Introduction to Ceramic PCB
Ceramic printed circuit boards (PCBs) are a type of substrate material used in the manufacturing of electronic circuits. Unlike traditional PCBs that use FR4 or other organic materials, ceramic PCBs utilize a ceramic substrate, which offers unique properties and advantages in certain applications. Ceramic PCBs are known for their excellent thermal conductivity, high durability, and ability to withstand extreme temperatures and harsh environments.
Composition of Ceramic PCBs
Ceramic PCBs are typically made from alumina (aluminum oxide) or aluminum nitride. These materials are known for their high thermal conductivity, low coefficient of thermal expansion (CTE), and excellent dielectric properties. The composition of ceramic PCBs allows them to dissipate heat efficiently, making them ideal for high-power applications where thermal management is crucial.
Manufacturing Process
The manufacturing process of ceramic PCBs differs from that of traditional PCBs. It involves the following steps:
- Substrate Preparation: The ceramic substrate is cleaned and prepared for the manufacturing process.
- Metallization: A thin layer of metal, usually copper, is deposited onto the ceramic substrate using techniques such as screen printing, sputtering, or electroplating.
- Patterning: The desired circuit pattern is created on the metallized ceramic substrate using photolithography or laser etching.
- Plating: Additional layers of metal, such as nickel and gold, may be plated onto the circuit pattern to improve conductivity and protect against oxidation.
- Singulation: The ceramic pcb panel is cut into individual boards using diamond cutting tools or laser cutting techniques.
Advantages of Ceramic PCBs
Ceramic PCBs offer several advantages over traditional PCBs, making them suitable for specific applications. Some of the key advantages include:
High Thermal Conductivity
One of the most significant advantages of ceramic PCBs is their high thermal conductivity. Alumina and aluminum nitride ceramics have thermal conductivity values ranging from 20 to 200 W/mK, which is significantly higher than FR4 (0.3 W/mK) used in traditional PCBs. This property allows ceramic PCBs to efficiently dissipate heat generated by electronic components, preventing overheating and improving the overall reliability of the circuit.
Low Coefficient of Thermal Expansion (CTE)
Ceramic materials have a low CTE, which means they experience minimal expansion or contraction when subjected to temperature changes. This property is crucial in applications where dimensional stability is important, such as in high-precision circuits or in environments with large temperature fluctuations. The low CTE of ceramic PCBs helps minimize stress on the components and solder joints, reducing the risk of failure due to thermal cycling.
High Durability and Strength
Ceramic PCBs are known for their high durability and strength. They can withstand mechanical stresses, vibrations, and impacts better than traditional PCBs. The ceramic substrate is inherently rigid and resistant to bending or warping, making it suitable for applications that require a robust and reliable circuit board. Additionally, ceramic PCBs have a high flexural strength, which allows them to withstand higher loads without cracking or breaking.
Excellent Dielectric Properties
Ceramic materials possess excellent dielectric properties, which make them suitable for high-frequency and high-voltage applications. They have low dielectric loss and high dielectric strength, enabling them to maintain signal integrity and minimize signal distortion. This property is particularly important in RF and microwave applications, where signal quality is critical.
Wide Temperature Range
Ceramic PCBs can operate in a wide temperature range, typically from -55°C to +400°C, depending on the specific ceramic material used. This temperature tolerance is significantly higher than that of traditional PCBs, which are limited to a maximum operating temperature of around 130°C. The ability to withstand extreme temperatures makes ceramic PCBs suitable for applications in aerospace, automotive, and industrial environments where high-temperature operation is required.
Chemical and Corrosion Resistance
Ceramic materials are chemically inert and resistant to corrosion. They can withstand exposure to various chemicals, solvents, and acids without degradation. This property is advantageous in applications where the PCB may be exposed to harsh chemicals or corrosive environments, such as in chemical processing plants or marine applications.
