Introduction to High TG PCBs
High TG PCBs, also known as high glass transition temperature printed circuit boards, are specialized types of PCBs designed to withstand elevated temperatures and harsh environmental conditions. These PCBs are manufactured using materials with higher glass transition temperatures (Tg), which refers to the temperature at which a material transitions from a rigid, glassy state to a softer, rubbery state.
What is Glass Transition Temperature (Tg)?
Glass transition temperature (Tg) is a critical property of PCB materials that determines their ability to maintain their mechanical and electrical properties at elevated temperatures. It is the temperature at which a material transitions from a hard, glassy state to a soft, rubbery state. Materials with higher Tg values can withstand higher temperatures without losing their structural integrity or electrical performance.
Importance of High TG PCBs in Electronics Industry
High TG PCBs are essential in the electronics industry, particularly in applications that require reliable performance under extreme temperature conditions. Some of the key applications of high TG PCBs include:
- Automotive electronics
- Aerospace and defense systems
- Industrial control systems
- High-power LED lighting
- Medical devices
In these applications, PCBs are often exposed to high temperatures, thermal cycling, and other harsh environmental factors. High TG PCBs ensure that the electronic components and circuits remain stable and functional despite these challenges.
Materials Used in High TG PCBs
Common High TG PCB Materials
Several materials are commonly used in the manufacture of high TG PCBs. These materials are selected based on their thermal, mechanical, and electrical properties. Some of the most popular high TG PCB materials include:
- Polyimide (PI)
- High Tg FR-4
- Bismaleimide Triazine (BT)
- Cyanate Ester (CE)
- Polytetrafluoroethylene (PTFE)
Each of these materials has unique characteristics that make them suitable for specific applications. The choice of material depends on factors such as the required Tg value, dielectric constant, dissipation factor, and cost.
Comparison of High TG PCB Materials
Material | Glass Transition Temperature (Tg) | Dielectric Constant | Dissipation Factor | Thermal Conductivity (W/mK) |
---|---|---|---|---|
Polyimide (PI) | 260°C – 400°C | 3.4 – 3.5 | 0.002 – 0.003 | 0.1 – 0.3 |
High Tg FR-4 | 170°C – 180°C | 4.2 – 4.5 | 0.02 – 0.03 | 0.3 – 0.4 |
Bismaleimide Triazine (BT) | 210°C – 250°C | 3.9 – 4.1 | 0.01 – 0.02 | 0.2 – 0.3 |
Cyanate Ester (CE) | 250°C – 290°C | 3.2 – 3.4 | 0.003 – 0.005 | 0.2 – 0.3 |
Polytetrafluoroethylene (PTFE) | 327°C | 2.1 – 2.3 | 0.0002 – 0.0008 | 0.2 – 0.3 |
As seen in the table above, each material has its own set of properties that make it suitable for specific applications. Polyimide (PI) has the highest Tg range, making it ideal for high-temperature applications. PTFE, on the other hand, has the lowest dielectric constant and dissipation factor, making it suitable for high-frequency applications.
Manufacturing Process of High TG PCBs
Multilayer High TG PCB Fabrication
Multilayer high TG PCBs are fabricated using a process similar to that of standard FR-4 PCBs, with some modifications to accommodate the unique properties of high TG materials. The general steps involved in the manufacturing process are:
- Material selection and preparation
- Inner layer fabrication
- Lamination
- Drilling
- Plating
- Outer layer fabrication
- Solder mask application
- Surface finish application
- Electrical testing and inspection
Challenges in High TG PCB Manufacturing
Manufacturing high TG PCBs presents several challenges due to the unique properties of the materials used. Some of the key challenges include:
- Higher processing temperatures
- Increased brittleness of materials
- Difficulty in drilling and plating
- Increased cost of materials and processing
To overcome these challenges, PCB manufacturers use specialized equipment and processes, such as laser drilling, controlled-depth drilling, and high-temperature lamination. They also employ strict quality control measures to ensure that the finished PCBs meet the required specifications.
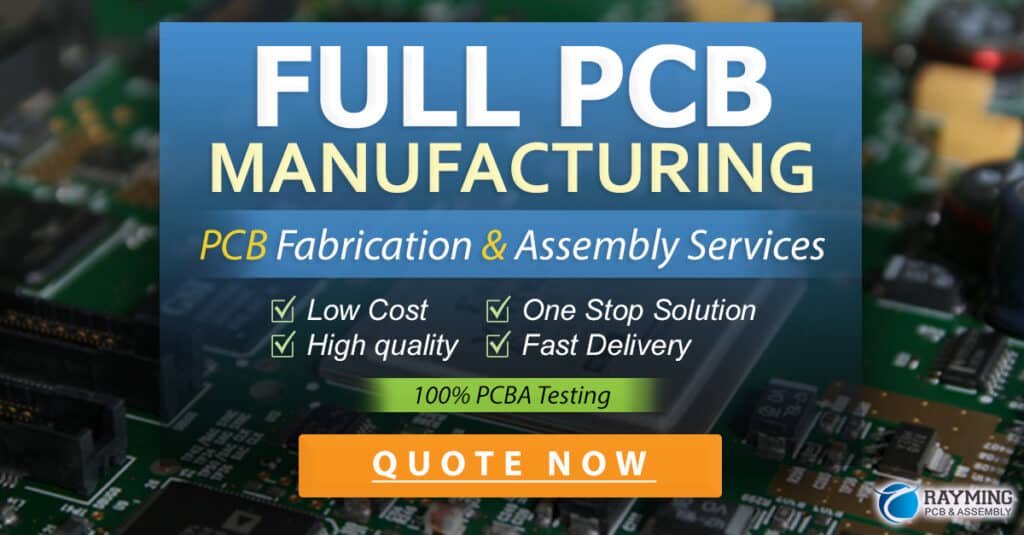
Design Considerations for High TG PCBs
Thermal Management
Thermal management is a critical aspect of high TG PCB design. As these PCBs are intended to operate at elevated temperatures, it is essential to ensure that the heat generated by the electronic components is effectively dissipated. Some of the thermal management techniques used in high TG PCB design include:
- Proper component placement and spacing
- Use of thermal vias and heat sinks
- Selection of materials with high thermal conductivity
- Incorporation of active cooling methods, such as fans or liquid cooling
Signal Integrity
Signal integrity is another important consideration in high TG PCB design. The high operating temperatures and the unique properties of high TG materials can affect the signal transmission characteristics of the PCB. To maintain signal integrity, designers must consider factors such as:
- Impedance matching
- Crosstalk reduction
- Minimizing signal reflections
- Proper termination of transmission lines
Reliability and Durability
High TG PCBs are often used in applications where reliability and durability are critical. To ensure that the PCBs can withstand the harsh operating conditions, designers must consider factors such as:
- Material selection based on the expected environmental conditions
