What are PTH holes in PCB?
PTH (Plated Through Hole) refers to holes in a PCB that have been electroplated with a conductive material, typically copper. The plating process creates an electrical connection between the top and bottom layers of the PCB, allowing components to be soldered on both sides of the board. PTH holes are commonly used for mounting through-hole components, such as resistors, capacitors, and connectors.
Advantages of PTH holes
- Strong mechanical connection: PTH holes provide a robust mechanical connection between the component and the PCB, making it suitable for applications that require high reliability and durability.
- Excellent electrical conductivity: The plating process ensures a low-resistance electrical connection between the component leads and the PCB traces.
- Compatibility with through-hole components: PTH holes are essential for mounting through-hole components, which are still widely used in various applications.
Disadvantages of PTH holes
- Higher manufacturing cost: The plating process adds an extra step to the PCB manufacturing process, increasing the overall cost.
- Larger footprint: Through-hole components typically have a larger footprint compared to surface-mount components, which can limit the PCB’s component density.
- Reduced design flexibility: PTH holes restrict the routing of traces on the PCB, as the holes must be avoided when laying out the circuit.
What are NPTH holes in PCB?
NPTH (Non-Plated Through Hole) refers to holes in a PCB that are not electroplated with a conductive material. These holes are used for various purposes, such as mounting hardware, providing mechanical support, or allowing for the passage of non-electrical components like screws or standoffs. NPTH holes do not create an electrical connection between the layers of the PCB.
Advantages of NPTH holes
- Cost-effective: Since NPTH holes do not require the plating process, they are less expensive to manufacture compared to PTH holes.
- Design flexibility: NPTH holes do not interfere with the routing of traces on the PCB, allowing for more flexible circuit layouts.
- Versatile applications: NPTH holes can be used for various non-electrical purposes, such as mounting hardware or providing mechanical support.
Disadvantages of NPTH holes
- No electrical connection: NPTH holes do not provide an electrical connection between the layers of the PCB, limiting their use for mounting electronic components.
- Potential for misalignment: Without the plating process, there is a higher risk of misalignment between the holes on different layers of the PCB.
Applications of PTH and NPTH holes in PCB
PTH and NPTH holes are used in various applications, depending on the specific requirements of the electronic device. Some common applications include:
- Through-hole component mounting: PTH holes are essential for mounting through-hole components, such as connectors, switches, and large capacitors.
- Mounting hardware: NPTH holes are commonly used for mounting hardware, such as screws, standoffs, and spacers, to provide mechanical support and stability to the PCB.
- Heatsinking: PTH holes can be used to mount heatsinks or other thermal management components, allowing for efficient heat dissipation from the PCB.
- Grounding: PTH holes can be used to create a low-impedance ground connection between the layers of the PCB, improving the device’s electromagnetic compatibility (EMC) performance.
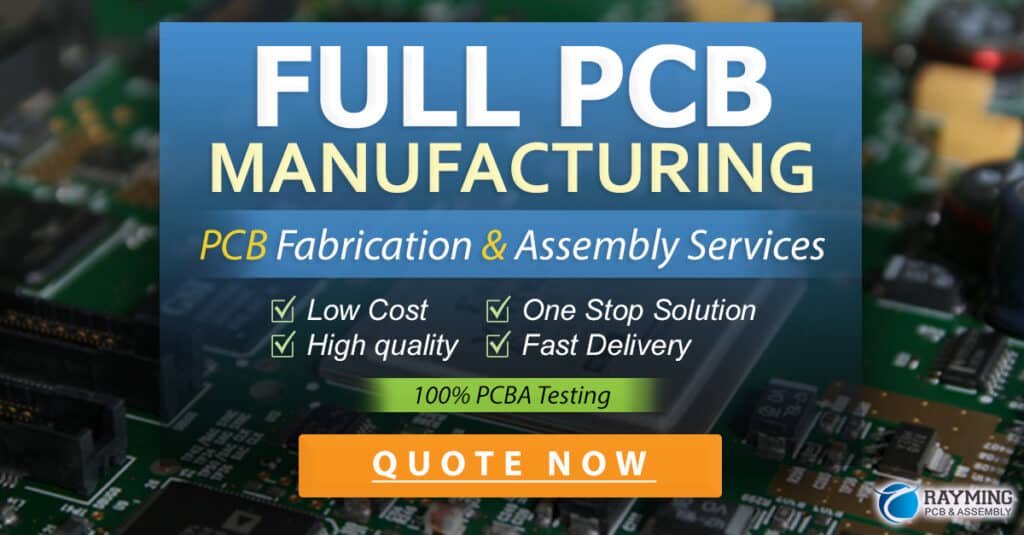
PCB hole sizes and tolerances
When designing a PCB, it is essential to consider the sizes and tolerances of the PTH and NPTH holes. The hole size is determined by the component lead diameter or the mounting hardware requirements. The tolerance of the hole size is crucial to ensure a proper fit and reliable connection.
