Introduction to PCB Traces
Printed Circuit Boards (PCBs) are essential components in modern electronics, providing a platform for interconnecting various electronic components. One of the most critical elements of a PCB is the network of conductive pathways known as traces. PCB traces are the copper lines that carry electrical signals and power between components on the board. Understanding the role and characteristics of PCB traces is crucial for designing and manufacturing reliable and efficient electronic devices.
What are PCB Traces?
PCB traces are thin, conductive paths etched onto the surface of a printed circuit board. These traces are typically made of copper and are designed to carry electrical signals and power between the various components mounted on the PCB. The width, thickness, and spacing of these traces are carefully calculated to ensure proper signal integrity, power delivery, and electromagnetic compatibility.
The Importance of PCB Traces
PCB traces play a vital role in the functioning of electronic devices. They facilitate the communication between components, allowing signals to travel from one point to another on the board. The quality and design of these traces directly impact the performance, reliability, and longevity of the electronic device. Poorly designed or manufactured traces can lead to signal degradation, crosstalk, and even complete device failure.
PCB Trace Design Considerations
Trace Width
The width of a PCB trace is a critical factor in its ability to carry electrical current. Wider traces can handle higher currents and are less prone to overheating. The appropriate trace width depends on several factors, including the amount of current the trace needs to carry, the thickness of the copper layer, and the temperature rise allowed on the board. Designers use various calculators and tools to determine the optimal trace width for a given application.
Current (A) | Trace Width (mm) |
---|---|
0.5 | 0.2 |
1.0 | 0.4 |
2.0 | 0.8 |
3.0 | 1.2 |
4.0 | 1.6 |
Table 1: Example trace width values for different current requirements (assuming 1 oz copper thickness and a 10°C temperature rise).
Trace Thickness
The thickness of a PCB trace, also known as its height, is determined by the copper weight used during the PCB manufacturing process. Copper weight is typically measured in ounces per square foot (oz/ft²), with common values being 0.5 oz, 1 oz, and 2 oz. Thicker traces can carry more current and are less susceptible to damage during the assembly process. However, thicker traces also increase the overall cost of the PCB.
Trace Spacing
Trace spacing, or the distance between adjacent traces, is another critical design consideration. Proper spacing helps prevent crosstalk, which occurs when signals from one trace interfere with those in a nearby trace. The minimum spacing between traces depends on factors such as the signal voltage, frequency, and the PCB material’s dielectric constant. Designers must adhere to industry standards and guidelines when determining trace spacing to ensure signal integrity and electromagnetic compatibility.
Signal Integrity and PCB Traces
Impedance Control
Maintaining proper impedance is crucial for ensuring signal integrity in high-speed digital circuits. Impedance is the measure of opposition to the flow of alternating current (AC) in a circuit. PCB traces must be designed to have a specific characteristic impedance, typically 50 ohms or 100 ohms, to match the impedance of the components and connectors used in the system. Mismatched impedances can lead to signal reflections, distortions, and ultimately, poor system performance.
To achieve the desired characteristic impedance, designers must carefully control the trace width, thickness, and spacing, as well as the properties of the PCB substrate material. Various calculators and simulation tools are available to help designers optimize trace geometry for impedance control.
Crosstalk
Crosstalk is a phenomenon where signals from one trace interfere with those in an adjacent trace. This interference can lead to signal degradation, noise, and even false triggering of digital circuits. To minimize crosstalk, designers must ensure adequate spacing between traces and, in some cases, use guard traces or ground planes to provide additional isolation.
Length Matching
In high-speed digital systems, it is crucial to ensure that signals arrive at their destinations at the same time. If signals arrive at different times, it can lead to timing errors and system malfunctions. To prevent this, designers must carefully match the lengths of traces carrying related signals. Length matching is particularly important for differential pairs, such as those used in USB, HDMI, and Ethernet interfaces.
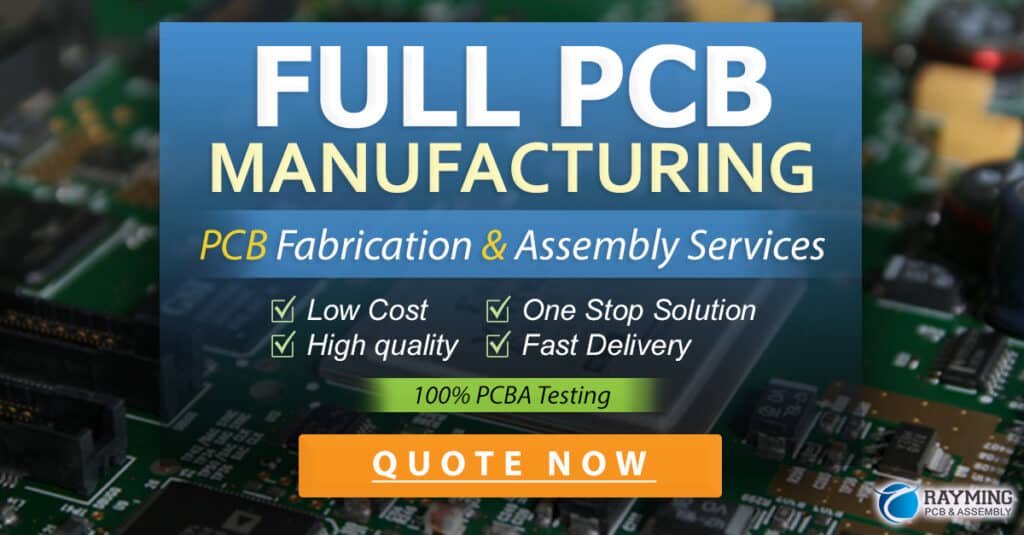
PCB Trace Routing Techniques
Manual Routing
Manual routing involves manually placing and connecting traces on the PCB layout using CAD software. This method allows for precise control over trace placement and is often used for critical signals or in areas where automated routing may not provide optimal results. However, manual routing can be time-consuming and requires a high level of expertise.
