Introduction to PCB Connectors
A printed circuit board (PCB) connector is an electromechanical component that facilitates the connection between a PCB and other devices, such as cables, wires, or other PCBs. These connectors play a crucial role in establishing reliable electrical and mechanical connections, enabling the transfer of power, signals, and data within an electronic system.
Types of PCB Connectors
There are various types of connectors used in PCB design, each serving specific purposes and applications. Some common types include:
-
Pin Headers: These are male connectors with a series of pins arranged in a row or matrix, often used for board-to-board or board-to-wire connections.
-
Socket Headers: Female counterparts to pin headers, these connectors have a series of sockets that accept the pins of a male connector.
-
Edge Connectors: These connectors are designed to mate with the edge of a PCB, where conductive pads or fingers are exposed. They are commonly used in expansion cards and modules.
-
Board-to-Board Connectors: These connectors are used to establish connections between two PCBs, either in a stacking or side-by-side configuration.
-
Wire-to-Board Connectors: These connectors facilitate the connection between wires or cables and a PCB. They can be in the form of screw terminals, crimp connectors, or IDC (insulation displacement connectors).
-
USB Connectors: Universal Serial Bus (USB) connectors are widely used for connecting peripherals, such as keyboards, mice, and storage devices, to a PCB.
-
RF Connectors: Radio Frequency (RF) connectors, such as SMA, BNC, and MMCX, are used for high-frequency signal transmission in wireless applications.
-
Power Connectors: These connectors are designed to handle higher currents and voltages, providing a means to supply power to a PCB from an external source.
PCB Connector Selection Criteria
When selecting a connector for a PCB, several factors need to be considered to ensure proper functionality, reliability, and compatibility. Some key selection criteria include:
1. Electrical Requirements
- Current Rating: The connector must be capable of handling the required current without overheating or suffering from excessive voltage drop.
- Voltage Rating: The connector should withstand the maximum voltage expected in the system, with an appropriate safety margin.
- Contact Resistance: Low contact resistance is essential for maintaining signal integrity and minimizing power loss.
- Insulation Resistance: High insulation resistance prevents leakage currents and ensures proper isolation between contacts.
2. Mechanical Requirements
- Mating Cycles: The connector should withstand the expected number of mating and unmating cycles without deterioration in performance.
- Insertion Force: The force required to mate the connector should be within acceptable limits for easy assembly and prevention of damage.
- Retention Force: Adequate retention force ensures a stable connection and prevents accidental disconnection.
- Vibration and Shock Resistance: The connector must withstand the expected levels of vibration and shock in the intended application.
3. Environmental Factors
- Operating Temperature Range: The connector should be suitable for the expected temperature range of the application.
- Humidity Resistance: Moisture-resistant materials and proper sealing prevent corrosion and maintain performance in humid environments.
- Chemical Resistance: The connector materials should withstand exposure to chemicals, solvents, and other substances present in the operating environment.
- Flammability Rating: For safety-critical applications, connectors with appropriate flammability ratings, such as UL94V-0, may be required.
4. PCB Layout Considerations
- Footprint Compatibility: The connector footprint must match the PCB layout, ensuring proper alignment and solderability.
- Clearance and Creepage: Sufficient clearance and creepage distances between contacts prevent electrical breakdown and maintain insulation integrity.
- Mounting Style: The connector mounting style (through-hole, surface-mount, or mixed) should be compatible with the PCB manufacturing process.
- Placement and Orientation: Connector placement and orientation should consider factors such as cable routing, accessibility, and assembly ergonomics.
5. Application-Specific Requirements
- Data Rate: For high-speed digital applications, connectors with appropriate bandwidth and signal integrity characteristics are essential.
- Shielding: In EMI/RFI-sensitive environments, shielded connectors may be necessary to prevent interference.
- Sealing: Waterproof or dustproof connectors are required in outdoor or harsh industrial environments.
