1. Computer-Aided Design (CAD) Software
What is CAD Software?
Computer-Aided Design (CAD) software is a fundamental tool in modern manufacturing. It enables engineers and designers to create detailed 2D and 3D models of products, components, and assemblies. CAD software provides a virtual environment for designing, visualizing, and simulating products before they are physically manufactured.
Key Features of CAD Software
- 2D and 3D modeling capabilities
- Parametric and feature-based design
- Assembly modeling and simulation
- Design automation and customization
- Integration with other manufacturing software
Benefits of Using CAD Software
- Improved design accuracy and precision
- Faster product development cycles
- Enhanced collaboration among design teams
- Reduced design errors and rework
- Seamless integration with downstream processes
Popular CAD Software in Manufacturing
Software | Description |
---|---|
AutoCAD | Versatile 2D and 3D CAD software widely used across industries |
SolidWorks | Powerful 3D CAD software known for its user-friendly interface and robust features |
Inventor | Feature-rich 3D CAD software with advanced simulation and tooling capabilities |
CATIA | Comprehensive CAD software suite for complex product design and engineering |
2. Computer-Aided Manufacturing (CAM) Software
What is CAM Software?
Computer-Aided Manufacturing (CAM) software is used to control and automate manufacturing processes. It takes the digital designs created in CAD software and generates machine-readable instructions for CNC machines, 3D printers, and other manufacturing equipment. CAM software optimizes tool paths, minimizes material waste, and ensures precise and efficient manufacturing operations.
Key Features of CAM Software
- Toolpath generation and optimization
- CNC machine simulation and verification
- Postprocessor generation for various machine controllers
- Material removal and additive manufacturing support
- Integration with CAD software and manufacturing execution systems
Benefits of Using CAM Software
- Increased manufacturing efficiency and productivity
- Reduced manufacturing errors and scrap
- Optimized tool utilization and extended tool life
- Improved product quality and consistency
- Faster time-to-market for new products
Popular CAM Software in Manufacturing
Software | Description |
---|---|
Mastercam | Widely used CAM software with extensive toolpath and machine support |
Autodesk CAM | Integrated CAM solution for Autodesk’s CAD software |
GibbsCAM | Versatile CAM software known for its ease of use and flexibility |
ESPRIT | Powerful CAM software with advanced 3D machining capabilities |
3. Enterprise Resource Planning (ERP) Software
What is ERP Software?
Enterprise Resource Planning (ERP) software is a comprehensive business management solution that integrates various functions of an organization, including manufacturing, finance, supply chain, human resources, and customer relationship management. ERP software provides a centralized database and streamlines information flow across different departments, enabling better decision-making and resource optimization.
Key Features of ERP Software
- Integrated modules for different business functions
- Real-time data visibility and reporting
- Automated workflows and business processes
- Inventory and supply chain management
- Financial management and accounting
Benefits of Using ERP Software
- Improved operational efficiency and productivity
- Enhanced data visibility and decision-making
- Streamlined supply chain and inventory management
- Better financial control and reporting
- Increased customer satisfaction and service levels
Popular ERP Software in Manufacturing
Software | Description |
---|---|
SAP ERP | Comprehensive ERP software suite widely used by large enterprises |
Oracle ERP Cloud | Cloud-based ERP solution with extensive manufacturing capabilities |
Microsoft Dynamics 365 | Flexible and scalable ERP software with strong integration capabilities |
Epicor ERP | Industry-specific ERP solution tailored for manufacturing businesses |
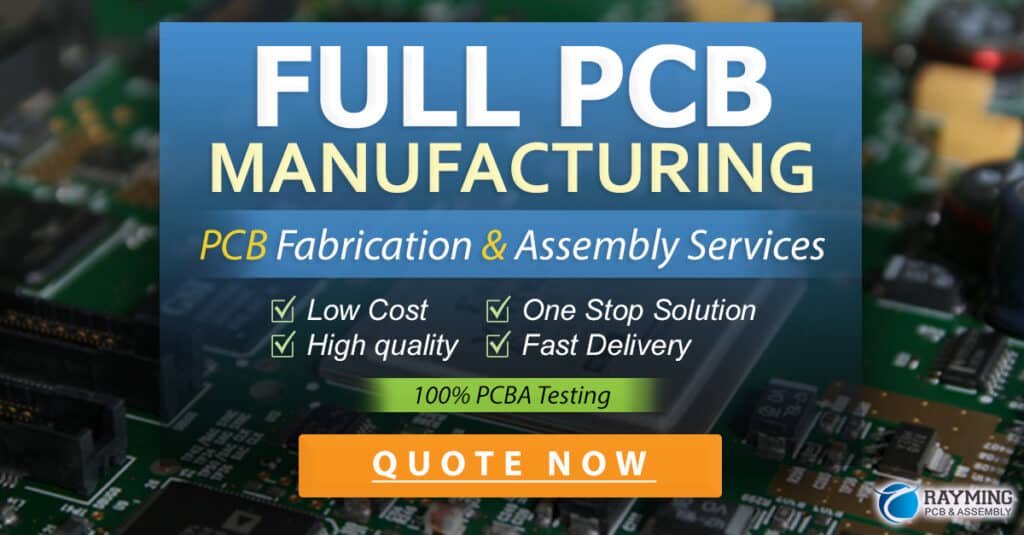
4. Manufacturing Execution System (MES) Software
What is MES Software?
