Introduction to PCB Fabrication
A printed circuit board (PCB) is the foundation of nearly all modern electronic devices. PCBs mechanically support and electrically connect electronic components using conductive tracks, pads, and other features etched from one or more sheet layers of copper laminated onto and/or between sheet layers of a non-conductive substrate. The process of manufacturing PCBs is known as PCB fabrication or PCB fab.
PCB fabrication involves several steps to turn a PCB design into the physical board that will go into an electronic product. The main steps in the PCB fab process include:
1. PCB Design & Output
2. Pre-production Engineering
3. Copper Foil Lamination
4. Drilling
5. Plating & Etching
6. Solder Mask Application
7. Silkscreen
8. Surface Finish
9. Routing & Profiling
10. Electrical Testing
11. Final Inspection
Let’s take a more detailed look at each of these key PCB fab process steps.
PCB Design & Output
The PCB fabrication process starts with the customer’s design files, typically created in an Electronic Design Automation (EDA) or Computer-Aided Design (CAD) program. The most common PCB design file format is Gerber, which is a vector image file format. Gerber files define each individual layer of the PCB, including the copper layers, solder mask, silkscreen, drills, and board outline.
In addition to the Gerber files, the customer will provide drill files that specify the location and size of all the holes that need to be drilled in the PCB. The fabricator also needs a netlist or IPC-D-356 file that maps the connections between different components on the board.
Pre-production Engineering
Once the PCB fab receives the design files from the customer, they go through a pre-production engineering phase. In this step, the fabricator’s engineers review the design files to check for any errors or potential manufacturability issues. They may make suggestions for changes to improve yield or reliability.
The fabricator generates photomasks or stencils based on the Gerber files for the various layers. For a typical double-sided PCB, there will be photomasks for the top and bottom copper layers, top and bottom solder mask, and top and bottom silkscreen. More complex multilayer boards will have additional photomasks for the inner layers. The photomasks are used to transfer the PCB image to the copper-clad laminates.
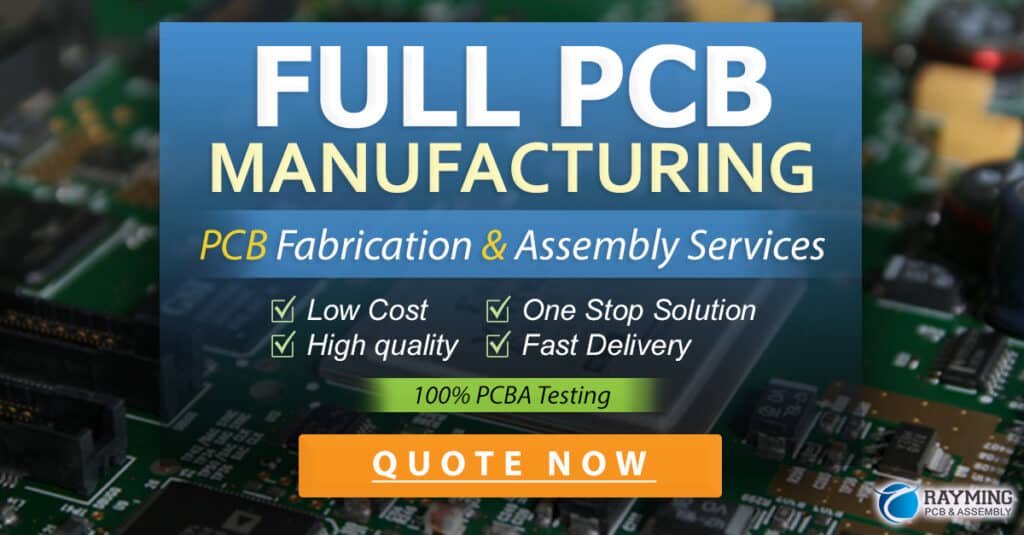
Copper Foil Lamination
With the photomasks ready, the fabrication process moves on to preparing the copper-clad laminate (CCL). This is the base material from which PCBs are made. It consists of a sheet of insulating material, such as FR-4 glass epoxy, with a thin layer of copper foil bonded to one or both sides.
