Understanding High Speed PCBs
What Makes a PCB “High Speed”?
A PCB is considered “high speed” when it operates at frequencies above 100 MHz or when the rise time of the signal is less than 1 nanosecond. At these high frequencies, the PCB’s physical properties and layout become critical factors in maintaining signal integrity and minimizing noise and interference.
Signal Integrity Issues in High Speed PCBs
High speed PCBs face several signal integrity issues that can degrade the quality of the transmitted signal. These issues include:
- Reflections: When a signal encounters an impedance mismatch, a portion of the signal is reflected back to the source, causing distortion and noise.
- Crosstalk: When signals from adjacent traces interfere with each other, causing unwanted coupling and noise.
- Electromagnetic Interference (EMI): High frequency signals can radiate electromagnetic energy, causing interference with other electronic devices.
- Attenuation: As signals travel through the PCB, they lose energy due to the material properties and trace geometry, leading to signal degradation.
High Speed PCB Design Considerations
To mitigate signal integrity issues and ensure optimal performance, high speed PCB design requires careful consideration of several factors:
Material Selection
The choice of PCB material is crucial for high speed applications. The material should have a low dielectric constant (Dk) and low dissipation factor (Df) to minimize signal loss and distortion. Some common high speed PCB materials include:
Material | Dielectric Constant (Dk) | Dissipation Factor (Df) |
---|---|---|
FR-4 | 4.2 – 4.5 | 0.02 |
Rogers 4003C | 3.38 | 0.0027 |
Isola I-Speed | 3.0 – 3.6 | 0.0025 – 0.004 |
Controlled Impedance
Maintaining a consistent impedance throughout the signal path is essential to prevent reflections and ensure proper signal termination. The PCB’s trace width, thickness, and spacing, as well as the dielectric material properties, determine the characteristic impedance of the trace.
Trace Routing and Layout
Proper trace routing and layout techniques help minimize crosstalk and EMI. Some best practices include:
- Keeping signal traces as short as possible
- Avoiding sharp bends and corners in traces
- Providing adequate spacing between traces
- Using ground planes to provide a low-impedance return path and shield signals
- Routing critical signals on inner layers to minimize external interference
Grounding and Power Distribution
A well-designed grounding and power distribution system is essential for high speed PCBs. The use of ground planes, power planes, and proper decoupling capacitors helps maintain a low-impedance power supply and minimize noise.
High Speed PCB Manufacturing Processes
Manufacturing high speed PCBs requires specialized processes and stringent quality control to ensure the desired performance. Some key aspects of high speed PCB manufacturing include:
Multilayer Construction
High speed PCBs often utilize multilayer construction to accommodate the complex routing and shielding requirements. The number of layers can range from 4 to 20 or more, depending on the application’s complexity.
High-Resolution Patterning
To achieve fine trace widths and spacing, high-resolution patterning techniques such as laser direct imaging (LDI) and photolithography are used. These methods allow for trace widths as small as 25 microns and spacing of 50 microns or less.
Copper Thickness and Surface Finish
The copper thickness and surface finish of the PCB can impact signal integrity and manufacturability. Thicker copper traces help reduce resistance and improve current-carrying capacity, while smooth surface finishes like immersion silver or electroless nickel/immersion gold (ENIG) provide better signal transmission and solderability.
Controlled Depth Drilling
Precise control of drill depth is critical for high speed PCBs to ensure proper layer registration and minimize signal reflections caused by stub effects. Controlled depth drilling techniques, such as back-drilling and sequential lamination, are employed to remove unwanted stub portions of vias.
