Introduction to PCB BOM
In the world of printed circuit board (PCB) design, the term “BOM” is frequently used. BOM stands for “Bill of Materials,” and it is a crucial document that lists all the components required to manufacture a PCB. A well-prepared BOM ensures smooth communication between the PCB designer, the procurement team, and the manufacturing facility. In this article, we will dive deep into the concept of BOM in PCB design, its importance, and best practices for creating an effective BOM.
What is a PCB BOM?
A PCB BOM is a comprehensive list of all the components, materials, and quantities needed to assemble a printed circuit board. It includes every item that goes into the construction of the PCB, from the raw PCB substrate to the smallest resistor or capacitor. The BOM acts as a blueprint for the procurement team to source the necessary components and for the manufacturing team to assemble the PCB accurately.
Why is a PCB BOM Important?
A well-prepared PCB BOM is essential for several reasons:
-
Accurate Procurement: The BOM provides a clear list of components required, enabling the procurement team to source the correct parts in the right quantities. This helps avoid delays due to missing or incorrect components.
-
Cost Estimation: By listing all the components and their quantities, the BOM allows for accurate cost estimation of the PCB project. This information is crucial for budgeting and pricing decisions.
-
Efficient Manufacturing: The manufacturing team relies on the BOM to assemble the PCB correctly. A detailed and accurate BOM minimizes the chances of assembly errors and ensures a smooth production process.
-
Revision Control: As PCB designs evolve, the BOM helps track changes in components and quantities between different versions of the board. This is important for maintaining proper documentation and revision control.
Elements of a PCB BOM
A typical PCB BOM includes several key elements that provide comprehensive information about the components used in the PCB design. Let’s explore these elements in detail:
1. Item Number
Each component in the BOM is assigned a unique item number or reference designator. This number serves as an identifier for the component and helps in cross-referencing the BOM with the schematic and PCB layout. Examples of item numbers include R1 for a resistor, C1 for a capacitor, and U1 for an integrated circuit.
2. Quantity
The quantity column in the BOM specifies the number of each component required for a single PCB assembly. It is essential to ensure that the quantities are accurate to avoid shortages or excess inventory during the manufacturing process.
3. Manufacturer Part Number (MPN)
The manufacturer part number (MPN) is a unique identifier assigned by the component manufacturer to a specific part. It provides precise information about the component, including its specifications, package type, and tolerance. Including the MPN in the BOM ensures that the correct components are procured and used in the PCB assembly.
4. Description
The description column provides additional information about each component, such as its value, package type, and any special characteristics. For example, a resistor’s description might include its resistance value and tolerance, while a capacitor’s description might specify its capacitance and voltage rating.
5. Manufacturer
The manufacturer column lists the name of the company that produces each component. This information is important for sourcing components and ensuring compatibility between different parts.
6. Supplier and Supplier Part Number
In addition to the manufacturer information, the BOM often includes details about the preferred supplier for each component. The supplier part number is the unique identifier assigned by the supplier to the component, which may differ from the manufacturer part number. Including supplier information in the BOM helps streamline the procurement process and ensures consistent sourcing.
7. Reference Designator
The reference designator column links each component in the BOM to its corresponding symbol on the schematic and footprint on the PCB layout. This information is crucial for assembling the PCB correctly and troubleshooting any issues that may arise during the manufacturing process.
BOM Management Best Practices
Creating and managing a PCB BOM requires attention to detail and adherence to best practices. Here are some guidelines to follow:
1. Standardize the BOM Format
Establish a standardized format for your BOM that includes all the necessary columns and information. Use consistent naming conventions and terminology throughout the BOM to avoid confusion and errors.
2. Use Automated BOM Generation Tools
Many PCB design software packages include tools for automatically generating BOMs based on the schematic and PCB layout. These tools help ensure accuracy and consistency, reducing the chances of manual errors.
3. Review and Validate the BOM
Before finalizing the BOM, carefully review and validate the information. Cross-check the BOM against the schematic and PCB layout to ensure that all components are accounted for and that the quantities and reference designators are correct.
4. Include Alternate Components
In some cases, it may be beneficial to include alternate components in the BOM. This can be useful if the primary component is out of stock or if a cheaper alternative is available. Clearly indicate any alternate components and ensure that they meet the necessary specifications.
5. Maintain Revision Control
As the PCB design evolves, keep track of changes to the BOM. Use revision numbers or dates to distinguish between different versions of the BOM and maintain a history of the changes made. This helps in tracking updates and ensures that the correct version of the BOM is used for production.
6. Collaborate with Stakeholders
Involve relevant stakeholders, such as the procurement team and manufacturing partners, in the BOM creation and review process. Their input can help identify potential issues and optimize the BOM for efficient procurement and manufacturing.
