Characteristics of High Current PCBs
To handle elevated current levels reliably, high current PCBs have several distinct characteristics:
Thicker Copper Traces
One of the most critical aspects of high current PCB design is the use of thicker copper traces. The thickness of the copper layer on a PCB is measured in ounces per square foot (oz/ft²). Standard PCBs often use 1 oz/ft² copper, which equates to a thickness of about 35 microns. However, high current PCBs typically employ copper weights ranging from 2 oz/ft² (70 microns) to 10 oz/ft² (350 microns) or more.
Thicker copper traces offer several advantages:
-
Lower resistance: Thicker traces have lower electrical resistance, allowing current to flow more easily and reducing power loss due to heat generation.
-
Improved heat dissipation: The increased copper volume helps to spread and dissipate heat more effectively, preventing localized hot spots that could damage components or the board itself.
-
Enhanced mechanical strength: Thicker traces are more robust and less prone to physical damage from vibration, impact, or thermal stress.
The choice of copper weight depends on the specific current requirements of the application. Here’s a general guide:
Current Range | Recommended Copper Weight |
---|---|
Up to 5A | 2 oz/ft² |
5A to 10A | 3 oz/ft² |
10A to 20A | 4 oz/ft² |
20A to 50A | 6 oz/ft² |
50A to 100A | 8 oz/ft² |
Over 100A | 10 oz/ft² or more |
Wider Trace Widths
In addition to being thicker, the traces on high current PCBs are also typically wider than those on standard boards. Wider traces further reduce resistance and increase current carrying capacity. The optimal trace width depends on several factors, including:
- The amperage of the current
- The allowable temperature rise
- The thickness of the copper layer
- The length of the trace
- The ambient temperature
PCB design software often includes tools to calculate the appropriate trace width based on these parameters. As a rule of thumb, trace widths for high current PCBs range from 0.5mm to several millimeters, compared to the 0.1-0.2mm traces common on signal-level boards.
Special Materials
High current PCBs may utilize specialized substrate materials to enhance their thermal and mechanical properties. While standard FR-4 glass-reinforced epoxy is suitable for many applications, high-performance alternatives include:
-
Aluminum-backed PCBs: These boards have an aluminum substrate that acts as a heat sink, efficiently dissipating heat away from the copper traces and components.
-
Ceramic substrates: Materials like alumina or aluminum nitride offer excellent thermal conductivity and stability, making them ideal for high-temperature environments.
-
Metal core PCBs (MCPCBs): Similar to aluminum-backed PCBs, MCPCBs have a metal core (usually aluminum) sandwiched between the copper traces and a thin dielectric layer. This construction provides superior heat dissipation and mechanical strength.
The choice of substrate material depends on the specific requirements of the application, such as the operating temperature range, power density, and cost constraints.
Power Management Techniques
Designing a high current PCB involves more than just using thicker copper and wider traces. Several power management techniques are employed to ensure optimal performance and reliability:
Power and Ground Planes
Instead of using individual traces for power distribution, high current PCBs often incorporate dedicated power and ground planes. These large, uninterrupted copper areas span the entire board, providing a low-impedance path for current flow. Power planes minimize voltage drops, reduce electromagnetic interference (EMI), and improve heat dissipation.
When designing power planes, it’s essential to consider the current density and the spacing between the planes. A general guideline is to keep the current density below 200 mA/mm² to prevent excessive heating. The spacing between power and ground planes should be sufficient to maintain a low impedance while avoiding capacitance issues that could affect signal integrity.
Decoupling Capacitors
Decoupling capacitors play a crucial role in managing power supply noise and transient currents on high current PCBs. These capacitors are placed close to the power pins of active components, such as ICs and microprocessors, to provide a local reservoir of charge. When a component demands a sudden surge of current, the decoupling capacitor supplies it, preventing the power supply voltage from drooping.
The placement and selection of decoupling capacitors are critical. They should be located as close as possible to the power pins, minimizing the inductance of the connection. A combination of ceramic and electrolytic capacitors is often used to cover a wide range of frequencies. Ceramic capacitors, typically in the nanofarad range, handle high-frequency noise, while electrolytic capacitors, in the microfarad range, deal with lower-frequency transients.
Current Sensing and Protection
Monitoring and controlling the current flow on a high current PCB is essential for safety and reliability. Current sensing techniques allow the system to detect overcurrent conditions and take appropriate action, such as shutting down or limiting the current.