- Compliance and Certifications: Connectors may need to meet specific industry standards or certifications, such as USB, HDMI, or automotive requirements.
Factor | Considerations |
---|---|
Electrical Requirements | Current rating, voltage rating, contact resistance, insulation resistance |
Mechanical Requirements | Mating cycles, insertion force, retention force, vibration and shock resistance |
Environmental Factors | Operating temperature range, humidity resistance, chemical resistance, flammability rating |
PCB Layout Considerations | Footprint compatibility, clearance and creepage, mounting style, placement and orientation |
Application-Specific Requirements | Data rate, shielding, sealing, compliance and certifications |
PCB Connector Materials and Plating
The choice of materials and plating for PCB connectors is crucial for ensuring reliable performance, durability, and compatibility with the PCB and mating components. Some common materials and plating options include:
1. Contact Materials
- Copper Alloys: Brass and phosphor bronze are widely used for their good electrical conductivity, mechanical strength, and corrosion resistance.
- Stainless Steel: Used in demanding applications requiring high strength and durability, but with lower conductivity compared to copper alloys.
- Beryllium Copper: Offers excellent spring properties, making it suitable for contacts that require frequent mating and unmating.
2. Insulator Materials
- Thermoplastics: Materials like nylon, polyester, and polypropylene are common choices for their good insulation properties, mechanical strength, and moldability.
- Thermosets: Phenolics, epoxies, and polyimides offer higher temperature resistance and dimensional stability compared to thermoplastics.
- Ceramics: Used in high-temperature or high-voltage applications, ceramics provide excellent insulation and thermal resistance.
3. Plating Options
- Gold: Gold plating provides excellent corrosion resistance, low contact resistance, and good solderability. It is often used for high-reliability and low-signal applications.
- Nickel: Nickel plating offers good wear resistance and acts as a barrier layer between the base metal and the final plating. It is commonly used as an underplate for gold.
- Silver: Silver plating has high conductivity and good corrosion resistance. It is used in some RF connectors and for contacts in high-current applications.
- Tin: Tin plating provides good solderability and is a cost-effective option for general-purpose connectors. However, it is prone to oxidation over time.
- Palladium-Nickel: This alloy plating combines the benefits of palladium’s low contact resistance and nickel’s wear resistance. It is a popular choice for high-reliability connectors.
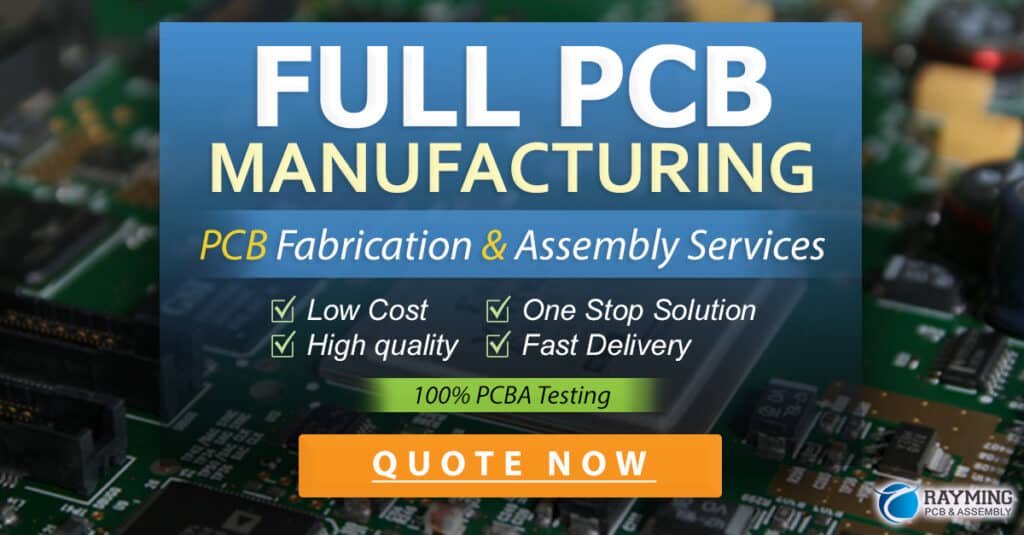
PCB Connector Termination Methods
The termination method refers to how the connector is attached to the PCB. The choice of termination method depends on factors such as the connector type, PCB manufacturing process, and application requirements. Some common termination methods include:
1. Through-Hole Mounting
Through-hole connectors have pins that are inserted into plated holes on the PCB and soldered in place. This method provides a strong mechanical connection and is suitable for connectors subjected to high stress or vibration.