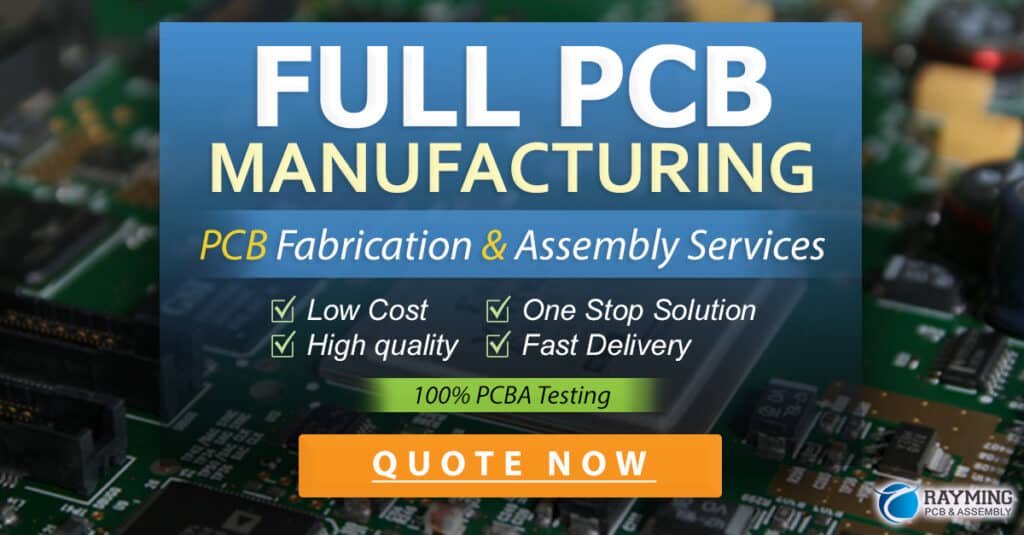
PCB BOM Example
To illustrate the structure and content of a PCB BOM, let’s consider an example. Suppose we have a simple LED blinking circuit that consists of an Arduino Uno microcontroller, an LED, a resistor, and some connectors. The BOM for this project might look like this:
Item | Qty | Manufacturer Part Number | Description | Manufacturer | Supplier | Supplier Part Number | Reference Designator |
---|---|---|---|---|---|---|---|
1 | 1 | A000066 | Arduino Uno – R3 SMD | Arduino | Digi-Key | 1050-1024-ND | U1 |
2 | 1 | TLHG5400 | LED – SMD Green 574nm | Vishay | Mouser | 78-TLHG5400 | LED1 |
3 | 1 | ERJ-6GEYJ103V | RES SMD 10K OHM 5% 1/8W 0805 | Panasonic | Digi-Key | P10KACT-ND | R1 |
4 | 2 | 0022232041 | CONN HEADER VERT 4POS 2.54MM | Molex | Mouser | 538-22-23-2041 | J1, J2 |
This example BOM provides all the necessary information for procuring the components and assembling the PCB. It includes the item numbers, quantities, manufacturer part numbers, descriptions, manufacturers, suppliers, supplier part numbers, and reference designators.
Frequently Asked Questions (FAQ)
-
What is the difference between a PCB BOM and a schematic?
A PCB BOM is a list of all the components required to manufacture a PCB, while a schematic is a graphical representation of the circuit diagram, showing how the components are connected. The BOM provides the component details, quantities, and sourcing information, while the schematic focuses on the electrical connections and functionality of the circuit. -
Can I use generic components instead of the specific ones listed in the BOM?
It is generally recommended to use the exact components specified in the BOM to ensure compatibility and performance. However, in some cases, generic equivalents or alternate components may be used if they meet the required specifications and have been approved by the design team. -
How do I handle components that are obsolete or out of stock?
If a component in the BOM becomes obsolete or is out of stock, it is important to find a suitable replacement. Work with the design team and suppliers to identify alternative components that meet the necessary specifications. Update the BOM accordingly and communicate the changes to all relevant stakeholders. -
What should I do if I find discrepancies in the BOM during the assembly process?
If you encounter discrepancies in the BOM during PCB assembly, such as missing or incorrect components, notify the design team and the procurement team immediately. They will investigate the issue and provide guidance on how to proceed. It may be necessary to update the BOM and re-source the affected components. -
How often should I review and update the PCB BOM?
It is good practice to review and update the PCB BOM regularly, especially when changes are made to the design or when components become obsolete. Establish a process for periodically reviewing the BOM, incorporating feedback from the manufacturing and procurement teams, and making necessary updates. This helps ensure that the BOM remains accurate and up to date throughout the product lifecycle.
Conclusion
A well-prepared PCB BOM is a critical document in the PCB design and manufacturing process. It provides a comprehensive list of all the components required to assemble the PCB, enabling accurate procurement, cost estimation, and efficient manufacturing. By understanding the elements of a BOM and following best practices for BOM management, PCB designers can ensure smooth communication and collaboration with procurement and manufacturing teams.
When creating a PCB BOM, it is essential to include detailed information such as item numbers, quantities, manufacturer part numbers, descriptions, manufacturers, suppliers, and reference designators. Using standardized formats, automated BOM generation tools, and maintaining revision control helps minimize errors and streamline the process.
By paying close attention to the BOM and involving relevant stakeholders in its creation and review, PCB designers can optimize the design for manufacturability and avoid potential issues during production. A well-managed BOM is a key factor in the success of any PCB project, ensuring timely delivery, cost-effectiveness, and high-quality results.
Leave a Reply