Manufacturing Execution System (MES) software is designed to monitor, control, and optimize production processes in real-time. It bridges the gap between the shop floor and higher-level planning systems like ERP. MES software collects data from machines and operators, tracks production metrics, and provides visibility into the manufacturing process, enabling quick decision-making and continuous improvement.
Key Features of MES Software
- Real-time production monitoring and control
- Work order management and scheduling
- Material and inventory tracking
- Quality management and traceability
- Integration with shop floor automation systems
Benefits of Using MES Software
- Increased production efficiency and throughput
- Reduced manufacturing cycle times and lead times
- Improved product quality and compliance
- Enhanced visibility and control over the manufacturing process
- Better utilization of resources and assets
Popular MES Software in Manufacturing
Software | Description |
---|---|
Wonderware MES | Comprehensive MES software with strong visualization and analysis capabilities |
GE Digital MES | Scalable MES solution with advanced analytics and IoT integration |
Siemens MES | Integrated MES software suite for discrete and process manufacturing |
SAP Manufacturing Execution | MES solution tightly integrated with SAP ERP for seamless data flow |
5. Product Lifecycle Management (PLM) Software
What is PLM Software?
Product Lifecycle Management (PLM) software is used to manage the entire lifecycle of a product, from conception and design to manufacturing, service, and retirement. PLM software provides a centralized platform for managing product data, documents, and processes, enabling collaboration among cross-functional teams and ensuring data integrity throughout the product lifecycle.
Key Features of PLM Software
- Product data management and version control
- Bill of materials (BOM) management
- Change and configuration management
- Collaboration and workflow management
- Integration with CAD, CAM, and ERP systems
Benefits of Using PLM Software
- Improved product quality and compliance
- Faster time-to-market for new products
- Reduced product development costs and errors
- Enhanced collaboration and knowledge sharing
- Better traceability and control over product changes
Popular PLM Software in Manufacturing
Software | Description |
---|---|
Siemens Teamcenter | Comprehensive PLM software suite with extensive industry-specific capabilities |
PTC Windchill | Scalable PLM solution with strong collaboration and change management features |
Dassault Systèmes 3DEXPERIENCE | Cloud-based PLM platform with integrated design, simulation, and manufacturing capabilities |
Oracle Agile PLM | Flexible PLM software with robust product data management and collaboration tools |
6. Quality Management System (QMS) Software
What is QMS Software?
Quality Management System (QMS) software is designed to help organizations manage and improve the quality of their products and processes. It provides tools for document control, nonconformance management, corrective and preventive actions (CAPA), and auditing. QMS software ensures compliance with quality standards and regulations, reduces quality-related costs, and enhances customer satisfaction.
Key Features of QMS Software
- Document control and version management
- Nonconformance and deviation management
- Corrective and preventive action (CAPA) tracking
- Audit management and scheduling
- Integration with other manufacturing software systems
Benefits of Using QMS Software
- Improved product quality and consistency
- Reduced quality-related costs and rework
- Enhanced compliance with quality standards and regulations
- Faster identification and resolution of quality issues
- Increased customer satisfaction and loyalty
Popular QMS Software in Manufacturing
Software | Description |
---|---|
MasterControl | Comprehensive QMS software with strong document control and compliance features |
ETQ Reliance | Flexible QMS solution with extensive configurability and integration capabilities |
Sparta Systems TrackWise | Scalable QMS software with advanced analytics and reporting tools |
IQS | User-friendly QMS software with integrated training and competency management |
7. Inventory Management Software
What is Inventory Management Software?
Inventory management software is used to track and control the flow of materials, components, and finished goods within a manufacturing organization. It provides real-time visibility into inventory levels, helps optimize stock levels, and streamlines the process of ordering, receiving, and issuing inventory. Inventory management software ensures the right materials are available when needed, minimizes inventory carrying costs, and improves overall supply chain efficiency.