2. Surface Mount Technology (SMT)
SMT connectors have terminations that are soldered directly onto pads on the surface of the PCB. This method enables smaller footprints, higher connection density, and compatibility with automated assembly processes.
3. Press-Fit
Press-fit connectors have compliant pins that are pressed into plated through-holes on the PCB, establishing a gas-tight connection without the need for soldering. This method is useful for high-volume production and applications where connectors may need to be replaced or serviced.
4. Compression Mount
Compression mount connectors use a clamping mechanism to hold the connector in place on the PCB. The connector is compressed against pads on the PCB surface, establishing an electrical connection without soldering. This method allows for easy removal and replacement of connectors.
5. Wire Bonding
Wire bonding is used for connecting fine wires directly to pads on the PCB. This method is commonly used in high-frequency applications and for connecting chip-scale packages to the PCB.
Termination Method | Advantages | Disadvantages |
---|---|---|
Through-Hole | Strong mechanical connection, suitable for high stress or vibration | Larger footprint, less compatible with automated assembly |
Surface Mount | Smaller footprint, higher connection density, compatible with automated assembly | Limited mechanical strength compared to through-hole |
Press-Fit | Gas-tight connection without soldering, suitable for high-volume production | Requires precise hole dimensions and plating quality |
Compression Mount | Easy removal and replacement of connectors | May require additional mechanical support |
Wire Bonding | Suitable for high-frequency applications and chip-scale packages | Limited to fine wire connections, requires specialized equipment |
PCB Connector Standards and Specifications
Various standards and specifications govern the design, performance, and compatibility of PCB connectors. These standards ensure interoperability between connectors from different manufacturers and provide guidelines for product safety and reliability. Some notable standards and specifications include:
1. IEC 60603-2
This standard series defines the mechanical, electrical, and environmental requirements for connectors used in electronic equipment. It covers various connector types, including D-subminiature, rectangular, and circular connectors.
2. USB (Universal Serial Bus)
USB specifications define the requirements for USB connectors and cables, ensuring compatibility between USB devices from different manufacturers. The most common USB connector types are USB Type-A, Type-B, Mini-USB, Micro-USB, and USB Type-C.
3. HDMI (High-Definition Multimedia Interface)
HDMI specifications define the requirements for HDMI connectors and cables used for transmitting digital video and audio signals. The standard covers mechanical, electrical, and signal integrity aspects of HDMI connectors.
4. PCI Express (PCIe)
PCIe specifications define the requirements for edge connectors used in PCIe expansion cards and slots. The standard covers mechanical, electrical, and signal integrity aspects of PCIe connectors.
5. SATA (Serial ATA)
SATA specifications define the requirements for connectors used in SATA storage devices and motherboards. The standard covers mechanical, electrical, and signal integrity aspects of SATA connectors.
6. IEEE 1394 (FireWire)
IEEE 1394 specifications define the requirements for FireWire connectors and cables used for high-speed serial communication. The standard covers mechanical, electrical, and protocol aspects of FireWire connectors.
7. MIL-DTL-38999
This military specification defines the requirements for circular connectors used in harsh environments, such as aerospace and defense applications. The standard covers mechanical, electrical, and environmental aspects of these connectors.
