Introduction to PCB designing
PCB designing is the process of creating a printed circuit board that connects electronic components to form a functional circuit. The PCB acts as a base for the components and provides electrical connections between them. PCB designing involves several steps, including schematic capture, layout design, and manufacturing.
Steps in PCB designing
1. Concept and Schematic Design
The first step in PCB designing is to develop a concept and create a schematic design. The schematic design is a graphical representation of the electronic circuit, showing the components and their connections. It is created using specialized software such as KiCad, Eagle, or Altium Designer.
1.1 Define the project requirements
Before starting the schematic design, it is essential to define the project requirements. This includes the functionality of the circuit, the components needed, and any constraints such as size, power consumption, or environmental factors.
1.2 Create the schematic diagram
Once the requirements are defined, the next step is to create the schematic diagram. This involves placing the components and connecting them according to the circuit design. The schematic diagram should include all the necessary information, such as component values, pin numbers, and power supply connections.
1.3 Simulate and verify the design
After creating the schematic diagram, it is important to simulate and verify the design to ensure that it works as expected. This can be done using simulation tools such as SPICE or Multisim. Simulation helps to identify any errors or issues in the design before proceeding to the next step.
2. PCB Layout Design
Once the schematic design is complete and verified, the next step is to create the PCB layout. The PCB layout is a physical representation of the circuit, showing the placement of components and the routing of traces.
2.1 Define the board outline and constraints
The first step in PCB layout design is to define the board outline and any constraints such as mounting holes, keepout areas, or component heights. This information is used to create the board shape and ensure that the components fit within the available space.
2.2 Place the components
The next step is to place the components on the board. This involves arranging the components in a logical and efficient manner, taking into account factors such as signal integrity, power distribution, and thermal management. The placement of components should also consider the manufacturing process and any assembly requirements.
2.3 Route the traces
After placing the components, the next step is to route the traces between them. Traces are the copper paths that carry electrical signals between the components. The routing process involves creating a network of traces that connect the components according to the schematic design. The routing should be optimized for signal integrity, minimizing crosstalk and electromagnetic interference (EMI).
2.4 Add copper pours and planes
Copper pours and planes are used to provide a low-impedance path for power and ground signals. They also help to reduce EMI and improve thermal management. Copper pours are added to the top and bottom layers of the board, while planes are added to the inner layers.
2.5 Perform design rule checks (DRC)
Design rule checks (DRC) are used to verify that the PCB layout meets the manufacturing and assembly requirements. DRC checks for issues such as minimum trace width, minimum clearance between traces, and minimum drill size. Any violations of the design rules must be corrected before proceeding to the next step.
3. Manufacturing
Once the PCB layout is complete and verified, the next step is to manufacture the board. The manufacturing process involves several steps, including fabrication, assembly, and testing.
3.1 Generate manufacturing files
The first step in manufacturing is to generate the necessary files for fabrication and assembly. This includes Gerber files for the pcb layers, drill files for the holes, and pick-and-place files for the component placement. These files are sent to the pcb manufacturer for production.
3.2 pcb fabrication
PCB fabrication involves creating the physical board from the design files. The process starts with the creation of a copper-clad laminate, which is a sandwich of copper foil and insulating material. The copper is etched away to create the traces and pads according to the Gerber files. Holes are drilled for through-hole components and vias, and the board is plated with a protective finish such as solder mask and silkscreen.
3.3 PCB assembly
After fabrication, the PCB is assembled with the electronic components. The components are placed on the board using a pick-and-place machine, which uses the pick-and-place files generated earlier. The components are then soldered to the board using a reflow oven or wave soldering machine.
3.4 Testing and inspection
The final step in manufacturing is testing and inspection. The assembled pcb is tested for functionality and performance, and any defects or issues are identified and corrected. Visual inspection is also performed to ensure that the board meets the quality standards and specifications.