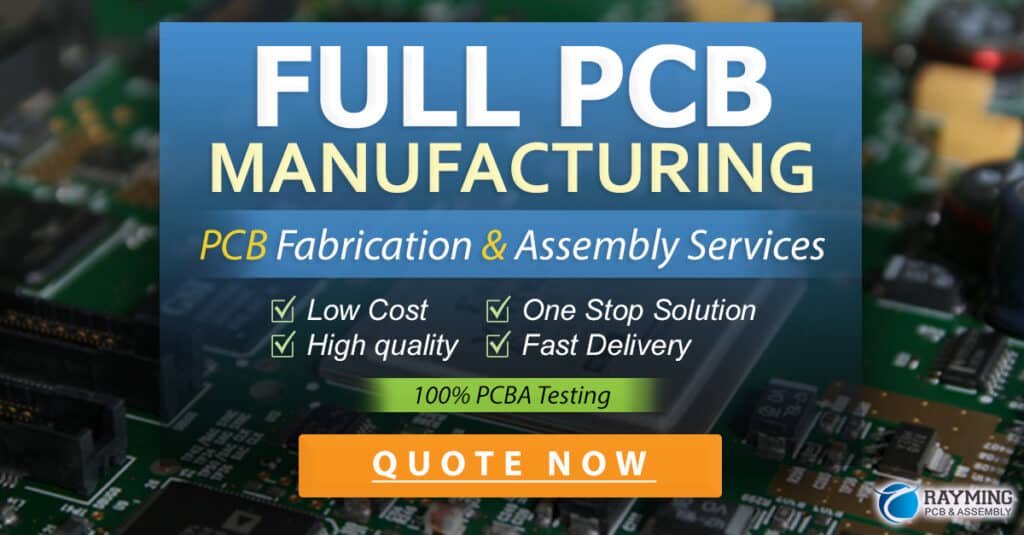
Applications of High Speed PCBs
High speed PCBs find applications in various industries and products that require fast data transmission and processing. Some common applications include:
- High-performance computing systems
- Telecommunications equipment (5G networks, base stations, etc.)
- Automotive electronics (advanced driver assistance systems, infotainment systems)
- Medical devices (diagnostic imaging equipment, patient monitoring systems)
- Aerospace and defense systems (radar, satellite communication)
- Consumer electronics (smartphones, gaming consoles, virtual reality devices)
Frequently Asked Questions (FAQ)
1. What is the difference between a standard PCB and a high speed PCB?
A standard PCB operates at lower frequencies (typically below 100 MHz) and has less stringent design and manufacturing requirements compared to a high speed PCB. High speed PCBs are designed to handle high frequency signals (above 100 MHz) and require specialized materials, design techniques, and manufacturing processes to maintain signal integrity.
2. What materials are commonly used for high speed PCBs?
Common materials used for high speed PCBs include FR-4, Rogers 4003C, and Isola I-Speed. These materials have low dielectric constants and dissipation factors, which help minimize signal loss and distortion at high frequencies.
3. Why is controlled impedance important in high speed PCB design?
Controlled impedance is crucial in high speed PCB design to prevent signal reflections caused by impedance mismatches. By maintaining a consistent impedance throughout the signal path, signal integrity is preserved, and reflections are minimized.
4. How does multilayer construction benefit high speed PCBs?
Multilayer construction allows for complex routing and shielding in high speed PCBs. By using dedicated layers for power distribution, grounding, and signal routing, signal integrity is improved, and crosstalk and EMI are minimized.
5. What are some best practices for high speed PCB trace routing?
Some best practices for high speed PCB trace routing include keeping signal traces as short as possible, avoiding sharp bends and corners, providing adequate spacing between traces, using ground planes for shielding and low-impedance return paths, and routing critical signals on inner layers to minimize external interference.
Conclusion
High speed PCBs are essential components in modern electronic devices that require fast data transmission and processing. Designing and manufacturing these boards involve careful consideration of materials, impedance control, trace routing, grounding, and power distribution to maintain signal integrity and minimize noise and interference.
As technology continues to advance, the demand for high speed PCBs will only increase. By understanding the principles and best practices of high speed PCB design and manufacturing, engineers and manufacturers can create reliable, high-performance electronic systems that meet the ever-growing demands of the industry.
Leave a Reply