Table of Contents
- Introduction to PCBs
- The History of PCBs
- PCB Materials and Composition
- PCB Manufacturing Process
- Types of PCBs
- pcb design Considerations
- pcb assembly Techniques
- Applications of PCBs
- The Future of PCBs
- Frequently Asked Questions (FAQ)
Introduction to PCBs
A PCB is a thin board made of insulating materials, such as fiberglass or composite epoxy, with conductive copper traces printed on its surface. These traces form the electrical connections between various components mounted on the board, such as resistors, capacitors, integrated circuits (ICs), and connectors.
PCBs offer several advantages over traditional point-to-point wiring:
- Compact size: PCBs allow for high-density component placement, reducing the overall size of electronic devices.
- Reliability: Copper traces on PCBs provide stable and reliable electrical connections, minimizing the risk of short circuits or loose connections.
- Mass production: PCBs can be easily mass-produced using automated manufacturing processes, reducing production time and costs.
- Consistency: Automated PCB manufacturing ensures consistent quality and eliminates human errors in wiring.
The History of PCBs
The development of PCBs can be traced back to the early 20th century. Here are some key milestones in the history of PCBs:
Year | Milestone |
---|---|
1903 | Albert Hanson files a patent for a “printed wire” concept, using conductive metal strips on an insulating board. |
1925 | Charles Ducas receives a patent for a method of creating an electrical path directly on an insulated surface. |
1936 | Paul Eisler develops the first operational printed circuit for a radio application. |
1943 | The U.S. military adopts PCBs for use in proximity fuses during World War II. |
1948 | The U.S. Army releases the first specifications for PCB design and manufacturing. |
1950s | Double-sided PCBs and plated through-holes are introduced, enabling more complex designs. |
1960s | Multilayer PCBs and surface-mount technology (SMT) emerge, further reducing the size of electronic devices. |
1980s | Computer-aided design (CAD) software revolutionizes PCB design and manufacturing processes. |
1990s | High-density interconnect (HDI) PCBs gain popularity, enabling even smaller and more complex designs. |
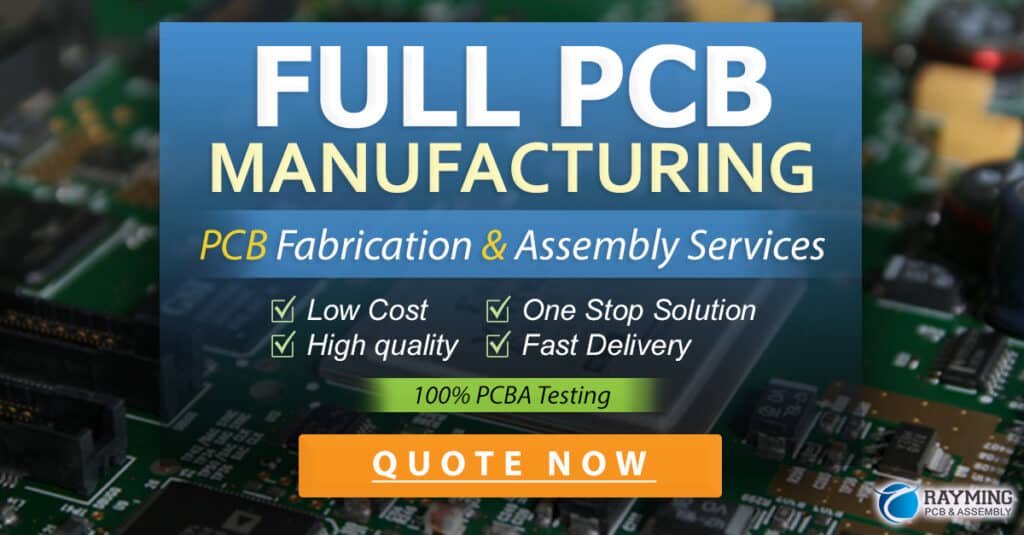
PCB Materials and Composition
A typical PCB consists of several layers:
- Substrate: The base material, usually made of fiberglass (FR-4) or composite epoxy, provides mechanical support and electrical insulation.
- Copper layers: Thin layers of copper foil are laminated onto the substrate, forming the conductive traces for electrical connections.
- Solder mask: A protective layer applied over the copper traces, leaving only the exposed areas for soldering components.
- Silkscreen: A printed layer containing text and symbols for component identification and assembly instructions.
Other materials used in PCB manufacturing include:
- Prepreg: A partially cured epoxy resin used to bond copper layers together in multilayer PCBs.
- Solder: A metal alloy, typically composed of tin and lead (or lead-free alternatives), used for soldering components to the PCB.
- Conformal coating: A protective coating applied to the finished PCB to protect against moisture, dust, and other environmental factors.
PCB Manufacturing Process
The PCB manufacturing process involves several key steps:
- Design: The pcb layout is designed using CAD software, specifying the component placement, trace routing, and other design parameters.
- Fabrication: The designed PCB is fabricated using a series of processes, including:
- Printing the circuit pattern onto the copper-clad substrate using photoresist and etching techniques.
- Drilling holes for through-hole components and vias.
- Applying solder mask and silkscreen layers.
- Assembly: Components are mounted onto the fabricated PCB using various techniques, such as through-hole assembly or surface-mount technology (SMT).
- Testing and inspection: The assembled PCB undergoes rigorous testing and inspection to ensure proper functionality and quality.
Types of PCBs
PCBs can be classified based on various factors, such as the number of layers, component mounting method, and manufacturing technology. Some common types of PCBs include:
- Single-sided PCBs: Components are mounted on one side of the board, with conductive traces on the opposite side.