Some common current sensing methods include:
-
Shunt resistors: A low-value resistor is placed in series with the load, and the voltage drop across it is measured to determine the current. This method is simple but dissipates power and affects the load voltage.
-
Hall effect sensors: These devices measure the magnetic field generated by the current flowing through a conductor. They provide galvanic isolation and don’t introduce a voltage drop, but they require additional circuitry and calibration.
-
Current transformers: A transformer with a primary winding in series with the load and a secondary winding connected to a measurement circuit. Current transformers offer isolation and low power dissipation but are bulky and expensive.
Once the current is sensed, protection mechanisms can be implemented. These may include fuses, circuit breakers, or electronic over-current protection (OCP) circuits that limit or disconnect the load when a fault is detected.
Thermal Management
Managing heat is a critical aspect of high current PCB design. As current flows through the traces, it generates heat due to the resistance of the copper. If this heat is not effectively dissipated, it can lead to component failure, board damage, and reduced reliability.
Several thermal management techniques are used in high current PCBs:
Heatsinks and Thermal Vias
Heatsinks are metal structures attached to components or areas of the PCB that generate significant heat. They increase the surface area available for heat dissipation and promote air flow, allowing heat to be removed more efficiently. Heatsinks can be passive (relying on natural convection) or active (using fans or other forced cooling methods).
Thermal vias are small holes drilled through the PCB and plated with copper. They provide a low-resistance path for heat to flow from the top layer of the board to the bottom layer or to an internal ground plane. By creating a network of thermal vias around high-power components, heat can be spread more evenly across the board, preventing hot spots.
Component Placement and Spacing
The placement of components on a high current PCB can have a significant impact on thermal management. Components that generate a lot of heat, such as power transistors or voltage regulators, should be spaced apart to avoid concentrating heat in one area. They should also be located close to the edge of the board or near mounting holes to facilitate heat transfer to an external heatsink or chassis.
When placing components, it’s important to consider the air flow pattern around the board. Components should be oriented to allow for maximum air flow, with hot components placed upstream of cooler ones. Obstructions to air flow, such as tall components or connectors, should be minimized.
Thermal Interface Materials
Thermal interface materials (TIMs) are substances used to improve the transfer of heat between components and heatsinks or between the PCB and a chassis. TIMs fill the microscopic gaps and irregularities between mating surfaces, eliminating air pockets that would otherwise act as thermal insulators.
Common TIMs include:
-
Thermal greases and pastes: These are viscous materials that are applied in a thin layer between the component and heatsink. They have good thermal conductivity and can conform to surface irregularities but can be messy to apply and may dry out over time.
-
Thermal pads: These are soft, flexible sheets of material that are placed between the component and heatsink. They are easier to apply than greases but have lower thermal conductivity and may require higher clamping pressure.
-
Phase change materials: These materials are solid at room temperature but melt and flow when heated, filling surface gaps and improving thermal contact. They offer good performance and ease of use but may be more expensive than other options.
The choice of TIM depends on the specific application, taking into account factors such as the expected temperature range, the clamping pressure available, and the ease of assembly and maintenance.
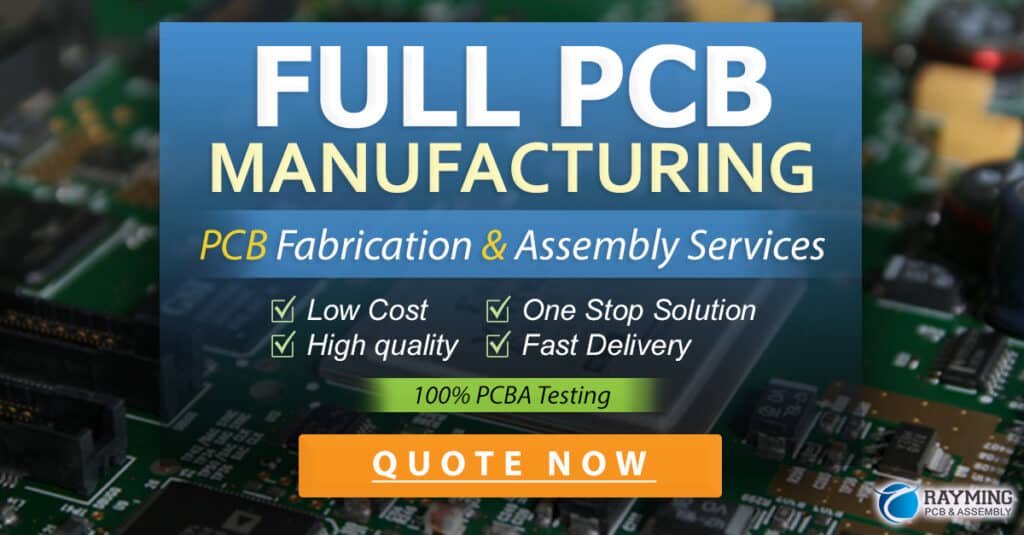
High Current PCB Manufacturing Considerations
Manufacturing high current PCBs requires specialized equipment and processes to ensure the quality and reliability of the finished board. Some key considerations include:
Copper Plating
To achieve the thick copper layers required for high current PCBs, the manufacturing process must include a plating step. The most common method is electroplating, where the board is immersed in a copper sulfate solution, and an electric current is applied to deposit copper onto the surface. The plating time and current density determine the final copper thickness.
