Introduction to PCB Cleaning
Printed Circuit Boards (PCBs) are essential components in modern electronics. They are used in a wide range of applications, from simple devices like calculators to complex systems such as computers and smartphones. PCBs are made up of conductive tracks, pads, and other features etched from copper sheets laminated onto a non-conductive substrate. During the manufacturing process and subsequent handling, PCBs can accumulate contaminants such as dust, dirt, grease, and flux residues. These contaminants can adversely affect the performance and reliability of the PCB, leading to malfunctions or even complete failure of the electronic device. Therefore, it is crucial to clean PCBs properly to ensure their optimal functionality and longevity.
Why Is PCB Cleaning Important?
PCB cleaning is important for several reasons:
-
Removing contaminants: Cleaning helps remove contaminants such as dust, dirt, grease, and flux residues that can accumulate on the PCB during manufacturing and handling.
-
Improving performance: Contaminants can interfere with the electrical properties of the PCB, leading to poor performance or even failure of the electronic device. Cleaning ensures optimal functionality of the PCB.
-
Enhancing reliability: A clean PCB is less likely to experience malfunctions or failures, thus improving the overall reliability of the electronic device.
-
Extending lifespan: Regular cleaning can help extend the lifespan of the PCB by preventing the buildup of contaminants that can cause corrosion or other damage over time.
Common Contaminants Found on PCBs
PCBs can accumulate various types of contaminants, including:
-
Dust and dirt: These can settle on the PCB during manufacturing, storage, or handling.
-
Grease and oils: These can come from human handling or from the manufacturing process itself.
-
Flux residues: Flux is used during the soldering process to prevent oxidation and improve solder joint quality. However, flux residues can be corrosive and conductive, leading to problems if not removed.
-
Solder balls and splashes: These can occur during the soldering process and can cause short circuits if not removed.
-
Fingerprints: Human handling can leave fingerprints on the PCB, which can contain oils and other contaminants.
PCB Cleaning Methods
There are several methods for cleaning PCBs, each with its own advantages and disadvantages. The choice of cleaning method depends on factors such as the type of contaminants present, the size and complexity of the PCB, and the available resources. Here are some common PCB cleaning methods:
Manual Cleaning
Manual cleaning involves using hand tools and cleaning agents to remove contaminants from the PCB. This method is suitable for small-scale cleaning or for hard-to-reach areas on the PCB. Common manual cleaning tools include:
-
Brushes: Soft-bristled brushes can be used to gently scrub away contaminants from the PCB surface.
-
Swabs: Cotton or foam swabs can be used to apply cleaning agents and remove contaminants from tight spaces or delicate components.
-
Tweezers: Tweezers can be used to pick up and remove larger contaminants such as solder balls or splashes.
Manual cleaning agents include:
-
Isopropyl alcohol (IPA): IPA is a common solvent used for cleaning PCBs. It is effective at dissolving oils, greases, and flux residues.
-
Deionized water: Deionized water can be used to rinse away cleaning agents and contaminants without leaving mineral deposits on the PCB.
-
Specialized cleaning solutions: There are various commercial cleaning solutions specifically designed for PCB cleaning, such as flux removers and contact cleaners.
Ultrasonic Cleaning
Ultrasonic cleaning uses high-frequency sound waves to agitate a cleaning solution, creating tiny bubbles that implode and generate a scrubbing action on the PCB surface. This method is effective at removing stubborn contaminants and can clean hard-to-reach areas. The process involves:
-
Placing the PCB in a tank filled with a cleaning solution (usually a mixture of water and a specialized cleaning agent).
-
Applying ultrasonic energy to the tank, which causes the cleaning solution to cavitate and scrub the PCB surface.
-
Rinsing the PCB with deionized water to remove any remaining cleaning solution and contaminants.
-
Drying the PCB using compressed air or a low-temperature oven.
Advantages of ultrasonic cleaning include:
- Thorough cleaning of hard-to-reach areas
- Reduced cleaning time compared to manual methods
- Consistent cleaning results
Disadvantages include:
- Higher equipment costs
- Potential damage to delicate components due to high-frequency vibrations
Spray Cleaning
Spray cleaning involves using a pressurized spray of cleaning solution to remove contaminants from the PCB surface. This method is suitable for larger PCBs or batch cleaning. The process involves:
-
Placing the PCB in a spray cleaning machine or using a handheld spray device.
-
Applying a pressurized spray of cleaning solution (usually a mixture of water and a specialized cleaning agent) to the PCB surface.
-
Allowing the cleaning solution to dissolve and remove contaminants.
-
Rinsing the PCB with deionized water to remove any remaining cleaning solution and contaminants.
-
Drying the PCB using compressed air or a low-temperature oven.
