Types of PCB Makers
Before diving into specific companies, it’s essential to understand the different types of PCB makers:
1. Captive PCB Manufacturers
Captive PCB manufacturers are in-house divisions of larger electronics companies. These manufacturers primarily produce PCBs for their parent company’s products and are not typically available for outside contracts. Examples include:
- Intel
- Samsung
- Apple
2. Contract PCB Manufacturers
Contract PCB manufacturers, also known as electronic manufacturing services (EMS) providers, offer PCB fabrication services to a variety of clients. These companies often provide additional services such as component sourcing, assembly, and testing. Some notable contract PCB makers include:
- Foxconn
- Jabil
- Flextronics
3. Specialty PCB Manufacturers
Specialty PCB manufacturers focus on producing boards for specific industries or applications that require unique materials, designs, or certifications. Examples include:
- TTM Technologies (aerospace and defense)
- Sanmina (medical devices)
- Zhen Ding Technology (flexible and rigid-flex PCBs)
Top PCB Makers Worldwide
1. Nippon Mektron
Headquarters: Japan
Founded: 1969
Employees: 10,000+
Revenue: $3.5 billion (2020)
Nippon Mektron is a leading Japanese PCB manufacturer specializing in flexible printed circuits (FPCs) and rigid-flex PCBs. The company serves a wide range of industries, including automotive, consumer electronics, and medical devices.
2. Unimicron
Headquarters: Taiwan
Founded: 1990
Employees: 30,000+
Revenue: $3.2 billion (2020)
Unimicron is a Taiwanese PCB maker that offers a comprehensive range of PCB products, including HDI, rigid-flex, and substrate-like PCBs. The company has manufacturing facilities in Taiwan, China, and Germany, serving customers in the consumer electronics, automotive, and telecommunications sectors.
3. Ibiden
Headquarters: Japan
Founded: 1912
Employees: 15,000+
Revenue: $3.1 billion (2020)
Ibiden is a Japanese company that specializes in high-end PCBs for the automotive, ICT, and industrial sectors. The company is known for its advanced packaging solutions, such as anylayer HDI and copper coin technology.
4. Zhen Ding Technology
Headquarters: Taiwan
Founded: 1996
Employees: 40,000+
Revenue: $2.8 billion (2020)
Zhen Ding Technology (ZDT) is a leading Taiwanese PCB manufacturer specializing in flexible and rigid-flex PCBs. The company serves a diverse range of industries, including consumer electronics, automotive, and medical devices. ZDT has manufacturing facilities in Taiwan and China.
5. TTM Technologies
Headquarters: United States
Founded: 1998
Employees: 25,000+
Revenue: $2.1 billion (2020)
TTM Technologies is a leading American PCB manufacturer with a strong presence in the aerospace, defense, and automotive industries. The company offers a wide range of PCB technologies, including HDI, rigid-flex, and RF/microwave pcbs. TTM has manufacturing facilities in North America, Europe, and Asia.
Comparison of PCB Makers
Company | Headquarters | Founded | Employees | Revenue (2020) | Specialization |
---|---|---|---|---|---|
Nippon Mektron | Japan | 1969 | 10,000+ | $3.5 billion | Flexible and rigid-flex PCBs |
Unimicron | Taiwan | 1990 | 30,000+ | $3.2 billion | HDI, rigid-flex, and substrate-like PCBs |
Ibiden | Japan | 1912 | 15,000+ | $3.1 billion | High-end PCBs for automotive, ICT, and industrial sectors |
Zhen Ding Technology | Taiwan | 1996 | 40,000+ | $2.8 billion | Flexible and rigid-flex PCBs |
TTM Technologies | United States | 1998 | 25,000+ | $2.1 billion | HDI, rigid-flex, and RF/microwave PCBs |
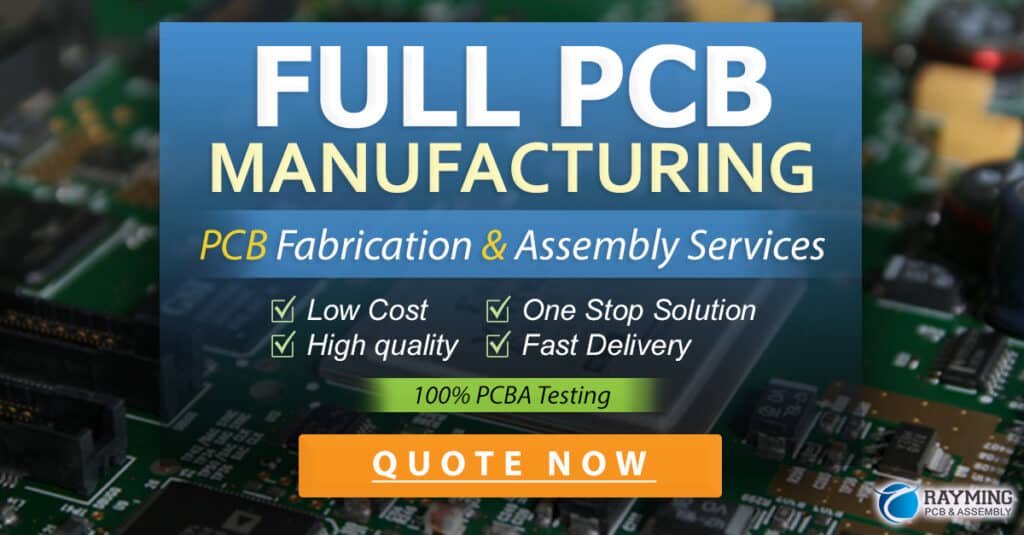
Factors to Consider When Choosing a PCB Maker
When selecting a PCB manufacturer, there are several key factors to consider:
1. Technical Capabilities
Ensure that the PCB maker has the necessary technical capabilities to produce your desired PCB type, such as HDI, flexible, or rigid-flex. Consider their experience with specific materials, design rules, and manufacturing processes.
