The PCB Assembly Process
The PCB assembly process typically involves the following steps:
- Design and Fabrication
- Solder Paste Application
- Component Placement
- Reflow Soldering
- Inspection and Testing
- Conformal Coating
- Final Assembly and Packaging
Let’s dive into each of these steps in more detail.
1. Design and Fabrication
The first step in the PCB assembly process is the design and fabrication of the PCB itself. This involves creating a schematic diagram of the circuit and then designing the physical layout of the PCB using specialized software. The design must take into account factors such as component placement, trace routing, and signal integrity.
Once the design is complete, the PCB is fabricated using a process called photolithography. This involves applying a photoresist layer to a copper-clad board, exposing it to light through a mask, and then etching away the unwanted copper to create the desired circuit pattern.
2. Solder Paste Application
The next step in the PCB assembly process is to apply solder paste to the pads on the PCB where the components will be placed. Solder paste is a mixture of tiny solder particles suspended in a flux medium. The flux helps to clean the metal surfaces and prevent oxidation during the soldering process.
There are several methods for applying solder paste, including screen printing, stencil printing, and dispensing. Screen printing involves using a mesh screen with a stencil to apply the solder paste to the PCB. Stencil printing is similar, but uses a metal stencil instead of a mesh screen. Dispensing involves using a syringe or other dispensing tool to apply the solder paste directly to the pads.
3. Component Placement
Once the solder paste has been applied, the next step is to place the components onto the PCB. This is typically done using a pick-and-place machine, which uses a vacuum nozzle to pick up the components and place them onto the pads on the PCB.
The pick-and-place machine is programmed with the coordinates of each component on the PCB, and it uses these coordinates to accurately place the components onto the board. Some machines also have vision systems that can inspect the components and the PCB to ensure that they are placed correctly.
4. Reflow Soldering
After the components have been placed onto the PCB, the next step is to perform reflow soldering. This involves passing the PCB through an oven that heats the solder paste until it melts and forms a permanent connection between the components and the PCB.
The reflow soldering process typically involves several stages, each with a specific temperature profile. The stages may include:
- Preheat: The PCB is heated to a temperature just below the melting point of the solder paste to activate the flux and remove any moisture.
- Soak: The temperature is maintained for a period of time to allow the flux to clean the metal surfaces and the solder to begin to melt.
- Reflow: The temperature is increased to the melting point of the solder, allowing it to flow and form a connection between the components and the PCB.
- Cooling: The PCB is cooled back down to room temperature, allowing the solder to solidify and form a permanent connection.
5. Inspection and Testing
After the reflow soldering process is complete, the next step is to inspect and test the PCB to ensure that it is functioning correctly. This may involve visual inspection, automated optical inspection (AOI), and/or electrical testing.
Visual inspection involves examining the PCB under a microscope or other magnifying device to look for defects such as bridging (where solder has flowed between two adjacent pads), insufficient solder, or misaligned components.
AOI uses cameras and image processing software to automatically inspect the PCB for defects. This can be faster and more accurate than manual visual inspection, especially for high-volume production.
Electrical testing involves powering up the PCB and testing its functionality using specialized equipment. This may include in-circuit testing (ICT), which tests the individual components on the PCB, and functional testing, which tests the overall functionality of the assembled PCB.
6. Conformal Coating
In some cases, the PCB may require a conformal coating to protect it from environmental factors such as moisture, dust, or chemical exposure. Conformal coating is a thin layer of material that is applied over the surface of the PCB to provide a barrier against these factors.
There are several types of conformal coating materials, including acrylic, silicone, and urethane. The choice of material depends on the specific requirements of the application, such as the level of protection needed and the operating environment.
Conformal coating can be applied using various methods, including spray coating, brush coating, and dip coating. The coating must be applied evenly and consistently to ensure adequate protection without affecting the functionality of the PCB.
7. Final Assembly and Packaging
The final step in the PCB assembly process is to assemble the PCB into its final housing or enclosure and package it for shipping. This may involve attaching connectors, cables, or other components to the PCB, as well as labeling and packaging the finished product.
The specific requirements for final assembly and packaging will depend on the application and the customer’s needs. Some products may require specialized packaging to protect them during shipping, while others may need to be labeled with specific information such as serial numbers or regulatory markings.
Benefits of PCB Assembly
PCB assembly offers several benefits over other methods of assembling electronic devices, such as point-to-point wiring or breadboarding. Some of the key benefits include:
- Improved reliability: PCBs provide a stable and reliable platform for mounting and interconnecting electronic components, reducing the risk of failures due to loose connections or other issues.
- Reduced size and weight: PCBs allow for the miniaturization of electronic devices by providing a compact and efficient way to mount and interconnect components.
- Increased automation: PCB assembly can be highly automated, reducing the need for manual labor and increasing production efficiency.
- Lower cost: PCB assembly can be more cost-effective than other methods of assembling electronic devices, especially for high-volume production.