For double-sided and multilayer PCBs, the fabricator creates a PCB stackup that alternates layers of CCL with layers of prepreg, which is a pre-impregnated bonding material. The stackup is placed in a hydraulic press where high temperature and pressure bond the layers together into a solid board. Careful process control is necessary to ensure proper flatness and avoid defects like delamination.
Drilling
After lamination, the next step is to drill all the holes in the board. This includes holes for through-hole component leads, vias for interconnecting different layers, and tooling holes for registration during fabrication. The holes are drilled using high-speed Computer Numerical Control (CNC) drilling machines.
The drilling process can significantly impact the quality and reliability of the finished PCB. Factors such as hit rate, hole wall quality, and cleanliness are critical. Mechanical drills are the most common, but some PCB fabs use laser drills for smaller microvias.
Plating & Etching
Once all the holes are drilled, the PCB goes through a plating process to make the holes conductive and to form the interconnects between layers. There are two main methods:
-
Electroless copper – The PCB is dipped in a series of chemical baths that deposit a thin layer of copper on all exposed surfaces, including the hole walls. This provides the necessary conductivity for electroplating.
-
Direct metallization – This newer process uses a conductive polymer to make the hole walls conductive, eliminating the need for electroless copper.
After the holes are made conductive, the PCB is electroplated with copper to the desired thickness, typically 1-2 oz. The photoresist is then applied and the unwanted copper is etched away, leaving only the desired copper pattern. The etching is usually done with an alkaline ammonia solution.
Solder Mask Application
The solder mask is a polymer coating that is applied on top of the copper layer. It serves two main purposes:
-
Insulate the copper traces from accidental contact with other metal, solder, or conductive bits.
-
Protect the copper from oxidation and corrosion.
The solder mask is typically green, but other colors are available. The mask is applied by silkscreen printing and then cured with UV light. Openings in the solder mask are left for solder pads and exposed copper features.
Silkscreen
The silkscreen is the white lettering and component outlines that you see on a finished PCB. It is applied on top of the solder mask by a similar silkscreen printing process. The silkscreen helps with assembling the PCB by indicating component placement and orientation.
The ink used for the silkscreen has to be compatible with the solder mask material and withstand the temperature of the soldering process. It also needs good adhesion and durability properties.
Surface Finish
The exposed copper areas on the PCB, such as component pads and test points, receive a final surface finish. The surface finish serves several purposes:
- Protect the exposed copper from oxidation and corrosion
- Enhance the solderability of the exposed copper
- Provide a good contact surface for test probes and connectors
There are several options for pcb surface finish, each with its own advantages and trade-offs. Some of the most common ones are:
Surface Finish | Composition | Advantages | Disadvantages |
---|---|---|---|
HASL (Hot Air Solder Leveling) | Tin-lead alloy | Low cost, good solderability | Not suitable for fine pitch, uneven surface |
ENIG (Electroless Nickel Immersion Gold) | Nickel with thin gold layer | Flat surface, good shelf life, aluminum wire bonding | Higher cost, possible black pad, not suitable for press-fit |
OSP (Organic Solderability Preservative) | Organic anti-oxidation compound | Low cost, flat surface | Limited shelf life, not suitable for multiple reflow |
Immersion Silver | Pure silver | Good solderability, low cost | Prone to tarnishing, limited shelf life |
Immersion Tin | Pure tin | Good solderability, better than silver | Prone to tin whiskers, cannot be used with lead-free processes |
The choice of surface finish depends on the specific application requirements, cost constraints, and the PCB assembly process to be used.
Routing & Profiling
The finished pcb panels are routed out of the larger production panel. This is done with a CNC routing machine that cuts along the board outline defined in the Gerber files. V-score or tab routing techniques are often used to keep multiple small pcbs attached in a panel for easier assembly.
