Table of Contents
- Schematic Design
- Component Selection
- PCB Layout
- Design Rule Check (DRC)
- Gerber File Generation
- PCB Fabrication
- PCB Assembly
- Testing and Inspection
- Rework and Repair
- Final Product and Documentation
1. Schematic Design
The first stage of the PCB design process is creating a schematic diagram. A schematic is a graphical representation of the electronic circuit, showing the interconnections between components. The schematic design stage involves:
- Defining the circuit’s functionality and requirements
- Selecting the appropriate components
- Creating the schematic using electronic design automation (EDA) software
- Verifying the schematic for accuracy and completeness
A well-designed schematic is essential for the success of the subsequent stages in the PCB design flow.
2. Component Selection
Once the schematic is complete, the next stage is to select the components that will be used in the PCB. Component selection involves:
- Choosing components that meet the circuit’s requirements (e.g., voltage, current, power, frequency)
- Considering factors such as cost, availability, and reliability
- Ensuring compatibility between components
- Creating a bill of materials (BOM) that lists all the required components
Proper component selection is crucial for ensuring the PCB’s performance, reliability, and cost-effectiveness.
3. PCB Layout
With the schematic and components finalized, the next stage is to create the PCB layout. The PCB layout stage involves:
- Determining the PCB’s dimensions and shape
- Placing components on the PCB
- Routing the interconnections between components
- Ensuring proper signal integrity and electromagnetic compatibility (EMC)
- Optimizing the layout for manufacturing and assembly
The PCB layout stage is critical for ensuring the PCB’s functionality, reliability, and manufacturability.
4. Design Rule Check (DRC)
After completing the PCB layout, the next stage is to perform a design rule check (DRC). The DRC stage involves:
- Verifying that the PCB layout meets the design rules and constraints
- Checking for issues such as short circuits, open circuits, and signal integrity problems
- Ensuring that the PCB layout is compatible with the manufacturing process
- Making necessary corrections and optimizations to the PCB layout
Performing a thorough DRC helps to identify and resolve issues before the PCB is manufactured, reducing the risk of costly errors and delays.
5. Gerber File Generation
Once the PCB layout has passed the DRC, the next stage is to generate the Gerber files. Gerber files are the industry-standard format for representing the PCB layout data. The Gerber file generation stage involves:
- Exporting the PCB layout data from the EDA software
- Creating separate Gerber files for each layer of the PCB (e.g., top copper, bottom copper, solder mask, silkscreen)
- Verifying the Gerber files for accuracy and completeness
- Sending the Gerber files to the PCB manufacturer
Accurate and complete Gerber files are essential for ensuring that the PCB is manufactured correctly.
6. PCB Fabrication
With the Gerber files generated, the next stage is to fabricate the PCB. The PCB fabrication stage involves:
- Selecting the appropriate PCB material (e.g., FR-4, Rogers, flexible)
- Creating the copper layers using photolithography and etching processes
- Applying the solder mask and silkscreen layers
- Drilling holes for through-hole components and vias
- Performing electrical tests to ensure the PCB’s functionality
The PCB fabrication stage is critical for ensuring the quality and reliability of the final product.
7. PCB Assembly
After the PCB is fabricated, the next stage is to assemble the components onto the PCB. The PCB assembly stage involves:
- Applying solder paste to the PCB pads
- Placing components onto the PCB using pick-and-place machines or manual assembly
- Soldering the components to the PCB using reflow ovens or wave soldering machines
- Inspecting the assembled PCB for defects and errors
- Performing functional tests to ensure the PCB’s performance
Proper PCB assembly is essential for ensuring the PCB’s reliability and functionality.
8. Testing and Inspection
Once the PCB is assembled, the next stage is to perform thorough testing and inspection. The testing and inspection stage involves:
- Performing visual inspections to identify any visible defects or errors
- Conducting electrical tests to verify the PCB’s functionality and performance
- Performing environmental tests (e.g., temperature, humidity, vibration) to ensure the PCB’s reliability
- Documenting the test results and any issues found
- Making necessary repairs or modifications to the PCB
Rigorous testing and inspection help to ensure that the PCB meets the required quality standards and specifications.
9. Rework and Repair
If issues are found during the testing and inspection stage, the next stage is to perform rework and repair. The rework and repair stage involves:
- Identifying the root cause of the issue
- Determining the appropriate repair or rework method
- Performing the necessary repairs or modifications to the PCB
- Re-testing the PCB to ensure that the issue has been resolved
- Documenting the rework and repair process
Effective rework and repair processes help to minimize the impact of issues on the final product’s quality and reliability.