Challenges of PCB Assembly
Despite its many benefits, PCB assembly also presents some challenges that must be addressed to ensure a successful outcome. Some of the key challenges include:
- Component availability: The availability of electronic components can be a challenge, especially for older or discontinued parts. This can lead to delays or the need to redesign the PCB to accommodate alternative components.
- Manufacturing defects: PCB assembly involves many complex processes, and defects can occur at any stage. These defects can range from minor cosmetic issues to major functional failures, and they must be detected and corrected before the product is shipped to the customer.
- Electrostatic discharge (ESD): Electronic components can be damaged by ESD, which can occur during handling or assembly. Proper ESD protection measures must be in place to prevent damage to sensitive components.
- Thermal management: The heat generated by electronic components must be properly managed to prevent overheating and ensure reliable operation. This may require the use of heat sinks, fans, or other thermal management techniques.
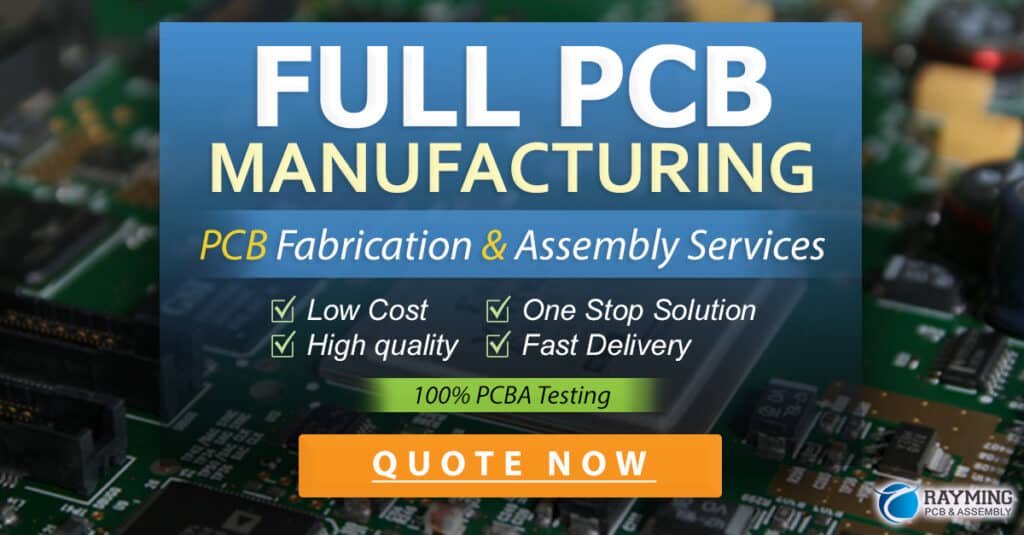
The Future of PCB Assembly
As electronic devices continue to become smaller, more complex, and more powerful, the PCB assembly process will need to evolve to keep pace. Some of the key trends and developments in PCB assembly include:
- Miniaturization: The trend towards miniaturization will continue, with smaller and more densely packed components becoming the norm. This will require advanced manufacturing techniques and materials to ensure reliability and performance.
- 3D printing: 3D printing technology is beginning to be used for PCB assembly, allowing for the creation of complex three-dimensional structures and the integration of electronic components directly into the PCB.
- Flexible and stretchable electronics: The development of flexible and stretchable electronic materials will enable the creation of new types of electronic devices that can conform to the shape of the human body or other objects.
- Sustainability: There is growing interest in developing more sustainable and environmentally friendly PCB assembly processes, such as the use of lead-free solder and the recycling of electronic waste.
Conclusion
PCB assembly is a complex and critical process that involves many steps and challenges. By understanding the various stages of the process and the key considerations at each stage, manufacturers can ensure the quality and reliability of their electronic products.
As technology continues to evolve, the PCB assembly process will need to adapt and innovate to keep pace with changing requirements and demands. By staying up-to-date with the latest trends and developments in PCB assembly, manufacturers can position themselves for success in the fast-paced and competitive world of electronics manufacturing.
Frequently Asked Questions (FAQ)
-
What is PCB assembly?
PCB assembly is the process of assembling electronic components onto a printed circuit board (PCB) to create a functional electronic device. -
What are the main steps in the PCB assembly process?
The main steps in the PCB assembly process include design and fabrication, solder paste application, component placement, reflow soldering, inspection and testing, conformal coating, and final assembly and packaging. -
What are some of the benefits of PCB assembly?
Some of the benefits of PCB assembly include improved reliability, reduced size and weight, increased automation, and lower cost compared to other methods of assembling electronic devices. -
What are some of the challenges of PCB assembly?
Some of the challenges of PCB assembly include component availability, manufacturing defects, electrostatic discharge (ESD), and thermal management. -
What are some of the future trends in PCB assembly?
Some of the future trends in PCB assembly include miniaturization, 3D printing, flexible and stretchable electronics, and sustainability.
Leave a Reply