Advantages of spray cleaning include:
- Fast cleaning of large PCBs or batches
- Consistent cleaning results
- Reduced manual labor
Disadvantages include:
- Higher equipment costs
- Potential for overspray and contamination of surrounding areas
Vapor Degreasing
Vapor degreasing is a cleaning method that uses the vapors of a solvent to clean the PCB. The process involves:
-
Placing the PCB in a vapor degreasing machine, which consists of a tank filled with a solvent (usually a specialized cleaning agent) and a heating element.
-
Heating the solvent until it vaporizes and forms a dense vapor layer above the liquid solvent.
-
Lowering the PCB into the vapor layer, where the solvent vapors condense on the PCB surface and dissolve contaminants.
-
Raising the PCB out of the vapor layer, allowing the solvent to evaporate and leaving a clean PCB surface.
Advantages of vapor degreasing include:
- Thorough cleaning of hard-to-reach areas
- Fast cleaning process
- Minimal manual labor
Disadvantages include:
- Higher equipment costs
- Potential health and environmental hazards associated with solvent vapors
- Strict regulations on the use of certain solvents
Choosing the Right Cleaning Agent
Selecting the appropriate cleaning agent is crucial for effective PCB cleaning. The ideal cleaning agent should:
- Effectively remove the specific contaminants present on the PCB
- Be compatible with the PCB materials and components
- Be safe for the environment and the user
- Be cost-effective
Here are some common cleaning agents used for PCB cleaning:
Isopropyl Alcohol (IPA)
IPA is a widely used solvent for PCB cleaning due to its effectiveness in dissolving oils, greases, and flux residues. It is relatively safe, inexpensive, and evaporates quickly, leaving no residue. However, IPA can be flammable and may not be suitable for certain plastics or rubber components.
Deionized Water
Deionized water is used for rinsing PCBs after cleaning with other agents. It helps remove any remaining contaminants or cleaning solution without leaving mineral deposits on the PCB surface. Deionized water is safe and environmentally friendly but may not be effective at dissolving certain contaminants on its own.
Specialized Cleaning Solutions
There are various commercial cleaning solutions designed specifically for PCB cleaning, such as:
-
Flux removers: These solutions are formulated to dissolve and remove flux residues from PCBs. They are available in both solvent-based and water-based formulations.
-
Contact cleaners: These solutions are designed to clean and protect electrical contacts on PCBs. They help remove oxidation, corrosion, and other contaminants that can interfere with electrical conductivity.
-
Aqueous cleaners: These are water-based cleaning solutions that contain surfactants and other additives to help remove contaminants. They are generally safer and more environmentally friendly than solvent-based cleaners.
When choosing a specialized cleaning solution, it is essential to consider factors such as:
- Compatibility with the specific contaminants and PCB materials
- Environmental and safety regulations
- Cost and availability
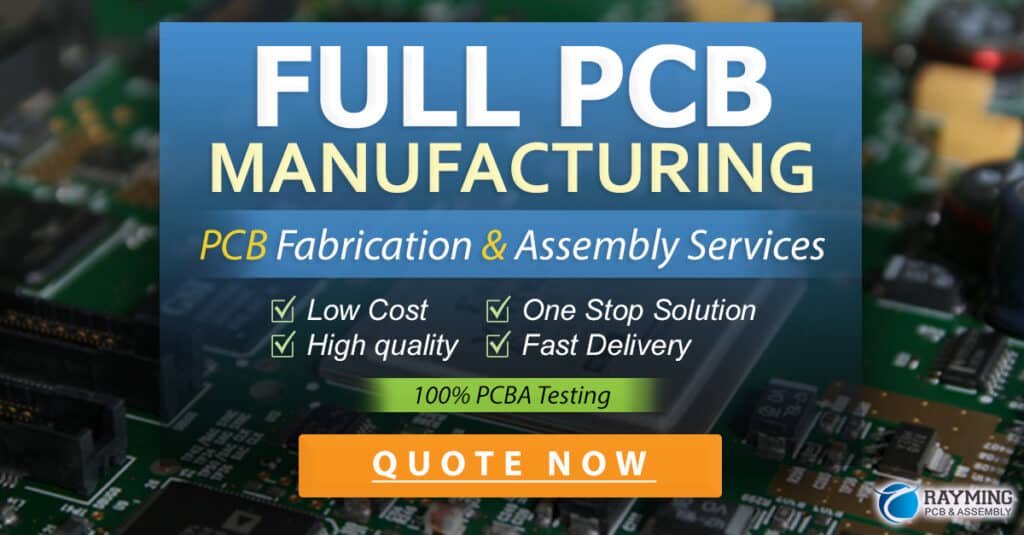
PCB Cleaning Procedure
A typical PCB cleaning procedure involves the following steps:
-
Preparation: Ensure that the PCB is powered off and disconnected from any power sources. Remove any loose debris or large contaminants using tweezers or a soft-bristled brush.
-
Cleaning: Apply the chosen cleaning method (manual, ultrasonic, spray, or vapor degreasing) using the appropriate cleaning agent. Follow the manufacturer’s instructions for the specific cleaning equipment and solutions used.
