Mount Technology), is a more modern method of PCB assembly. It involves placing components directly onto pads on the surface of the PCB and soldering them in place. SMT allows for smaller components and higher component density, resulting in more compact and efficient PCB designs. It is faster and more cost-effective than through-hole assembly, making it the preferred choice for high-volume production.
The pcb assembly process
The PCB assembly process typically involves the following steps:
-
Solder Paste Application: Solder paste, a mixture of tiny solder particles and flux, is applied to the pads on the PCB using a stencil or screen printing process.
-
Component Placement: Components are placed onto the pads on the PCB using automated pick-and-place machines or by hand for low-volume or prototype assemblies.
-
Reflow Soldering: The PCB with components is passed through a reflow oven, which heats the board to a specific temperature profile, melting the solder paste and forming a solid connection between the components and the pads.
-
Inspection and Testing: The assembled pcb is visually inspected for any defects or misaligned components. Automated optical inspection (AOI) systems may be used for high-volume production. Functional testing is performed to ensure the PCB operates as intended.
-
Cleaning and Coating: The PCB is cleaned to remove any residual flux or contaminants. A protective coating, such as conformal coating, may be applied to protect the PCB from environmental factors like moisture, dust, and corrosion.
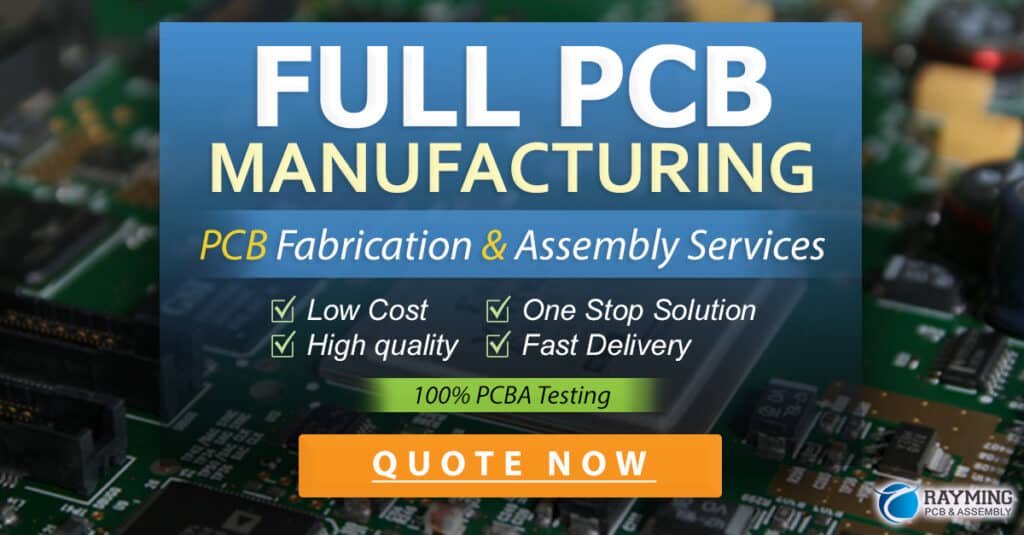
PCB Assembly Equipment and Tools
Various equipment and tools are used in the PCB assembly process, depending on the type of assembly and the scale of production. Some common equipment and tools include:
- Stencil Printer: Used to apply solder paste to the pads on the PCB.
- Pick-and-Place Machine: Automated machine that places components onto the PCB with high speed and precision.
- Reflow Oven: Heats the PCB to melt the solder paste and form a solid connection between components and pads.
- Soldering Iron: Hand tool used for manual soldering of through-hole components or rework.
- Inspection Microscope: Used for visual inspection of the assembled PCB.
- Automated Optical Inspection (AOI) System: Automated system that uses cameras and image processing to inspect the PCB for defects.
- Functional Testing Equipment: Various equipment used to test the functionality of the assembled PCB, such as oscilloscopes, multimeters, and in-circuit testers.