- Double-sided PCBs: Components and conductive traces are present on both sides of the board, with through-hole connections between layers.
- Multilayer PCBs: Multiple layers of conductive traces are sandwiched between insulating layers, enabling more complex designs and higher component density.
- flexible pcbs: Made from flexible materials, such as polyimide, these PCBs can bend and conform to various shapes.
- Rigid-flex PCBs: A combination of rigid and flexible PCBs, allowing for both stability and flexibility in the design.
- High-density interconnect (HDI) PCBs: Featuring finer trace widths and smaller vias, HDI PCBs enable even higher component density and miniaturization.
PCB Design Considerations
Designing a PCB involves several key considerations to ensure optimal performance, reliability, and manufacturability:
- Component placement: Proper component placement is crucial for signal integrity, thermal management, and ease of assembly.
- Trace routing: Traces must be routed efficiently to minimize signal interference, maintain proper impedance, and avoid crosstalk.
- Power and ground planes: Dedicated power and ground planes help maintain signal integrity and reduce electromagnetic interference (EMI).
- Thermal management: Adequate heat dissipation measures, such as thermal vias and copper pours, must be incorporated to prevent overheating.
- Manufacturing constraints: The design must adhere to manufacturing limitations, such as minimum trace widths, hole sizes, and clearances.
- Testing and debugging: Provisions for testing and debugging, such as test points and debug headers, should be included in the design.
PCB Assembly Techniques
There are two primary methods for assembling components onto a PCB:
- Through-hole assembly: Components with wire leads are inserted through drilled holes in the PCB and soldered on the opposite side.
- Surface-mount technology (SMT): Components are mounted directly onto the surface of the PCB, with solder paste applied to the component pads before placement and soldering.
SMT has largely replaced through-hole assembly in modern electronics manufacturing due to its numerous advantages:
- Higher component density
- Faster assembly process
- Lower production costs
- Improved mechanical stability
- Better high-frequency performance
However, some components, such as connectors and large power devices, may still require through-hole assembly.
Applications of PCBs
PCBs are ubiquitous in modern electronic devices and systems, finding applications across various industries:
- Consumer electronics: Smartphones, tablets, laptops, televisions, and home appliances.
- Automotive: Engine control units (ECUs), infotainment systems, and advanced driver assistance systems (ADAS).
- Medical devices: Diagnostic equipment, patient monitoring systems, and implantable devices.
- Industrial automation: Programmable logic controllers (PLCs), sensors, and motor drives.
- Aerospace and defense: Avionics, satellite communication systems, and military equipment.
- Internet of Things (IoT): Smart home devices, wearables, and industrial IoT sensors.
The widespread adoption of PCBs has enabled the rapid advancement of electronic technologies, making devices smaller, more powerful, and more affordable.
The Future of PCBs
As electronic devices continue to evolve, so do PCB technologies. Some emerging trends and developments in the PCB industry include:
- Advanced materials: New substrate materials, such as high-frequency laminates and metal-core PCBs, are being developed to meet the demands of 5G, automotive, and aerospace applications.
- Embedded components: Integrating passive components, such as resistors and capacitors, directly into the PCB substrate, further reducing the size and improving the performance of electronic devices.
- 3D printing: Additive manufacturing techniques are being explored for pcb fabrication, enabling rapid prototyping and customization.
- Artificial intelligence (AI) in design and manufacturing: AI-driven tools are being developed to optimize PCB design, component placement, and manufacturing processes, improving efficiency and reducing time-to-market.
- Environmental sustainability: The industry is focusing on developing eco-friendly materials and processes, such as halogen-free laminates and lead-free solders, to minimize the environmental impact of PCB manufacturing.
As technology continues to advance, PCBs will remain at the heart of electronic devices, adapting and evolving to meet the ever-changing demands of the industry.
Frequently Asked Questions (FAQ)
- What is the difference between a PCB and a printed wiring board (PWB)?
-
PCB and PWB are often used interchangeably, but historically, PWB referred to boards with through-hole components, while PCB encompassed both through-hole and surface-mount technologies.
-
Can PCBs be recycled?
-
Yes, PCBs can be recycled to recover valuable materials, such as copper and precious metals. However, the recycling process is complex and requires specialized facilities to handle the various materials and potential hazardous substances.
-
How long does it take to manufacture a PCB?
-
The manufacturing time for a PCB depends on factors such as the complexity of the design, the number of layers, and the manufacturing process. Simple, single-sided PCBs can be manufactured in a few days, while complex, multilayer PCBs may take several weeks.
-
What is the minimum feature size possible on a PCB?
-
The minimum feature size on a PCB depends on the manufacturing capabilities of the PCB fabricator. Advanced HDI PCBs can have trace widths and spacing as small as 50 microns (0.05 mm), while standard PCBs typically have minimum feature sizes around 0.1 mm.
-
How can I ensure my PCB design is manufacturable?
- To ensure manufacturability, follow design guidelines provided by your PCB fabricator, such as minimum trace widths, hole sizes, and clearances. Utilize design for manufacturing (DFM) tools to check your design for potential manufacturing issues, and consult with your fabricator early in the design process to address any concerns.
In conclusion, PCBs have revolutionized the electronics industry, enabling the development of smaller, more powerful, and more reliable electronic devices. As technology continues to advance, PCBs will remain a critical component in the design and manufacturing of electronic systems, adapting to meet the ever-evolving demands of the industry.
Leave a Reply