-
Rinsing: Rinse the PCB thoroughly with deionized water to remove any remaining cleaning solution and contaminants. Ensure that all areas of the PCB are rinsed, including hard-to-reach spaces.
-
Drying: Use compressed air or a low-temperature oven to dry the PCB completely. Ensure that there is no moisture left on the PCB surface, as this can lead to corrosion or other issues.
-
Inspection: Visually inspect the PCB for any remaining contaminants or damage. Use a magnifying glass or microscope for a more thorough inspection if necessary.
-
Reassembly: Once the PCB is clean and dry, reassemble the electronic device, taking care not to introduce any new contaminants during the process.
Best Practices for PCB Cleaning
To ensure the best results when cleaning PCBs, follow these best practices:
-
Wear proper protective equipment: Always wear gloves, safety glasses, and a lab coat or apron when handling cleaning agents and PCBs. Some cleaning agents may be harmful if inhaled or come into contact with skin.
-
Work in a well-ventilated area: Many cleaning agents contain volatile organic compounds (VOCs) that can be harmful if inhaled in high concentrations. Ensure that the work area is well-ventilated to minimize exposure.
-
Follow manufacturer’s instructions: Always read and follow the manufacturer’s instructions for the specific cleaning equipment and solutions used. Improper use can lead to damage to the PCB or ineffective cleaning.
-
Use the least aggressive method: Start with the least aggressive cleaning method and progress to more aggressive methods only if necessary. This helps minimize the risk of damage to the PCB and its components.
-
Avoid over-cleaning: Excessive cleaning can damage the PCB or its components. Clean only as much as necessary to remove contaminants and ensure optimal performance.
-
Store PCBs properly: After cleaning, store PCBs in a clean, dry, and static-free environment to prevent recontamination or damage.
Frequently Asked Questions (FAQ)
-
What is the best cleaning agent for removing flux residues from PCBs?
Specialized flux removers are the most effective cleaning agents for removing flux residues from PCBs. These solutions are formulated specifically to dissolve and remove the types of flux commonly used in electronics manufacturing. Isopropyl alcohol (IPA) can also be effective at removing flux residues, but it may not be as thorough as a dedicated flux remover. -
Can I use household cleaners to clean my PCB?
It is not recommended to use household cleaners for PCB cleaning, as they may contain chemicals that can damage the PCB or its components. Additionally, household cleaners may not be effective at removing the specific contaminants found on PCBs. Always use cleaning agents designed specifically for PCB cleaning to ensure the best results and minimize the risk of damage. -
How often should I clean my PCB?
The frequency of PCB cleaning depends on factors such as the environment in which the PCB is used, the type of contaminants present, and the performance requirements of the electronic device. In general, it is a good practice to clean PCBs whenever they are visibly dirty or when the device experiences performance issues that may be related to contamination. For critical applications, regular preventive maintenance cleaning may be necessary to ensure optimal performance and reliability. -
Can I use compressed air to dry my PCB after cleaning?
Yes, compressed air can be used to dry PCBs after cleaning. However, ensure that the compressed air is clean, dry, and free of oil or other contaminants that could harm the PCB. Additionally, be careful not to use excessive air pressure, as this can damage delicate components on the PCB. If available, a low-temperature oven is a more controlled and gentle method for drying PCBs. -
What should I do if my PCB is still not working properly after cleaning?
If your PCB is still not working properly after cleaning, there may be other issues beyond contamination. First, visually inspect the PCB for any signs of damage, such as cracked or burned components, loose connections, or corroded traces. If no visible damage is found, consider seeking the assistance of a professional electronics repair service to diagnose and resolve the issue. In some cases, the PCB may be beyond repair and require replacement.
Conclusion
Proper cleaning is essential for maintaining the performance, reliability, and longevity of PCBs in electronic devices. Contaminants such as dust, dirt, grease, and flux residues can interfere with the electrical properties of the PCB and lead to malfunctions or failures. There are several methods for cleaning PCBs, including manual cleaning, ultrasonic cleaning, spray cleaning, and vapor degreasing. The choice of cleaning method depends on factors such as the type of contaminants present, the size and complexity of the PCB, and the available resources.
Selecting the appropriate cleaning agent is also crucial for effective PCB cleaning. Isopropyl alcohol (IPA), deionized water, and specialized cleaning solutions such as flux removers and contact cleaners are commonly used. When choosing a cleaning agent, consider factors such as compatibility with the specific contaminants and PCB materials, environmental and safety regulations, and cost-effectiveness.
To ensure the best results when cleaning PCBs, follow best practices such as wearing proper protective equipment, working in a well-ventilated area, following manufacturer’s instructions, using the least aggressive cleaning method, avoiding over-cleaning, and storing PCBs properly after cleaning. By implementing a regular and thorough PCB cleaning process, you can help ensure the optimal performance and longevity of your electronic devices.
Leave a Reply