PCB Assembly Standards and Regulations
PCB assembly must adhere to various industry standards and regulations to ensure the quality, reliability, and safety of the final product. Some common standards and regulations include:
-
IPC Standards: The Association Connecting Electronics Industries (IPC) maintains a set of standards for PCB design, fabrication, and assembly, such as IPC-A-610 for acceptability of electronic assemblies and IPC-J-STD-001 for requirements for soldered electrical and electronic assemblies.
-
RoHS (Restriction of Hazardous Substances): A directive that restricts the use of certain hazardous substances, such as lead, in electronic and electrical equipment.
-
REACH (Registration, Evaluation, Authorization, and Restriction of Chemicals): A European Union regulation that addresses the production and use of chemical substances and their potential impacts on human health and the environment.
-
UL (Underwriters Laboratories): An independent safety certification organization that tests and certifies electronic products for safety.
PCB Assembly Challenges and Solutions
PCB assembly can present various challenges, depending on the complexity of the design, the components used, and the manufacturing process. Some common challenges and their solutions include:
Tombstoning
Tombstoning is a defect that occurs when a surface mount component stands up on one end during the reflow soldering process, resulting in a poor or missing connection. This can be caused by uneven heating, incorrect solder paste application, or component misalignment.
Solutions:
– Ensure proper solder paste application and component placement
– Optimize reflow oven temperature profile
– Use solder paste with appropriate viscosity and particle size
Bridging
Bridging is a defect where solder connects two or more pads or leads that should not be connected, creating a short circuit. This can be caused by excessive solder paste application, incorrect component placement, or insufficient spacing between pads.
Solutions:
– Ensure proper solder paste application and component placement
– Optimize stencil design for appropriate solder paste volume
– Increase spacing between pads in the PCB design
Component Shifting
Component shifting occurs when components move from their intended position during the reflow soldering process, resulting in misalignment or poor connections. This can be caused by insufficient solder paste, incorrect placement, or vibrations during the reflow process.
Solutions:
– Ensure proper solder paste application and component placement
– Use a pick-and-place machine with vision systems for accurate placement
– Optimize reflow oven conveyor speed and minimize vibrations
pcb assembly cost Factors
The cost of PCB assembly depends on various factors, including:
- PCB Complexity: More complex PCB designs with higher layer counts, smaller feature sizes, and tighter tolerances will increase the assembly cost.
- Component Count and Type: The number and type of components used in the assembly will affect the cost. Surface mount components are generally less expensive than through-hole components.
- Assembly Method: Automated assembly methods, such as pick-and-place and reflow soldering, are more cost-effective for high-volume production, while manual assembly may be more suitable for low-volume or prototype runs.
- Order Quantity: Higher order quantities typically result in lower per-unit costs due to economies of scale.
- Turnaround Time: Faster turnaround times may incur additional costs due to expedited processing and shipping.
Choosing a PCB Assembly Service Provider
When selecting a PCB assembly service provider, consider the following factors:
- Capabilities: Ensure the provider has the necessary equipment, expertise, and experience to handle your specific PCB assembly requirements.
- Quality Control: Look for providers with a robust quality control process, including automated inspection systems and adherence to industry standards and regulations.
- Turnaround Time: Consider the provider’s typical turnaround times and whether they can accommodate your project timeline.
- Customer Support: Choose a provider with responsive and knowledgeable customer support to assist with any questions or issues throughout the assembly process.
- Pricing: Obtain quotes from multiple providers and compare pricing, but also consider the value of quality, reliability, and service.
PCB Assembly vs. pcb fabrication
PCB assembly and PCB fabrication are two distinct processes in the overall manufacturing of printed circuit boards.