Applications of Ceramic PCBs
Ceramic PCBs find applications in various industries and domains where their unique properties are beneficial. Some of the common applications include:
High-Power Electronics
Ceramic PCBs are extensively used in high-power electronic applications due to their excellent thermal conductivity and ability to dissipate heat efficiently. They are commonly used in power modules, high-power LEDs, automotive electronics, and power converters. The high thermal conductivity of ceramic PCBs helps in managing the heat generated by power components, ensuring reliable operation and extended lifespan.
RF and Microwave Circuits
Ceramic PCBs are well-suited for RF and microwave applications due to their excellent dielectric properties. They offer low dielectric loss and high dielectric strength, which are essential for maintaining signal integrity at high frequencies. Ceramic PCBs are used in radar systems, wireless communication devices, satellite communications, and high-frequency test equipment.
Aerospace and Defense
The aerospace and defense industries require PCBs that can withstand extreme temperatures, mechanical stresses, and harsh environments. Ceramic PCBs are extensively used in these applications due to their high durability, wide temperature range, and resistance to vibrations and shocks. They are used in avionics systems, missile guidance systems, and satellite electronics.
Automotive Electronics
Ceramic PCBs find applications in automotive electronics, particularly in high-temperature environments such as engine control units, exhaust gas sensors, and brake systems. The ability of ceramic PCBs to operate reliably at high temperatures makes them suitable for these demanding automotive applications.
Medical Devices
Ceramic PCBs are used in medical devices that require high reliability, precision, and resistance to sterilization processes. They are employed in implantable devices, surgical instruments, and diagnostic equipment. The biocompatibility and chemical resistance of ceramic materials make them suitable for medical applications.
Industrial Control Systems
Industrial control systems often operate in harsh environments with extreme temperatures, vibrations, and exposure to chemicals. Ceramic PCBs are used in industrial control applications due to their high durability, wide temperature range, and resistance to corrosion. They are employed in process control systems, automation equipment, and industrial sensors.
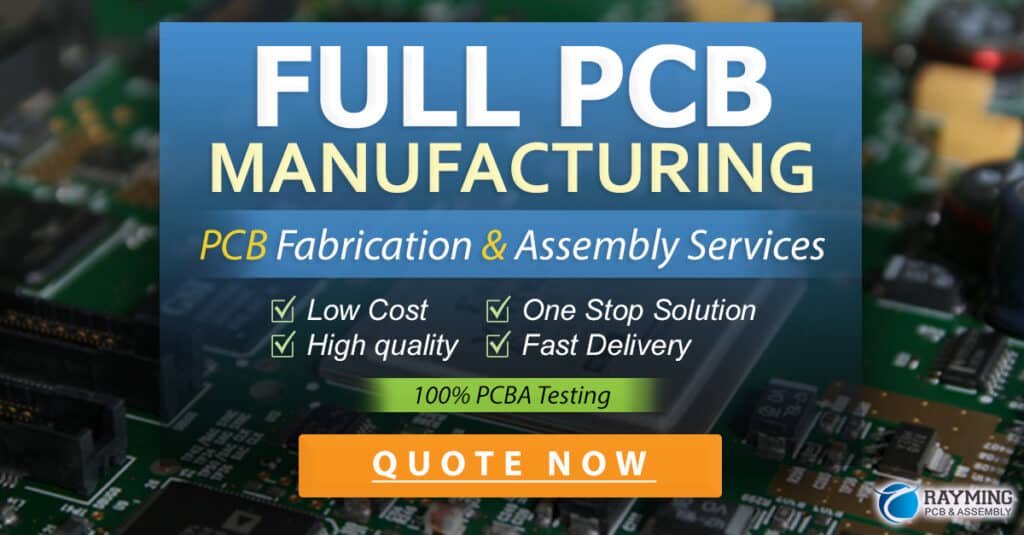
Challenges and Considerations
While ceramic PCBs offer numerous advantages, there are also some challenges and considerations to keep in mind when using them:
Higher Cost
Ceramic PCBs are generally more expensive than traditional PCBs due to the cost of the ceramic substrate materials and the specialized manufacturing processes involved. The higher cost may be justified in applications where the unique properties of ceramic PCBs are critical, but it can be a limiting factor in cost-sensitive applications.