Key Features of Inventory Management Software
- Real-time inventory tracking and visibility
- Inventory optimization and replenishment planning
- Barcode and RFID integration for accurate data capture
- Lot and serial number tracking for traceability
- Integration with ERP and other manufacturing software systems
Benefits of Using Inventory Management Software
- Reduced inventory carrying costs and obsolescence
- Improved inventory accuracy and visibility
- Faster order fulfillment and reduced stockouts
- Enhanced traceability and recall management
- Increased supply chain efficiency and responsiveness
Popular Inventory Management Software in Manufacturing
Software | Description |
---|---|
Fishbowl Inventory | Affordable inventory management software for small to medium-sized businesses |
NetSuite Inventory Management | Cloud-based inventory management solution with strong ERP integration |
Sage Inventory Advisor | Intelligent inventory optimization software with demand forecasting capabilities |
Zoho Inventory | User-friendly inventory management software with multi-channel sales support |
8. Maintenance Management Software
What is Maintenance Management Software?
Maintenance management software, also known as Computerized Maintenance Management System (CMMS), is used to plan, schedule, and track maintenance activities for manufacturing equipment and assets. It helps optimize maintenance resources, reduces downtime, and extends the lifespan of equipment. Maintenance management software ensures that preventive maintenance is performed on schedule, breakdowns are quickly addressed, and maintenance costs are controlled.
Key Features of Maintenance Management Software
- Asset management and tracking
- Preventive maintenance scheduling and planning
- Work order management and assignment
- Spare parts and inventory management
- Reporting and analytics for maintenance performance
Benefits of Using Maintenance Management Software
- Increased equipment uptime and availability
- Reduced maintenance costs and unplanned downtime
- Improved maintenance planning and resource allocation
- Enhanced asset performance and lifespan
- Better compliance with safety and regulatory requirements
Popular Maintenance Management Software in Manufacturing
Software | Description |
---|---|
IBM Maximo | Comprehensive maintenance management software with strong asset lifecycle management capabilities |
eMaint CMMS | Flexible maintenance management solution with extensive customization options |
UpKeep | Mobile-first maintenance management software with intuitive user interface |
Fiix | Cloud-based maintenance management software with strong integration capabilities |
Frequently Asked Questions (FAQ)
1. How do I choose the right manufacturing software for my business?
Choosing the right manufacturing software depends on several factors, including your industry, business size, specific manufacturing processes, and budget. Consider the following steps:
- Identify your key manufacturing challenges and goals
- Evaluate your current IT infrastructure and integration requirements
- Research software options that align with your industry and specific needs
- Request demos and trials to assess the functionality and user-friendliness of the software
- Consider the scalability, support, and total cost of ownership of the software
2. Can different types of manufacturing software be integrated with each other?
Yes, most modern manufacturing software systems are designed to integrate with each other through APIs, web services, or direct database connections. Integration enables seamless data flow between different software systems, eliminates manual data entry, and provides a holistic view of the manufacturing process. However, the ease and extent of integration may vary depending on the specific software vendors and their integration capabilities.
3. How long does it typically take to implement manufacturing software?
The implementation timeline for manufacturing software varies depending on the complexity of the software, the size of your organization, and the scope of the implementation. Simple software implementations may take a few weeks, while more complex ERP or PLM implementations can span several months to a year. It’s essential to work closely with the software vendor and implementation partners to establish a realistic timeline and ensure a smooth transition.
4. What are the common challenges in implementing manufacturing software?
Some common challenges in implementing manufacturing software include:
- Resistance to change from employees and stakeholders
- Data migration and cleansing from legacy systems
- Integration with existing systems and processes
- Customization and configuration to match specific business requirements
- Training and adoption by end-users
To mitigate these challenges, it’s crucial to have a well-defined implementation plan, strong leadership support, effective change management, and ongoing user training and support.
5. How can I ensure the success of my manufacturing software implementation?
To ensure the success of your manufacturing software implementation, consider the following best practices:
- Clearly define your project goals, scope, and success criteria
- Involve key stakeholders and end-users throughout the implementation process
- Allocate sufficient resources, including budget, time, and personnel
- Perform thorough data migration and testing before going live
- Provide comprehensive user training and support
- Establish metrics to measure the success and ROI of the implementation
- Foster a culture of continuous improvement and user feedback
By following these best practices and working closely with your software vendor and implementation partners, you can maximize the benefits of your manufacturing software investment and drive long-term success.
Conclusion
In conclusion, the eight types of software used in manufacturing – CAD, CAM, ERP, MES, PLM, QMS, inventory management, and maintenance management – play critical roles in optimizing manufacturing processes, improving efficiency, and driving business success. By leveraging the right combination of these software solutions, manufacturing organizations can streamline operations, reduce costs, improve product quality, and enhance customer satisfaction.
When selecting and implementing manufacturing software, it’s essential to carefully evaluate your specific business needs, consider integration requirements, and follow best practices for successful implementation. By doing so, you can unlock the full potential of your manufacturing software investment and gain a competitive edge in today’s dynamic manufacturing landscape.
As the manufacturing industry continues to evolve and embrace digital transformation, the role of electronic manufacturing software will only become more crucial. By staying up-to-date with the latest software advancements and trends, manufacturing organizations can position themselves for long-term success and remain agile in the face of changing market demands and technological disruptions.
Leave a Reply