Autorouting
Autorouting is an automated process where the CAD software uses algorithms to place and connect traces on the PCB layout. This method is much faster than manual routing and can handle complex designs with thousands of traces. However, autorouting may not always provide the most optimal results, particularly for high-speed or critical signals. Designers often use a combination of manual and autorouting techniques to achieve the best balance between efficiency and quality.
Via Placement
Vias are conductive holes that allow traces to pass from one layer of the PCB to another. Proper via placement is essential for maintaining signal integrity and minimizing the impact of vias on trace impedance. Designers must consider factors such as via size, spacing, and hole-to-pad ratio when placing vias on the PCB layout.
Advanced PCB Trace Techniques
Differential Pairs
Differential signaling is a technique used in high-speed digital systems to improve signal integrity and reduce electromagnetic interference (EMI). In differential signaling, two traces carry complementary signals, with the voltage difference between the traces representing the actual signal. Differential pairs must be carefully routed to maintain a constant spacing between the traces and to avoid any discontinuities that could impact signal quality.
Serpentine Traces
Serpentine traces are used to add controlled amounts of delay to signals, helping to match the lengths of related traces. These traces are shaped like a serpentine or zigzag pattern, allowing designers to fine-tune the delay without significantly increasing the overall trace length. Serpentine traces are commonly used in high-speed memory interfaces, such as DDR3 and DDR4.
Microstrip and Stripline
Microstrip and stripline are two common types of transmission lines used in PCB design. Microstrip traces are routed on the outer layers of the PCB, with a ground plane on the layer beneath the trace. Stripline traces, on the other hand, are routed on inner layers, with ground planes above and below the trace. Both microstrip and stripline traces offer controlled impedance and are used in high-speed applications.
PCB Trace Manufacturing Considerations
Etching Process
PCB traces are created through an etching process, where unwanted copper is removed from the PCB substrate, leaving behind the desired trace pattern. The most common etching methods are wet etching and dry etching. Wet etching involves using chemicals to dissolve the unwanted copper, while dry etching uses plasma or laser technology to remove the copper. The choice of etching method depends on factors such as the desired trace resolution, production volume, and environmental considerations.
Soldermask and Silkscreen
Soldermask is a protective coating applied to the PCB surface, covering the traces and leaving only the pads and other areas that require soldering exposed. Soldermask helps prevent short circuits and oxidation of the copper traces. Silkscreen is a printed layer on top of the soldermask that provides text and graphics for component identification and assembly instructions. Designers must ensure that the soldermask and silkscreen designs do not interfere with the functionality of the PCB traces.
Trace Finishing
After the etching process, PCB traces are typically finished with a protective coating to prevent oxidation and improve solderability. Common finishing options include Hot Air Solder Leveling (HASL), Immersion Silver (IAg), Immersion Tin (ISn), and Electroless Nickel Immersion Gold (ENIG). The choice of finish depends on factors such as the intended application, cost, and compatibility with the assembly process.
Frequently Asked Questions (FAQ)
1. What is the difference between a PCB trace and a wire?
A PCB trace is a conductive path etched directly onto the surface of a printed circuit board, while a wire is a separate, insulated conductor that connects components. PCB traces are fixed in place and are typically used for shorter distances, while wires are more flexible and can be used for longer distances or connections between separate PCBs.
2. Can PCB traces carry high voltages?
Yes, PCB traces can be designed to carry high voltages, but special considerations must be taken to ensure proper insulation and spacing between traces. High-voltage PCBs often use thicker copper layers, wider trace spacing, and specialized materials to prevent arcing and ensure safe operation.
3. What is the minimum width for a PCB trace?
The minimum width for a PCB trace depends on the manufacturing capabilities of the pcb fabricator and the design requirements of the circuit. Typically, the minimum trace width is around 0.1 mm (4 mil) for standard PCB designs, but advanced manufacturing techniques can produce traces as narrow as 0.05 mm (2 mil) or even smaller.
4. How do you calculate the current carrying capacity of a PCB trace?
The current carrying capacity of a PCB trace can be calculated using various formulas that take into account factors such as trace width, thickness, temperature rise, and copper weight. One common formula is the IPC-2152 standard, which provides guidelines for determining the appropriate trace size based on the required current and temperature rise.
5. What is the purpose of a ground plane in PCB design?
A ground plane is a large, continuous copper area on a PCB layer that serves as a reference point for electrical signals. Ground planes help reduce electromagnetic interference (EMI), provide a low-impedance return path for currents, and improve signal integrity by minimizing ground loops and providing shielding between traces.
Conclusion
PCB traces are the backbone of modern electronic devices, providing the critical interconnections between components that enable the functioning of the device. Designing and manufacturing high-quality PCB traces requires a deep understanding of signal integrity, impedance control, and routing techniques. By carefully considering factors such as trace width, thickness, spacing, and routing, designers can create PCBs that are reliable, efficient, and capable of meeting the demands of today’s complex electronic systems. As technology continues to advance, the role of PCB traces in enabling these advancements will only become more important, making a solid grasp of PCB trace design and manufacturing essential for engineers and technicians alike.
Leave a Reply