PCB Connector Reliability and Testing
Ensuring the reliability of PCB connectors is essential for the overall reliability of the electronic system. Connector failures can lead to system malfunctions, downtime, and costly repairs. To ensure connector reliability, various tests and qualification processes are performed, including:
1. Mechanical Tests
- Mating and Unmating Force: Measures the force required to mate and unmate the connector, ensuring it is within specified limits.
- Durability: Evaluates the connector’s ability to withstand repeated mating and unmating cycles without degradation in performance.
- Vibration and Shock: Assesses the connector’s resistance to mechanical stress caused by vibration and shock.
2. Electrical Tests
- Contact Resistance: Measures the electrical resistance of the connector contacts, ensuring low and stable values.
- Insulation Resistance: Verifies the integrity of the insulation between connector contacts and between contacts and the shell.
- Current Carrying Capacity: Determines the maximum current the connector can handle without overheating or degradation.
- Voltage Breakdown: Tests the connector’s ability to withstand high voltages without dielectric breakdown.
3. Environmental Tests
- Temperature Cycling: Exposes the connector to alternating high and low temperatures to evaluate its performance under thermal stress.
- Humidity: Assesses the connector’s resistance to moisture and corrosion under high humidity conditions.
- Salt Spray: Evaluates the connector’s corrosion resistance when exposed to a salt spray environment.
- Flammability: Tests the connector’s resistance to ignition and flame spread, particularly for applications with stringent safety requirements.
4. Signal Integrity Tests
- Impedance: Measures the connector’s characteristic impedance to ensure proper matching with the PCB and cable.
- Insertion Loss: Evaluates the signal attenuation caused by the connector across the frequency range of interest.
- Return Loss: Assesses the amount of signal reflections caused by impedance mismatches at the connector interface.
- Crosstalk: Measures the undesired coupling of signals between adjacent connector contacts.
By conducting these tests and ensuring compliance with relevant standards and specifications, manufacturers can provide reliable and high-quality PCB connectors for various applications.
Frequently Asked Questions (FAQ)
1. What is the difference between a header and a socket?
A header is a male connector with pins that protrude from the connector body, while a socket is a female connector with receptacles that accept the pins of a mating header. Headers and sockets are often used in pairs to establish a connection between two parts of a system.
2. Can I use a through-hole connector on a surface-mount PCB?
Yes, it is possible to use a through-hole connector on a surface-mount PCB by designing the PCB with plated through-holes for the connector pins. However, this approach may require additional manual assembly steps and may not be as space-efficient as using a surface-mount connector.
3. How do I choose the right connector for my application?
Choosing the right connector involves considering various factors such as the electrical requirements (current, voltage, and signal integrity), mechanical requirements (mating cycles, insertion force, and retention force), environmental factors (temperature, humidity, and chemical resistance), PCB layout considerations, and application-specific requirements (data rate, shielding, and sealing).
4. What is the purpose of gold plating on connector contacts?
Gold plating on connector contacts provides several benefits, including excellent corrosion resistance, low contact resistance, and good solderability. Gold-plated contacts are often used in high-reliability and low-signal applications where stable and reliable connections are critical.
5. How can I ensure the reliability of PCB connectors in my design?
To ensure the reliability of PCB connectors, consider the following practices:
– Select connectors that meet the electrical, mechanical, and environmental requirements of your application.
– Follow the manufacturer’s recommendations for PCB layout, including footprint design, hole size, and pad dimensions.
– Use appropriate termination methods, such as through-hole or surface-mount, based on the connector type and application requirements.
– Perform thorough testing and qualification, including mechanical, electrical, environmental, and signal integrity tests, to verify connector performance and reliability.
– Ensure proper handling, storage, and assembly procedures to prevent damage to the connectors during manufacturing and installation.
By understanding the types, selection criteria, materials, termination methods, standards, and testing requirements for PCB connectors, designers can make informed decisions and create reliable and high-performance electronic systems.
Leave a Reply