PCB Designing Tools
There are several PCB designing tools available in the market, ranging from free open-source software to commercial tools with advanced features. Some of the popular PCB designing tools are:
Tool | Description |
---|---|
KiCad | Free and open-source PCB design software |
Eagle | Popular PCB design software with a free version |
Altium Designer | High-end PCB design software with advanced features |
OrCAD | Comprehensive PCB design software with simulation capabilities |
Proteus | PCB design software with 3D visualization and simulation |
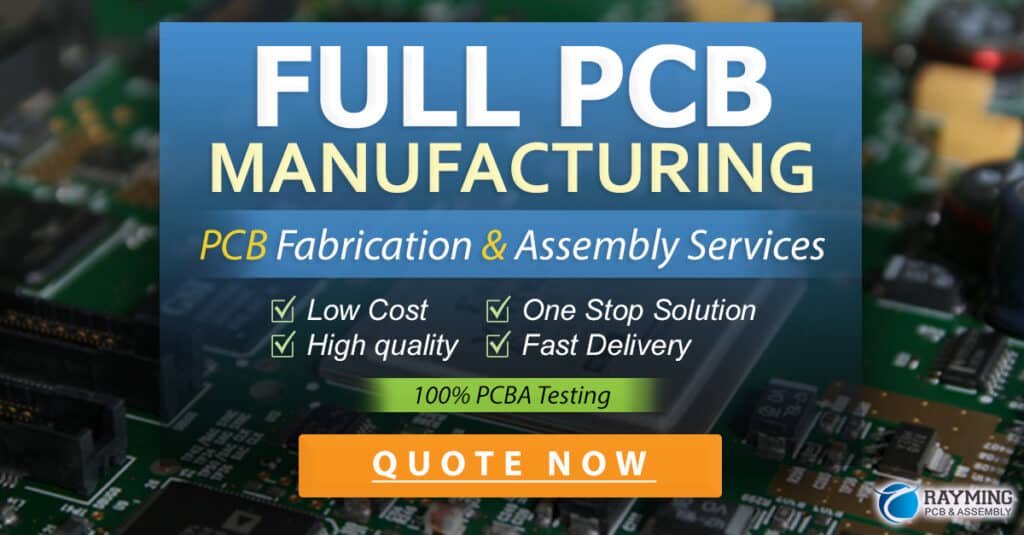
FAQ
1. What is the difference between a schematic and a PCB layout?
A schematic is a graphical representation of the electronic circuit, showing the components and their connections. A PCB layout, on the other hand, is a physical representation of the circuit, showing the placement of components and the routing of traces on the board.
2. What is the purpose of design rule checks (DRC) in PCB designing?
Design rule checks (DRC) are used to verify that the PCB layout meets the manufacturing and assembly requirements. DRC checks for issues such as minimum trace width, minimum clearance between traces, and minimum drill size. Any violations of the design rules must be corrected before proceeding to manufacturing.
3. What are the different types of PCB manufacturing processes?
There are two main types of PCB manufacturing processes: through-hole and surface-mount. Through-hole PCBs have components with leads that are inserted into holes drilled in the board and soldered on the opposite side. Surface-mount PCBs have components that are placed directly on the surface of the board and soldered using a reflow oven or wave soldering machine.
4. What is the role of copper pours and planes in PCB designing?
Copper pours and planes are used to provide a low-impedance path for power and ground signals. They also help to reduce electromagnetic interference (EMI) and improve thermal management. Copper pours are added to the top and bottom layers of the board, while planes are added to the inner layers.
5. What are the advantages of using PCB designing software?
PCB designing software offers several advantages over manual PCB design methods. It allows for faster and more accurate design creation, with features such as auto-routing, design rule checks, and 3D visualization. PCB designing software also enables collaboration and version control, making it easier to work with team members and manage design changes.
Conclusion
PCB designing is a complex process that requires a systematic approach and attention to detail. By following the steps outlined in this article, you can create high-quality PCBs that meet your project requirements and manufacturing standards. Whether you are a beginner or an experienced designer, understanding the pcb design process is essential for creating reliable and functional electronic circuits.
Leave a Reply