Process | Description | Key Steps |
---|---|---|
PCB Fabrication | The process of creating the bare PCB substrate, including etching copper traces, drilling holes, and applying solder mask and silkscreen. | 1. PCB Design 2. Substrate Preparation 3. Copper Etching 4. Drilling 5. Solder Mask Application 6. Silkscreen Application |
PCB Assembly | The process of attaching electronic components to the fabricated PCB to create a functional electronic assembly. | 1. Solder Paste Application 2. Component Placement 3. Reflow Soldering 4. Inspection and Testing 5. Cleaning and Coating |
pcb fabrication and assembly can be performed by the same company or by separate specialized providers, depending on the project requirements and the capabilities of the chosen manufacturers.
Future Trends in PCB Assembly
As electronic devices continue to advance and evolve, PCB assembly technologies and processes must keep pace. Some future trends in PCB assembly include:
- Miniaturization: The demand for smaller, more compact electronic devices will drive the need for advanced PCB assembly techniques to accommodate smaller components and higher component densities.
- Flexible and Stretchable Electronics: The growing interest in wearable devices and the Internet of Things (IoT) will require PCB assembly processes that can handle flexible and stretchable substrates.
- 3D Printing: Additive manufacturing technologies, such as 3D printing, may be increasingly used for creating complex PCB structures and embedding components within the board.
- Automation and AI: Advancements in automation and artificial intelligence will enable more efficient, accurate, and adaptive PCB assembly processes, improving quality and reducing costs.
- Sustainable Manufacturing: There will be a growing emphasis on environmentally friendly PCB assembly practices, such as the use of lead-free solders and the reduction of waste and energy consumption.
Frequently Asked Questions (FAQ)
-
What is the difference between through-hole and surface mount assembly?
Through-hole assembly involves inserting component leads through drilled holes in the PCB and soldering them to pads on the opposite side, while surface mount assembly involves placing components directly onto pads on the surface of the PCB and soldering them in place. Surface mount assembly allows for smaller components and higher component density, making it more space-efficient and cost-effective for high-volume production. -
What is solder paste, and how is it applied in PCB assembly?
Solder paste is a mixture of tiny solder particles and flux used in surface mount assembly. It is applied to the pads on the PCB using a stencil or screen printing process before components are placed. During the reflow soldering process, the solder paste melts and forms a solid connection between the components and the pads. -
What is the purpose of a pick-and-place machine in PCB assembly?
A pick-and-place machine is an automated machine used in surface mount assembly to place components onto the pads on the PCB with high speed and precision. It improves the efficiency and accuracy of the assembly process compared to manual placement, making it suitable for high-volume production. -
What are some common defects that can occur during PCB assembly, and how can they be prevented?
Some common defects in PCB assembly include tombstoning (components standing up on one end), bridging (solder connecting pads that should not be connected), and component shifting (components moving from their intended position). These defects can be prevented by ensuring proper solder paste application, optimizing reflow oven temperature profiles, using appropriate stencil designs, and maintaining accurate component placement. -
What factors should I consider when choosing a PCB assembly service provider?
When choosing a PCB assembly service provider, consider their capabilities, quality control processes, turnaround times, customer support, and pricing. Look for providers with the necessary equipment, expertise, and experience to handle your specific assembly requirements, and ensure they have a robust quality control process that adheres to industry standards and regulations. Also, consider their responsiveness and ability to accommodate your project timeline and budget.
Conclusion
PCB assembly is a critical process in the manufacturing of electronic devices, involving the attachment of electronic components to a printed circuit board. It encompasses various methods, such as through-hole and surface mount assembly, and requires specialized equipment, tools, and expertise. Successful PCB assembly depends on adherence to industry standards, effective quality control, and the ability to overcome common challenges, such as tombstoning, bridging, and component shifting.
As electronic devices continue to evolve, PCB assembly technologies and processes must adapt to accommodate new trends, such as miniaturization, flexible electronics, and sustainable manufacturing practices. By understanding the fundamentals of PCB assembly and partnering with experienced and reliable service providers, businesses can ensure the production of high-quality, reliable electronic products that meet the demands of an ever-changing market.
Leave a Reply