Hole Type | Typical Hole Diameter Range |
---|---|
PTH | 0.5 mm to 1.5 mm |
NPTH | 1.0 mm to 6.0 mm |
The tolerance of the hole size depends on various factors, such as the PCB material, the manufacturing process, and the specific application requirements. Generally, a tighter tolerance results in a higher manufacturing cost.
PCB hole placement and routing considerations
When placing PTH and NPTH holes on a PCB, designers must consider several factors to ensure optimal performance and manufacturability:
- Component placement: PTH holes should be placed in a way that allows for efficient component placement and soldering, while minimizing the risk of short circuits or other assembly issues.
- Trace routing: The placement of PTH and NPTH holes should not interfere with the routing of traces on the PCB. Designers must ensure adequate clearance between the holes and the traces to avoid signal integrity issues.
- Manufacturing constraints: The placement of holes must take into account the manufacturing capabilities and limitations, such as the minimum hole size, the minimum spacing between holes, and the drilling accuracy.
Frequently Asked Questions (FAQ)
1. Can PTH holes be used for non-electrical purposes?
While PTH holes are primarily used for creating electrical connections, they can also be used for non-electrical purposes, such as mounting heatsinks or providing mechanical support. However, NPTH holes are generally more suitable for non-electrical applications.
2. What is the difference between through-hole and surface-mount components?
Through-hole components have leads that are inserted into PTH holes on the PCB and soldered in place. Surface-mount components, on the other hand, are mounted directly onto the surface of the PCB using solder pads. Surface-mount components generally have a smaller footprint and allow for higher component density compared to through-hole components.
3. Can NPTH holes be plated?
NPTH holes are not typically plated, as they are designed for non-electrical purposes. However, in some cases, NPTH holes may be partially plated to provide additional mechanical strength or to improve the adhesion of solder mask or other coatings.
4. What is the minimum size of PTH and NPTH holes?
The minimum size of PTH and NPTH holes depends on various factors, such as the PCB material, the manufacturing process, and the specific application requirements. Generally, the minimum hole size for PTH holes is around 0.3 mm, while for NPTH holes, it is around 0.5 mm. However, these values may vary depending on the manufacturer’s capabilities.
5. How do PTH and NPTH holes affect the cost of PCB manufacturing?
PTH holes generally increase the cost of PCB manufacturing, as they require an additional plating process. The more PTH holes a PCB has, the higher the manufacturing cost. NPTH holes, on the other hand, do not require plating and are less expensive to manufacture. However, the overall cost of PCB manufacturing depends on various factors, such as the board size, the number of layers, and the materials used.
Conclusion
PTH and NPTH holes play a crucial role in PCB design and manufacturing. PTH holes are used for creating electrical connections and mounting through-hole components, while NPTH holes are used for non-electrical purposes, such as mounting hardware or providing mechanical support. Understanding the differences between PTH and NPTH holes, their applications, and their impact on PCB manufacturing is essential for designing reliable and cost-effective electronic devices.
When designing a PCB, it is important to consider the placement and routing of PTH and NPTH holes, taking into account factors such as component placement, trace routing, and manufacturing constraints. By carefully selecting the appropriate hole types and sizes, and following best practices for hole placement and routing, designers can ensure optimal performance and manufacturability of their PCBs.
As the electronics industry continues to evolve, with the increasing adoption of surface-mount technology and the demand for smaller, more compact devices, the use of PTH and NPTH holes in PCB design will likely adapt accordingly. However, the fundamental principles and considerations discussed in this article will remain relevant for the foreseeable future, providing a solid foundation for designers and manufacturers working with PCBs.
Leave a Reply