2. Quality and Certifications
Look for PCB manufacturers with robust quality control systems and relevant certifications, such as ISO 9001, ISO 14001, and industry-specific certifications like AS9100 for aerospace or IATF 16949 for automotive.
3. Production Capacity and Lead Times
Assess the PCB maker’s production capacity and their ability to meet your volume requirements and desired lead times. Consider their flexibility in handling both small and large-scale orders.
4. Cost and Value
While cost is an important consideration, it should be balanced with the value provided by the PCB manufacturer. Consider factors such as quality, reliability, and additional services offered, such as design support or logistics management.
5. Location and Supply Chain
The location of the PCB manufacturer can impact lead times, shipping costs, and communication. Consider the stability and resilience of their supply chain, as well as their ability to source components and materials reliably.
Future Trends in PCB Manufacturing
As technology advances and market demands evolve, PCB makers must adapt to stay competitive. Some key trends shaping the future of PCB manufacturing include:
1. Miniaturization and High Density Interconnect (HDI)
The trend towards smaller, more compact electronic devices is driving the demand for miniaturized PCBs with higher component density. HDI technology, which involves the use of micro vias and fine pitch traces, enables the production of highly compact and complex PCBs.
2. Flexible and Rigid-Flex PCBs
Flexible and rigid-flex PCBs are gaining popularity due to their ability to conform to unique device shapes and withstand repeated flexing. These PCBs are particularly useful in wearable electronics, medical devices, and automotive applications.
3. Environmentally Friendly Materials and Processes
As sustainability becomes a growing concern, PCB manufacturers are adopting eco-friendly materials and processes. This includes the use of halogen-free laminates, lead-free solders, and green manufacturing practices that minimize waste and energy consumption.
4. Industry 4.0 and Automation
The integration of Industry 4.0 technologies, such as artificial intelligence, machine learning, and the Internet of Things (IoT), is transforming PCB manufacturing. Automated production lines, real-time process monitoring, and predictive maintenance are enabling PCB makers to improve efficiency, quality, and flexibility.
Frequently Asked Questions (FAQ)
1. What is the difference between a captive and contract PCB manufacturer?
A captive PCB manufacturer is an in-house division of a larger electronics company that primarily produces PCBs for its parent company’s products. In contrast, a contract PCB manufacturer offers PCB fabrication services to a variety of clients and is not tied to a single company.
2. What are the advantages of using a specialty PCB manufacturer?
Specialty PCB manufacturers have expertise in producing boards for specific industries or applications that require unique materials, designs, or certifications. By working with a specialty PCB maker, you can benefit from their specialized knowledge, ensuring that your PCBs meet the specific requirements of your industry or application.
3. How do I choose the right PCB manufacturer for my project?
When choosing a PCB manufacturer, consider factors such as their technical capabilities, quality and certifications, production capacity and lead times, cost and value, and location and supply chain. Evaluate your specific project requirements and select a PCB maker that aligns with your needs and priorities.
4. What are HDI PCBs, and why are they becoming more popular?
HDI (High Density Interconnect) PCBs are boards with higher component density, achieved through the use of micro vias and fine pitch traces. HDI PCBs are becoming more popular due to the trend towards miniaturization in electronic devices, as they enable the production of highly compact and complex PCBs.
5. Are there eco-friendly options for PCB manufacturing?
Yes, many PCB manufacturers are adopting environmentally friendly materials and processes, such as halogen-free laminates, lead-free solders, and green manufacturing practices that minimize waste and energy consumption. When selecting a PCB maker, you can inquire about their sustainability initiatives and choose a company that aligns with your environmental goals.
Conclusion
PCB makers play a crucial role in the electronics industry, providing the foundation for the devices and systems that shape our modern world. From captive and contract manufacturers to specialty PCB makers, there is a wide range of companies offering PCB fabrication services. When selecting a PCB manufacturer, it’s essential to consider factors such as technical capabilities, quality, production capacity, cost, and location to ensure that you find the right partner for your project.
As technology continues to evolve, PCB makers must adapt to new trends and challenges, such as miniaturization, flexible and rigid-flex PCBs, environmentally friendly materials, and the integration of Industry 4.0 technologies. By staying at the forefront of these developments, PCB manufacturers can continue to support innovation and growth in the electronics industry.
Leave a Reply