Certain PCBs may require specific shapes or cutouts, like rounded corners or notches. This is also done during the routing stage according to the customer’s specifications.
Electrical Testing
Before the PCBs are shipped, they go through an electrical test to verify that all the connections are correct and there are no short circuits or open circuits. The two main types of electrical tests are:
-
Flying probe test – A set of movable test probes check the continuity and resistance of the PCB traces by touching down on the test points. This is suitable for small quantities or prototype runs.
-
Bed of nails test – The PCB is placed on a fixed grid of test probes that make contact with all the test points simultaneously. This is faster than flying probe and suitable for high volume production, but requires a custom test fixture for each unique PCB design.
Some PCB fabs also offer in-circuit testing (ICT) where they test the populated board with all the components loaded.
Final Inspection
The last step before the PCBs are packaged and shipped is a final visual inspection. This is to check for any obvious defects or cosmetic issues, like scratches, contamination, or incorrect marking. Many PCB fabs do 100% inspection, while others do sampling based on Acceptable Quality Level (AQL) standards.
Some common inspection tools and techniques include:
– Manual inspection with magnifying lamps
– Automated Optical Inspection (AOI) machines
– X-ray inspection for hidden defects
The boards are then packaged according to the customer’s requirements, which may include vacuum sealing, ESD protection, or moisture barrier bags for sensitive components.
Frequently Asked Questions (FAQ)
1. What is the typical lead time for a PCB fab?
The lead time depends on the complexity of the PCB, the quantity ordered, and the current workload of the fab. Simple 2-layer boards can often be turned around in 1-2 days for small quantities. More complex boards with 4 or more layers may take a week or more. Large volume orders also require more time. Many PCB fabs offer expedited services for an additional cost.
2. What are the main factors that affect the cost of PCB fabrication?
Some of the key cost drivers for PCB fab are:
– Number of layers
– Board size
– Smallest trace/space width
– Hole size
– Surface finish
– Material selection
– Quantity ordered
In general, higher complexity boards with finer features and tighter tolerances will cost more to fabricate. Ordering in larger quantities can provide economies of scale and reduce the unit price.
3. What is the minimum order quantity (MOQ) for PCB fab?
This varies by manufacturer, but many PCB fabs have no minimum quantity and can produce even single piece prototypes. However, the unit cost will be quite high for very small quantities. Typical MOQs for production orders are 100-500 pieces.
4. What are the most common PCB materials?
The most widely used PCB base material is FR-4, which is a glass-reinforced epoxy laminate. It offers good mechanical and electrical properties at a reasonable cost. For high-frequency or high-speed applications, materials with lower dielectric constant and loss, such as Rogers4350 or Isola370HR, are used. Aluminum is sometimes used as a base for metal core PCBs that require high thermal conductivity. Flex PCBs use flexible polyimide or polyester material.
5. What certifications should I look for when choosing a PCB fab?
Some important certifications to consider are:
– ISO 9001 for quality management systems
– IPC class 2 or 3 for workmanship standards
– UL listing for safety
– ISO 14001 for environmental management
– ITAR registration for defense and military work
Specific industries, like automotive or medical, may have additional certification requirements. It’s best to discuss your specific needs with potential fab partners.
Conclusion
PCB fabrication is a complex, multi-step process that turns a designer’s concept into a physical reality. By understanding the basics of how PCBs are made, you can design boards that are easier to manufacture, have higher yields, and are more reliable in the end application.
When choosing a PCB fab, consider factors like their capabilities, certifications, lead times, and customer support, in addition to the price. Building a good working relationship with your fab can save you a lot of headaches down the road.
As PCB technology continues to evolve, with finer features, higher layer counts, and new materials, having a strong understanding of the PCB fabrication process will be essential for anyone involved in electronics design and manufacturing.
Leave a Reply