10. Final Product and Documentation
The final stage of the PCB design process is to deliver the final product and documentation. The final product and documentation stage involves:
- Packaging the PCB for shipping and delivery
- Creating the necessary documentation (e.g., user manuals, technical specifications, test reports)
- Providing support and maintenance for the PCB throughout its lifecycle
- Continuously improving the PCB design process based on feedback and lessons learned
Delivering a high-quality final product and comprehensive documentation helps to ensure customer satisfaction and long-term success.
PCB Design Process Flow Chart
To better visualize the PCB design process, we can create a flow chart that shows the sequence of stages and the key activities involved in each stage:
graph TD
A[Schematic Design] --> B[Component Selection]
B --> C[PCB Layout]
C --> D[Design Rule Check]
D --> E[Gerber File Generation]
E --> F[PCB Fabrication]
F --> G[PCB Assembly]
G --> H[Testing and Inspection]
H --> I{Issues Found?}
I -->|Yes| J[Rework and Repair]
I -->|No| K[Final Product and Documentation]
J --> H
This flow chart provides a clear overview of the PCB design process and the dependencies between each stage.
FAQ
1. What is the importance of the schematic design stage in the PCB design process?
The schematic design stage is the foundation of the PCB design process. It defines the circuit’s functionality, interconnections, and requirements. A well-designed schematic is essential for ensuring the success of the subsequent stages and the overall quality of the final product.
2. Why is component selection critical in the PCB design process?
Component selection is critical in the PCB design process because it directly impacts the PCB’s performance, reliability, and cost-effectiveness. Choosing the right components that meet the circuit’s requirements, are compatible with each other, and are readily available is essential for ensuring the success of the PCB design.
3. What is the purpose of the design rule check (DRC) stage?
The purpose of the design rule check (DRC) stage is to verify that the PCB layout meets the design rules and constraints, and to identify any issues or errors that may impact the PCB’s functionality, reliability, or manufacturability. Performing a thorough DRC helps to catch and resolve issues before the PCB is manufactured, reducing the risk of costly mistakes and delays.
4. What are Gerber files, and why are they important in the PCB design process?
Gerber files are the industry-standard format for representing PCB layout data. They contain the information needed to manufacture the PCB, including the copper layers, solder mask, silkscreen, and drill data. Accurate and complete Gerber files are essential for ensuring that the PCB is manufactured correctly and meets the required specifications.
5. How does testing and inspection contribute to the quality of the final PCB product?
Testing and inspection are critical stages in the PCB design process that help to ensure the quality and reliability of the final product. Thorough testing and inspection can identify any defects, errors, or performance issues that may impact the PCB’s functionality or reliability. By catching and resolving these issues before the final product is delivered, testing and inspection help to ensure customer satisfaction and long-term success.
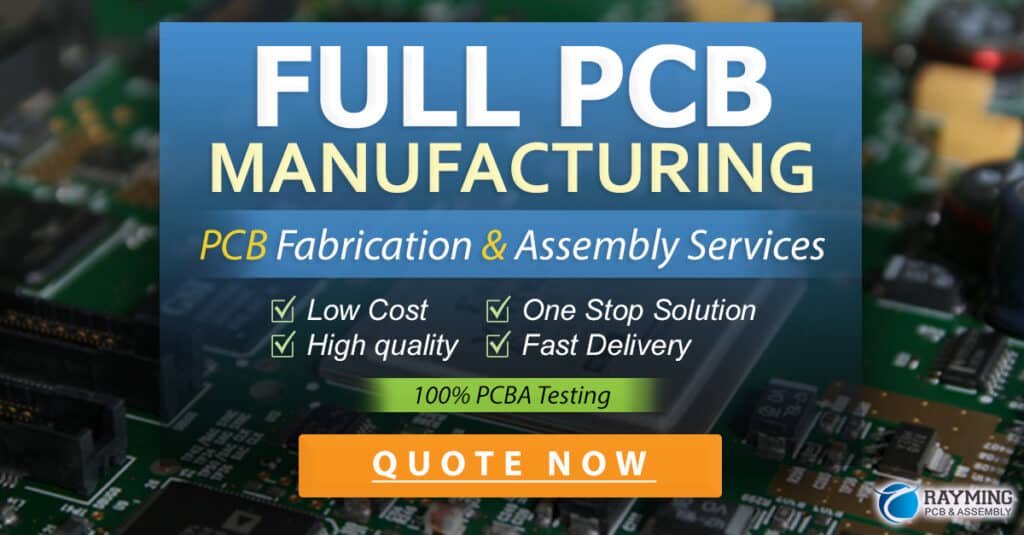
Conclusion
The PCB design process is a complex and multi-stage procedure that requires careful planning, execution, and collaboration between various teams and stakeholders. By understanding the 10 stages of the PCB design flow and the key activities involved in each stage, designers, engineers, and manufacturers can work together to create high-quality, reliable, and cost-effective PCBs that meet the required specifications and exceed customer expectations.
Leave a Reply