Limited Flexibility
Ceramic PCBs are inherently rigid and brittle, which limits their flexibility compared to traditional PCBs. They are not suitable for applications that require flexible or bendable circuits. The rigidity of ceramic PCBs also requires careful handling during assembly and installation to avoid cracking or damage.
Specialized Manufacturing
The manufacturing process for ceramic PCBs requires specialized equipment and expertise. Not all PCB manufacturers have the capability to produce ceramic PCBs, which can limit the availability and lead times. It is important to work with a manufacturer that has experience in ceramic PCB fabrication to ensure the desired quality and reliability.
Design Considerations
Designing circuits on ceramic PCBs requires consideration of the unique properties and limitations of the ceramic substrate. The thermal expansion mismatch between the ceramic substrate and the components needs to be taken into account to avoid stress and reliability issues. Additionally, the layout and routing of traces on ceramic PCBs may require different design rules compared to traditional PCBs.
FAQs
-
Q: What is the main difference between ceramic PCBs and traditional PCBs?
A: The main difference is the substrate material. Ceramic PCBs use a ceramic substrate, such as alumina or aluminum nitride, while traditional PCBs use organic materials like FR4. Ceramic PCBs offer higher thermal conductivity, durability, and ability to withstand extreme temperatures compared to traditional PCBs. -
Q: Are ceramic PCBs more expensive than traditional PCBs?
A: Yes, ceramic PCBs are generally more expensive than traditional PCBs due to the cost of the ceramic substrate materials and the specialized manufacturing processes involved. However, the higher cost may be justified in applications where the unique properties of ceramic PCBs are critical. -
Q: Can ceramic PCBs be used in flexible applications?
A: No, ceramic PCBs are inherently rigid and brittle, which limits their flexibility. They are not suitable for applications that require flexible or bendable circuits. If flexibility is a requirement, traditional PCBs or flexible PCBs made from polymeric materials are more appropriate. -
Q: What are the typical operating temperature ranges for ceramic PCBs?
A: Ceramic PCBs can operate in a wide temperature range, typically from -55°C to +400°C, depending on the specific ceramic material used. This temperature tolerance is significantly higher than that of traditional PCBs, which are limited to a maximum operating temperature of around 130°C. -
Q: Are there any special considerations when designing circuits on ceramic PCBs?
A: Yes, designing circuits on ceramic PCBs requires consideration of the unique properties and limitations of the ceramic substrate. The thermal expansion mismatch between the ceramic substrate and the components needs to be taken into account to avoid stress and reliability issues. Additionally, the layout and routing of traces on ceramic PCBs may require different design rules compared to traditional PCBs.
Conclusion
Ceramic PCBs offer a unique combination of properties that make them suitable for various applications where traditional PCBs may not suffice. Their high thermal conductivity, low CTE, high durability, excellent dielectric properties, and wide temperature range make them ideal for high-power electronics, RF and microwave circuits, aerospace and defense systems, automotive electronics, medical devices, and industrial control systems.
However, ceramic PCBs also come with challenges such as higher cost, limited flexibility, and specialized manufacturing requirements. Designers and engineers must carefully consider the specific requirements of their application and weigh the advantages and limitations of ceramic PCBs before making a decision.
As technology continues to advance, the demand for high-performance and reliable electronic circuits will continue to grow. Ceramic PCBs will play a crucial role in enabling the development of advanced electronic systems that can withstand extreme conditions and deliver superior performance. With their unique properties and capabilities, ceramic PCBs are poised to be a key enabling technology in the future of electronics.
Leave a Reply