- Proper design of plated through-holes (PTHs) and vias
- Use of conformal coatings or encapsulation to protect the PCB from moisture and contaminants
- Incorporation of strain relief features to minimize mechanical stress on the PCB
Applications of High TG PCBs
Automotive Electronics
High TG PCBs are widely used in automotive electronics, particularly in under-hood applications where temperatures can exceed 150°C. Some examples of automotive applications include:
- Engine control units (ECUs)
- Transmission control modules
- Brake control systems
- Exhaust gas recirculation (EGR) systems
Aerospace and Defense Systems
In aerospace and defense systems, high TG PCBs are used in applications that require reliable operation in extreme temperature conditions and harsh environments. Some examples include:
- Avionics systems
- Radar and communication equipment
- Missile guidance systems
- Satellite electronics
Industrial Control Systems
Industrial control systems often involve high-power electronics and operate in environments with elevated temperatures. High TG PCBs are used in applications such as:
- Power inverters and converters
- Motor drives
- Programmable logic controllers (PLCs)
- Sensor and actuator interfaces
High-Power LED Lighting
High-power LED lighting systems generate significant amounts of heat, which can affect the performance and lifespan of the LEDs. High TG PCBs are used in LED lighting applications to ensure reliable operation and efficient heat dissipation.
Medical Devices
Medical devices, particularly those used in surgical procedures, often require PCBs that can withstand high temperatures associated with sterilization processes. High TG PCBs are used in medical applications such as:
- Surgical instruments
- Imaging equipment
- Patient monitoring systems
- Implantable devices
Future Trends in High TG PCB Technology
As the demand for high-performance electronics continues to grow, the development of advanced high TG PCB materials and manufacturing techniques is expected to accelerate. Some of the future trends in high TG PCB technology include:
- Development of materials with even higher Tg values and improved thermal conductivity
- Increased adoption of advanced manufacturing processes, such as 3D printing and embedded component technology
- Integration of high TG PCBs with other advanced technologies, such as wide bandgap semiconductors and advanced cooling solutions
- Expansion of high TG PCB applications into new industries, such as renewable energy and electric vehicles
Frequently Asked Questions (FAQ)
1. What is the difference between high TG PCBs and standard FR-4 PCBs?
High TG PCBs are manufactured using materials with higher glass transition temperatures (Tg) compared to standard FR-4 PCBs. This allows high TG PCBs to maintain their mechanical and electrical properties at elevated temperatures, making them suitable for applications that require reliable operation in harsh environmental conditions.
2. What are the most common materials used in high TG PCBs?
The most common materials used in high TG PCBs include polyimide (PI), high Tg FR-4, bismaleimide triazine (BT), cyanate ester (CE), and polytetrafluoroethylene (PTFE). Each material has its own set of thermal, mechanical, and electrical properties that make it suitable for specific applications.
3. How do high TG PCBs differ from other types of high-temperature PCBs?
High TG PCBs are a specific type of high-temperature PCB that rely on materials with high glass transition temperatures to maintain their properties at elevated temperatures. Other types of high-temperature PCBs may use different strategies, such as ceramic substrates or special coatings, to achieve reliable operation in high-temperature environments.
4. What are the key design considerations for high TG PCBs?
The key design considerations for high TG PCBs include thermal management, signal integrity, and reliability/durability. Designers must carefully select materials, component placement, and layout techniques to ensure that the PCB can effectively dissipate heat, maintain signal integrity, and withstand the harsh operating conditions.
5. What are some of the emerging trends in high TG PCB technology?
Some of the emerging trends in high TG PCB technology include the development of materials with even higher Tg values and improved thermal conductivity, increased adoption of advanced manufacturing processes (e.g., 3D printing and embedded component technology), integration with other advanced technologies (e.g., wide bandgap semiconductors and advanced cooling solutions), and expansion into new industries (e.g., renewable energy and electric vehicles).
Conclusion
High TG PCBs are a critical component in the development of reliable, high-performance electronics for applications that involve elevated temperatures and harsh environmental conditions. By using materials with high glass transition temperatures and employing advanced design and manufacturing techniques, high TG PCBs enable the operation of electronic systems in challenging environments such as automotive, aerospace, industrial, and medical applications.
As the demand for high-performance electronics continues to grow, the development of advanced high TG PCB materials and manufacturing processes will play a crucial role in enabling the next generation of electronic devices and systems. By staying at the forefront of high TG PCB technology, designers and manufacturers can create innovative solutions that push the boundaries of performance, reliability, and efficiency in the electronics industry.
Leave a Reply