Ensuring a uniform and consistent copper plating is crucial for high current PCBs. Variations in thickness can lead to localized heating and premature failure. The plating process must be carefully controlled and monitored to maintain the desired copper weight across the entire board.
Drilling and Routing
High current PCBs often require larger holes and wider spacing between traces to accommodate the increased copper thickness. This can present challenges for drilling and routing equipment, which may need to be specially adapted or calibrated.
Drilling thick copper boards requires high-speed steel (HSS) or carbide drill bits that can withstand the increased wear and tear. The drilling process must be optimized to prevent smearing or delamination of the copper layers.
Routing high current PCBs also demands more robust equipment and tooling. The routers must be able to handle the increased material thickness and copper weight without causing excessive burring or tearing. The routing paths must also be carefully designed to maintain the necessary clearances and avoid sharp corners that could concentrate current and cause hotspots.
Soldermask and Silkscreen
The soldermask and silkscreen layers on high current PCBs must be able to withstand the elevated temperatures and mechanical stresses associated with high power operation. Standard soldermask materials may not be suitable, and specialized formulations may be required.
The soldermask must also be applied in a thick enough layer to provide adequate insulation between the copper traces and prevent shorts or leakage currents. At the same time, the soldermask must not interfere with the thermal dissipation properties of the board or impede the attachment of heatsinks or other cooling devices.
The silkscreen layer, which provides component markings and other visual indicators, must also be robust and durable. The ink must be able to withstand high temperatures without fading or flaking off, and the markings must remain legible throughout the life of the board.
FAQ
What is the difference between a high current PCB and a standard PCB?
A high current PCB is designed to handle much higher electrical currents than a standard PCB. It uses thicker copper traces, wider trace widths, and specialized materials to manage the increased power levels and heat generation. Standard PCBs, on the other hand, are designed for signal-level currents and have thinner traces and smaller components.
How do I know if I need a high current PCB for my application?
If your application involves currents greater than a few amps, or if you are designing a power electronics system, you will likely need a high current PCB. Some examples include motor controllers, battery management systems, power supplies, and industrial automation equipment. If you are unsure, consult with a PCB design expert or manufacturer to determine the best solution for your needs.
Can I use standard PCB design software to create a high current PCB?
While most PCB design software packages can handle high current designs, they may not have all the specialized tools and libraries needed for optimal results. Look for software that includes features such as copper pour and plane design, thermal analysis, and high-current component libraries. Some popular options include Altium Designer, Cadence OrCAD, and Mentor Graphics PADS.
How much does a high current PCB cost compared to a standard PCB?
The cost of a high current PCB can be several times higher than a standard PCB, depending on the specific requirements. Factors that influence the cost include the copper weight, the number of layers, the size of the board, and the materials used. However, the added expense is often justified by the improved performance, reliability, and safety of the finished product.
What are some common mistakes to avoid when designing a high current PCB?
Some common mistakes to avoid include:
- Undersizing the copper traces or using insufficient copper weight for the expected current levels.
- Failing to provide adequate clearance between traces or between the board and enclosure.
- Neglecting thermal management, such as proper heatsinking and air flow.
- Not using appropriate decoupling capacitors or power supply filtering.
- Overlooking safety features such as fuses, circuit breakers, or over-current protection.
By following best practices and working with experienced PCB designers and manufacturers, these mistakes can be avoided, and a high-quality, reliable high current PCB can be produced.
Leave a Reply